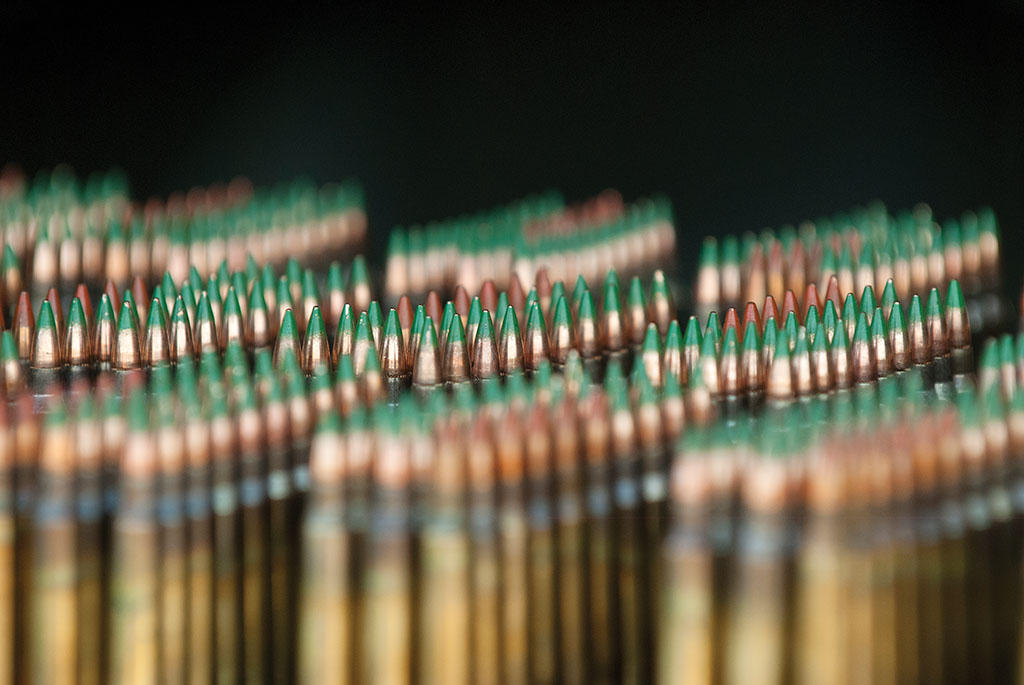
ARDEC and JMC aim to simplify procurement and reduce cost of conventional ammo with new contract clause
By Mr. Steve Stark
The U.S. Army Armament, Research, Development and Engineering Center (ARDEC) and the Joint Munitions Command (JMC) in the next few months will begin a pilot of a contract clause that should allow for a uniform, integrated approach to help conventional ammunition suppliers comply with acceptance inspection equipment (AIE) requirements while encouraging them to follow commercial best practices.
“Inspection is essential to any manufacturing system. It’s the means of identifying and rejecting nonconformities, thus ensuring that only conforming product gets to the warfighter,” said Jennifer Herrera, a quality engineer with Program Executive Office (PEO) Ammunition, who will manage the pilot of the new measurement system evaluation (MSE) clause. Inspection is even more important when the product is ammunition, she said, so it’s imperative that AIE requirements be clearly stated and understood by the government and contractors.
The MSE clause, developed for use in conventional ammunition acquisition, will clarify procurement and make life simpler for the services, special operations program managers and industry by taking information currently located in a variety of different places and putting it in one, easy-to-find location, said Herrera. Accompanying the MSE will be two contract data requirements lists (CDRLs), which spell out a time frame and required data for a specific procurement and which become a part of the contract. The new clause also includes a unique data item description (DID), which outlines the format and content of the data deliverables, and a detailed review guide.
In a nutshell, the review guide is meant to aid in applying the MSE clause and in developing and reviewing AIE submissions. It also helps personnel involved in the review, design or selection of AIE used to inspect characteristics identified in government technical data packages.

END-USER EXPERIENCE
Spc. Charles R. Reiff, an indirect fire infantryman with 1st Battalion, 506th Infantry Regiment, 4th Brigade Combat Team, 101st Airborne Division (Air Assault) (4-101 ABN), inspects ammunition at Combat Outpost Zormat, Afghanistan, Sept. 9, 2013, before going out on a mission. When it comes to ammunition, rigorous inspection is especially important, which makes it imperative that AIE requirements be clearly stated and understood by the government and contractors. (U.S. Army photo by Sgt. Justin A. Moeller, 4-101 ABN Public Affairs)
FROM HARD-TO-FIND TO ONE-STOP SHOP“The Joint Lethality and Munitions Life Cycle Management Command has had [the same] three AIE clauses for easily over 30 years,” said Jorge Munoz, technical lead for small-caliber ammunition at ARDEC. Currently there’s one AIE clause for ARDEC, one for JMC, and another at JMC that’s specific to the Air Force and Navy.
“During that time frame,” he continued, “manufacturing production processes have changed to become more automated. The production processes have changed and have become more automated and sometimes intertwined with the inspection processes, so we wanted to come up with one, all-inclusive AIE clause that could be used across the four military services and that will address the automation issues.”
