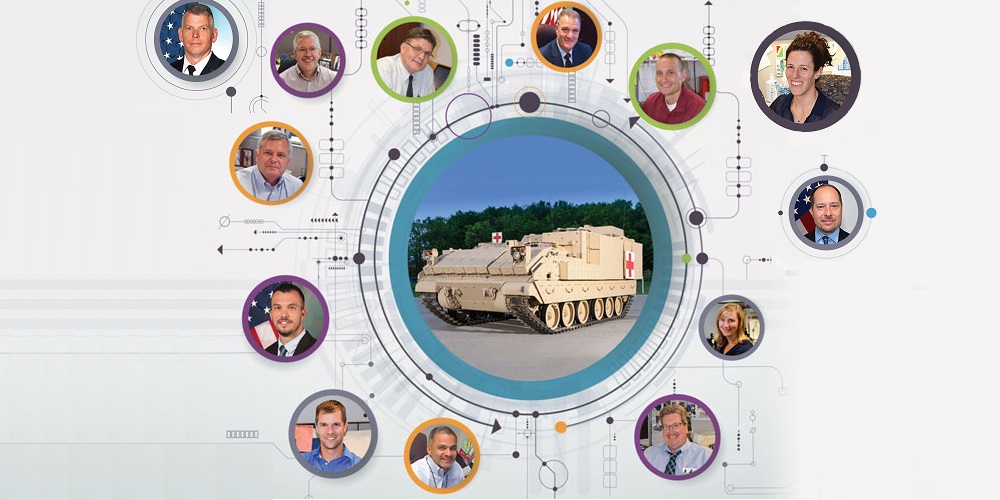
From the Director, Acquisition Career Management
Lt. Gen. Michael E. Williamson
To deliver complex capabilities to the warfighter takes a lot of different players, all focused on the same mission.
We often hear that “people make a difference” and “relationships matter.” Well, in Army acquisition those statements are the very foundation of successful programs. Strong leadership, clear communication, focused teamwork and the resulting bonds of trust—within the program office and with stakeholders—are vital in procuring and fielding capabilities that enable our warfighters to fight and win decisively.
There are many success stories about meeting the needs of our warfighters through teamwork. One that comes quickly to mind is the Joint Mine Resistant Ambush Protected (MRAP) Vehicle Program. MRAP was fielded in unprecedented time to U.S. and coalition forces to provide protected mobility and force protection from improvised explosive devices and other threats. The Joint MRAP team, the Joint MRAP enterprise, delivered highly survivable vehicles that saved lives—more than 27,000 lifesaving vehicles delivered in less than 5 years!

A UNIVERSE OF KNOW-HOW
The AMPV program requires expertise from a vast array of specialties to succeed, including but hardly limited to the knowledge and experience of these AMPV team members: from left, Deputy Product Manager for Integration Ed Lewis; Lead Systems Engineer and Systems Engineering Branch Chief Corey DeSnyder; Director of Engineering Kevin Houser; Deputy Project Manager Tom Landy; and Lead Cost Analyst and Operations Research Analyst Ryan Lasecki. (U.S. Army photo courtesy of PEO GCS)
In December 2009, then-Joint Program Manager Paul D. Mann wrote, “No matter how cliché our continued pronouncement of the importance of teamwork is … we will not let the Warfighters down … we will Rock and Roll our way to victory.” He continued, “The ultimate team sport is fed by the ultimate irony: team excellence springs forth from individual excellence when underpinned by an unquenchable pursuit of being a great teammate and building trust throughout the Enterprise! Our most effective teams and most dramatic progress are evident as we practice these principles in all of our affairs.” (Note: Mr. Mann is now a member of the Senior Executive Service and executive director of the White Sands Missile Range in New Mexico.)
My focus for this column is on the people behind the Army’s new Armored Multi-Purpose Vehicle (AMPV), which is in development for the armored brigade combat team (ABCT). The AMPV family of vehicles consists of five variants to resupply the formation; conduct battle command functions; deliver organic indirect fires; provide logistics support and medical treatment; and perform medical and casualty evacuation. What AMPV will mean to future warfighters is enhanced force protection, survivability and mobility, as well as the power of situational awareness from an inbound Army network and other future technologies.
