
THEN & NOW
2007 & 2018
Then: a veritable ‘petting zoo’ of 7,000 unique robots, each slightly different to operate and expensive to maintain. Now: the challenge of getting all the functions of those 7,000 on just three main robotic platforms.
by Ms. Mary Kate Aylward
It’s an arresting image: A dog—well, a “dog”—loose in the Sonoran Desert moves through a group of empty cars and trucks, sniffing around before halting and signaling to its handlers. Army personnel arrive on scene to dismantle the bomb identified by the “dog,” which is in fact a robot equipped with a powerful sensor that detects vapors or particles emanating from explosive devices.
It sounds novel even now, though robotic platforms have proliferated across the battlefield since 2005, when the test—described in a 2007 Army AL&T article—took place at Yuma Proving Ground, Arizona. The problem had particularly desperate urgency when casualties from improvised explosive devices (IEDs) were mounting in Iraq. “We had to do this,” Dr. John A. Parmentola said in an Oct. 21, 2017, interview with Army AL&T magazine. “I saw enough pictures of Soldiers blown up.” Parmentola, then director for Army research and laboratory management in the Office of the Assistant Secretary of the Army for Acquisition, Logistics and Technology, led the team that came up with the robotic explosive-sniffing dog and wrote about lessons learned from fielding it.
The problem persists today: how to keep Soldiers a safe distance from explosive devices and chemical hazards as they go out to find and remove them. And, as robots grow more capable, what other “dull, dirty and dangerous” tasks can they take over from Soldiers?
Parmentola led an early attempt, a quick-fielding project—two years from napkin sketch to 120 units in the field—that put an explosive-sniffing sensor (“Fido”) on robotic legs (called Fido/PackBot). Previously, explosive-detecting sensors were affixed to a handheld wand or device, putting Soldiers too close to the hazards they were looking for. Deploying Fido on a robotic platform kept them out of the way.
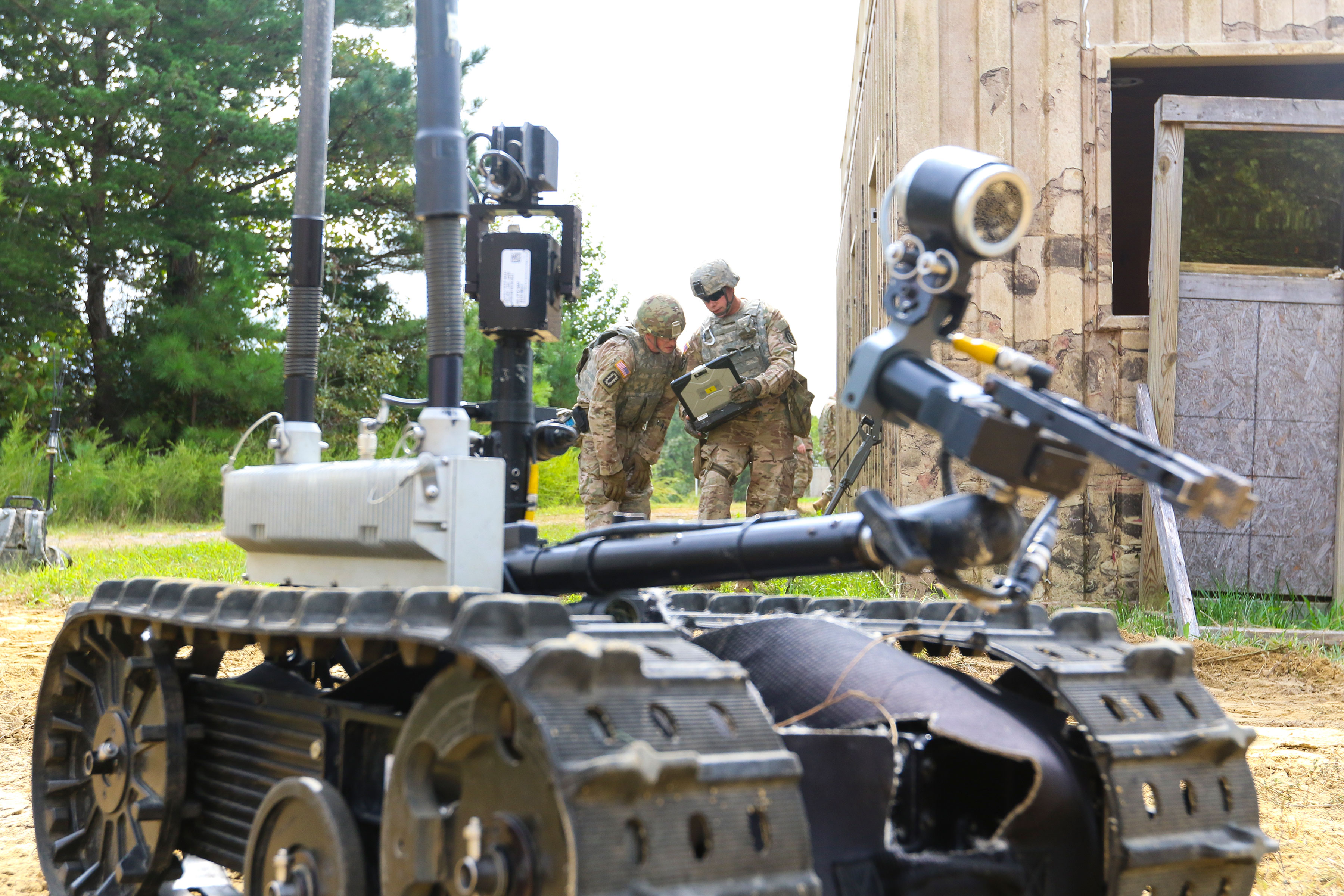
