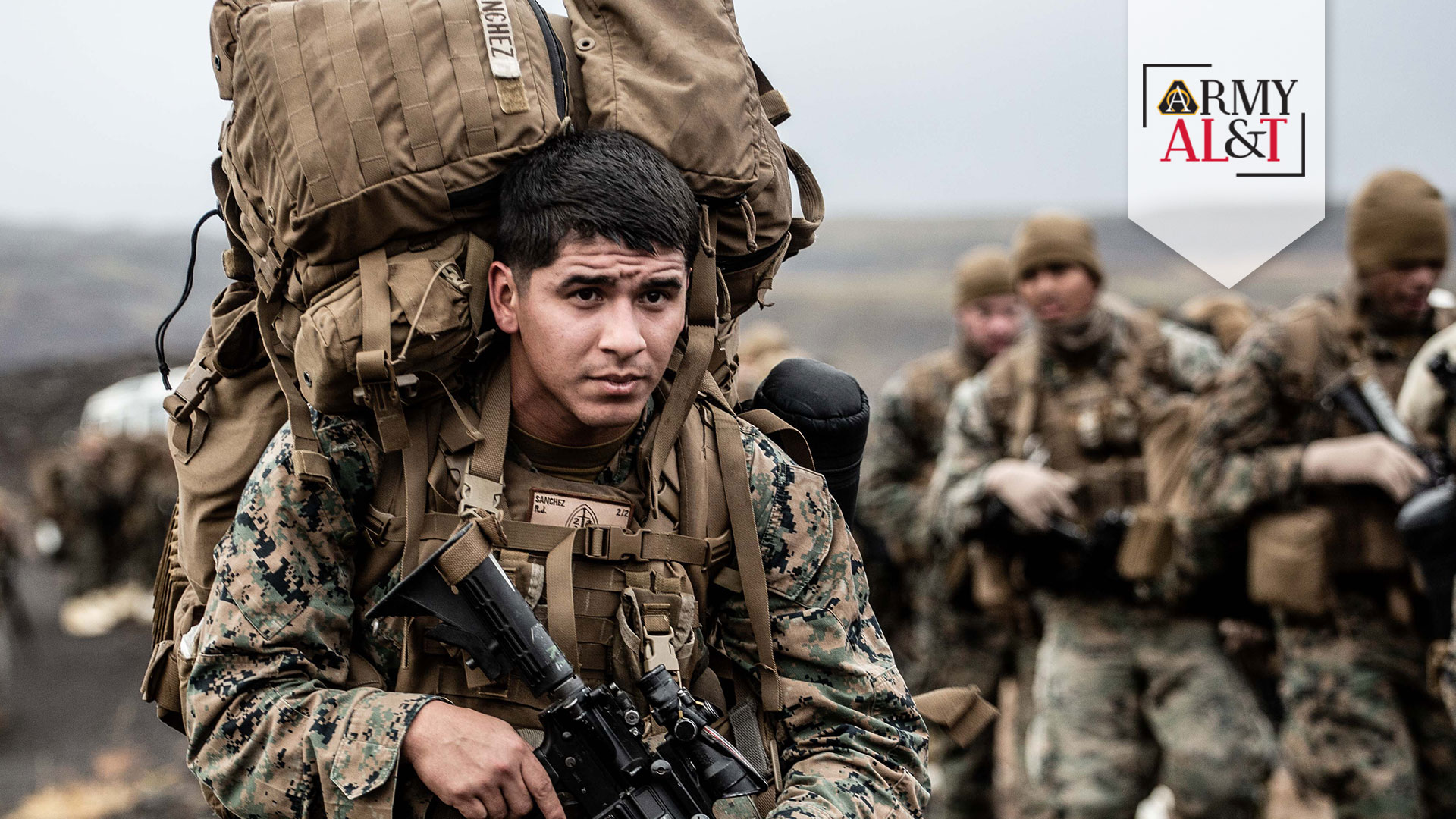
Army, Marines, U.K. collaborate to develop lightweight ammunition to reduce Soldiers’ load.
by Todd Townsend
As the conflicts in Afghanistan and Iraq intensified in the early 2000s, images of American warfighters carrying impossible loads while moving into operational theaters were all over the media. These images began an intense debate over how much we were asking our warfighters to carry and how materiel developers needed to prioritize lightening the load. The development community across the services took a hard look from the warfighter level at each piece of equipment to reduce ounces or pounds.