With nearly 50 stakeholders, including officials across the Army, the Office of the Secretary of Defense (OSD), the Office of the Chairman of the Joint Chiefs of Staff, the Defense Contract Management Agency (DCMA), Congress, the manufacturer and contractor BAE Systems and the user-Soldier, the AMPV program is on budget and on schedule to meet the first prototype delivery in December. Here is a look at some of the professionals who comprise the AMPV team.
THE TEAM IN ACTION
The AMPV Project Manager, Col. Michael “Mike” Milner, has been project manager (PM) since 2014, and as such has overall responsibility for the program’s performance, cost and schedule; workforce development; and communication with all stakeholders. To lay the groundwork for program success, he established and communicated a common vision of the program. He also worked closely with the Army staff to manage requirements that challenged the program’s intent. “Working with my peers to prepare the Army position on requirements adjustments,” he said, “enabled us to balance the performance, cost and schedule of the program through the Army Requirements Oversight Council [AROC], which is chaired by the Army chief of staff.”
Milner, who works for the Program Executive Office for Ground Combat Systems (PEO GCS), maintains regular contact with stakeholders when visiting various locations, namely the Pentagon, Fort Benning, Georgia, and others, to continuously communicate the status of the program, maintaining transparency on where the program is headed and requesting support or guidance when and where needed. “Open, honest, transparent and frequent communication of program status and how stakeholders can support us is a major factor in the program’s success,” he said.
His prior assignment as the portfolio manager for combat vehicles in the Office of the Assistant Secretary of the Army for Acquisition, Logistics and Technology (OASA(ALT)) enabled him to establish contact with stakeholders and understand the Army’s intent for the AMPV program from the beginning. “This allowed me to advance the program in the face of requirements challenges that I felt were outside the intent the Army had for the program,” he said. “The relationships developed and maintained allowed the program to find common ground and work through the challenges to balance the performance, cost and schedule.”
With 28 years of service in the Army and 17 years in the Army Acquisition Corps, Milner is Level III certified in both program management and contracting. He has an MBA from Clemson University and a master of strategic studies from the U.S. Army War College, in addition to a BBA in marketing from Georgia State University. In his first acquisition job as a contingency contracting officer with U.S. Army South in Puerto Rico, he learned the importance of flexibility and teamwork in developing requirements and supporting the mission.
When he became product manager for Excalibur, he learned the power of stakeholder support and the ability of his team and the contractor to formulate and execute plans when the chips were down—a software failure disabled all the projectiles just days before the initial operational test and evaluation (IOT&E). While waiting for a flight, Milner received a call from his deputy, who, working with the contractor, came up with a plan to retrofit the munitions. This would require them to be shipped, broken down, updated, reassembled and returned to White Sands Missile Range for testing.
Milner was pleased that, in the absence of details, his leadership supported him. “When I briefed the Operational Test Command officials, the test community dove into the problem and laid flat every issue associated with the repair of the rounds,” Milner said. “In the end, we started IOT&E three days late and completed on time. It was a great example of an extended team coming together to solve a complex problem.”
His advice to others in the Army Acquisition Workforce is to remain flexible and know that the system is adaptable. “While, from the outside, the acquisition process might seem rigid, it is actually very flexible,” Milner said. “But, in order to exercise that flexibility, you have to establish trust with the stakeholders responsible for oversight to ensure you are doing the right thing for the Soldier and the taxpayer. Trust your team. They are smart. Point them in the right direction and adjust as needed. Give them the resources to succeed.”
AMPV Deputy Project Manager Thomas “Tom” Landy, a civilian with more than 25 years of experience in program management, was competitively selected for the position in June 2014. At this stage of the program, his primary stakeholder interactions are with officials at the U.S. Army Training and Doctrine Command (TRADOC) Maneuver Center of Excellence (MCoE) regarding requirements issues and with acting Deputy Assistant Secretary of Defense for Systems Engineering Kristen Baldwin regarding programmatic assessments of systems engineering reviews.
Landy’s approach to successful stakeholder involvement is based on PEO GCS’ command philosophy:
- Fundamentals—Maintaining integrity through solid engineering and design analysis, and test planning that balances cost, schedule and performance risk.
