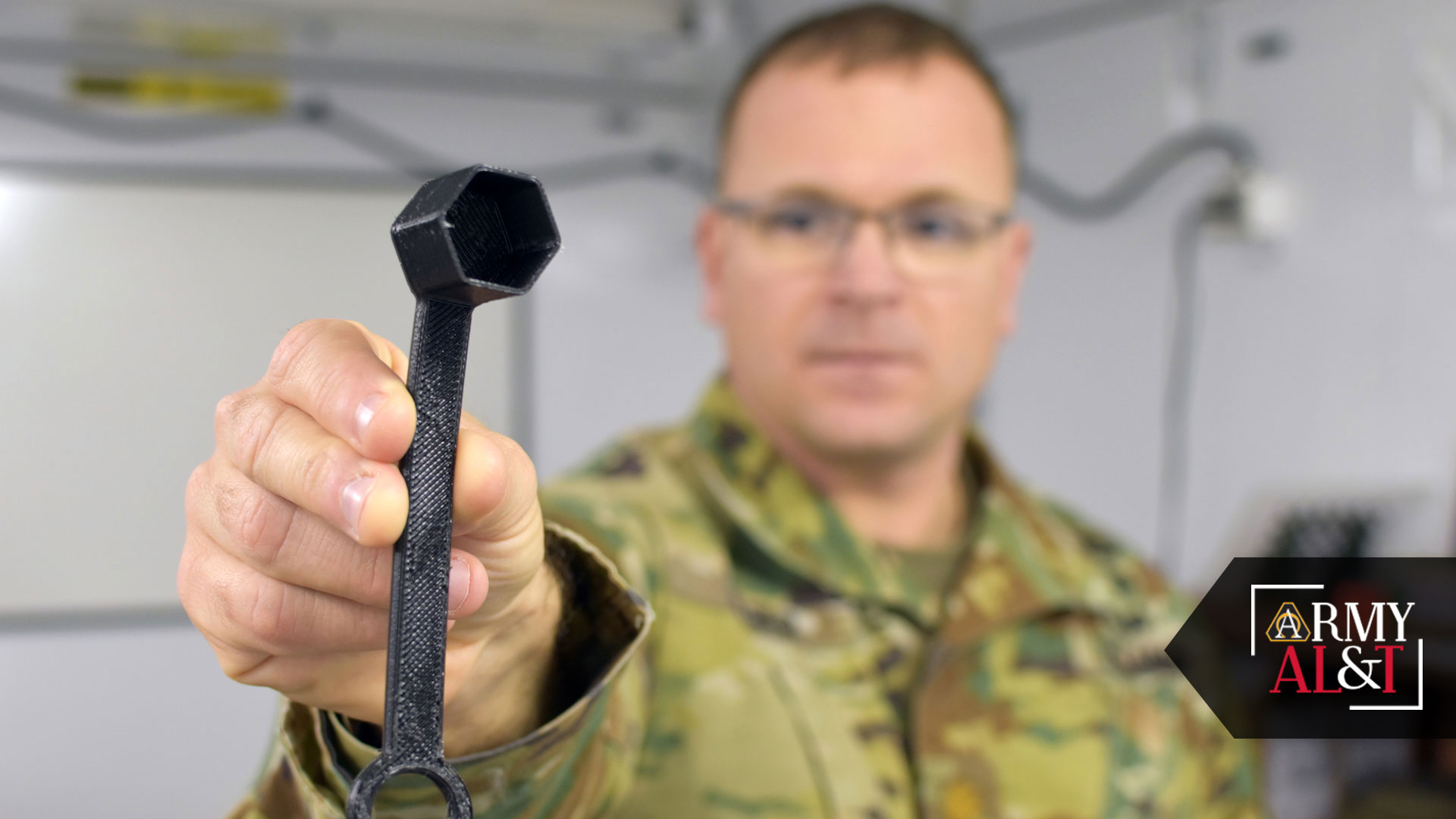
By Jacqueline M. Hames
In the future, what we call advanced manufacturing today will just be manufacturing. That doesn’t mean it will be obsolete, just that it will get more advanced. Henry Ford’s revolutionary assembly line is both outdated and not. We have plenty of assembly lines, just as Ford envisioned, but they’re vastly more efficient and effective—something he probably did not foresee. Even assembly lines outfitted in the past 30 years or so are no longer considered advanced, because the central quality of advanced manufacturing is that the technologies used are cutting-edge and near fruition.
