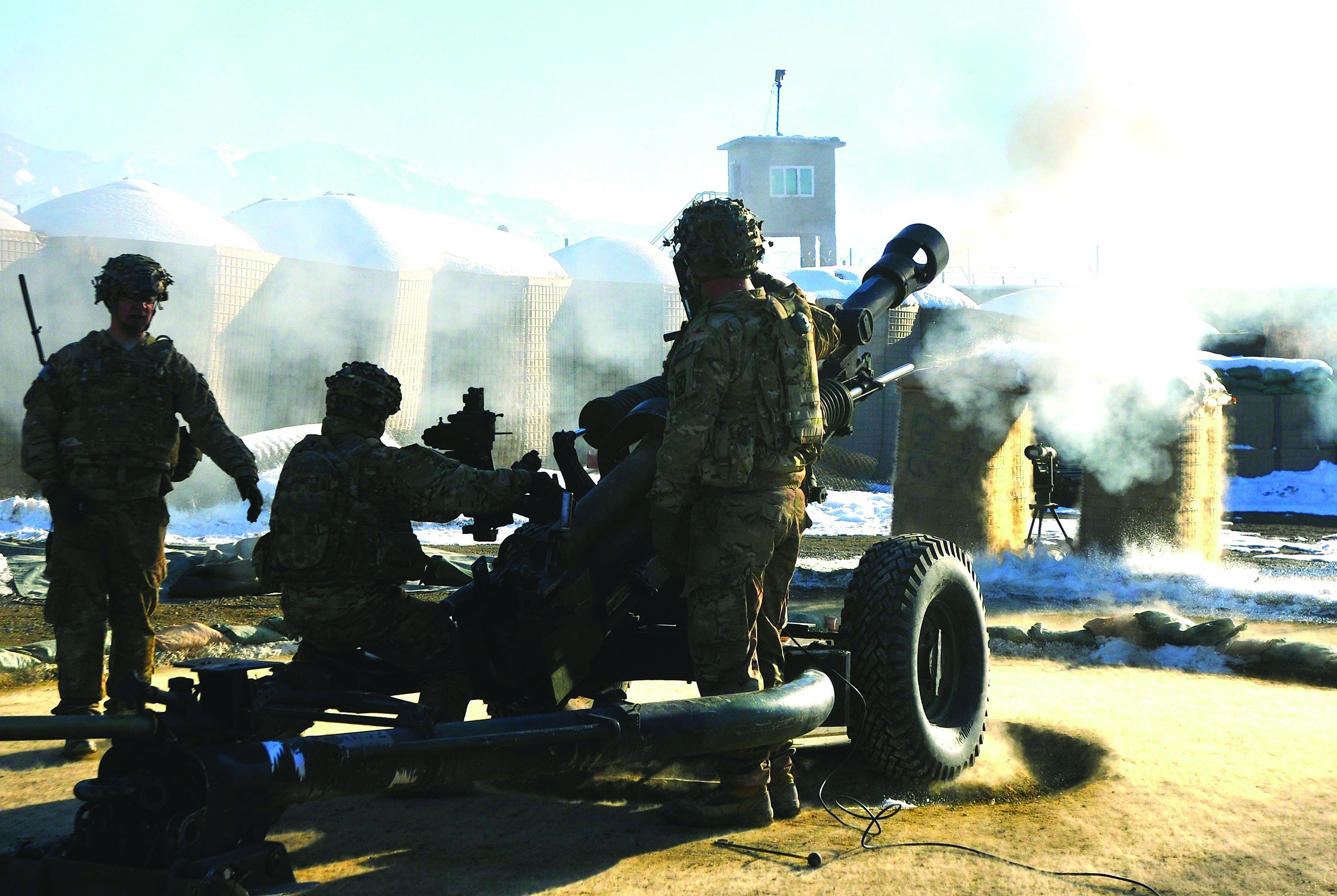
Design change strengthens battle-worn M119A3 howitzer at less cost than new system
By Mr. Joseph Lipinski and MAJ Wade Perdue
Over a decade has passed since the beginning of Operation Enduring Freedom (OEF), and the Army has asked more from its artillerymen than at any time in history. No matter what the mission, from multiple deployments to conducting nonstandard missions in some of the most remote locations in the world, artillerymen have always been flexible and adaptable. But high-altitude mountain warfare has tested more than the limits of our Soldiers; it has tested the limits of the howitzers they fire, as witness the M119A3.