- Transparency—A willingness to be open about emerging issues and look to stakeholders as assets for assistance in resolving the issues before they can impact the program.
- Realism—Establishing realistic schedules and expectations, and meeting them.
Landy points out that stakeholders share a common interest—the success of the AMPV program. “Our relationships have evolved over time from one of ‘oversight-audit-problem finding’ to one of collaborative identification and resolution of issues,” he said. “Our stakeholders help the AMPV program proceed while meeting the intent of acquisition policy and regulations, and they work well with us to tailor expectations when taking into account some of the fundamental assumptions of the AMPV program.”
As an example of efficiency, he noted that the AMPV Product Assurance and Test Directorate’s efforts with the OSD and Army’s test communities have not only controlled program costs but also reduced schedule risk. In addition, from an execution perspective, the program’s collaboration with the MCoE has been instrumental in looking at requirements at all levels (including key performance parameters) and conducting operational risk assessments to determine whether AMPV’s design is still operationally suitable and effective, which will set up the program for greater success during engineering and manufacturing development (EMD) test activities.
Landy worked for several years on the Future Combat Systems program, eventually leading the 80-person System of Systems Engineering and Integration Directorate, where he learned that “time was my most valuable resource.” He said, “There was never enough time to try and address every issue—the position forced me to focus on those issues most critical to my organization’s success and the needs of the associates working for me.”
He also chaired the source selection evaluation board for an acquisition category (ACAT) I program, which taught him how industry responds to government-issued requests for proposals, how to push industry to address critical needs, and the dynamics of senior-level decision-making. He also was the deputy product manager for requirements management and analysis for the Ground Combat Vehicle program, which taught him how to see a program from the stakeholder’s perspective.
Landy believes that the greatest satisfaction with the AMPV program will be when “we hand off the first unit set of AMPVs.” Until then, he said, satisfaction comes at smaller levels—making decisions that maintain program continuity while balancing risk, seeing associates digging into execution issues and finding solutions, and responding to external stakeholders’ concerns and seeing their approval of what the program is doing.
His advice to others is to seek diversity in assignments—learn about the different functions (contracting, financial management, logistics, test, organizational construct, etc.) required to execute an acquisition program. “Compete for positions on smaller acquisition programs that will require greater self-reliance and responsibilities than what you may be exposed to on larger programs,” he said. “Seek professional development training on leadership, management, supervision, negotiation, consensus building and stakeholder management.”
Landy is Level III certificated in both program management and engineering with a B.S. in chemical engineering from the University of Detroit and an M.S. in hazardous waste management from Wayne State University’s School of Chemical Engineering.
AMPV Director of Engineering Kevin Houser has 34 years of experience. He oversees two engineering branches, comprising 25 engineering personnel who serve as an integrated product team (IPT) in concert with the manufacturer’s engineers to design, develop, integrate and test AMPV systematically.
Experience has taught Houser that the Army typically wants an item faster (how can you speed up delivery and fielding?); bean counters want it at less cost (what can you do to make it cheaper?); the user representatives want more capability (requirements creep: what if we added this?); and the oversight team wants to ensure that whatever happens is traced to a document, i.e., a reduction in requirements can still be traced to the capability development document (CDD). A balanced approach allows the PM to reduce the tensions among the stakeholders and stay on track to deliver a vehicle that is “good enough without gold plating.”
Houser champions value engineering projects in which the program introduces a change that results in cost savings. So far with the AMPV program, the team has identified changes to the quantity of armor tiles required to support the prototype vehicle test program, which saved just over $1.5 million. This required numerous consultations with the test community, engineering, acquisition, and with BAE Systems. He indicated there may be potential for future cost savings as well.
His advice to others is a credo he’s carried with him since working for the Navy as a young engineer: “Support the mission first and don’t say no to an opportunity.” He is extremely proud of the AMPV engineering team, which, along with the manufacturer, has driven since day one to achieve a first-production prototype build within two years of the program’s start. “We have the best people on the team,” he said. “We’ve proven we’re the varsity.”
AMPV Director of Product Assurance and Test Joseph C. “Joe” Perri has 33 years of experience, a B.S. in engineering from the New Jersey Institute of Technology, and Level III certification in test and evaluation; project management; systems engineering; and production quality and manufacturing.
