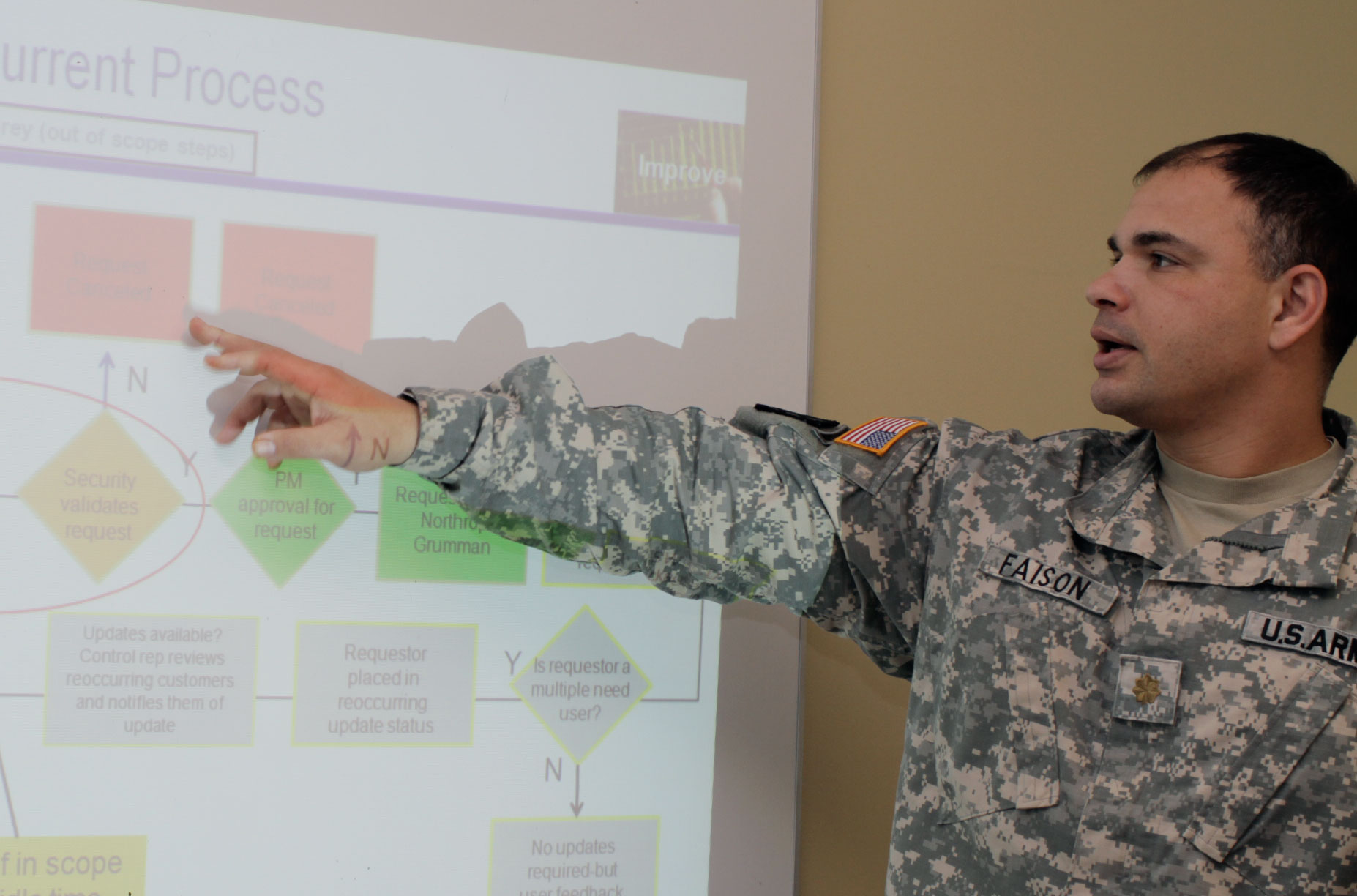
Meg Carpenter
If necessity is the mother of invention, then aggravation is the father of process improvement.
Undocumented methods for in-processing were so frustrating to Maj. Marty Jackson, he leveraged his Lean Six Sigma (LSS) training to find a solution. It took the former assistant product manager for Joint Battle Command-Platform (JBC-P) 15 days to set up his e-mail when he in-processed.
Jackson, now the Executive Officer to the Program Executive Officer for Command, Control and Communications-Tactical (PEO C3T), refused to let his experience be the norm. He completed a Green Belt LSS project to increase in-processing efficiencies within Project Manager JBC-P.
His LSS team made two recommendations. First, send new employees a welcome letter and any forms that can be completed prior to their start date and request that they take training that can be completed prior to arriving.
The second recommendation was to create a standard operating procedure (SOP) for new employees. This in-processing checklist applied to new military, civilian and support contractor employees for PM JBC-P. The checklist covers security, human resources and computer accounts.
