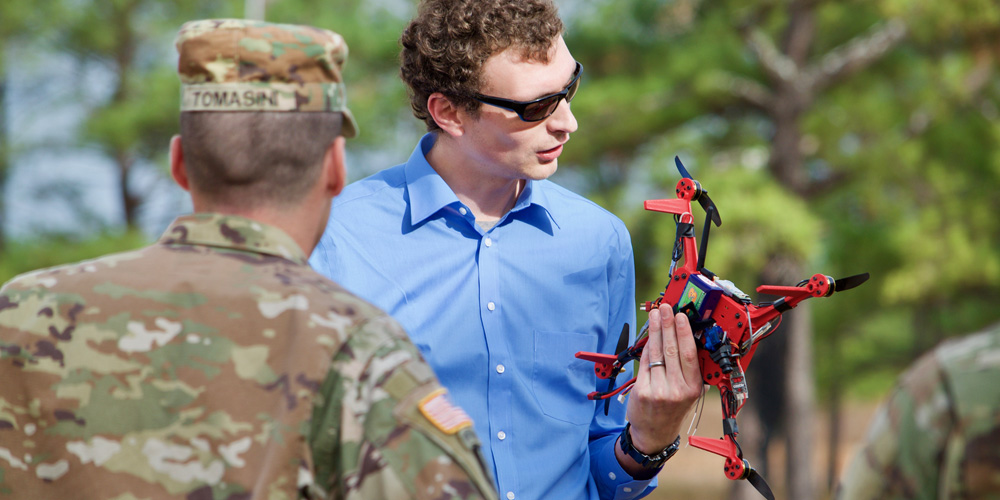
By David McNally, ARL Public Affairs
ABERDEEN PROVING GROUND, Md. (Dec. 28, 2016) — Soldiers witnessed the innovation of Army researchers recently during flight testing of 3-D printed unmanned aircraft systems that were created on-demand for specific missions.
The U.S. Army Training and Doctrine Command invited engineers from the Army Research Laboratory to Fort Benning, Georgia Dec. 1-3, to showcase new technology at the Army Expeditionary Warrior Experiments, or AEWE.
“We’ve created a process for converting Soldier mission needs into a 3-D printed On-Demand Small Unmanned Aircraft System, or ODSUAS, as we’ve been calling it,” said Eric Spero, team leader and project manager.
With this concept, once a patrol requires UAV support, Soldiers input all their requirements into mission planning software. The system then knows the optimal configuration for the aerial vehicle and it’s printed and delivered within 24-hours.
“We thought they’re not going to think that’s fast enough, but, actually it was the opposite,” Spero said. “The timeline of 24 hours to receive a mission-custom UAS fits right in line with the way they plan and execute their missions.”
Researchers said they felt the combination of 3-D printing and UAVs was a natural technology solution.
“Drones or quadcopters are really getting big right now, I mean in particular just the commercial and hobby markets have shown what can be done with a small amount of money,” said John Gerdes, an engineer on the project. “Additive manufacturing or 3-D printing has become huge and everybody knows all the great things that can be done with 3-D printers. So we figured let’s assemble these two new technologies and provide a solution to Soldiers that need something right now and don’t want to wait for it.”
The team spent many hours flight testing and verifying the designs and to make sure everything was going to work the way they expected.
“It was good that we didn’t have any mistakes on game day,” said fellow engineer Nathan Beals. “The day before we did some test flights and worked out some kinks. I think we had the quad up to 55 miles per hour.”
Spero said based on feedback from Army leaders, his team hopes to work on low noise, long standoff distance, heavier payload capacity and better agility.
I’m very optimistic that most of those are achievable. I think the hardest one that’s going to be achievable is the heavy payload.
Soldiers at AEWE also became fascinated with 3-D printing technologies, Spero said.
“Before we even started the briefing, we set up the 3-D printer in the conference room and started a print job,” Spero said.
The researchers printed a Picatinny Rail, which is a bracket used to mount accessories on a small arms weapon, such as an M4 carbine. In about two and a half hours, they had a rail that fit the Soldiers’ weapons perfectly.
They asked the group what other kinds of 3-D printed items they could use. In a matter of hours, the team presented a variety of functional printed parts that impressed the Soldiers.
This isn’t just about UASs,” Spero said. “It’s about forward-deployed, 3-D printing to help the Soldier.
The Army engineers continue to collaborate with partners at the Georgia Tech’s Aerospace Systems Design Lab as they continue to refine technologies for future Soldiers.

John Gerdes, an engineer with the U.S. Army Research Laboratory, explains the capabilities of the On-Demand Small Unmanned Aircraft System, or ODSUAS, to Soldiers at the Army Expeditionary Warrior Experiments, or AEWE, at Fort Benning, Georgia, Dec. 1, 2016. (U.S. Army photo by Angie DePuydt)
Subscribe to Army AL&T News, the premier online news source for the Acquisition, Logistics, and Technology (AL&T) Workforce.