For small-caliber ammunition, efforts across the services were in the early stages of technical maturity. Because of technical advances in this area in the past few years, the U.S. Army and the U.S. Marine Corps formed a Joint Lightweight Ammunition Integrated Product Team to synchronize these efforts with the goal of decreasing the weight of ammunition by at least 10 percent. This approach will ensure collaboration during development that will yield a better, faster, cheaper solution for the future warfighter.
Any reduction in equipment weight, often referred to as “warfighter load,” will enhance warfighters’ readiness and increase mobility, survivability and lethality. In post-combat surveys, weight carried by the warfighter is frequently among the top concerns of combat veterans. While there are many pieces of equipment that add to this overall load, one common denominator across the services is ammunition. The cartridge case is the heaviest and hence the most logical area for initial weight reduction efforts in small-caliber munitions.
BRASS HAS ITS ADVANTAGES
The cartridge case is a critical component that has remained largely unchanged since the advent of brass-cased ammunition in the mid- to late 19th century. The Army has investigated the use of lighter materials for the past 50-plus years, always falling back on the performance, ease of manufacturing and robustness of brass case designs. Brass is a tough material that not only can stand up to firing pressures exceeding 70,000 pounds per square inch, but can spring outward under those firing pressures to seal the chamber and then spring back for easy extraction. Brass cases also can function and withstand storage at extreme temperatures of -65 degrees F to more than 160 degrees F.
Those factors, combined with a reasonable material cost, good availability, scrap recyclability and ability to reload, make it a challenge to replace brass. Other services have also looked at possible alternatives, but had the same technical challenges in their own searches. Scattered efforts over time across the services did not yield successful designs.
