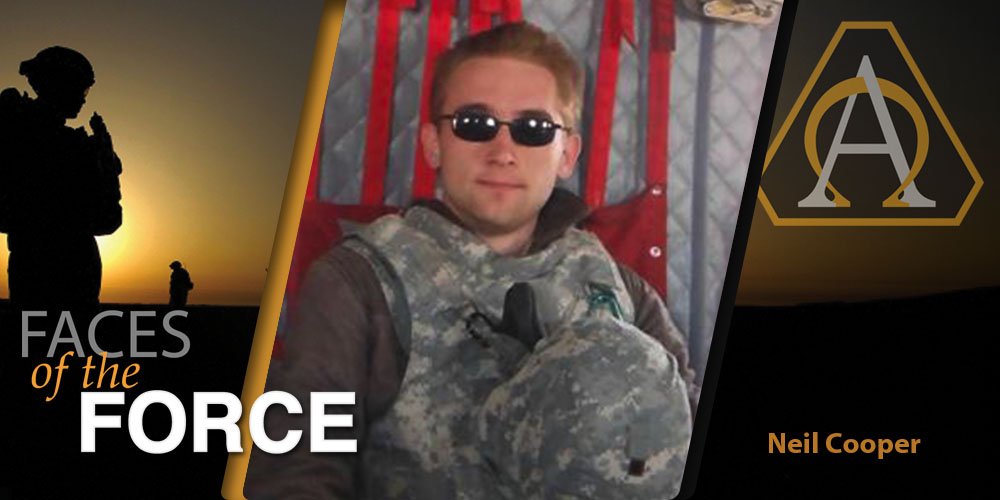
Faces of the Force: Neil Cooper
POSITION: Systems Engineer
UNIT: Project Manager Mobile Electric Power (PM MEP), Program Executive Office Combat Support and Combat Service Support, Warren, Mich.
TOTAL YEARS OF SERVICE: 3
EDUCATION: Oakland University B.S.E., mechanical engineering
DEPLOYMENTS: Afghanistan, 2013
By Steve Stark
Neil Cooper is an engineer who spent several months deployed to Afghanistan performing power assessments of austere base camps in support of Project Manager Mobile Electric Power (PM MEP) and its effort to “right size” mobile power equipment. In an unusual twist, Cooper deployed while he was an intern in the TARDEC [U.S. Army Tank Automotive Research, Development and Engineering Center] intern program. ”I was told they do not deploy interns but after some research I found it was possible,” he said in an interview. Prior to his deployment, he had been working on modeling and simulation of expeditionary contingency bases.
Cooper was working two projects, designed to “investigate the implications of changes to systems and how they impact the logistic system and the resource demands of bases. The CBI [Contingency Base Infrastructure] effort’s initial focus was on 50, 300 and 1,000-Soldier bases. We modeled and simulated changes to these bases to see what effect changes to base systems would have on resource consumption using a system-of-systems approach.” In a framework developed by Sandia National Laboratories, he said, “we modeled laundry, vehicles, repair parts, repair times, generators and any kind of system we could with scientifically sound data,” that could affect resource consumption.
“You can have many different systems, [included in the simulation] run it thousands of times and get a picture of how resources are used.” In effect, modeling and simulation, Cooper said, helps to validate or invalidate assumptions using vetted data—a crucial step in the planning effort. According to Cooper, the practice could significantly aid acquisition decisions, no matter what the system, by helping to evaluate and inform requirements in every aspect of acquisition. Then, when acquiring a system, the program would have real data that the system would meet the mission. “After modeling bases on their own, we began to look at how the changes to the sustainment concept or one base affect another base with the JOEI [Joint Operational Energy Initiative].
“At a JOEI meeting at Fort Lee,” Cooper said, “we saw an operational needs statement (ONS) stating that the way we do power distribution at contingency bases is inefficient, and there is a lack of a champion tasked with optimizing bases. I expressed to my supervisor an interest in working on this. I wanted to work on a project using my experience to directly improve things for the warfighter.” While he was working with JOEI, Cooper said, his supervisor was on a telephone conference in which it came up that PM MEP needed a volunteer to go to Afghanistan to help fulfill this ONS, “So I volunteered.”
He got a week’s worth of training on “military generators, power distribution and environmental control equipment, and the software to determine the right sized generators and distribution systems you need along with the best way to hook them up,” he said. Then he went to Bagram, Afghanistan to help units quantify their energy consumption, and provide support in upgrading their assets from older commercial units to newer, more efficient and supportable military equipment.
