
By Eric Kowal, ARDEC Public Affairs
PICATINNY ARSENAL, N.J. (Jan. 21, 2015) — By integrating many small sensors into light mortar systems, Picatinny engineers are developing a technology for use on all U.S. military mortar systems to give Soldiers faster, more accurate mortar fire.
The Weaponized Universal Lightweight Fire-Control, known as WULF, couples many small sensors together to create a robust, lightweight pointing device that will increase mortar fire.
How much faster?
An average gun crew is expected to have the 81mm system aimed on target from a dismantled state in four minutes 30 seconds. With WULF, the setup time for the 81mm mortar systems is cut to one minute. The time between shots is reduced from 20 seconds to one or two seconds, increasing the repeatability of shots.
Fire control involves a computer, a pointing device, and gunner’s display to assist in aiming the weapon system.
The WULF allows Soldiers to fire on a target rapidly, up to the full range of the weapon. However, fire-control systems were previously limited to the 120mm tube because the sensor box is too large and heavy for the 60mm and 81mm mortar systems.
Picatinny engineers Michael Wright and Ralph Tillinghast from the Armament Research, Development and Engineering Center, saw a solution with WULF. They created a fire control using a sensor that can perform like the larger fire-control systems, yet small enough to work on all three mortar platforms.
This smaller sensor is consistent with the Army’s strategic goal of lightening Soldier load.

With WULF, Soldiers will use a hand-held computer to digitize the mortar weapon system, calculating ballistic solutions, determining where the weapon needs to be pointed to hit the target, and will see an increase response time and repeat fires while decreasing the chance for error. (Photo by Todd Mozes)
Soldiers currently use man portable mortar systems with the Lightweight Handheld Mortar Ballistic Computer, which allows Soldiers to calculate ballistic solutions, where the weapon needs to be pointed to hit the target, but uses World War II-era optical sight components for aiming.
WULF modernizes aiming by digitizing the weapon system to increase response time and repeat fires while decreasing the chance for error.
The 150-pound fire-control system on the 120mm system is now reduced to 10 pounds overall, according to Tillinghast. He is the lab director of the Collaboration Innovation Lab, Mortar Common Fire Control Systems Division of the ARDEC Fire Control Systems and Technology Directorate.
Tillinghast and Wright have worked on WULF for about five years. They discovered that a combination of several technologies would make the system work with smaller mortar systems.
“When we started to approach the problem of developing a small, lighter fire control system it became clear early on that the current methods for pointing the weapon system (Laser Ring Gyro) could not be reduced in size enough to be practical,” said Wright, ARDEC Project Officer for WULF.
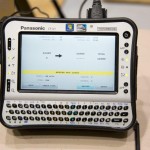
With WULF, Soldiers will use a hand-held computer to digitize the mortar weapon system, calculating ballistic solutions, determining where the weapon needs to be pointed to hit the target, and will see an increase response time and repeat fires while decreasing the chance for error. (Photo by Todd Mozes)
“With WULF we started from the ground up, by coupling many small sensors together to create a small, robust, lightweight pointing device,” Wright said. “As we would add one sensor we would see a flaw in that sensor (magnetic instability, gyro drift, sensor saturation) and add another sensor to correct for that problem.”
Five technologies come together to make WULF’s pointing device work: a magnetic compass, a forward facing optical camera, Micro-Electro-Mechanical (MEM)s gyroscope, MEMs accelerometer, and a celestial compass. A celestial compass is expected in the next generation of WULF, which will significantly increase an accuracy rate that is already high.
“The problem with magnetic compasses is that they will point at anything magnetic, so changes in the environment would throw off the reading, sometimes completely unknown to the user,” Wright said.
“To combat this flaw, the MEMs gyro’s and accelerometers were integrated into the system to detect whether a change in heading was caused by tube movement or magnetic influence, allowing us to detect a magnetically anomaly,” he said. “The optical camera was added to stabilize and correct for drift that is inherent to accelerometers and gyroscopes of such a small size. By integrating all the sensors together we were able to create a pointing device that rivals the bigger units, but at a tenth the cost and size.”
The most significant advance of the sensor system was optical tracking. Using technology and algorithms designed by a commercial company, Inertial Labs, during a Small Business Innovation Research effort, the optical tracking not only corrected for drift in the gyroscopes and accelerometers, but to also allow tracking after a firing event when other sensors may not function for a second or two.
The optical system works by dynamically creating known features in a reference image. When these features are seen again, the system knows the heading at which that image was taken, and can realign all sensors back to an accurate reference. As the system is used, hundreds of reference frames are created, allowing the system to track almost purely on optics, if needed, for a short time.
“Setting up the first shot and the time between shots will decrease significantly,” Tillinghast said.
WULF started as a concept in the Collabortaion Innovation Lab and was awarded funding through ARDEC’s Technology Exploitation, Exploration and Examination program and then evolved into a Systems Concept and Technology project. WULF’s transition to a U.S. Army project manager is expected in fiscal 2017.

U.S. Army Pfc. Gregory Conway, left, prepares to drop a mortar into the tube during a live-fire training exercise at a range several miles north of Forward Operating Base Hammer, Iraq, Sept. 30, 2009. Conway is an indirect fire infantryman assigned to the 82nd Airborne Division’s Company C, 2nd Battalion, 505th Parachute Infantry Regiment, 3rd Brigade Combat Team. (Photo by Pvt. Jared N. Gehmann)
This article appears in the January/February 2015 issue of Army Technology Magazine, which focuses on sensors research. The magazine is available as an electronic download, or print publication. The magazine is an authorized, unofficial publication published under Army Regulation 360-1, for all members of the Department of Defense and the general public.
The Armament Research, Development and Engineering Center is part of the U.S. Army Research, Development and Engineering Command, which has the mission to develop technology and engineering solutions for America’s Soldiers.
RDECOM is a major subordinate command of the U.S. Army Materiel Command. AMC is the Army’s premier provider of materiel readiness–technology, acquisition support, materiel development, logistics power projection and sustainment–to the total force, across the spectrum of joint military operations. If a Soldier shoots it, drives it, flies it, wears it, eats it or communicates with it, AMC provides it.
Subscribe to Access AL&T is the premier online news source for the Acquisition, Logistics, and Technology (AL&T) Workforce.
Subscribe