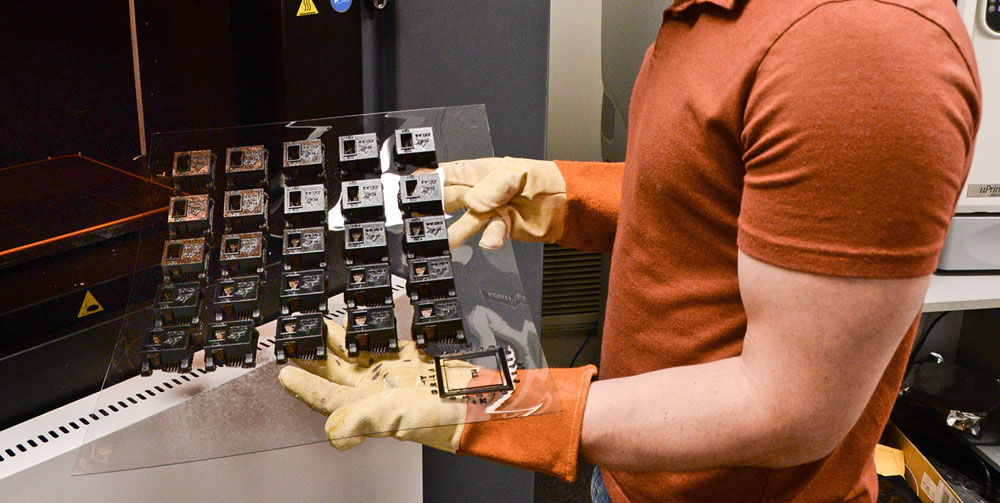
RDECOM explores new ways of using 3-D printing to meet Soldiers’ needs quickly and inexpensively while minimizing the logistics footprint.
by Argie Sarantinos-Perrin
A Soldier heads back to camp, grabs a power bar and unloads his gear. The power bar, which was “printed” minutes earlier, contains all the nutrients his body currently needs, according to sensors that are embedded in his uniform.
While this sounds like something from a sci-fi movie, engineers and scientists at the U.S. Army Research, Development and Engineering Command (RDECOM) are looking at ways to use additive manufacturing (AM, also known as 3-D printing) to meet Soldiers’ needs. Using AM to supply Soldiers with customized nutrient-dense food, or to repair critical parts on demand or to print new cells to repair burned skin, will not only lighten the logistics burden but also make the acquisition process more efficient.

MAKING IT BETTER
Angel Cruz, a mechanical engineer with the U.S. Army Research, Development and Engineering Command (RDECOM), displays an Ex Lab project to improve the infrared beacons issued to Soldiers for identification, recovery and site marking. (U.S. Army photo by Conrad Johnson)
“The vision is to be able to have additive manufacturing as a tool in the toolbox so that Soldiers can manufacture and produce a product as close to the point of need as possible,” said Andy Davis, program manager for the Army’s Manufacturing Technology program (ManTech). Part of RDECOM, which is a major subordinate command of the U.S. Army Materiel Command, ManTech works closely with Army organizations to identify and fund projects that support the overall Army science and technology strategy.
One type of AM—fused filament fabrication—produces parts from plastic and other durable materials by adding material, layer by layer, using 3-D printers. The material, which resembles heavy fishing line or weed-eater string, is precisely pushed through a print head in the pattern of the item being built.
A key benefit of AM is that it uses only the material necessary to make a part, minimizing waste and saving money. Another important feature is that AM can be used to recycle waste and make new products. For example, RDECOM’s U.S. Army Research Laboratory (ARL) is working on a process that takes unwanted material, such as the packaging from Soldiers’ Meals Ready-to-Eat and water bottles, shreds or melts it and then processes it into a string that is used to make items such as a door handle or a rack. Recycling waste on the battlefield will not only minimize the cleanup process for Soldiers, but also eliminate the wait time for new parts, which can be days or weeks. The amount of time that it takes to print a part using AM depends on the material that is used and the part that is made, but overall it is quicker than waiting for a part to be shipped.
