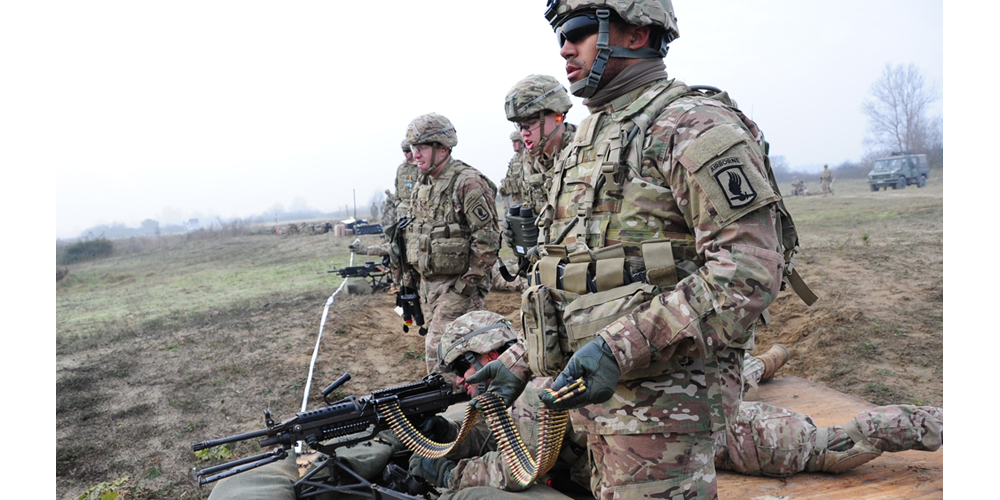
PM MAS secures ManTech and R&D funds to enable the industrial base to experiment with green machining to produce the next generation small-caliber round.
by Mrs. Marta Hess, Mr. Jeremy Lucid and Mr. Joseph Paras
Until 2010, ammunition for small arms weapons has not kept up with evolving threats, and the performance of legacy ammunition has remained relatively stagnant since the early 1980s. Developed using Cold War-era technology, legacy ammunition has a number of deficiencies in providing warfighters with a definitive advantage against current and future threats. A large-scale effort to develop and field the next generation of small caliber ammunition—and with it, the overmatch capability legacy ammunition does not provide—is underway at Project Manager Maneuver Ammunition Systems (PM MAS), Product Manager Small Caliber Ammunition, located at Picatinny Arsenal, New Jersey.
This next generation of small caliber ammunition includes advanced technologies to improve lethality at greater distances, as well as alternate cartridge case materials to lighten a Soldier’s standard combat ammunition load. PM MAS secured U.S. Army Manufacturing Technology (ManTech) Program funding to supplement existing research, development, engineering and testing (RDT&E) funds starting in FY15, to mature the manufacturing readiness level of improved material solutions. These additional resources have played an important role in reducing manufacturability and cost risks as products transition to full-rate production, providing the warfighter with improved capability at the quantity needed to conduct training and combat operations. Without this crucial resource to advance manufacturing readiness, it would have been too costly for the ammunition industry to field enhanced capabilities in required quantities of small caliber ammunition.
COMPONENT MANUFACTURING AND ASSEMBLY
The focus on improving small arms ammunition began in earnest around 2008, when the U.S. Army Maneuver Center of Excellence (MCOE), representing the voice of the user, received mixed reviews in post-combat surveys regarding legacy 5.56 mm and 7.62 mm ammunition. This triggered the MCOE to generate small caliber family of ammunition capability development documents for 5.56 mm, 7.62 mm and .50-caliber ammunition. These documents established the Army’s requirements for small caliber ammunition to reduce or eliminate existing operational capability gaps and ensure overmatch in future combat environments through the foreseeable future. These requirements formed the basis for multiple research and development (R&D) programs to improve lethality, survivability, mobility and training flexibility.

