
By T’Jae Gibson
Shock waves from battlefield explosions are invisible threats for U.S. Soldiers and their top-of-the-line combat helmets, but with new studies in synthetic human physiology, researchers are learning how to lessen blast wave effects on the brain.
Exactly how, and to what degree, these waves cause brain damage is what the U.S. Army Research Laboratory scientists and engineers and a group of university partners are trying to answer as part of a multi-year, multi-disciplinary research project. That research is the focus of the latest episode of “Inside the Lab,” an ARL-produced feature news broadcast.
But in a related research project, Army researchers are investigating new material development for helmet padding systems and from this research, they expect greater insight and innovation in addressing what is likely to be the next big development in head protection: strategies for mitigating the effects of blast.
They’re creating synthetic cranial bones that look and behave like the skulls of 20- and 30- year old Soldiers that will be tested in laboratory experiments that mimic combat-like blast events in hopes of improving military helmet pads, shells, and other protective equipment.
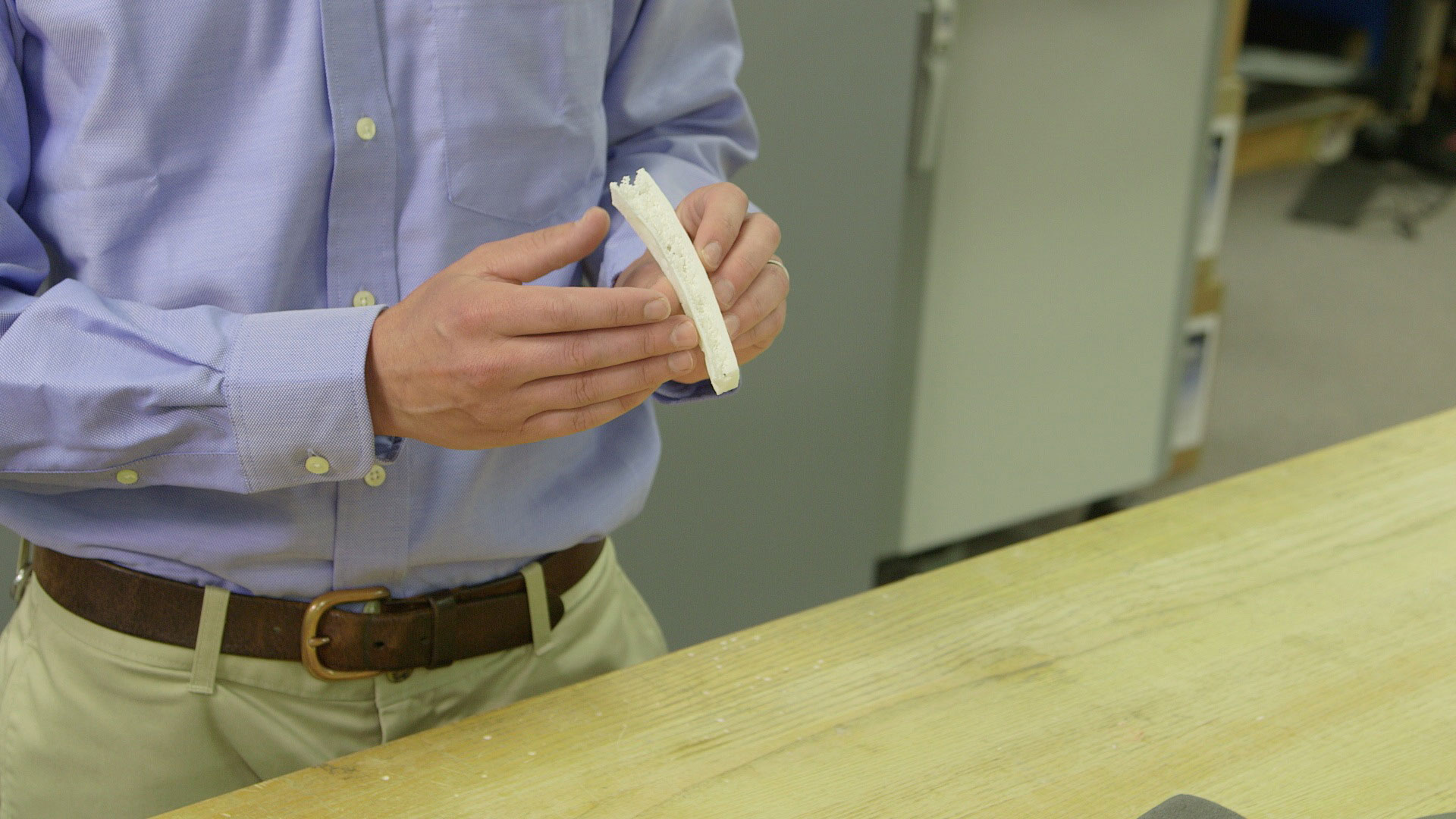
Synthetic cranial bones, as shown here, are being created by the Army Research Laboratory to behave like the skulls of 20- and 30- year old Soldiers’ bones. These stimulants have a highly-graded structure, from a tough outer layer, a spongy inner section, to a more brittle inner layer, which together are responsible for how it responds under impact conditions, Dr. Thomas Plaisted said. U.S. Army photo)
Dr. Thomas Plaisted, materials engineer in the Materials and Manufacturing Science Division at the ARL, said even though synthetic bones are commercially available they’re used primarily by doctors to practice surgical procedures. But, their design prevents them from “behaving like real human bones when subjected to blast tests.”