Perri serves in the key leader position for test/lead developmental tester responsible for detailed planning, preparation, integration, execution and reporting of developmental, operational and live fire testing. He is also responsible for system assessment of reliability, availability, maintainability and testability, and for quality assurance and quality engineering of hardware and software. He and his team help stakeholders evaluate the system; currently, they work primarily with the OSD and Army test communities.
He credits the careful planning and review of the test and evaluation master plan, in collaboration with OSD test officials, as a strong predictor that there will be no issues or surprises as to how tests are conducted. “Early one-on-one, face-to-face reviews and working-level meetings with test officials in OSD have built trusting relationships,” Perri said. “In an environment of the internet and email, good old-fashioned meetings still add an important element to the process.”
Perri said he learned from one of his first bosses that there is no compromising integrity—nor, he adds, the needs of the Soldiers. “I also learned that relationships with the Office of the Secretary of Defense, the Army Test and Evaluation Command, test centers and contractors are not built by sitting at your desk,” he said. “There is no substitute for personal engagement.”
His advice to others is to learn as much as you can from the programmatic side (how the acquisition process works, how the funding works, how programs get approved and go forward), and become an expert in your area of interest. “You need to know how the Army acquisition cycle works, and you need to be respected in your technical area of interest,” he said. “Your knowledge of both will help you build trust.”
Deputy Product Manager for Integration Ed Lewis keeps his focus on program management. He has 29 years in the workforce, is Level III certified in both management and engineering, and holds a master’s in management science and a bachelor’s in industrial engineering, both from Ohio State University. A member of the program’s initial team, he is very proud of the synergy within the program office and with stakeholders, as well as how far the program has come.
Lewis and his team are responsible for design, integration and test of the Mission Command variant of the AMPV; the execution of the acquisition strategy to accelerate AMPV fielding to support the European Reassurance Initiative, in which DOD seeks to reassure our NATO allies and bolster the security and capacity of our partners; the supply chain management of the AMPV prototype build and negotiating the low-rate initial production option; and any future AMPV initiatives. In his involvement with stakeholders, Lewis said his communications are open and transparent to gain an understanding of everyone’s interests.
Lewis said that, from his standpoint, there are three major factors that contribute to the success of the AMPV program through stakeholder involvement.
The first is user and materiel developer coordination in developing the CDD and associated performance specification (PSpec). There were multiple meetings between the user and materiel developer to ensure achievable requirements given the acquisition strategy and available technology, he said. “We also had an independent technical team of subject matter experts review our PSpec for clarity and achievability.”
The second is industry days. AMPV hosted two industry days that provided valuable feedback on performance specification and the contract scope of work. These two engagements led directly to PSpec and CDD modifications.
Finally, Lewis cited “knowledge points,” the venue whereby the PM kept senior Army leaders aware of program status and requested decisions. It also was the venue that initiated a CDD change based on feedback from industry days, which resulted in a revised CDD in 60 days.
Lewis advises members of the workforce who aspire to leadership positions to focus on current responsibilities and do the best job possible without worrying about the next job. He said it is important to learn as much as you can from your present position and make sure to obtain appropriation certifications, as well as to seek developmental opportunities.
Lead Cost Analyst and Operations Research Analyst Ryan Lasecki is charged with estimating the program’s full life cycle costs. In this position, he works with many stakeholders throughout the Army and OSD, as well as the engineers, logisticians, and members of the contracting and test communities to make sure that everyone understands what should be included in successfully designing, producing, fielding and sustaining AMPV.
With a bachelor’s in business administration and management from Western Michigan University and an MBA from Lawrence Technological University, Lasecki is Level III certified in business (cost estimating) and in business (financial management), and Level I certified in program management.
Lasecki is always looking for ways to help reduce both production and sustainment costs. A mandate from the Milestone B Defense Acquisition Board meeting with the Hon. Frank Kendall, the undersecretary of defense for acquisition, technology and logistics, was to establish should-cost initiatives. Because the AMPV program has “a good amount of government-furnished material” from other programs, a plan was conceived to reduce costs by not buying all the equipment needed for testing purposes, but instead borrowing or reusing hardware already in the inventory. The result was a savings of $4 million in FY16 alone.