PRECISELY ASSEMBLED
Modified through a ManTech-funded R&D program, this new bullet assembly machine has a higher operational availability and lower scrap rates than predecessor equipment, and it provides more processer feedback while offering the ability for faster tooling changes. Improvements in precision means higher quality ammunition can be fielded faster and cheaper. (Image courtesy of PM MAS)
As with many innovative products or systems, advancements can result in price increases. Over the last decade, improvements in small caliber ammunition have required modifying critical projectile components with state-of-the-art designs and complex shapes, such as a modified projectile jacket with an exposed tip to achieve consistent soft-target effects, and advanced materials such as tungsten carbide to achieve enhanced hard-target terminal effects at greater distances. This in turn has required research in advanced manufacturing techniques including machining in a pre-formed state, called “green machining,” advanced grinding and multistage projectile assembly operations that the ammunition industry previously was not required to use.
By leveraging $5 million of multiyear RDT&E funding from ManTech, PM MAS, in partnership with the U.S. Army Armaments Research, Development and Engineering Center (ARDEC), funded two major initiatives to assist the industrial base in developing and refining advanced manufacturing processes to provide higher-performance ammunition to the warfighter at an affordable cost.
For example, PM MAS and ARDEC have been able to drive down the unit cost of tungsten carbide components by using ManTech resources. Because of the hardness of tungsten carbide, manufacturing it has historically involved lengthy grinding operations. Using these labor-intensive operations resulted in one part completed every 15 minutes, and the unit cost exceeded $20 per part, mainly because existing manufacturing methods for tungsten carbide material were not optimal for complex shapes and configurations.
Using ManTech funding, the team engaged with several small businesses, via market surveys and competitive bids, to incentivize development and improvements in novel and advanced tungsten carbide manufacturing techniques. This funding allowed the small businesses to invest in developing alternative manufacturing processes that have the potential to be leveraged for other military applications as well as commercial ventures, all while reducing investment risk on their end. Ultimately, PM MAS and ARDEC selected a green machining process as the most viable approach to drive down component costs. The process is a powder metallurgy technique where chalk-like pre-forms of tungsten carbide powder are shaped before sintering, a heat treatment process that binds the powder particles together to produce a hard, dense material. Traditional tungsten carbide manufacturing involves sintering simple stock shapes, such as bars or rods, and then hard-grinding the final shape into the material.

GETTING TO THE POINT
More than 30,000 components have been produced to date using the green machining method demonstrated by PM MAS. The resultant reduction in manufacturing time—from 4 parts per hour to 120 parts per hour—reduced the projected unit price to less than 25 percent of the original cost, yielding millions in savings over the life of the program. (Image courtesy of PM MAS)
Green-machining decreases the product cost by increasing the efficiency of producing complex shapes and configurations. More than 30,000 components were produced from October 2015 through December 2016 using this method.These improvements reduced manufacturing time from one part every 15 minutes to two parts every minute. It reduced the projected unit price to less than 25 percent of the original cost—resulting in a potential savings of more than $300 million over the expected 20-year life of the program.
Following the initial success in developing a more efficient and cost-effective manufacturing process for complex tungsten carbide components, PM MAS and ARDEC again leveraged ManTech resources to implement improvements in 7.62 mm bullet assembly. Typically, small caliber bullets are assembled on a bullet assembly machine (BAM), where a copper cup is drawn into a bullet jacket that encapsulates the other bullet components (penetrator and slug) and ultimately a small caliber projectile is produced. Because the design of small caliber ammunition has not changed since the early 1980s, legacy BAMs also have remained relatively unchanged, resulting in less than optimal operational availability, higher scrap rates and less flexibility in tooling changes for different ammunition types.
By leveraging ManTech funding, the team developed a new tooling package that uses a higher-precision BAM to eliminate many of these inefficiencies. This 21st century BAM, with enhanced controls for precise assembly, is anticipated to maintain the existing rate of 60 parts per minute with higher operational availability, lower scrap rates, more process feedback to the operator and the ability to make faster tooling changes. More importantly, as the manufacturing equipment becomes available to the industrial base for full-rate production, the higher precision means better-quality ammunition delivered to the field, more quickly and at a lower cost.
LIGHTWEIGHT CARTRIDGE CASES
The next endeavor the program office is tackling with ManTech support involves developing manufacturing and loading processes for lightweight cartridge cases. PM MAS, with support from ARDEC, is exploring new manufacturing processes that include injection-molding polymer or metal using multicavity molds; over-molding; thermal bonding; metal laser edging; and rapid propellant loading of lightweight cases. All these process are new to the Army’s small caliber ammunition production base. Lighter-weight cases reduce combat loads, resulting in greater mobility for Soldiers in combat as well as reduced weight for vehicular and aerial platforms. Using nontraditional cartridge case materials is key to realizing weight savings in small caliber ammunition.