“We’re changing what we can change,” Jackson explained. “The Garrison’s Network Enterprise Center (NEC) still has its own process and timeline; however, we can get our new employees’ paperwork to the NEC sooner.”
With the recommendations accepted and in-processing checklists in place, PM JBC-P will see $340,000 in net cost avoidance over six years.

Creating standard operating procedures for deployment and leveraging the PEO C3T suspense tracking system helped provide an easier deployment process. Supervisory Human Resources Specialist (Military) Hector M. Torres (left) now has a mechanism to track when Soldiers complete forms during the deployment process. Maj. Michael J. Williams reviews the deployment process with Torres. (Photo by Meg Carpenter, PEO C3T)
Cumbersome Process Revamped
A time-consuming process prompted Maj. Charles F. Faison, product director for Tactical Ground Reporting, part of JBC-P, to complete a software distribution project. The problem was that JBC-P software needed to be sent to various vendors and customers. The tracking process was paper-based and averaged 51 days from start to finish.
Faison’s team used LSS to analyze why it was taking so long.
“The LSS training I received gave me an array of tools to streamline my software distribution process,” Faison said.
LSS training advises team members not to focus on solutions too early during the LSS project. Fully analyzing a problem elicits better solutions.
“My initial thoughts for a solution would not have gained as much efficiency as attacking the root causes of the problem,” Faison said. “It’s human nature to want to fix a problem right away. But you really have to analyze the causes.”
Faison’s team created a process map of the software distribution process as it was, and then the team identified steps that had limited or no value. The team also found there was no database of information—the ‘database’ was a manila folder containing past requests from customers for software.
“Keeping our customers serviced with new software upgrades by leafing through papers was highly inefficient,” Faison said.
The team recommended creating a database and an automated process, both of which were adopted. Since then, delivery time has decreased from 51 days to three days. Because the process is more efficient, JBC-P did not need to hire an additional person to coordinate this process. An employee now does this as an additional duty. The cost avoidance is $11,000 per year for JBC-P.
“This is not a high monetary metric,” Faison explained. “But we did not have to hire an additional person and the whole process is much smoother for everyone involved.”

Maj. Charles F. Faison credits LSS training to teaching him to look deeper into challenges to find the root causes instead of going for a quick solution. Faison’s LSS team shortened a 51-day software distribution process to 3 days. (Photo by Meg Carpenter, PEO C3T)
From Chaos to Order
Confusion while trying to deploy prompted Maj. Michael J. Williams, assistant product manager for Product Manager Warfighter Information Network-Tactical Increment 1 (PdM WIN-T Inc 1), to undertake an LSS project to improve the deployment procedures for Aberdeen Proving Ground (APG) military personnel.
“When I deployed on temporary duty to Afghanistan in 2011 it was a chaotic process,” Williams said. “There was no definitive source from Aberdeen’s perspective nor visibility at the PEO level.”
PEO C3T military personnel are expected to comply with APG policies. At the time Williams deployed, the PEO was at only a 75 percent compliance rate.
Williams’ LSS team created SOPs for deployment by combining the Garrison’s policies and the PEO’s policies. One new procedure involves the Military Human Resources specialist tracking Soldiers in the PEO suspense tracking system as they complete the deployment process and sending in completed paperwork on behalf of Soldiers.
“This SOP makes it easier for people to deploy and the suspense system provides visibility for people down range,” Williams said.
Continuous Process Improvement (CPI) at PEO C3T
PEO C3T’s CPI program’s mission is to improve the efficiency of operations by optimizing key processes and identifying and executing CPI projects, with the ultimate vision of driving value to the Soldier and the citizen. Program Executive Officer Maj. Gen. N. Lee S. Price requires all PEO C3T majors to undertake LSS training and complete their Green Belts and encourages all workforce members to undertake the training.
“We always need to be finding efficiencies and quantifying them,” Price said. “It’s up to us to save taxpayers’ money by consolidating or stripping out unnecessary processes.”
In FY12, the Army certified 22 Green Belts and four Black Belts at PEO C3T, including 13 majors and one captain. The PEO’s 26 gated projects and 10 non-gated projects resulted in $23.5 million in cost savings and $116 million in cost avoidance across FY12-18, surpassing the PEO’s goal of 2 percent of its total obligation authority, or $72.5 million.
“We are raising the bar for FY13,” said Thom Hawkins, chief, Program Analysis Branch, and CPI program director for PEO C3T. “The PEO has set a goal of 3 percent of its total obligation authority, or $87.4 million. The PEO also plans to re-deploy its certified belts on PEO-level enterprise projects.”
The FY13 LSS Training schedule is on AKO at https://www.us.army.mil/suite/doc/36722897. Contact your training coordinator or LSS deployment director to register for a course in the Army Training Requirements and Resources System.