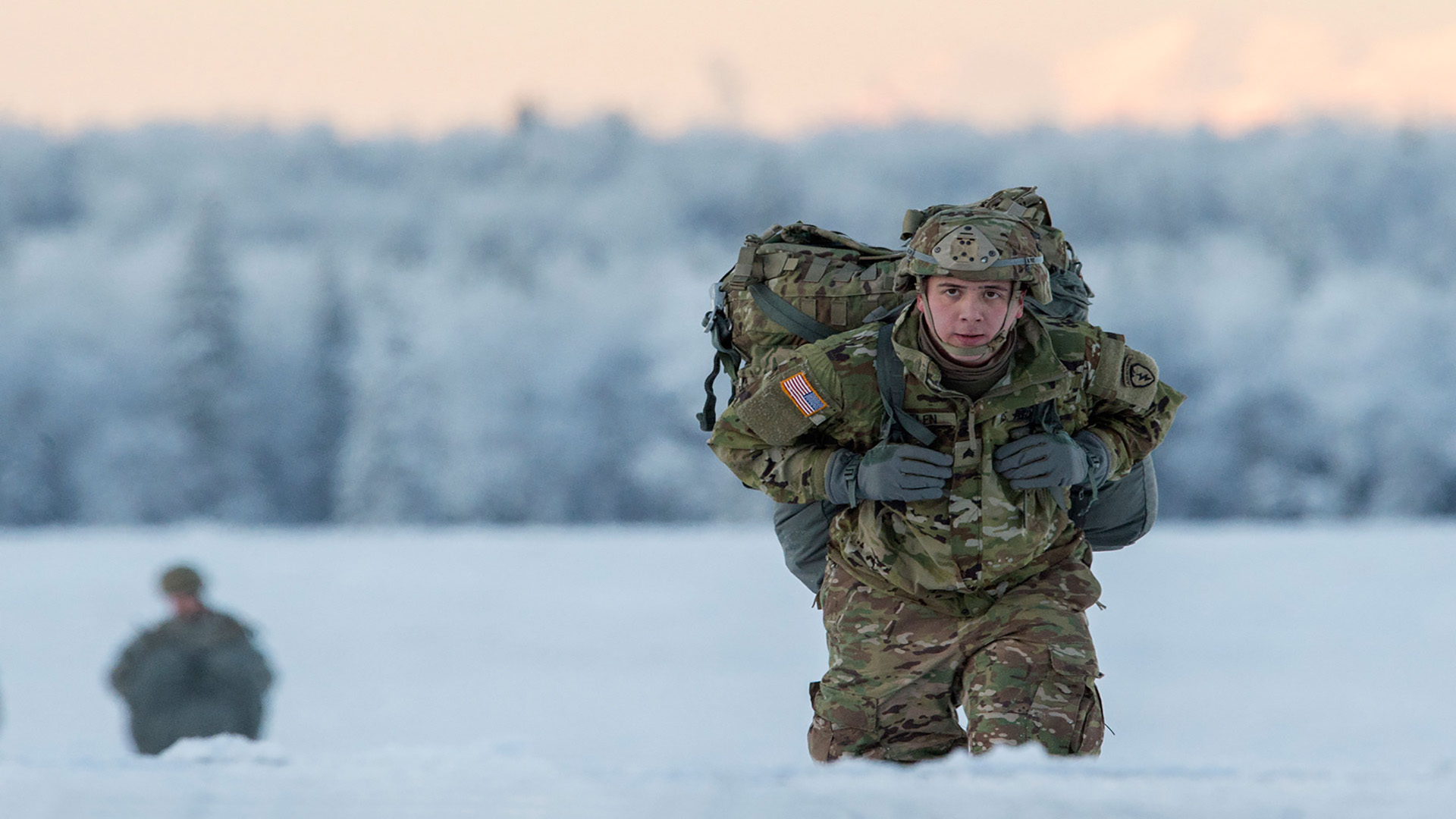
U.S. Army Sgt. Bruce Allen, assigned to the 4th Infantry Brigade Combat Team (Airborne), 25th Infantry Division, proceeds to the rally point after completing an airborne training jump at Joint Base Elmendorf-Richardson, Alaska, in January 2018. One of the reasons brass cartridge cases have remained in use for so long is their ability to withstand extreme temperatures, both hot and cold. (U.S. Air Force photo by Alejandro Peña, Joint Base Elmendorf-Richardson Public Affairs)
Within the past few years, emerging technologies and manufacturing improvements have created the opportunity for a fresh look at lightweight ammunition. With focused investments in research and development, improvements in ammunition cartridge cases are possible and with development can be ready for military use.
In 2016, the Project Manager for Maneuver Ammunition Systems (PM MAS) within the Joint Program Executive Office for Armaments and Ammunition (JPEO A&A, formerly the PEO for Ammunition), along with the U.S. Marine Corps, led an effort to establish a charter among key stakeholders that would help bring together requirement and materiel developers from all services.
The purpose of the Joint Lightweight Ammunition Integrated Product Team is to document the approach and to synchronize activities and investments across programs to achieve lightweight ammunition goals. The mission of the team is to collaborate on combat requirements, materiel developer solutions and joint qualification of lightweight ammunition using alternative case materials that would meet or exceed the performance of current brass-cased ammunition in standard service weapons. The objectives include activities that will support a successful transition to the single manager for conventional ammunition, which is represented by PM MAS. Moreover, the integrated product team used active international partnerships to gain valuable insight into active lightweight efforts within Britain’s Ministry of Defense.
