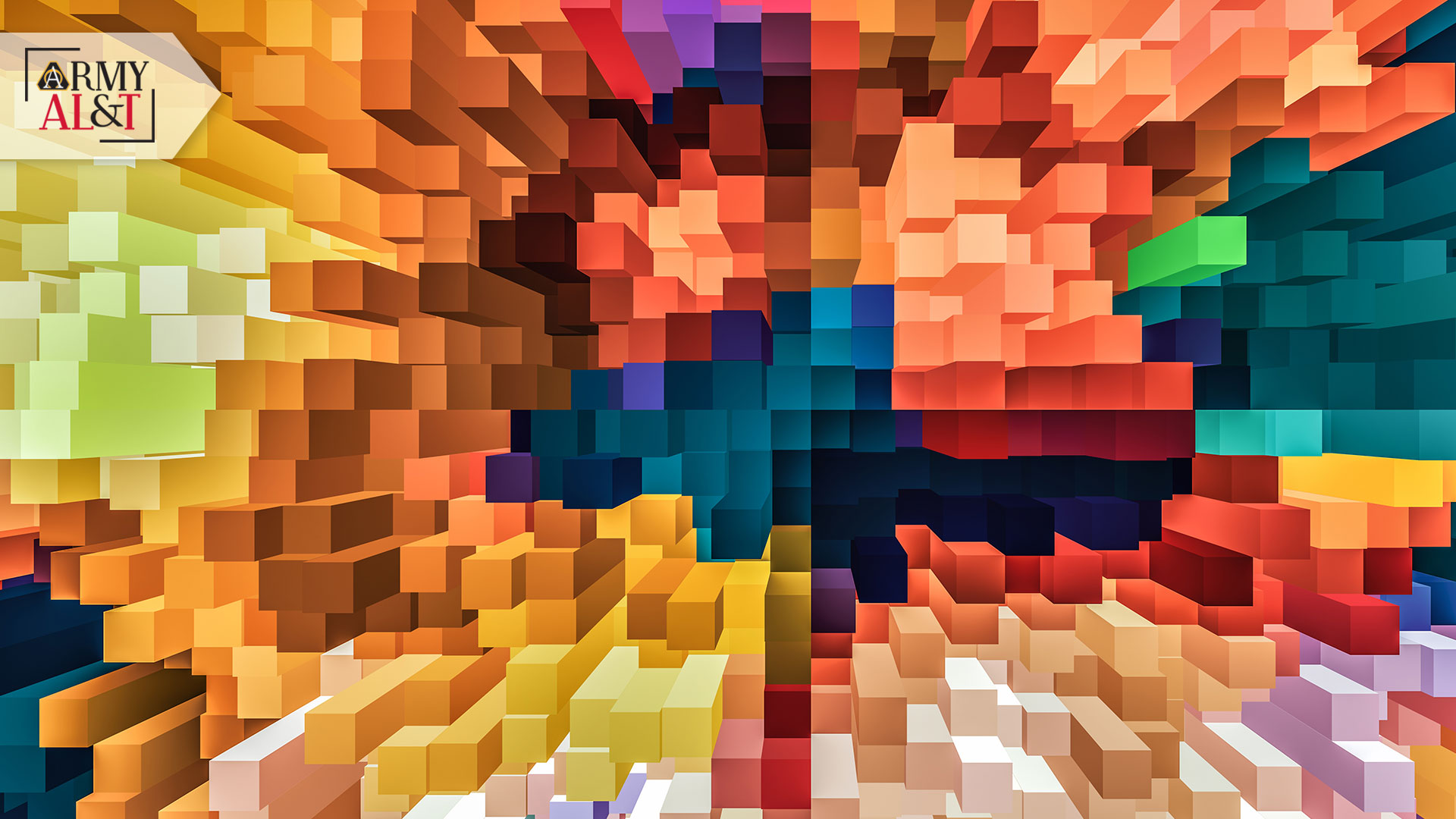
Sidebar to Complex Geometry
By Steve Stark
Additive manufacturing demands a whole new way of thinking, and we’re not even close to what’s possible in this exciting technology.
