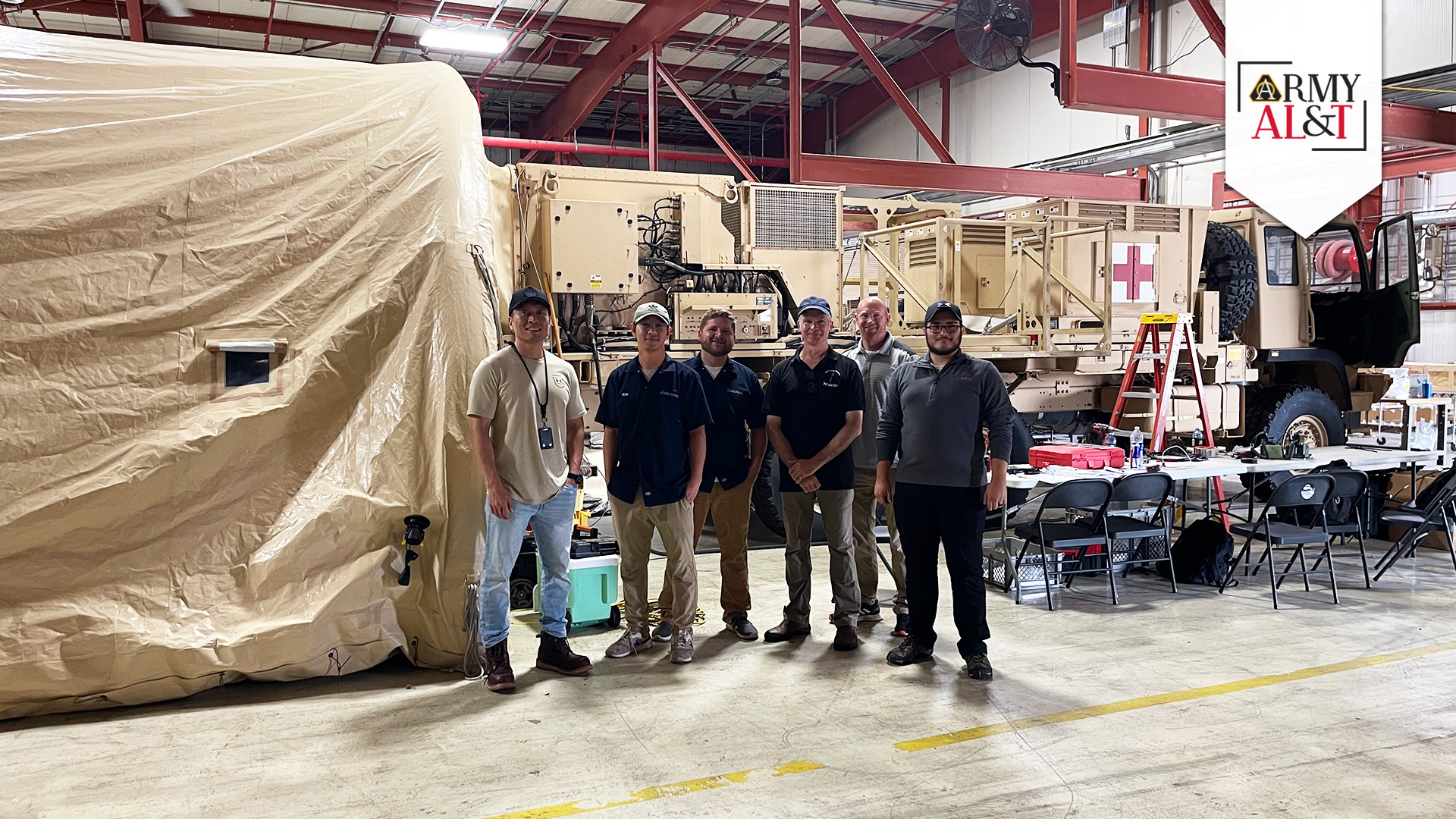
UP TO THE TASK: The Army’s Handheld Manpack and Small Form-Fit platform integration team is responsible for Next-Gen radio platform integration across the force, including a recent effort at Pine Bluff Arsenal, Arkansas, for a M1085 vehicle pilot build. The team’s engineers incorporated 3D CAD software and other modern tools to digitally build TDPs, all hosted on the Army’s ePDM framework as part of the Army’s digital transformation effort. (Photo by Htay Thet, U.S. Army)
by Fred Kelso, Kenny Lee and Jack Schaefer
Did you know that the U.S. Army has hundreds of vehicle variants and that each one needs a custom-designed and custom-built kit to mount its radios? Add to this the reality that the Army also carries multiple radio types, originally designed to be hand-held or carried in rucksacks and produced by several different vendors, and it’s easy to see how managing the design, production, testing and installation of these kits (a process known as integration) presents a challenge for the engineers and logisticians who must routinely ensure that every kit fits and works perfectly across the Army’s diverse portfolio of vehicles.
The Army’s Handheld, Manpack and Small Form Fit (HMS) platform integration team is tackling these challenges by moving out of the analog age and into the digital age, aligning their processes with the goals of Army Directive 2024-02, “Enabling Modern Software Development and Acquisition Practices”—particularly the need to “accelerate the Army’s digital transformation to deliver needed capabilities to Soldiers.