Sgt. 1st Class Joshua Tygret, left, and Sgt. Austin Murphy, assigned to 744th Ordnance Disposal Company, 52nd Explosive Ordnance Group, navigate the TALON during the EOD Team of the Year competition in September 2017 at Fort A.P. Hill, Virginia. The weeklong competition, one of three sponsored by the U.S. Army Ordnance Corps, recognizes exceptional expertise among EOD Soldiers and provides senior leaders the opportunity to assess ammunition, maintenance and EOD professionals across the institutional Army and the operational force. (U.S. Army photo by Staff Sgt. Lance Pounds, 71st Ordnance Group (EOD) Public Affairs)
ROBOTS FAR AND WIDE
The first ground robot in wide use, PackBot had been in Afghanistan since 2002. Made by iRobot Corp., it had just a camera and an extendable arm, mounted on a base with two tracked wheels. It could peer around corners and into caves.
By 2007, when the Fido sensor was added to some models, PackBot weighed 42 pounds, could cover 5.8 miles per hour and could flip itself over and keep rolling; some versions could climb stairs. Fido/PackBot could range about 1,000 feet from its operational control unit (that is, the joystick Soldiers used to direct the robot’s movements). It could retract the appendages on which its sensors were mounted, to creep underneath vehicles. It could also stand on its tracked base to add another foot of extension to its six-foot robotic arm, to peer inside the cab of a truck or the trunk of a car.
PackBot wasn’t alone on the battlefield—indeed, the Army fielded a “petting zoo of various ground robots,” to borrow reporter Jen Judson’s phrase from an April 12, 2017, Defense News article. Qinetic North America’s Dragon Runner robots and Qinetic unit Foster-Miller’s TALON platforms—among other robots, acquired as needs arose—rolled ahead of explosive ordnance disposal (EOD) Soldiers on route clearance missions and stood checkpoint duty.
Their descendants can roam farther, do more and, crucially, will be fewer in number: The Army plans to replace much of its collection of unmanned ground vehicles with just three main robotic platforms: small, medium and large. This is important not only because it’s cheaper and easier to maintain fewer multipurpose robots—but also for Soldiers. A Soldier in one unit might become familiar with a particular variant of a small Dragon Runner ground robot—which buttons to push on the controller, how much ground clutter the robot can navigate through. But when he transfers to another unit, which might be using a TALON robotic platform, he has to learn to operate the new platform from scratch.