He added that the command also sought to develop a clause that applies a unified standard instead of changing standards, as in the past, that depended on which service the product was for. The result is the MSE clause, developed by a multiservice, multidisciplinary Supplier Quality Initiative (SQI) process action team representing contracting, legal, quality and engineering personnel.
“Our current requirements are pretty good. It’s just that they’re in so many different places,” said Sanket Patel, a member of the SQI team and the Joint Ordnance Commanders Group (JOCG) Quality Assurance (QA) Subgroup chairperson. “There were minor variances between the requirements, like the three top-level contract clauses.
“Our goal,” he explained, “was to come up with one contract clause, one data item description, and pull all these references to commercial industry best practices into one place, so a contractor could bid on these effectively and execute to the requirements effectively.”
Because contract requirements were not in the same place, Munoz said, “if the contractor or even the engineers here wanted to review what the requirements were, they had to go to different sources. There was no ‘one-stop shop.’ By using the MSE clause instead of the three AIEs, all of the DIDs and CDRLs for all of the requirements would be in one place,” he noted.
The intended result, said Chris Mahoney, manufacturing quality lead for Naval Air Warfare Center Weapons Division China Lake, California, is to simplify things for both the government and the contractor. He explained the benefit to contractors: “Say you’re a contractor who has a Navy contract, an Air Force contract and an Army contract, and they have three different clauses. It causes some headaches” for all concerned when “there are different requirements that should be common requirements.”
For example, said Rick Boyle, QA specialist at JMC, “Before, we had varying timelines” in requirements. “The Navy and the Air Force have some of their own unique requirements that were in a separate clause. Sometimes the CDRLs would get confused, [and] they would end up picking up on the wrong CDRL, or the wrong CDRL may get included in the contract, so what [the MSE clause] will do is make sure that we only have one CDRL” that will go into the contract.
That, said Patel, could significantly reduce non-value-added overhead. “Here’s a simple example,” he said: “You may have an older commercial reference on one requirement and a newer commercial reference on another requirement, but they’re really the same requirement” with very little difference.
“They’re both commercial standards that industry uses—it’s just that one has the latest variant of it.” The bottom line, according to Patel, is that “it’s a lot of minutiae that creates non-value-added overhead requirements on the contractor to do further analysis, when we really don’t have to have them spend that time and energy doing so.”
The SQI held an MSE industry day in December 2013 to address any concerns among suppliers regarding the details of the government’s draft MSE clause, Herrera said. More than 50 suppliers attended the event, which culminated in a draft supplier-government clause developed in cooperation with the suppliers who attended. Working collaboratively with the supplier industrial base will contribute to more effectively initiating, executing and implementing the clause on future contracts, she noted.

TEST AND EVALUATION
Engineer Mike Menegus prepares equipment for testing at the Environmental Test Laboratory at Picatinny Arsenal, New Jersey. Inspection helps identify and reject nonconformities to ensure that only conforming product goes to the warfighter. Testing determines how equipment will perform in various settings. The intent of the new MSE contract clause is to support a uniform, integrated approach to both for conventional ammunition suppliers. (U.S. Army photo)
SAFETY, PREVENTION AND DETECTION
The development of the MSE clause came out of ARDEC and JMC’s SQI, which began in 2006 “as a sub-integrated process team to the JOCG QA subgroup,” Patel said. “The intent was to look at our requirements and engage in continuous improvement activities based on impact and effort.”
Specifically, that meant assessing core requirements for quality at the Single Manager for Conventional Ammunition level, and deciding which requirements should undergo “continuous improvement activities to ensure that we have clean and stable requirements,” Patel said. The first product to emerge from that initiative “was a single critical characteristics clause,” he said. “When it comes to safety, that jumped out as the number one criterion—that we should ensure that all requirements are clean and stable. We created a single critical characteristics clause for ammunition procurements.”
The second outcome was the process capability control and improvement clause, “which addresses the prevention element of quality, or preventing defects from happening in the first place,” Patel said. (See “Process Capability, Control, and Improvement Clause Allows Enhanced Process Monitoring and Control,” Army AL&T magazine, January – March 2011, Page 66.)
The MSE, the newest effort out of the SQI, addresses the detection of defects. “We addressed safety, then we addressed prevention,” Patel said, “Now we’re addressing the detection element, which is the inspection process. So that’s the genesis of the project and the process we’ve been using with standard Lean Six Sigma [LSS] tools.”
The idea behind the initiative is for process action teams to use the LSS tools to investigate and improve a defined work process, with the goal of improving customer satisfaction.