Before the establishment of the team, each of the services was exploring lightweight ammunition, with little or no coordination. The efforts were often overlapping, and resources were not optimized to ensure product development within an established plan to deliver lightweight ammunition to the warfighter.
In the Army, the Joint Capabilities Integration and Development System-approved Family of Ammunition requirements (5.56 mm, 7.62 mm, .50-caliber) call for reducing the weight of ammunition. The Marine Corps and the U.S. Special Operations Command (SOCOM) continued to investigate lighter ammunition not only for their warfighters but for their aircraft operations as well. Reducing the weight of the ammunition allows aircraft to carry more ammunition to support critical missions, allows room for other critical supplies or creates additional fuel capacity for extended missions. The need to collaborate and learn from each service’s efforts is clear. The chartered integrated product team enabled the services to craft a joint road map that yielded immediate benefits by creating a common understanding of technologies available in industry.
FOCUS AREAS
The Joint Lightweight Ammunition Integrated Product Team meets twice a year, hosted by one of the core members, but remains continuously engaged to coordinate efforts. The focus of the biannual team meeting is to review ongoing efforts, look at test results and establish focus areas for upcoming activities.
During initial meetings, the services outlined the status of each of the ongoing and future programs and planned a joint road map, an overall approach to coordinating lightweight ammunition programs. Based on the working partners’ priorities, initial efforts fell into the following focus areas:
- Army—7.62 mm.
- Marine Corps—.50 caliber.
- British Ministry of Defense—5.56 mm.
Additionally, SOCOM continued to explore commercially available solutions that fit niche capabilities, thus increasing the knowledge base across the integrated product team. This has allowed each partner to successfully leverage emerging data from multiple industry solutions in various calibers to minimize the workload and maximize resources.
Under the integrated product team, the joint services assessed lightweight case solutions from seven potential sources, including traditional defense contractors as well as small businesses, which are considered nontraditional sources. The assessments looked strictly at requirements to demonstrate reliable function in legacy weapon systems while maintaining military-specified performance, which is more stringent than commercial standards. Primary challenges made apparent in testing include the ability to function reliably across extreme temperatures, the ability to maintain pressure and muzzle velocity, and the ability for the cases to properly eject from the weapon.
These robust performance requirements are balanced with the expected cost of manufacturing and any current capacity limitations on vendors for future manufacturing requirements. By coordinating within the Joint Lightweight Ammunition Integrated Product Team, the services can leverage results from multiple test events, which eliminates redundant testing and allows for a broad assessment across industry.
Lightweight ammunition technology and joint qualification efforts are moving forward thanks to the integrated product team’s activities. The 7.62 mm lightweight case program is a prime example of successful collaboration. Test results from lightweight case assessments by the Army, the Marine Corps, SOCOM and Britain’s Ministry of Defense demonstrated that several lightweight case technologies had the potential to meet military requirements.