Consolidating to just three robotic platforms prevents this waste of knowledge. A common chassis and operating system could be configured to carry different tools for different missions, while keeping the basics similar enough that Soldiers don’t need to relearn a new system to operate it.
“The Army purchased more than 7,000 unique robotic systems” during the last decade-plus, said Bryan McVeigh, the Army’s project manager for Force Projection within the Program Executive Office for Combat Support and Combat Service Support (PEO CS&CSS), in announcing the Oct. 2, 2017, award of a contract to build the medium-size robot. “That gave Soldiers the capabilities they needed, and it was the right thing to do for the mission. But we bought unique systems that weren’t very flexible. The robots often had just one capability [and] used expensive, proprietary software.”
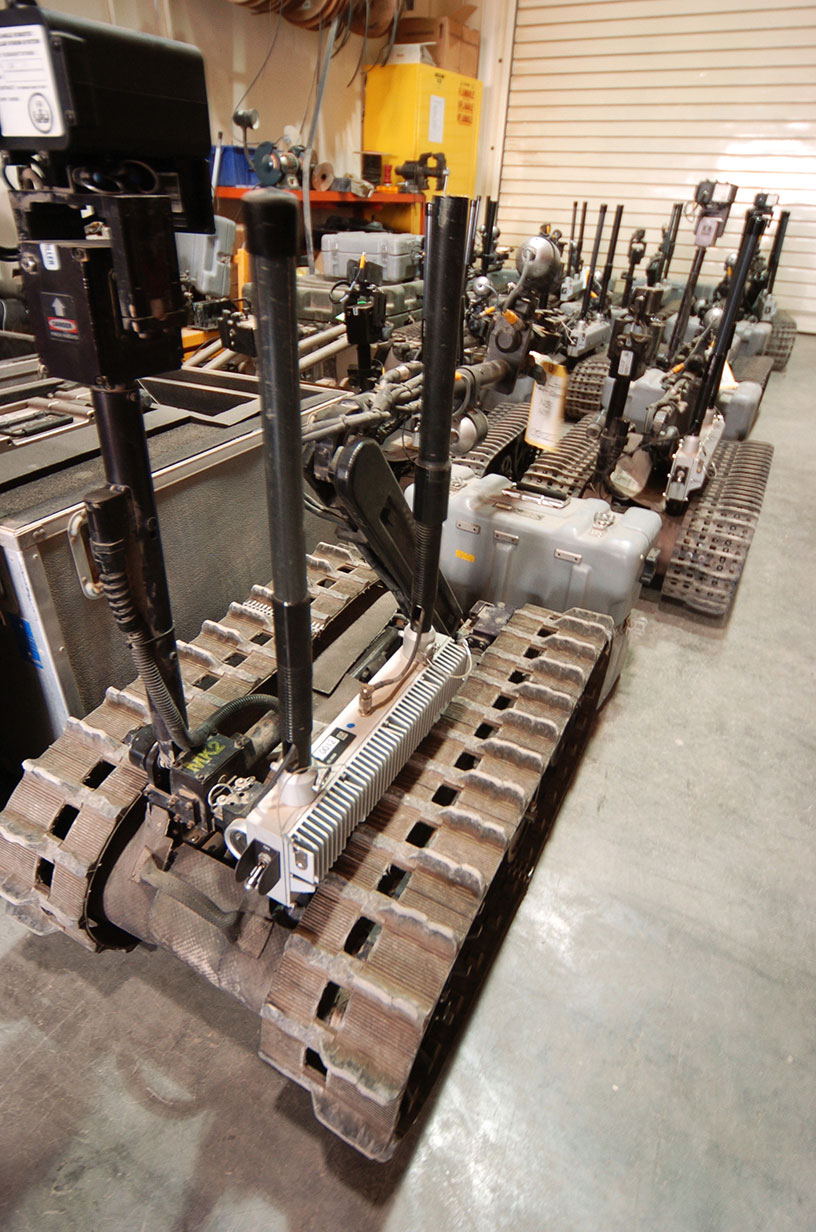
An army of robots stands ready for their next mission at the Joint Robotics Repair Facility at Camp Victory, Iraq, in 2009. Roughly 11 years after the robots were first fielded, the Army now faces the challenge of consolidating thousands of variants to just three platforms. (Photo by Spc. Richard Frost, 114th Public Affairs Detachment)
A MORE CLOSE-KNIT FAMILY
Soldiers and engineers at PEO CS&CSS have been sorting through this collection of robots to streamline it.