“Computer numerical control [NC] in machining was considered advanced manufacturing in 1980,” said H. Edward Flinn, director of the Advanced Manufacturing Center of Excellence at Rock Island Arsenal – Joint Manufacturing and Technology Center (RIA-JMTC). “It shifted the workload from the shop floor, where a machinist manually operated a cutting tool path, to the office environment where an NC programmer wrote computer code to control the tool path.” Advanced manufacturing via artificial intelligence and feature-based recognition—algorithms that classify by feature—are now working “to minimize the need for NC programmers in the platform that would be used to machine a part, the tools that will be used and, of course, the tool path.”
The Advanced Manufacturing Center of Excellence reached full operational capacity in May, and its ultimate goal is to improve Soldier readiness, said Flinn, the center’s director. To do that, the center plans to use advanced manufacturing methods like process simulation, artificial intelligence, and 3D printing or additive manufacturing.
Flinn worked closely with the Army development and engineering centers (the former DECs, now part of the U.S. Army Combat Capability Development Command) to specify the capabilities the center of excellence should house. He has coordinated with HQDA to help develop a policy on supporting tactical use and requirements of advanced manufacturing, and has begun working with organic industrial base locations on their advanced manufacturing needs. Not only has the center has been working with the organic industrial base, but it has also been working with private industry, academia and the other services to leverage their best practices, he said.
Flinn said 3D printing offers point-of-use fabrication options, is competitive for small production and is a new method of manufacturing that opens up design freedom. In the past decade, 3D printing has gone from a method of making prototypes with little manufacturing applicability to becoming an integral part of the manufacturing process. Improvements in printing speed and accuracy, materials, cost and computer modeling-and-simulation systems have dramatically accelerated the technology’s use in manufacturing, he said. The technology can help the tactical Army right now, by providing on-demand, temporary replacement parts, he added.
While the center is currently focused on 3D printing, other advanced manufacturing techniques are being introduced into mainstream processes within RIA-JMTC. Those include the use of robotics, process simulation and material optimization, Flinn said. “Robotics is being used at the arsenal in the welding and investment casting processes to remove repetitive motion and improve process stability.” Investment casting comprises precise wax parts created using an injection-molding machine and a die that contains the shape of the part to be made, Flinn said. Smaller parts can be attached to a tree—a frame that enables batch-creation of the parts’ shells. This process can create almost any part for any piece of equipment—any part that can be created in wax can go through this process.
The wax object is then dipped in and coated with a wet refractory material—a ceramic slurry and sand that, when hardened, won’t be degraded by heat—and then the whole assembly goes to an autoclave that melts the wax away for reclamation, then onto the furnace to harden the ceramic refractory material, creating a shell. Any wax that’s left will be burned away in the furnace. Then, metal goes into the mold to make the part. Robotics helps to increase the efficiency, volume and speed of the process. Robotics “also allowed us to expand weight of the [investment casting] mold, which increased our yield and our range of parts that we could [make bigger]. The robot’s job is finished once the ‘dipping’ of the shell is completed. From there, it is removed from the process and hand-delivered to all follow-on operations.” (For more on how the process works, go to https://www.facebook.com/RIAJMTC/videos/670254872464/?v=670254872464.)
The center is also using process simulation whereby “we can, through mathematic models, recreate solidification and stress that are induced during the transformation of metal from a liquid to a solid.” This, Flinn continued, reduces the need to have an expert on casting on hand. It also helps to reduce costs by eliminating trial-and-error iterations on the shop floor. “The present system has shifted the need from a casting [expert] to a modeling and simulation [expert].” That parallels what happened with computer numerical control machining after its introduction.
Artificial intelligence has the potential to aid in shifting repetitive tasks from humans to machines—for example, combining AI with process simulation. “In combining the two, much of the human interface necessary to write NC programs, prepare process plans, design tooling and manage the logistic chain will be minimized, if not eliminated,” Flinn said.
Advanced manufacturing will be key to the Army’s future overmatch capabilities. “It provides opportunities to improve readiness, optimize design and lethality, drive down cost and expand the manufacturing base,” he said.
For more information read Getting started now.
This article is published in the Fall 2019 issue of Army AL&T magazine.
Subscribe to Army AL&T News – the premier online news source for the Army Acquisition Workforce.
Subscribe