In Lasecki’s view, the AMPV program is successful because there is a good mix of younger, energetic people and seasoned employees who help focus the program with historical knowledge. Additionally, he said, the program office is roughly 100 people, and all employees are empowered to make or recommend decisions without going through layers and layers of management.
His career advice is to be like a “sponge” and soak up all the information you possibly can about the program you are working on. “Don’t just stay in your functional stovepipe,” he said. “Get out and see what others are doing, and see if you can add value to their ideas.”
Steve Herrick was the system acquisition manager and DA systems coordinator (DASC) until his recent move to the PEO for Combat Support and Combat Service Support. With more than eight years of civilian service as a CP-51 in the Army Acquisition Corps, he is Level III certified in both program management and engineering. He holds a B.S. in biomedical engineering from Lawrence Technological University and an M.S. in program and project management from the University of Michigan.
Herrick’s approach to stakeholders is to understand what makes them tick and what their “true position” is on a given subject. He knows the value of communication and regular updates. “One thing I learned is that each stakeholder is needed critically at any given time, and having personal relationships allows for amazing communication,” he said.
As a civilian, Herrick deployed as the lead engineer in Afghanistan for the MRAP and fielded the first MRAP All-Terrain Vehicle in Operation Enduring Freedom. “This gave me a better understanding early in my career how the operational Army works,” he said, “and what our true job is as acquisition professionals—to produce safe, suitable, supportable and survivable products for the critical needs of our warfighters.”
Herrick believes that a major factor in AMPV’s program success was shaped years ago by the late Maj. Gen. Harold J. “Harry” Greene, then the ASA(ALT)’s deputy for acquisition and systems management; Col. William Sheehy, then the PM for the ABCT; and Ed Lewis, then a deputy product manager on special assignment from the Bradley program office. Herrick said Greene was the beacon that kept AMPV on the agenda in senior Pentagon leaders’ meetings and in the executive summaries that followed; at the time, the AMPV program was preparing to release its request for proposals for the EMD phase, and Greene’s counsel and leadership kept the program tracking through its reviews with senior leaders and helped manage the expectations of all involved. Herrick credits Sheehy and Lewis with devising plans to rotate a steady flow of AMPV program office personnel through the Pentagon as DASCs to keep the program in the forefront and shepherd it through its reviews.
“A colleague and I combined for 16 months of the two-year ‘rent-a-DASC’ phase,” Herrick said. “We came back to the program office, shared our experiences and explained to other AMPV personnel what these stakeholders at the Pentagon do and how the process ‘actually’ works.”
Herrick said his greatest satisfaction in being a part of the AMPV program “was the feeling of family. We came to work and had fun.” The program office got through multiple acquisition strategies; protests; congressional meetings, issues and reports; milestone documentation; meetings; long hours; no support and too much support; and awarded a multibillion-dollar contract to support and produce a product our Soldiers need. “I can’t say it enough: AMPV personnel are some of the finest professionals, friends and people I have ever known,” he said.
His career advice is to never turn away from challenge or adversity, because either or both can lead to great and unexpected things. “Get out of your comfort zone and move around in your career field,” he said.
Director of Logistics and Product Support Manager William “Bill” Cuneo has 35 years of service, a B.A.in English and Level III certification in acquisition logistics. He came to the AMPV program seeking a change after several years in various positions culminating as the logistics director for the Stryker family of vehicles. It was there that he learned everything from early life cycle analysis and testing to vehicle condemnation and demilitarization—during a time of war. “It was one continual Defense Acquisition University class with a whole lot of real-life examples,” he said.
Cuneo said his logistics team at AMPV interacts with primary stakeholders during quarterly supportability IPT meetings that address all 12 product support elements; working group meetings, usually weekly, that focus on a subset of the 12 product support elements; and milestone events. Behind the scenes, he said, there is a constant flow of emails, teleconferences, and one-on-one discussions that flesh out issues and challenges that need addressing, risks that need mitigating, and proposed courses of action to be evaluated on the way to a decision or path forward.