The medium-size Man-Transportable Robotic System (MTRS) is the furthest along in the trek to the field, and replaces the TALON family of robots. The 164-pound tracked vehicle is controlled by a handheld remote controller. Depending on what kind of equipment the base is fitted with, it can identify and clear land mines, IEDs and unexploded ordnance, or chemical, biological, radiation and nuclear (CBRN) hazards. PEO CS&CSS awarded a $100 million contract (with an option for an additional $58 million worth of work) to Endeavor Robotics of Chelmsford, Massachusetts, and expects to begin producing MTRS Increment II for engineer, CBRN and EOD units in FY19.
Part of the MTRS robot’s inner workings is the Army’s Unmanned Ground Vehicle Interoperability Profile. Akin to the operating system on a smartphone, it is an architecture that governs how the various parts of the robot communicate with one another and how the robot communicates with external command-and-control systems. The same way that a new app can be downloaded to a smartphone, the interoperability profile makes it possible to apply new payloads or functional tools to the robot.
The profile is also an open system; because the government owns the standards, rather than any one company, it should be easier for Army robots to change and adapt with technology, rather than the Army needing to buy a whole new platform when robotics technology inevitably advances. Should the software that processes the images a robot captures improve, old software can be swapped out and new software uploaded, so Soldiers can take advantage of the better vision sooner.
The Common Robotic System (Individual) and (Heavy) round out the planned trio of interoperable robotic platforms; they also will run with the Unmanned Ground Vehicle Interoperability Profile. The individual model will top out at 25 pounds; it is designed so that a Soldier can transport it in a pack and fit it for different missions while in the field. Theoretically, this robot could perform reconnaissance one day, then be reconfigured at the post for an EOD mission the next day. The heavy model, though still in the early stages of acquisition, could reach 1,000 pounds; the ability to disarm vehicle-borne IEDs is one desired capability, which requires a robot of significant size.
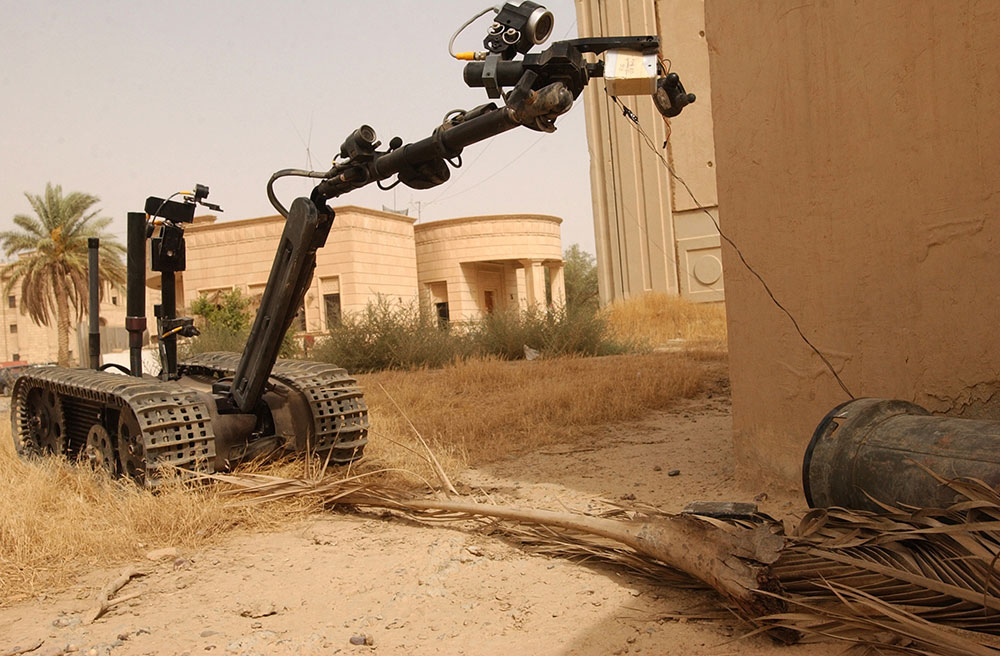
The TALON, shown in use in Tikrit, Iraq, in 2005, was among the first systems that allowed Soldiers to disarm IEDs from a distance, using a remote controller in the EOD vehicle. In an effort to standardize its robotic platforms and reduce its operational footprint, the Army plans to replace the TALON with MTRS, a 164-pound tracked vehicle that can identify and clear land mines, IEDs and CBRN hazards. (Photo courtesy of 22nd Mobile Public Affairs Detachment)
DOD is exploring the use of robots in almost every facet of military operations; the Army’s near-term priorities are to increase situational awareness and lighten the Soldier’s physical and mental load, according to the Army’s Robotic and Autonomous Systems Strategy. Based on his experience, Parmentola cautions that solving those specific problems must remain the focus, despite the allure of the high concept and the cutting edge. “I looked at the technology first, and that told me something. But I had to go to Fort Leonard Wood [in Missouri] to find out if the technology was really relevant.” There, a user need statement validated that Soldiers had identified a need for what the technology could do.