The scope and magnitude of the efforts required from the integration team for the Army’s HMS tactical radios gradually increased over many years until it suddenly exploded with the advent of the Next-Generation (Next-Gen) radios. In addition, radio fielding needs are subject to short-notice changes due to real-world conditions. In the face of these complex challenges, increased efficiency became imperative to maintain the flexibility needed for kit design and production.
PLATFORM INTEGRATION CONCEPT OF OPERATIONS
The first step in designing a Next-Gen radio installation kit is to get boots on the ground who can perform hands-on engineering work by evaluating space constraints, cable routing paths, available power sources and any potential impediments to successful integration. Depending on the scope of the work, the team may also decide to build and install a prototype kit based on the initial engineering findings to work out any remaining kinks in the design.
The designs vary by mission, as sometimes our kit designs include ancillary equipment for the special needs of the warfighters. For instance, Soldiers in a medical unit may need to take their tent-based chem-bio shelter off their vehicle and deploy it in a hazardous environment; once inside the protective shelter, however, they have typically been unable to access their radio controls. To solve this, the integration team added a keypad display unit to the shelter, connected by a very long cable to the radio in the cab of the truck. This kit design enhancement, added during a recent engineering trip to Pine Bluff Arsenal, Arkansas, will allow Soldiers to operate their Next-Gen radio inside their shelter while the hazard persists.
Once the kit configuration and integration details are laid out, technical data packages (TDPs) can be built. Currently, the HMS Platform Integration team maintains about 100 different TDPs covering vehicle installation kits for two Manpack (rucksack) radio variants and two Leader Radio (hand-held) variants. When maximum communication capabilities are needed, roof space may be required for five or more antennas, with cables from each antenna running back to the radios, while additional pieces of hardware are needed to make the system fully functional. Furthermore, cable routing on any platform can be challenging, as antennas must be far enough apart to preclude electromagnetic interference and safety hazards, and most platforms were not designed to accommodate future cabling requirements.
Given all this equipment complexity, the TDPs themselves can be quite challenging, requiring numerous part drawings, many of which are used across multiple TDPs.
SWITCHING OUT THE TOOLBOXES
To simplify the process, the integration team kicked off a digital transformation initiative, which includes the current effort to update all legacy TDPs, using a new toolbox. The old toolbox was inefficient and error-prone. That’s because it consisted of 2D computer-aided design (CAD) software, PDF software to save drawings and data sheets, email to share files and conduct engineering change control and the use of spreadsheets for configuration management—which, taken together, meant that revisions to a single drawing necessitated manually replacing the relevant pages in the TDP PDF package, sometimes across dozens of kit designs.
For example, reliance on the 2D software required the team to first identify which structural members of an equipment rack shouldn’t be painted and then take the time to mask those areas before painting. What’s more, an incorrect reading of the drawing could lead to improper paint application, which would result in rework and schedule delays. Utilizing 3D models will make part details, such as the areas to be masked, much more visible.
By incorporating these digital transformation efforts, the new toolbox will feature the latest 3D CAD model format and an enterprise Product Lifecycle Management (PLM) library to digitally build TDPs with built-in revision controls—all hosted on the Army’s enterprise Product Data Management (ePDM) framework.
Industry has long been using ePDM to protect designs and improve efficiency, and now the Army will reap similar benefits. For example, by using the PLM software on the new platform, the team can complete two legacy TDP updates in just three weeks, compared to the three or four months it took with the old. What’s more, it tracks the latest revisions of all drawings and incorporates them into each new legacy TDP update. The PLM’s engineering change request function also enables the team to efficiently initiate, manage, review, approve and release engineering change proposals entirely through the software. And most importantly, it allows for more than one person to make changes and update the component, which ensures that the component cannot move to the next revision level without going through this process.
Now that the team is using ePDM for the radio kits with 3D modeling software, they are seeing increased efficiency and reduced downtime, while maintaining the highest quality for our products and TDPs.