With its extended range, accuracy, reliability and mobility, the M119A3 howitzer has proven to be a vital fire support platform for infantry brigade combat team (IBCT) commanders. The howitzer has seen extensive use in the mountainous territory of Afghanistan, firing multiple-round, high-angle, high-charge missions daily in support of combat troops. Continuous firing of high charges at high angle caused component damage, such as holes and cracks, on the lower carriage and baseplate of the M119A3, eventually making these items unserviceable. “High angle” defines fire delivered at elevations greater than that of the maximum range for the gun and ammunition concerned. Range decreases as the angle of elevation increases.
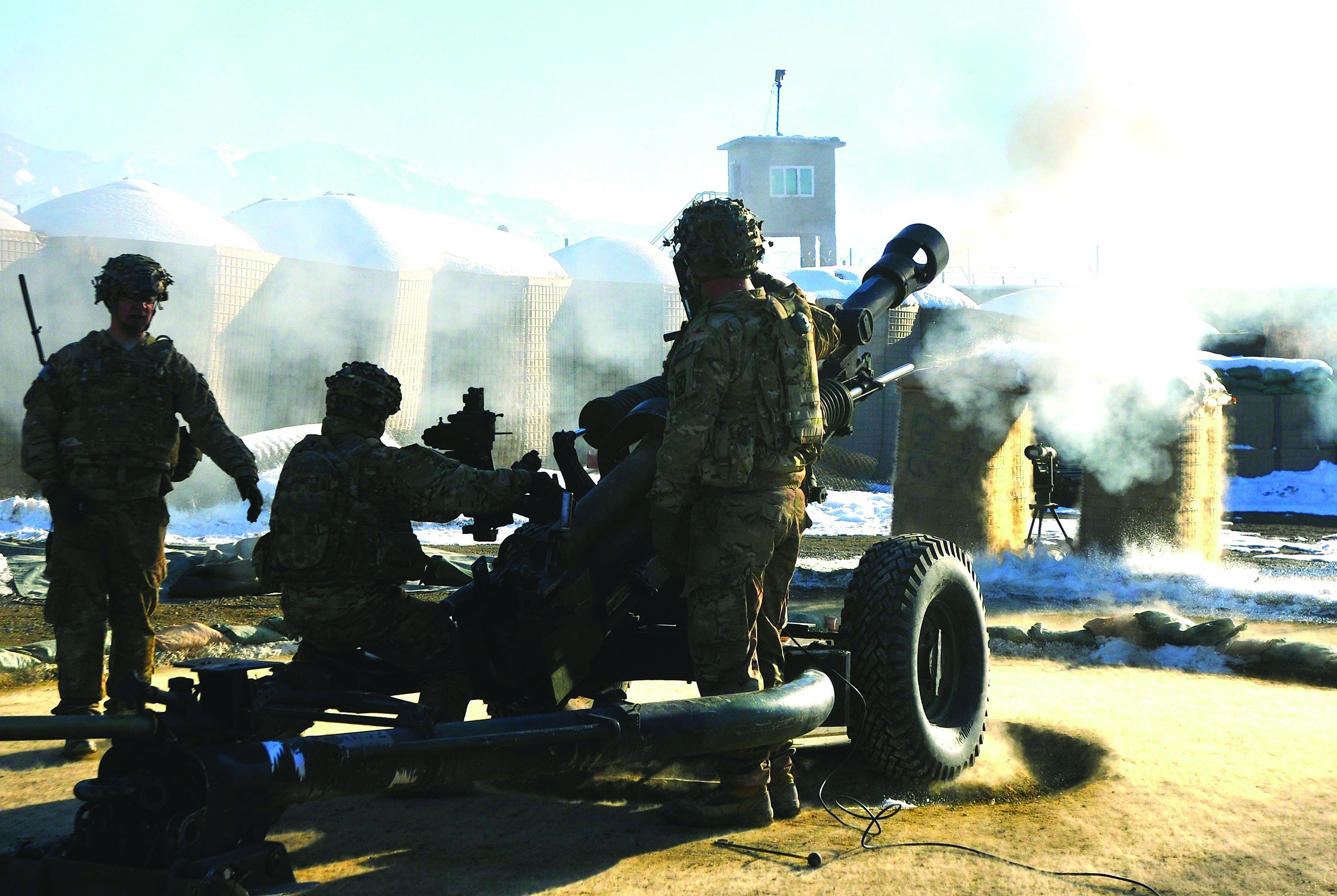
HEAVY USE: Soldiers of 4th Battalion, 25th Field Artillery Regiment, 3rd Brigade Combat Team, 10th Mountain Division (3-10 MTN) calibrate their M119 howitzer during a live-fire exercise Jan. 15 at Forward Operating Base Lighting, Afghanistan. The howitzer has seen extensive use in the rugged territory of Afghanistan, which over time has caused damage to the lower carriage and baseplate of the weapon. (Photo by SGT Javier Amador, 3-10 MTN Public Affairs)
High-angle fire is used for firing into or out of deep defilade, such as that found in heavily wooded, mountainous and urban areas. It is also used to fire over high-terrain features near friendly troops.