“I believe in early and constant communication with all stakeholders,” Cuneo said. “Bad news does not get better with age, and the sooner we know the bad news, the more time we have to develop a solution. The more brains we have working on the problem, the more likely we are to come up with a good fix.”
Cuneo said that the AMPV program was unusual in that, upon contract award, it immediately entered Milestone B. This presented a few challenges, as a number of milestone documents are usually required for Milestone B. Many of these documents could not be provided at Milestone B because they required that a defined materiel solution be in place, which could not have occurred for this program. “Given the close ties and level of trust that we had developed with all our stakeholders over the many months leading to contract award and entering at Milestone B,” Cuneo said, “it was a relatively easy process to get all the stakeholders’ buy-in to defer a number of logistics milestone documents until well past Milestone B.” That ensured a more useful set of documents in time to benefit and inform the program.
His career advice is to take the “tough” jobs. Seek to be challenged. You will grow and learn. Said Cuneo: “Mistakes are OK as long as you learn from them.”
Program Officer for Acquisition Amy Kozlowski is assigned to the AMPV Mission Command variant. With nine years of civilian experience, Kozlowski has an MBA, an M.S. in mechanical engineering and a B.S. in mechanical engineering, all from Lawrence Technology University. She is Level III certified in both program management and engineering.
Kozlowski came to the AMPV program in January 2014, before Milestone B, following a developmental assignment within OASA(ALT) at the Pentagon. She is responsible for managing cost, schedule and performance for efforts related to the AMPV Mission Command variant, including the complexities of network integration.
In her position, she works primarily with stakeholders that represent the user—the TRADOC capabilities managers (TCMs) for the ABCT within the MCoE at Fort Benning. “We come to a better understanding of the users’ interests through face-to-face discussions on requirements and through requirements decomposition,” Kozlowski said. “We did this with the support of the MCoE’s Mounted Requirements Division during requirements development prior to RFP [request for proposal] release.” Detailed discussions continue throughout EMD in working groups to review preliminary and detailed designs.
This detailed attention ensures not only that the PM clearly understands user requirements and translates them appropriately into a PSpec and scope of work, but also that the manufacturer meets the requirements in executing the design, she said. The ultimate goal is to produce an AMPV that meets the Soldiers’ needs, expectations and operational requirements.
Kozlowski said her greatest satisfaction in being part of the AMPV program came with a decision to turn the manufacturer on for a third workstation. The original CDD for the Mission Command Variant called for a minimum of two workstations with an objective of up to four. Additional analysis from operational exercises determined that the vehicle would need at least three workstations. TCM officials believed the program team could work with the manufacturer to design for three workstations with no disruption, but AMPV program personnel had to coordinate with stakeholders to make the change and support the cost increase to each vehicle. Working through the AROC, they obtained concurrence from Army leadership to pursue a design update and increase the capability. This high-level support enabled the program office to work with the contracting center quickly to enact the required changes, directing the contractor to update the design to include three workstations, thus allowing the vehicle to carry additional support personnel. The requirement was clarified after the contract award.

ARMORED, CAPABLE AND VERSATILE
On budget and on schedule to deliver the first prototype in December, the Army’s Armored Multi-Purpose Vehicle (AMPV) program will provide the ABCT with a family of vehicles comprising five variants to resupply the formation; conduct battle command functions; deliver organic indirect fires; provide logistics support and medical treatment; and perform medical and casualty evacuation. (BAE photo)
It was “a good example of a series of interactions over several months with the TCM, and eventually broader stakeholders as the issue was briefed up to the Army chief of staff at the AROC,” Kozlowski explained. There were a number of key considerations to discuss with the TCM representatives, some face to face, to understand the reasons for adding a workstation as well as the challenges and constraints—fiscal, contractual, schedule-based, etc.—of executing the change.
Then, Kozlowski said, “We were able to come together to successfully communicate this requirement clarification at the AROC.” Now, she said, “we are in process of executing a contract modification to have the manufacturer integrate the third workstation for EMD prototypes. This is a win for the Soldier.”