KEEPING THE RECORD STRAIGHT
Spc. Henryon Russell, left, Staff Sgt. Ricky Sheppard and Staff Sgt. Yolandia Quinn catalog ammunition, explosives and spent munitions during a Mine Resistant Ambush Protected Vehicle ammunition abatement inspection Oct. 12, 2013, at the Camp John Pratt Redistribution Property Assistance Team yard, Afghanistan. The process of delivering high-quality ammunition to the U.S. military involves a number of players, including ARDEC and JMC, which are conducting the pilot of the new MSE clause. (U.S. Army photo by Sgt. 1st Class Timothy Lawn, 1st Theater Sustainment Command Public Affairs)
MSE AT WORK
Besides the three current AIE clauses, current requirements documents include the military specifications MIL-A-70625, “Automated Acceptance Inspection Equipment Design, Testing and Approval of”; and MIL-A-48078, “Ammunition, Standard Quality Assurance Provisions, General Specification for.” According to Patel, having the applicable requirements referenced in one document, the MSE clause, will facilitate communication of requirements between government officials and contractors, and will improve the first-pass yield of AIE submissions.
That means when a contractor says, “Here’s our inspection equipment that we’re using to validate the critical and major characteristics,” they’ll get it right the first time. Contractors will know exactly what’s expected of them because they’re not switching between multiple variants of the same requirement.
The MSE clause supports and reinforces the expectations of MIL-A-70625 and of MIL-STD-1916, “DOD Preferred Method for Acceptance of Product,” Paragraph 4.4, “critical characteristics,” which states: “Unless otherwise specified in the contract or product specifications, the contractor is required for each critical characteristic to implement an automated screening or a failsafe manufacturing operation and apply sampling plan VL-VII to verify the performance of the screening operation. The occurrence of one or more critical nonconformances requires corrective action as specified in paragraph 4.5.”
MIL-A-70265 “prescribes requirements for design, testing and design approval of all automated acceptance inspection equipment systems,” and “is applicable to both government- and contractor-owned equipment, which is used to assure that supplies offered for government acceptance conform to the government design requirements.”
A CDRL, in conjunction with the appropriate DID, specifies and schedules the ordering and delivery of data that the government requires. The MSE clause has time frame requirements for two separate but interdependent deliverables; hence the need for two CDRLs. The first provides the recommended time frame for delivery of the AIE package.
The second corresponds to the measurement system analysis (MSA) paragraph of the MSE clause, which requires delivery of MSA assessment plans, associated data and analysis in accordance with ASTM E2782-11, in a certain timeline for specific characteristics identified in the clause.
To put that in more concrete terms, Munoz said, if a specification requires that, for example, a ball bearing should have a particular outside diameter within narrow tolerances (a major characteristic), then the contractor will have to provide the specific type of equipment (the AIE) it uses to determine those tolerances, and the accuracy of that equipment. The government can require the contractor to conduct a repeatability and reproducibility (R&R) test of the equipment. (R&R is a kind of MSA.) So the MSA CDRL is triggered for specific characteristics defined in the contract that require analysis, after the MSE CDRL has been satisfied for general acceptance inspection equipment requirements.
As its name implies, the data item description specifically defines the data content, format and intended use for the contractor to prepare required data for the government’s use. This unique MSE DID consolidates the existing AIE DIDs, references special inspection equipment and methods, and outlines the recommended content and format for AIE submissions that contractors are to provide to the government for review
and approval.
CONCLUSION
“The benefit to the contractor and the benefit to the program manager is mutual—reducing cost and schedule impact while increasing the quality and reliability of the end product,” said Ricardo Martinez, SQI Team member representing the Systems Engineering and Technology Integration Division of PEO Ammunition’s Project Manager (PM) Maneuver Ammunition Systems. “The MSE clause will help the contractors bid and schedule AIE work appropriately and consistently,” he said. That, in turn, “will lead to cost avoidance and reduce schedule impact. Essentially, the clause will help the contractor and government operate more efficiently while reducing or eliminating misinterpretation of the current AIE requirements” on either side.
“Essentially,” Martinez continued, piloting the clause “will serve as validation to the ammunition and weapons community, especially the program managers and contractors, that the intended benefit of implementing the MSE clause has been achieved. A pilot program gives us objective evidence to prove our claims. So taking the time to do a pilot program will improve adoption across the enterprise, which includes all military services, small and large businesses, and a very diverse portfolio, and ensure that any lingering questions or unknowns are addressed.”
To those who might fear that the MSE clause is adding requirements, Martinez said it is not, nor is it exposing hidden requirements that are currently being overlooked or misinterpreted. “The SQI team has worked hard at wording the clause and supporting documents in a way to meet the goal and also add flexibility for the PM to adjust some requirements as needed,” he said.
For further information, contact Rick Boyle at richard.p.boyle4.civ@mail.mil or Jorge Munoz at jorge.a.munoz8.civ@mail.mil.
MR. STEVE STARK provides contracting support to the U.S. Army Acquisition Support Center for SAIC. He holds an M.A. in creative writing from Hollins University and a B.A. in English from George Mason University. He has worked in a variety of positions supporting communications for the Army and Navy, and has written about defense-related topics for more than a decade. He was the founding editor of the Program Executive Office Soldier Portfolio and edited the Army’s Weapon Systems handbook for six years.
This article was originally published in the April – June 2014 issue of Army AL&T magazine.
Subscribe to Access AL&T is the premier online news source for the Acquisition, Logistics, and Technology (AL&T) Workforce. Subscribe