Parmentola continued: “What always matters is: What is the problem you’re trying to solve? We were trying to solve a specific problem: how to keep Soldiers out of harm’s way while looking for suspicious objects. Define the problem carefully and try to work backward from that, taking into account the operational issues. Most of the time in the Pentagon, I found that people spent the least amount of time defining the problem they’re trying to solve.”
For more information on the Army’s planned portfolio of unmanned ground vehicles, go to http://www.peocscss.army.mil/pdmugv.html.
For a historical tour of Army AL&T over the past 56 years, go the Army AL&T magazine archives at https://asc.army.mil/web/magazine/alt-magazine-archive/.
ONLINE EXTRAS
“Technology Transition—Lessons Learned From Fido/PackBot,” Army AL&T, October – March 2007: https://asc.army.mil/docs/pubs/alt/2007/4_OctNovDec/articles/12_Technology_Transition_—_Lessons_Learned_From_Fido_Packbot_200710.pdf
“iRobot’s PackBot now ready for deployment,” Engadget.com, March 30, 2007: https://www.engadget.com/2007/03/30/irobots-packbot-now-ready-for-deployment/
“Old Dog, New Nose,” Army AL&T, January – March 2015: http://usaasc.armyalt.com/?iid=110040#folio=156
“A Momentous Discovery … Or Is It?” Army AL&T, April – June 2015: http://usaasc.armyalt.com/?iid=115528#folio=100
“The U.S. Army Robotics and Autonomous Systems Strategy,” U.S. Army Training and Doctrine Command, March 2017: http://www.arcic.army.mil/App_Documents/RAS_Strategy.pdf
“Army awards first wave of enduring ground robotic programs,” Army.mil, Oct. 2, 2017: https://www.army.mil/article/194715/army_awards_first_wave_of_enduring_ground_robotic_programs
The Origin Story
In 2005, I was attending a meeting at TARDEC [the U.S. Army Tank Automotive Research, Development and Engineering Center] where TARDEC personnel demonstrated ODIS, a low-profile robotic system. About a month earlier, I had visited the Army[-established] Institute for Soldier Nanotechnologies [at the Massachusetts Institute of Technology] to discover they had taken the Defense Advanced Research Projects Agency’s Dog’s Nose Program to an operational device, Fido. At the time it was the world’s most sensitive explosive detector.
Because ODIS had a mast that retracted into the robot, a NASA technology, I began to think of putting Fido on the mast and using it to remotely sniff inside a vehicle for explosives, rather than having a Soldier exposed to an IED. The idea began to come together where we could put Fido and a state-of-the-art camera on a robotic system, so if a Soldier had a wearable vest with a display, the Soldier could see what the robot was seeing, and at the same time see an indicator showing whether an explosive is present. [It also had] a joystick used to maneuver the robot to a position where it could sniff something suspicious. The world’s first robotic dog that could see and sniff and could be remotely controlled—that was the concept.