Kozlowski said her prior work experience prepared her well for this job. Her two most recent assignments, as the assistant product and project manager (APM) on the Bradley program and as part of OASA(ALT), gave her valuable experience. “My Bradley APM experience helped me to understand the APM roles and responsibilities,” she said. “My time in the Pentagon on developmental assignment provided me with unparalleled experiences in seeing senior Army leaders from various stakeholders, staffs and functional areas in action.” She came to understand in depth the interests of all the key players in the acquisition community and how they all worked together at the most senior levels, she said. “This is tremendous insight to be able to bring back into a PM and into an APM role.”
Kozlowski’s career advice is to recognize the critical importance of being able to manage the details and see the big-picture strategy at the same time.
Lead Systems Engineer and Systems Engineering Branch Chief Corey DeSnyder has seven years of service as a civilian and 11 years as a government support contractor. He has an M.S. in systems engineering from Johns Hopkins University and a B.S. in aerospace engineering from the University of Michigan. He is Level III certified in systems engineering and Level I certified in program management.
DeSnyder leads the Systems Engineering Integration Team, which is in charge of technical design decisions for the program with configuration control of the PSpec and systems engineering plan. From his vantage point, he sees that “finally,” DOD as a whole is willing to make the performance trades necessary to field a vehicle within cost and schedule constraints. “Too many times,” he said, “we get promised the full set of requirements fast and cheap and, therefore, get stuck with cost and schedule overruns with a subset of functionality.”
DeSnyder is prepared for his role with the AMPV program because of his prior experience as an engineer on the Joint Strike Fighter program, handling airborne software. “I was part of the initial stages of that program that culminated in the system development and demonstration contract,” he said. “I saw firsthand how competition drove a lower-cost proposal on a cost-plus contract, which resulted in cost overruns and functionality delays from the start. I was able to convey those observations when the AMPV competition had similar results, and we were prepared to present tradeoffs that needed to be made against cost, schedule and performance.” The difference with the AMPV program is that those trades still stayed within cost and schedule, he noted.
His career advice is to build your background experience. “Don’t get pigeonholed in one program and in one technical area,” he said. “It helped that I had experience in a joint program.”
Architecture Lead Juan Carlos Santiago has 18 years of civilian experience, a B.S. in electrical engineering and a master’s in engineering management from the New Jersey Institute of Technology. He is Level III certified in engineering. Santiago is responsible for managing development of the system architecture and ensuring that it remains in sync with requirements and design. He said AMPV is using a process developed by the U.S. Army Tank Automotive Research, Development and Engineering Center (TARDEC), the Ground System Architecture Framework (GSAF).
Aside from interacting with the AMPV manufacturer to ensure that the architecture is developed in accordance with GSAF and aligned with requirements and design, Santiago works with the TARDEC systems engineering personnel to support the maturation of the GSAF process. “I consider both the manufacturer and TARDEC to be my stakeholders,” he said.
His greatest satisfaction is getting through a critical design review, and he looks forward to the first prototype delivery in December. A lot of tough decisions have been necessary to balance cost, schedule and performance, but the leadership and personnel on the AMPV program made that possible, Santiago said.
His career advice is to work hard, keep open lines of communication, and always understand your end goal so that you can develop achievable steppingstones to get there.
Director of Business Management and Program Analysis Officer Tom Lazenby leads three teams within AMPV’s business management office: cost estimating and analysis; resource management; and performance measurement and program reporting.
The cost team works primarily with OSD and Army officials and generates cost estimates that support program-level decisions, trade studies, and “what if” exercises. In addition, it monitors the contractor’s affordability processes and assess its progress in meeting program cost targets. The resource management team, working with similar stakeholders, develops, justifies and executes the AMPV budget. The performance measurement and program reporting team oversees the earned value management program and generates program-level reports, such as the defense acquisition executive summary and selected acquisition report. It works with DCMA as well as the OASA(ALT) reporting staff.
With 29 years of civilian service, Lazenby holds an M.S. in industrial and systems engineering and a B.S. in industrial and systems engineering, both from the University of Michigan at Dearborn. He is Level III certified in both business (financial management) and program management.
“From my perspective, the primary stakeholders are interested in ensuring that the program has adequate resources to do what it needs to do,” Lazenby said. “The big thing was realizing that everyone wanted to get AMPV right the first time, in order to avoid the historic problem of programs being underestimated and under-resourced.” He said there is a great satisfaction in getting a major new program off the ground, but that “the real satisfaction will come when the program starts fielding a capability to Soldiers.”