MAKE IT LIGHTER, FASTER
PM MAS is working with a handful of stakeholders to improve the manufacturability of lightweight cases, including the PCP Ammunition case on the left and the USG steel case on the right, while attempting to drive down manufacturing costs. Cutting cartridge weight has the potential to significantly reduce the burden on the Soldier—and on vehicular and aerial platforms as well. (Images courtesy of PCP Ammunition and USG)
PM MAS held an industry day on April 19, 2016, to inform industry partners of the desire to reduce the Soldier’s load in small arms ammunition. The Army shared program requirements, industry opportunities and a planned schedule. The event also provided a forum for smaller non-defense businesses to meet with ammunition producers to discuss the challenges in meeting the Army’s needs. During the next five years, the challenge will be designing and delivering the same quantities of current brass-cased 7.62 mm ammunition requirements in a lightweight case that meets the performance requirements of the M240 machine gun.
The Army encouraged companies to explore polymer, steel or hybrid metal designs, with the goal of reducing overall weight by 10 to 50 percent over existing brass-cased cartridges while ensuring proper function in weapon systems; the new design also needed to be produced at typical small caliber ammunition production rates of 75 to 125 million cartridges per year and at a comparable price. Several innovative small businesses have developed lightweight case prototypes but have difficulty meeting the above criteria because of their limited manufacturing capability. The team will use ManTech funding to improve the manufacturability of these innovative, lightweight cases while attempting to drive down manufacturing costs.
CONCLUSION
ManTech funding has enabled the development of a novel manufacturing capability at three companies with the ability to produce next-generation small caliber ammunition. As a result of the R&D effort, the program office has learned the importance of engaging with industry partners early in the RDT&E phase to develop and mature manufacturing processes concurrently with product development. Bringing industry’s expertise in during product development allows program management to build more realistic schedules, reduce costs and field higher performance ammunition that will provide overmatch capability to our warfighters. The ManTech program is instrumental in developing and refining innovative manufacturing technologies that will transition to the industrial base in support of full-rate production—a win-win scenario improving national security while preparing the industrial base for future needs.

CLICK BOOM
Paratroopers from 54th Brigade Engineer Battalion, 173rd Airborne Brigade, conduct a qualification range in December with a M240B machine gun during Exercise Castle Warfare at Foce Reno Training Area in Ravenna, Italy. Research efforts, led by PM MAS and ARDEC and supported in part by funding from ManTech, are looking at new manufacturing processes for producing lighter ammunition for the M240 that still meets the weapon’s performance requirements. (U.S. Army photo by Elena Baladelli, Training Support Activity Europe)
For more information about the work of ManTech and PM MAS on green machining, go to http://www.armymantech.com/TCPACR.php.
MRS. MARTA HESS is a PM MAS project officer for the Lightweight Small Caliber Ammunition program. She holds an M.S in mechanical engineering from Stevens Institute of Technology and B.S. in mechanical engineering from New Jersey Institute of Technology. She has been part of ARDEC’s Quality Engineering and System Assurance Directorate for 13 years and is an Army Acquisition Corps (AAC) member. She is Level III certified in production, quality and manufacturing.
MR. JEREMY LUCID is a PM MAS project officer for multiple small caliber ammunition RDT&E initiatives. He holds an M.S. in mechanical engineering from Stevens Institute of Technology and a B.S. in mechanical engineering from The College of New Jersey. He has worked for the federal government for 12 years and is Level III certified in project management as well as systems planning, research, development and engineering.
MR. JOSEPH PARAS is ARDEC’s project officer for ManTech’s Tungsten Carbide Penetrator & Assembly Cost Reduction Program. He holds a B.S. in ceramics and materials engineering from Rutgers University. He has been assigned to the Munitions Engineering and Technology Center’s Armaments Engineering Analysis and Manufacturing Directorate for nine years. He is an AAC member and is Level III certified in systems planning, research, development and engineering.
This article is scheduled to be published in the April – June issue of Army AL&T Magazine.
Subscribe to Army AL&T News, the premier online news source for the Acquisition, Logistics, and Technology (AL&T) Workforce.