One of the best ways to understand how different the approach has to be for additive manufacturing is to think of objects as things that exist in space—volumes. The designer also needs to think of the capacity of the machine as the volume that contains the printed object’s volume, because, for the most part, the object can be no larger than the printer. (That’s “for the most part” because in some cases, printed objects can be larger than the printer, and there are robotic printers that can print in free space, subject to the law of gravity, at least on Earth. But each is still a volume in terms of design.)
The geometries of that volume can be quite precise and quite complex. They can also be simple. Additive doesn’t care. The software used for printing an object breaks it into slices; each object is made up, essentially, of stacks of slices. Each of those slices, in turn, is made up of voxels. To understand the concept of the voxel, it’s a portmanteau word, a mash of volume and pixel.
Those voxels can be as small or as large as the design requires, but they have to be within the capability of the machine that will print the design.
“When you break a volume into essentially three-dimensional pixels, the idea would be that each voxel—each pixel within your volume—could have different properties because either it’s a different material when we’re mixing materials, or alternatively we’re modulating materials,” said Dr. William Benard, senior campaign scientist in materials development with the U.S. Army Research Laboratory in Adelphi, Maryland. “For example, dynamic alloying, or even changing the properties of a particular alloy by modulating the process as we print.” In other words, to add particular properties to the object, a printer could deposit different types of metals in close proximity, and they’d be alloyed as a laser melts them.
“You already have some degree [of control in manipulating materials] in conventional manufacturing, and so we’ll profile the material at different places,” Benard said. “When you cast something, it’s not going to be identical, but you don’t have very much option to control it. It’s largely a function of the process and the part geometry. There are some things you can do to sort of nudge [the material] here and there. But with additive, there’s really this unprecedented potential.” To have real control of each voxel, he said, “is really far down the road.”
This is not only about shapes but also about the composition of materials and the deliberate blending of materials to gain a particular result. The desired goal, Benard said, is “that the material might perform a substantively different function. So a good example is in electronics packaging. We may print a volume that has both conductive elements and dielectric elements.”
Dielectrics, Benard said, are materials that both resist against electricity and have some capacity to store it. What interests scientists about dielectrics is what is known as the dielectric constant and the strength of the dielectric. “We care about both,” he said, “but we care about the dielectric constant for the design of the normal operating performance of a device (antenna, capacitor, etc.), while the dielectric strength sets the operating bounds—essentially how much charge we can safely apply before the device fails catastrophically.”
With that in mind, he said, “We might place a microchip and then print around that to get a solid volume, which would make it much more mechanically robust. We could print in the electrical contact as part of the volume, as opposed to having it be a discrete wire.”
That means that additive manufacturing has the potential to “design electronics with embedded antennas, for instance. So we can use … metal traces to now make antennas.
“But we may want different dielectrics, and now we’re going to use different-property materials on the dielectric side, depending on what the properties of the antenna need to be. There have also been demonstrations of embedding things like wave guides. That can be optimal wave guides, akin to a fiber, and these can all be embedded in a structural member. So you could theoretically use glass fiber both as a reinforcing agent, to make the member stronger but also for optical communications at the same time.”
But as wonderful as that flexibility and manipulability of materials in design sounds, Benard was quick to caution that we’re not there yet, because creating such structures also brings in variables that have to be foreseen.
To illustrate that in the context of the antenna, he said, “I’m using my fiber optic as a structural member, but I’m also using it for communications. But now, as I strain the lever arm that it’s reinforcing, that may modulate the properties of the fiber, which will affect my communications. It gets into a very complex space. It gives lots of opportunity for high performance. There’s also a lot of opportunity for unintended consequences.”
For Benard, one of the most important things that the Army can do as it moves forward with additive manufacturing is to create the digital design tools that will be necessary for structures that are complex not only in their geometry, but also in materials. That’s why “we’re building digital design tools to help manage that complexity and help understand what the impacts are going to be,” he said.
Because of this approach to an object as a volume, giving designers the inherent ability to digitally explode it into a million or more tiny voxels, “there’s all kinds of functions and ways you can build these in all different sizes and scales.” There’s “a lot of opportunity, but also a lot of complexity that you’ve now got to manage on the design side. Very exciting, but very challenging at the same time.”
This article is published in the January – March 2019 issue of Army AL&T magazine.
Subscribe to Army AL&T News – the premier online news source for the Army Acquisition Workforce.
Subscribe