Lazenby said that in the lead-up to the Milestone B decision, program cost estimates were compared and contrasted, differences were analyzed and, in many cases, the up-front conversation resulted in the estimates converging. As a result, the Army and OSD estimates presented at the Defense Acquisition Board were very close. The Army committed sufficient resources to execute the program, and it has been operating within its acquisition-program baseline. Lazenby attributes the success of the AMPV program to open and honest communication.
His career advice is to look for experiences that broaden your knowledge base. “If you want to progress,” he said, “do not be content to spend your career in the same office doing essentially the same thing year after year.”
“More than anything else,” he continued, “it was career experiences that prepared me for this job. Classes help, but there’s no substitute for experience.”
Test Engineer Courtney Young joined the AMPV test team less than a year ago to focus on medical vehicle variants. With a B.S. in biomedical engineering from Michigan Technological University, Young is Level III certified in engineering; Level II certified in test and evaluation; and Level I certified in life cycle logistics. She leads the planning for a medical demonstration event to help verify several requirements specific to the medical variant AMPVs. This involves coordination with stakeholders from the MCoE, the Army Medical Department Center and School, and the Army Evaluation Center.
Young also works with program, product and project offices that will provide products to be fielded on the AMPV in order to plan new equipment training (NET) for test personnel during the EMD phase. Her interaction with stakeholders is on a daily, weekly and monthly basis, with face-to-face meetings for IPTs, working groups and technical reviews. “It’s always best to address program challenges as a group so that we can provide the best value mitigation and path forward for all parties,” she said.
Young came to the AMPV program office from the Edgewood Chemical Biological Center in Aberdeen, Maryland, where she started as an intern. Her supervisors there supported her career development. “I was fortunate to be afforded every opportunity for professional training,” Young said. “The most rewarding training experience for me was the Joint Senior Leader Course at Fort Leonard Wood, Missouri. “I was the youngest student in the course by far and very grateful for the opportunity to learn from such experienced colleagues. The course provided me with a great foundation for understanding how joint organizations function together, and provided unique experiences which helped me to understand the user perspective.” She also said that attending fielding, NET courses, and operational tests and demonstrations were excellent developmental experiences for her as a young engineer.
The “sense of purpose” is her greatest satisfaction in being part of the AMPV program. “The whole team really is driven to develop the best value product to support the Army mission,” Young said. “We also are a working family who cares genuinely about each other, both inside and outside the workplace.”
Young said that team collaboration is always the key to successful stakeholder involvement. “After relationships are developed, compromise and balance are easier to achieve,” she said. “Regular meetings are essential in keeping the lines of communication open for successful resolution of any issues.” Open and honest relationships with stakeholders are critical, she said. “Never attempt to bury issues under the rug. Be open and honest with your stakeholders, and they will be willing to help you mitigate problems because we are all working toward a common goal: to support the Army mission.”

CLOSE AND CONSTANT COMMUNICATION
Lead Systems Engineer and Systems Engineering Branch Chief Corey DeSnyder, Director of Engineering Kevin Houser and Lead Cost Analyst and Operations Research Analyst Ryan Lasecki meet to discuss progress on the AMPV program. A recurring observation among members of the AMPV team was that nothing beats face-to-face interaction to build relationships with program stakeholders and cement a common understanding of program goals and objectives. (U.S. Army photo courtesy of PEO GCS)
CONCLUSION
Several things are abundantly clear from the experience of the AMPV program as it stands. First, a successful program is built on a firm foundation—with stable requirements and proper funding.
Second, program leadership is important, both in assembling a team and keeping it focused on the mission and its important roles in achieving that mission. Third, diversity of assignments and “tough” jobs create an experienced workforce ready to take on new assignments. Fourth, open and honest communication at all levels—vertically and horizontally—is vital.
Finally, highly engaged stakeholders contribute significantly to an acquisition program’s success!
This article was originally published in the October – December 2016 issue of Army AL&T magazine.
Subscribe to Army AL&T News, the premier online news source for the Acquisition, Logistics, and Technology (AL&T) Workforce.