“The mechanical properties of the human skull change with age and depend on the health of the individual. Donor skulls that may be available for testing would typically come from older people, and the properties of those skulls can be highly variable and may not have the same response as the average skull of the Army soldier population,” said Plaisted.
He said this is among the variables that “add uncertainty when trying to evaluate head protection devices, like helmets.”
“So we are developing our own synthetic bone capturing material and architecture response, specific to the human skull.”
The skull simulant ARL researchers are developing is made of synthetic materials with the goal of creating a uniform response that is representative of the soldier population to use in tests to understand how to best protect the head during exposure to blast waves and blunt impact.
“The cranial bones have a highly-graded structure, from a tough outer layer, a spongy inner section, to a more brittle inner layer, which together are responsible for how it responds under impact conditions, he said.
Slice-by-slice images taken from a CT scan help researchers get the geometry and structure of the skull right. ARL composite materials combined with these images rely on 3D printing technology to produce models of bone-like surrogates that ARL researchers will use to test new helmet padding materials in simulated blast and impact conditions. The goal is to determine how the pads and helmet shell materials protect the head from injury, Plaisted said.
“We are developing new helmet padding materials to improve the impact protection afforded by the Army’s helmets. The helmet can withstand impact at a certain velocity while protecting the head from accelerations that would lead to injury. In the extreme case, excessive acceleration may lead to skull fracture,” he said.
“We are using computer modeling of head and helmet impacts to understand how tailoring the padding properties can reduce acceleration at various impact locations around the helmet. Then, those properties are engineered into materials and tested in the laboratory to validate what we are seeing in the computer models. The research is giving insight on optimal material structures and material combinations that achieve increased energy absorption while still being comfortable to wear.”

Right now, U.S. Army helmets provide the best known defense against ballistic weapons but no one knows how well they can stand up against combat’s most clandestine foe: shock waves. ARL researchers are taking multiple approaches at studying the impact of shock waves inside, on and outside of the skull, and they expect to discover what’s needed to make Army helmets go beyond protecting the head to protecting the brain. (U.S. Army photo)
Earlier this year, ARL evaluated the base material of the synthetic bones by hitting it a high rate, and comparing the fracture properties to human bones tested by the same technique. They’ve determined it to be a “close match” to human bones, he said.
“Our next step is in determining the limits of resolution we can achieve with the 3D printing, and how fine the resolution needs to be to capture the properties we are looking for.”
He said he expects to start printing synthetic skulls with 3D technology by the fall.
“Part of ARL’s mission is to take varying levels of risk in finding state of the art science and developing the technologies that could potentially provide the Soldier with more protection, more capability, or both. What is equally important is that ARL strategically reduce the risk of these new technologies so that RDECs, such as Natick Soldier RDEC, can begin to think about how they would integrate into a larger Soldier “system.” Many of ARL’s material, processing, and conceptual technologies were transitioned and demonstrated in NSRDEC’s “HEaDS UP” program,” said Dr. Shawn Walsh, who leads ARL’s Agile Manufacturing Technology Team .
“[Dr. Plaisted’s] efforts are unique in that he is bringing fundamental material science and modeling to the dual problem of accurately representing biological systems (for example the skull) and coupling this biological model to a materials model to provide better insight on how impulses are transmitted during an impact to the helmet and head. Such insight will lead to new and quantifiably proven methods for reducing the adverse effects of violently applied forces to the head and helmet system,” Walsh said.
View the latest episode of ARL’s “Inside the Lab” here.
Subscribe to Access AL&T is the premier online news source for the Acquisition, Logistics, and Technology (AL&T) Workforce. Subscribe