To correct the damage problem, the Office of the Project Manager for Towed Artillery Systems (PM TAS) of the Program Executive Office for Ammunition, in collaboration with engineers at the U.S. Army Armament Research, Development and Engineering Center (ARDEC), developed a creative solution known as the Suspension Lock-Out System (SLOS), which PM TAS will begin fielding during the fourth quarter of FY15.
The SLOS will not only alleviate holes and cracks on the lower carriage and the firing platform, but will also provide increased howitzer stability when firing all quadrant elevations with top-zone propelling charges, essentially allowing M119A3 crew members to provide more accurate and responsive fires. Quadrant elevation is the angle between the level base of the trajectory and the axis of the bore when the howitzer is laid, or simply the elevation or depression of the howitzer gun barrel. The quadrant elevation of the M119A3 ranges from -100 mils minimum to +1,244 mils maximum.
STRONGER DESIGN
The hardware for SLOS has three main components: struts and brackets, a fixed-recoil system and a titanium firing platform. The struts and brackets are lightweight, titanium, easily installable and field-deployable mechanisms that attach to the lower carriage of the howitzer. The SLOS kit removes the problematic variable-recoil hardware and replaces it with a fixed-recoil system. With the fixed-recoil system, the maximum recoil the operator will experience during operations, including high-angle, high-charge fire missions, will be 25 inches. With the variable-recoil system, the maximum recoil at maximum elevation is 14.5 inches, and the maximum recoil at minimum elevation is 42 inches.
The fixed-recoil system translates into reduced firing loads on the carriage, thus increasing durability and reliability of the howitzer, and improves the rate of fire by significantly reducing unwanted displacement, or the unwanted movement of a howitzer caused by the shock of firing. Such movement requires the crew to realign the howitzer to the gun target line after each shot fired. Reducing displacement means more responsive fires and less wear and tear on the howitzer.
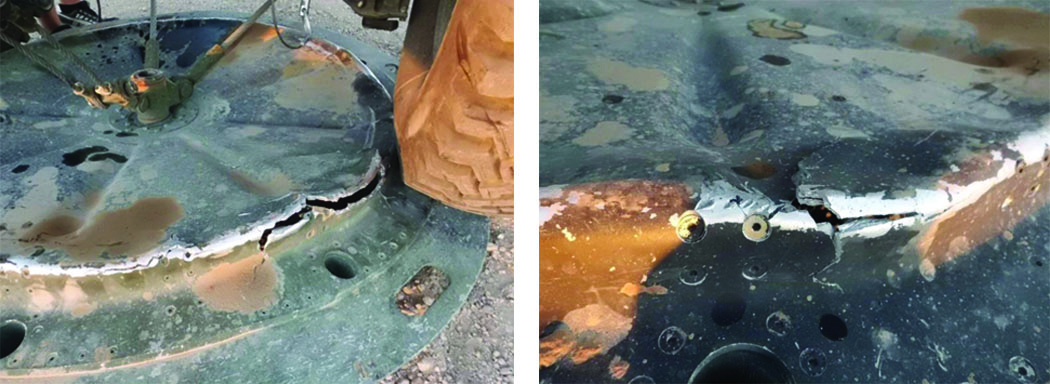
SIGNS OF WEAR: Damage, such as cracks and holes, occurs during high-quadrant elevation, high-charge firings when the existing bump stops impact the firing platform. (Above photos courtesy of MAJ Wade Perdue, PM TAS)
The titanium firing platform is an enhancement to the currently fielded aging steel firing platform. The legacy platform, made of aluminum and steel, is a multipiece assembly consisting of approximately 200 fasteners with significant welding. Though this design has served the Army well since it first saw service with the 7th Infantry Division in 1989, recent combat operations in OEF identified the need for a stronger, more durable platform.