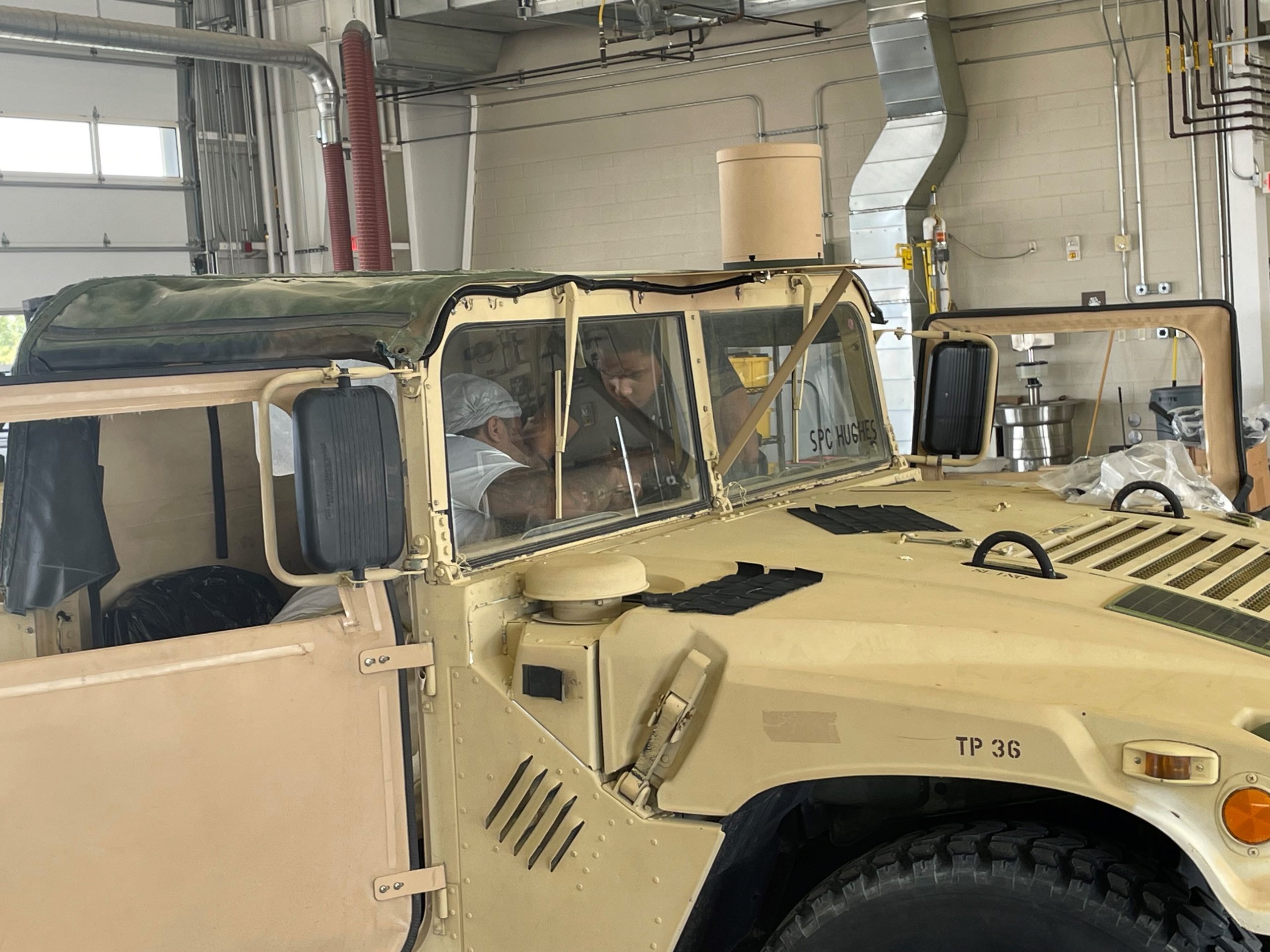
RIGHT FIT, RIGHT VEHICLE: Technicians with Program Executive Office for Command, Control, Communications and Network’s (PEO C3N) Project Manager Tactical Radios organization install a new radio into a High Mobility Multipurpose Wheeled Vehicle in August 2024 at Fort Bliss, Texas. Managing the design, production, testing and installation of radio kits requires engineers and logisticians to routinely ensure a perfect fit across the Army’s diverse portfolio of vehicles. (Photo courtesy of Project Manager Tactical Radios, PEO C3N)
CONCLUSION
Digital transformation is a key component to the Army’s modernization strategy, and it is now playing a vital role in ensuring that HMS Next-Gen radios continue to deploy across the entire Army vehicle portfolio, including a large number that are being integrated onto Army rolling stock. The added efficiencies and enhanced engineering change and configuration management processes enabled by transitioning from an analog to a digital TDP design and maintenance framework is making the entire radio-vehicle integration process more efficient, quicker and less prone to errors.
While the magnitude of ensuring that the right radio gets installed in the right way across hundreds of vehicle variants may seem daunting, we are committed to managing our efforts down to the single configuration item to ensure that every Soldier has access to the radio he or she needs, when they need it.
For more information on HMS radios, go to https://peoc3t.army.mil/Organizations/PM-Tactical-Radios/Handheld-Manpack-and-Small-Form-Fit/.
FRED KELSO was a platform integration engineer with Project Manager Tactical Radios within PEO C3N from August 2022 to October 2024 and currently works in Command, Control, Communications, Computers, Cyber, Intelligence, Surveillance and Reconnaissance’s Manufacturing Readiness/Industrial Base branch. He holds an M.S. in civil engineering from Johns Hopkins University and a B.S. in aerospace engineering from Penn State University. He is a DAWIA Certified Practitioner in engineering and technical management.
KENNY LEE is a mechanical engineer with the Platform Integration branch of Project Manager Tactical Radios within PEO C3N. Following his service in the U.S. Navy, he earned a B.S. in mechanical engineering from George Mason University.
JACK SCHAEFER is a platform integration systems engineer with the Platform Integration branch of Project Manager Tactical Radios within PEO C3N. He holds a B.S. in mechanical engineering from the University of Maryland-Baltimore County.