“One of the challenges associated with AM, however, is that it’s still new, and our understanding of the process down to the level that lets us repeat it and get the same results over and over again is not there yet,” said Davis.
Providing help at the point of need
To support forward-deployed Soldiers, RDECOM partners with the Rapid Equipping Force (REF) to help manage, staff and support expeditionary labs (Ex Labs), which can be deployed worldwide. The Ex Labs are designed to get innovative items to the Soldiers as quickly as possible; one lab is currently at Bagram Airfield in Afghanistan and another lab at Camp Arifijan, Kuwait.
Each lab is built into a 20-foot shipping container and two ISU90 containers, which are customized containers that hold a 3-D printer, supporting equipment and a computer-aided design (CAD) workstation. The CAD is used to create virtual working models before they are sent to a 3-D printer. Once a design is perfected, it will be stored in an enterprise-wide product data management (ePDM) system that RDECOM and AMC are creating. Other organizations will have access to the ePDM, fostering data-sharing and eliminating the need to make every design from scratch. The labs are also stocked with traditional tools, equipment and software to design and fabricate metal and plastic parts.

PUTTING THE PIECES TOGETHER
Sgt. 1st Class Justin Fulk, Ex Lab noncommissioned officer-in-charge, welds parts at Bagram Airfield, Afghanistan. Ex Labs are well stocked with traditional tools, equipment and software to design and fabricate metal and plastic parts. A second lab is located at Camp Arifjan, Kuwait. (U.S. Army photo) (U.S. Army photo)
“The labs have an open-door policy so the Soldier can come in and describe his mission capability shortfalls, and the [Ex Lab] team immediately starts brainstorming ideas and solutions,” said Angel Cruz, RDECOM Ex Lab project lead. “If the item doesn’t work or fit right the first time, then the [Ex Lab] team can revise the design on the spot. AM allows us to produce different iterations of a solution very quickly in order to get it just right.”
The on-site Ex Lab team includes a REF non-commissioned officer in charge, an RDECOM lead engineer, a support engineer and a machinist. Together, they develop solutions using textiles, electronics, subtractive manufacturing and additive manufacturing. AM is used for parts that are difficult to machine or as a substitute for parts that would normally be made using injection molding, which is expensive and requires specialized equipment. Other projects require traditional manufacturing or subtractive manufacturing, which takes away material by cutting, grinding, milling and other methods.
When the Ex Lab cannot complete the work because of a lack of subject matter expert, required supplies or time to complete the project, RDECOM’s Edgewood Chemical Biological Center provides reach-back support across the RDECOM network of engineers, scientists and technicians.
RDECOM plans to develop AM in three phases. Phase one will use AM to repair or replace existing parts. Phase two will reduce multipart assemblies from a series of parts to one part. For example, the receiver on a machine gun comprises titanium parts that are welded together in a multipart assembly; the goal is to print all of the parts as one part using AM, thereby reducing the number of parts and cost. Phase three will use AM to create new parts that don’t already exist.

EVOLUTION OF AN IDEA
This breaching tool, which is used to open doors and crates or to cut wires and other material, evolved from the initial pattern on the left to the final product on the far right. Based on Soldier feedback on the original design, the Ex Lab team added contouring to the handle for safety and grip. The team also added quick change blades and hex holes in the handle so that it can be used as a wrench. (U.S. Army photo)
“RDECOM envisions AM’s evolution across the Army’s acquisition and life cycle management ecosystem,” said Davis. “It is a crawl-walk-run approach that simultaneously targets low-hanging fruit such as non-structural repairs using additive manufacturing and longer-term material development activities such as designing new components using additive manufacturing.”
Partnering with industry and academia
In addition to RDECOM engineers and researchers who are developing new and innovative ways to use AM, the Army is partnering with industry and academia to share information and pool resources. The Army has partnered with GE, for example, and plans to leverage its experience and knowledge for future Army products.