BUT DOES SOMEONE NEED IT?
So then I needed to find a mission needs statement, where an Army school identified a need for this. It turned out that Fort Leonard Wood was the place where a need existed. George Anderson was a civilian working there. I connected with him, and he managed to find a mission needs statement calling for a platform that could inspect underneath a vehicle. I asked the proponents of the mission needs statement: “If we gave you much more than that, would you be happy?” They said they would.
If it weren’t for George Anderson, we wouldn’t have succeeded: He had to make a case for this solution with a culture that opposed using robotic systems. He demonstrated the kind of courage and persistence you need to accomplish something like this. We assembled the most dedicated, capable team of people I’ve ever worked with, to work on all aspects of this.
However, we had to do some homework: What specific platform would we use? We needed something low-profile that could go under a vehicle. TARDEC’s ODIS was one, iRobot had PackBot [and] Foster-Miller had a candidate robotic platform. I called a meeting among all of those in the Pentagon that touched on this issue: the OSD [Office of the Secretary of Defense] Robotics Office, TSWG [the Technical Support Working Group], Night Vision Laboratory, the Joint Robotics Office at Redstone Arsenal, TARDEC, Army Research Laboratory, etc. I told them we were going to do the fastest acquisition in history. Urgency was the motivation. We wanted to get something out that would save Soldier lives.
We didn’t follow a standard acquisition process. We created a single sheet of paper that had the selection criteria on it: low profile, ability to have an articulated arm, to reach high up (at least 6 feet), technical readiness level, etc., and also pan and tilt to look inside the cab or the trunk of a suspect vehicle. I arranged for three contractors to come in to HQ. Each one had half an hour to make a presentation on how they could fulfill the requirements. In two hours we did source selection. PackBot was the best choice, according to the team vote, and the most mature of all the technologies. There were cheaper platforms, but they weren’t operationally proven; PackBot was. That led to Fido/PackBot.
Then we had to estimate what it would cost to put together and how long it would take to complete the prototype. As Army director for research and laboratory management, I knew my labs well, and I knew Redstone and AMRDEC [the U.S. Air and Missile Research, Development and Engineering Center] had a well-established prototype integration facility. I contacted a very capable guy there by the name of Bill Schultz and said, “I want to prove to people that something like this can be done in record time.” I wanted to produce a full prototype, test it and have training manuals in 90 days. I told Bill to analyze this, talk to contractors, convince himself and then convince me and the people in my office that this could be done: “If there’s too much risk, we’ll change the schedule, but I want you to spend some time thinking about it. A week later he said, “I firmly believe we can do this.”
Starting from the day we received funding, we managed to pull this whole thing off in 90 days. That was a record; I’ll bet it still stands.
FEEDBACK UNDER FIRE
Five units were fully tested. We shipped four to Camp Victory in Iraq and kept one in the U.S. for troubleshooting. Soldiers started to experiment. There was a Marine, Col. Ed Ward, whose dedication to this project was phenomenal. He went into theater around Thanksgiving. He was in a vehicle taking a unit for testing to Abu Ghraib prison and he was sending me emails: “We’re under fire.”
Feedback from in theater was generally positive in terms of ease of use and effectiveness. JIEDDO [the Joint Improvised Explosive Device Defeat Organization] decided, based on that, to procure 120 units. Over 200 were eventually procured, I believe. In my home I have a plaque with a part of one of them that was blown up by an IED, saving a Soldier’s life. It’s the most precious and memorable thing I own.
—DR. JOHN A. PARMENTOLA, as told to Army AL&T.
This interview excerpt has been lightly edited for clarity and length. The U.S. Army Materiel Command named Fido/PackBot—officially called the Integrated Robotic Explosive Detection System—one of the 10 best inventions of 2006. Find out more at https://www.army.mil/article/3629/army_recognizes_greatest_inventions_for_2006.
Subscribe to Army AL&T News, the premier online news source for the Acquisition, Logistics, and Technology (AL&T) Workforce.