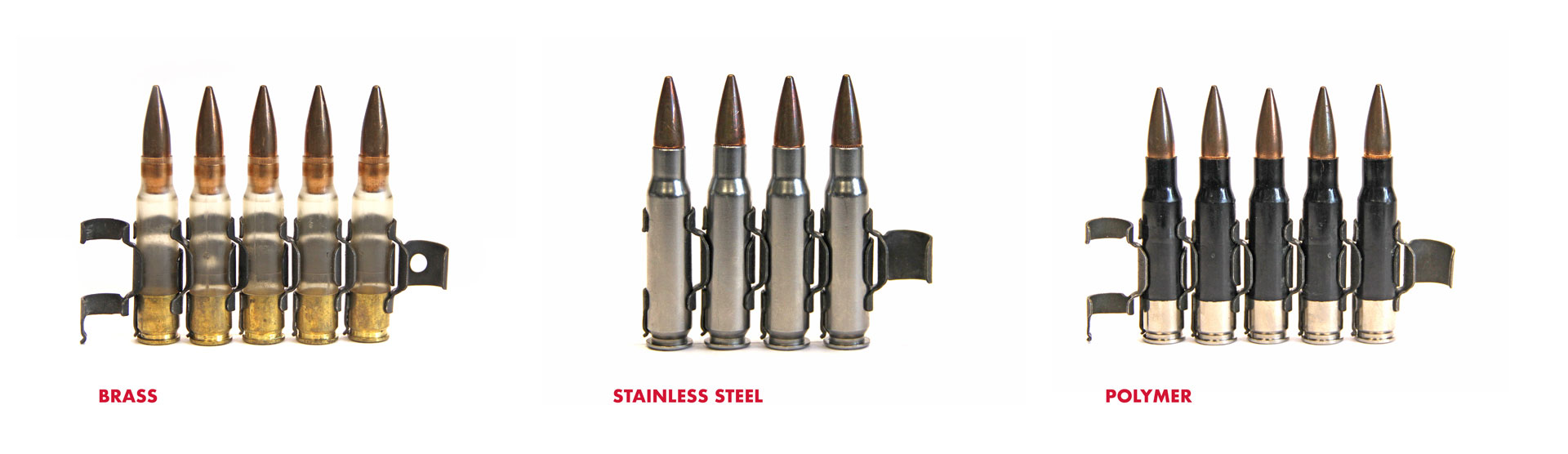
JPEO A&A has been evaluating concepts for new 7.62 mm ammunition casings for their weight and operational performance compared with traditional brass ammunition, left. The concepts include stainless steel casings, center, and composite casings with a stainless steel base and a polymer body, right. (Photos by JPEO A&A)
Based upon these assessments, the Army issued three competitively awarded contracts, the last of them in March 2019. The funding came from the Marine Corps and the Office of the Secretary of Defense Manufacturing Technology program to conduct a series of tests on early production designs. This limited test event, scheduled for October, will provide the information required to narrow down the top-performing design before engaging in final development and qualification test events.
Future activities for the integrated product team will include joint qualification of lightweight ammunition through a series of performance tests in current weapons. By establishing joint test plans, the team will reduce the number of test events and the quantity of rounds fired, thereby reducing the cost of qualification. Each service has distinct ammunition requirements within unique weapon systems, such as temperature and transportation environments. This coordination will ensure that the lightweight ammunition meets safety requirements as well as robust military uses in the various systems and is delivered to the joint warfighter much more rapidly than if tested and qualified independently.
Future activities also will include exploration of other efforts to save weight, including in ammunition links, (when ammunition is carried in a linked configuration) and in packaging, which will reduce the logistical burden during transportation.
CONCLUSION
As the services prepare for a future fight against highly capable adversaries, materiel developers will continue collaborating to increase operational capabilities and maintain overmatch. Combat and materiel developers will share and identify advancements in technologies across all weapon systems to reach that end.
Ammunition, as a fundamental component in warfighter load, is a key aspect of maintaining overmatch through technology. Collaboration through the Joint Lightweight Ammunition Integrated Product Team with the services and a key allied partner will lead to solutions that will significantly reduce ammunition weight and greatly enhance warfighter survivability and lethality through increased mobility on the ground.
For more information, contact the author at todd.n.townsend.civ@mail.mil, or go to https://jpeoaa.army.mil/jpeoaa/ or https://jpeoaa.army.mil/mas/.
TODD TOWNSEND serves as the research, development, test and evaluation supervisor for the Product Manager for Small Caliber Ammunition under PM MAS. He holds an M.S. in management from the Florida Institute of Technology, a B.S. in electrical engineering from Rensselaer Polytechnic Institute and a B.S. in physics from Roberts Wesleyan College. He is Level III certified in program management and in production, quality and manufacturing.
This article is published in the Fall 2019 issue of Army AL&T magazine.
Subscribe to Army AL&T News – the premier online news source for the Army Acquisition Workforce.
Subscribe