Helping units right-size and optimize their generation not only helps reduce logistics burdens, it also improves the quality of life for the Soldiers, Cooper said. The improvement in quality of life included replacing broken air conditioning equipment and sizing it correctly so it works like it should. “Reducing the logistics footprint,” Cooper went on, provides additional help to Soldiers because it “translates to fewer convoys transporting fuel and equipment, which translates to fewer to fewer Soldiers being placed in harm’s way.”
In his position, Cooper designed plans for power, distribution and environmental equipment for expeditionary bases, including small special operations “village stability platform” bases that often support fewer than 50 people. Designing the grids, he said, means “determining the best way to design the power grids on expeditionary bases so that generators are used as efficiently as possible and all systems get the power they need.”
FOTF: What do you do in the Army? Why is it important?
COOPER: I support the force by providing engineering support to PM MEP, which is fielding the latest generation of tactical mobile electric power and environmental control units. These units are more efficient and supportable than legacy units that have been in use by the troops in Afghanistan. At many bases, equipment has been added and removed over time creating inefficient power grids with little attention being paid to the operational energy aspects of these actions. U.S. Forces – Afghanistan has recognized the issue and created multiple operational needs statements to address it.

A Sikorsky CH-53E Super Stallion, a heavy-lift cargo helicopter, delivers a replacement generator to a contingency base in Afghanistan. Throughout his deployment, Cooper helped units right-size and optimize power grids to increase generator efficiency and ensure all base systems get the power they needed. (Photos by Neil Cooper)
FOTF: What has your experience been like so far? What has surprised you the most?
COOPER: My experience has been great and has taught me many things. As an intern and co-op, I’ve worked as a staff engineer in a program executive office; a program engineer for a product manager of a Milestone C program; an engineer on a Pre-Milestone A program; and in Afghanistan as power assessment engineer working directly with Soldiers and Marines in their operational environments directly supporting and improving their capabilities to operate.
Stopping to reflect on this, the thing that surprises me the most is how little the American public knows about our world. We [the Army] are the largest employer in the world, but most of the general public has no idea about what we do and how the government acquisition system works.
FOTF: Why did you go to work for the Army? What is your greatest satisfaction in being part of the Army?
COOPER: I began working for the Army in 2010 as a co-op [in what is now the Presidential Pathways Internship program] halfway through earning an engineering degree. At a job fair, I met someone from TARDEC, and she asked me to send her my resume. Three or four months later the phone rang asking me to come in for an interview. They presented me with an offer I couldn’t refuse: “We will pay for the rest of your college and, also, if you do a good job, offer you a job on graduation.” At the time, I had no real grasp of how large the world of government acquisition was and, over the years, I’ve gained a great appreciation for how much our acquisition workforce is capable of accomplishing and how much we help the warfighter by developing and fielding so many different items that affect every aspect of his or her life and how we are always striving to provide better materiel support to the force.
FOTF: What was your deployment like?
COOPER: I deployed to Afghanistan from January to June this year. I was based out of Bagram for a couple weeks and then in the remote Paktika province from mid-January through the end of February. I went back to Bagram for a week before going to Camp Leatherneck in March through the end of June. In that time, there was a lot of bouncing around to small bases in the area. Volunteering to go, my thoughts were to do something like this while I’m young without any serious responsibilities at home.
Before traveling to Afghanistan, the threat was a concern. While there is a threat present, it wasn’t as bad as I had imagined. Also, the living conditions were better than expected. I envisioned living in a tent and eating MREs, [meals ready-to-eat] but it was more like living in a bloc apartment complex at the beginning. It was interesting and a good opportunity to gain experience.
FOTF: What was your most memorable day?
COOPER: The day I found out the first VSP [village stabilization platform expeditionary base] power grid design-and-push package I created on my own worked. It’s kind of an architectural diagram of power, distribution and environmental equipment for something like a small campus. We sent it out to our guys and they would call every day and give us a status, and the design succeeded. That was a good day.

Cooper’s convoy travels through the Afghanistan terrain on its way to a contingency base earlier this year. Cooper visited several bases in support of Operation Dynamo to maximize energy efficiency, reduce the logistics footprint, and improve the quality of life for Soldiers. (Photos by Neil Cooper)
- “Faces of the Force” is an online feature highlighting members of the Army Acquisition Workforce. Produced by the U.S. Army Acquisition Support Center Communication Division, and working closely with public affairs officers, Soldiers and Civilians currently serving in a variety of AL&T disciplines are featured every other week. For more information, or to nominate someone, please contact 703-805-1006.