The redesigned titanium firing platform will be cast as a one-piece molded system, thereby eliminating multiple parts and fasteners while still serving the same purpose as the original platform. Another added benefit of the titanium platform is a reduction in weight; it is 30 pounds lighter than the legacy platform. It also incorporates new carrying handle geometries to increase robustness and carrying comfort. The legacy platform’s handle holes had sharp edges and often caused strain on the users’ hands during emplacement and displacement. The new design recognizes human factors and ergonomics. The new handles have a much larger, smoother surface to help reduce strain.
Although the titanium platform costs slightly more than the legacy platforms—roughly 7 percent more per unit—a greatly reduced logistics footprint mitigates the constant repair and replacement of legacy platforms, resulting in a significant increase in mission readiness and availability.
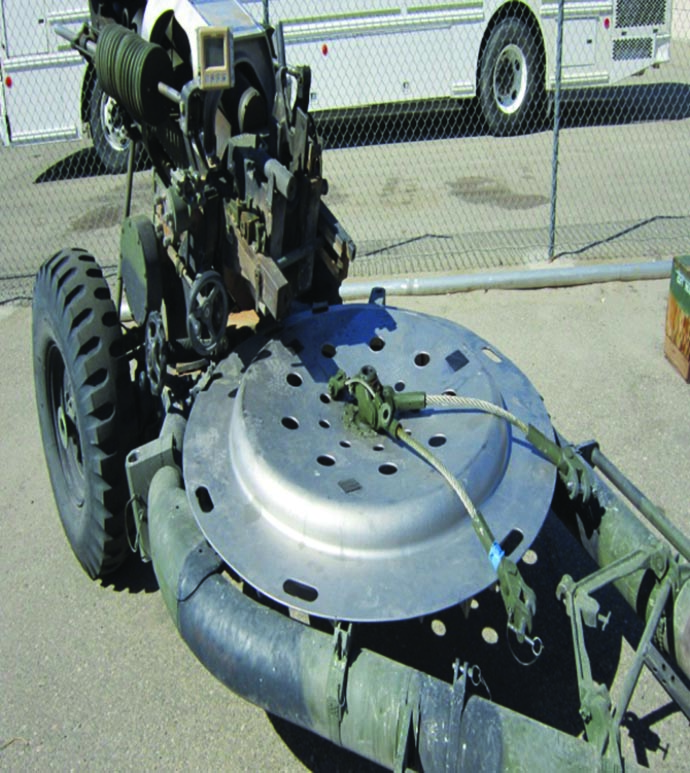
IMPROVED FIRING PLATFORM: This design is a one-for-one swap with the legacy platform. Interconnected ribs replace the spikes found on the legacy platform, increasing the platform strength and preventing excessive platform deformation. Holes are added to the new platform shroud, which improves removal from certain types of soil and shortens displacement times. (Photo courtesy of MAJ Wade Perdue, PM TAS)
CONTRACTING TOOLS
PM TAS awarded the SLOS and the titanium platform base contracts in FY14 as five-year, indefinite delivery/indefinite quantity contracts with firm, fixed-price (FFP) delivery orders. Design West Technologies Inc. of Tustin, CA, is the prime contractor for the SLOS, and Alcoa Howmet of Hampton, VA, is the prime contractor for the titanium firing platform. The ability of the PM TAS/ARDEC team to identify and mitigate performance risk early on by clearly articulating the contract specifications and thoroughly defining requirements has significantly reduced the overall risk to both the government and the prime contractors. These initiatives in turn promoted effective competition, allowing the government to obtain the goal of best value during the source selection process.