After years of research, GE has developed a way to produce a metal part for the fuel system on its LEAP engine using AM, which will yield 1 to 2 percent higher fuel economy. The LEAP engine is used on one of GE’s commercial airliners, and GE has a dedicated production facility that produces the part. ManTech is also working with GE to mature AM production for parts on the T700 engine, which is owned by GE and used on the Army’s Black Hawk and Apache aircraft. GE hopes to draw upon the benefits of AM to create parts that will reduce engine weight and improve efficiency.
“GE will take what it has developed plus what we have incentivized them to develop for Army engines, and then transition that technology and process into the next generation Army engine, which will be beneficial for many decades,” said Davis.

PRINTING UP THE FUTURE
These parts were made using additive manufacturing, which creates plastic items and other durable components by adding material, layer by layer, using 3-D printers. (U.S. Army photo)
Still early in AM
A fundamental challenge for Army-wide adoption of AM is the need to have a comprehensive understanding of the specific AM process that will be used to produce a given part as well as the materials that will be processed.
Material property and process data are paramount to the qualification and certification process of any part, whether produced by AM or traditional manufacturing. In traditional manufacturing, most processes (e.g., casting) and the properties and tolerances of the materials used (e.g., steel) are universally understood, documented and accepted. However, with AM, new processes and materials are being developed rapidly, and information about the performance of the parts that are produced is often insufficient. ManTech is making investments through several projects to create the capability and infrastructure required to capture, store and share this data across the Army.
“We hand off the data that we have collected after we mature technologies to a certain level,” said Davis. “Then, we look at the materials and what we want to do with them and find a program office that has potential applications and timelines that we can support.”
Conclusion
AM is an exciting area of research and one that promises dramatic results in the not too distant future. With a sophisticated AM printer nearby, Soldiers deployed in remote outposts around the world will be able to “print” virtually everything they need, from food to shelter to weapons. If a Soldier gets burned, a 3-D map of his injury will determine what types of cells should be printed and exactly where the cells need to go in order to grow new skin. Before a platoon moves to a new location, Soldiers will recycle any waste, making cleanup quick and easy. Without a cumbersome logistics process, the Army will be able to provide more capabilities at a lower cost. Parts will be printed on the spot, eliminating the shipping process. While there is much work to do, AM is gathering speed. In time, AM will not only make Soldiers’ lives easier, but also change how the Army conducts business.
For more information, visit www.army.mil/rdecom.
Creating a Technology Roadmap As the result of rapid growth in AM capabilities over the past several years and the Army’s increasing interest and need in using AM to improve readiness, the Army established an AM community of practice (CoP) in 2014. The CoP, with representatives from across the Army enterprise, meets quarterly to share information, coordinate projects and activities and leverage resources, avoid duplicating efforts and ultimately improve AM and promote its use across the Army. CoP meetings also serve to identify capability gaps in AM and provide recommendations to Army leadership regarding areas where additional research and development are needed. The Army recently completed an AM technology roadmap, which was sponsored and managed by ManTech. The project, which began this year, includes RDECOM, program executive offices, the acquisition community and Soldiers, and provides strategic guidance across the Army materiel and life cycle management communities. The roadmap has four key areas that are critical to using AM efficiently and effectively:
The AM technology roadmap will be used to inform industry and academia on how the Army plans to use AM, as well as issues that need to be addressed. The Army’s roadmap, along with individual AM roadmaps from the Navy, the Air Force, the Defense Logistics Agency and the Special Operations Command, were integrated into an overarching DOD-wide AM roadmap that was rolled out in December 2016. “I don’t know of any other time when organizations across the Army and DOD came together to develop a roadmap that involves everyone from the requirements community to the user community and all the way to the sustainment community,” said Davis. |
MS. ARGIE SARANTINOS-PERRIN is a public affairs specialist for Camber Corp., providing contract support to RDECOM. She holds an M.S. in professional writing and a B.A. in mass communications from Towson University. She has 11 years of public affairs experience supporting the DOD.
This article will be published in the January – March 2017 issue of Army AL&T Magazine.
Subscribe to Army AL&T News, the premier online news source for the Acquisition, Logistics, and Technology (AL&T) Workforce.