An example of how the team reduced technical and performance risk that the prime contractor might have incurred with the FFP contract is through the product technical data package (TDP) and the statement of work (SOW). Before the release of the request for proposals, PM TAS and ARDEC engineers tailored a TDP and SOW for the SLOS and the titanium platform. The TDP and SOW communicated a clear and complete description of the requirements to industry. This detailed approach resulted in lower technical risk and mitigated potential cost overruns.
In addition to reducing performance risk through well-defined requirements, the team implemented both first article testing (FAT) and first article confirmatory testing in the inspection-and-acceptance portion of the contract.
Incorporating both FAT and first article confirmatory testing can provide a number of advantages, including identifying critical design or manufacturing flaws before executing delivery orders with large quantities. The FAT includes the necessary inspections, tests and documentation to ensure that the product characteristics conform to drawings and specifications within the TDP. The first article confirmatory test is essentially a test of production or production-representative articles under realistic field environment conditions, in this case to demonstrate the strength of the SLOS and the titanium platform and validate that the systems meet the contractual requirements.
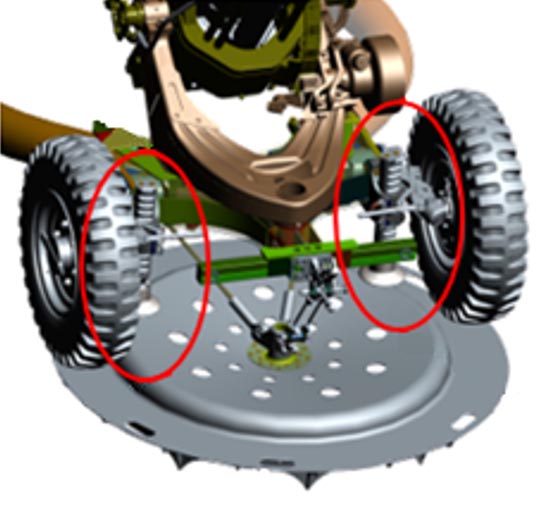
THE SLOS UP CLOSE: The hardware for SLOS has three main components: struts and brackets, a fixed-recoil system and a titanium firing platform. The struts (1) and brackets (2) are lightweight titanium, easily installable and field-deployable mechanisms that attach to the lower carriage of the howitzer. When the SLOS struts are deployed, the system is adjusted so that there is minimal distance from the firing platform. (Image courtesy of MAJ Wade Perdue, PM TAS)
CONCLUSION
Although the Army faces a multitude of uncertainties in the near future from force-structure reductions and resource constraints, the PM TAS/ARDEC team’s ingenuity and commitment to excellence not only improved the reliability, availability and maintainability of the howitzer, but also resolved some highly complex technical issues that have plagued the light artillery community for several years.
One of the most significant aspects of these modifications is to expand greatly on the operational capabilities of the field artillery while using the existing platform. This creative engineering solution allows light field artillery to provide more responsive fires with optimized performance in combat situations requiring high-quadrant elevation and high-charge fires, at a substantial cost savings to the government.
The operational environment continues to be dominated by a hybrid threat and will undoubtedly remain this way. In the future, as in the past, U.S. forces will employ both lethal and nonlethal actions across the continuum of operating environments to safeguard vital national interests. By developing an improvement such as the SLOS and titanium-firing platform, the PM TAS/ARDEC team has set the conditions for light field artillery to meet the challenges ahead.
For more information, contact MAJ Wade Perdue at wade.perdue.mil@mail.mil.
MR. JOSEPH LIPINSKI is the M119A3 product director for PM TAS, Picatinny Arsenal, NJ. He holds a B.S. in mechanical engineering from Lehigh University and is Level III certified in both systems planning, research, development and engineering – systems engineering and program management.
MAJ WADE PERDUE is an assistant product manager for PM TAS. He holds an M.S. in strategic leadership and management and a B.S. in health care management from The College of West Virginia. He is Level II certified in program management and is a member of the Army Acquisition Corps.
This article was originally published in the October – December 2014 issue of Army AL&T magazine.
Subscribe to Access AL&T is the premier online news source for the Acquisition, Logistics, and Technology (AL&T) Workforce.
Subscribe