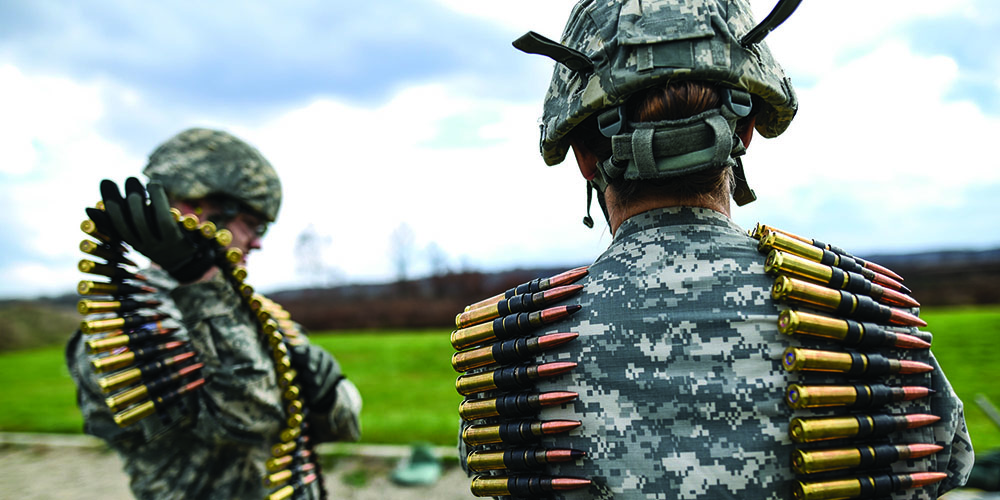
ARDEC and JMC worked together to develop an ammunition standard that reduces ambiguity, ensures quality and safety for Soldiers and promotes competition by making the procurement process more transparent for all stakeholders.
by Ms. Mary Kate Aylward
If the goal is to get more small businesses competing for government contracts, the government has several levers to pull to make that happen. One option is to make it easier for small businesses to compete—or, put another way, to level the playing field so that it’s no harder for small businesses to play. Clarifying requirements can foster competition and provide an opening for small businesses to enter a marketplace, whether used alone or as part of a broader package of incentives to increase small-business participation.
The Supplier Quality Initiative (SQI), a joint-services effort sponsored by the U.S. Army Materiel Command’s Armament, Research, Development and Engineering Center (ARDEC) and the Joint Munitions Command (JMC) to improve the reliability and quality of ammunition, is one example of just such a collaborative effort that has smoothed the way for greater competition.
Procuring high-quality ammunition wasn’t a new goal, but the way the SQI set about to achieve it was. Before the mid-2000s, every time the government ordered ammunition, the requirements could and did change—slightly, but enough to slow the supply chain and to make the ammunition harder to regulate and inspect. There were different requirements on different contracts, making it difficult for integrated product team (IPT) members to agree on what was required from suppliers.

READY FOR LOCK AND LOAD
No shortage of 5.56 mm rounds are ready for paratroopers from the 82nd Combat Aviation Brigade (CAB) 82nd Airborne Division to load into their M-4 carbines during a familiarization and qualification range at Fort Bragg, NC in July 2015. The SQI team wrote a review guide that expands on the CCC clause by providing examples and offering training opportunities at supplier facilities. (U.S. Army photo by SSG Christopher Freeman, 82nd CAB Public Affairs).
The process wasn’t transparent on either side: Suppliers weren’t always clear on what the government needed, and the government didn’t have a clear view of suppliers’ manufacturing processes or an easy way to evaluate them for safety and reliability.
Safety and reliability requirements were scattered across several different documents; in such an environment, an incumbent who had navigated the system before had an advantage over potential new suppliers who had to attempt to piece together the full picture from scratch.
SAFETY RISK, REDUNDANCY, CONFUSED SUPPLIERS
“From a warfighter’s perspective, it can all be summed up by saying we want that ammo to go off at our enemies when it’s supposed to and not when it’s not supposed to—in other words, that it be reliable,” said Greg Peterson, product quality manager at JMC.
The ammunition community had agreed that the best way to prevent the nightmare scenario (for example, a service member in a dangerous situation with ammunition that doesn’t work, or an ammunition defect that kills or injures a service member) was to prevent defective ammunition from ever leaving the factory. Ammunition has such a long life cycle that one defect at one manufacturing facility can cause problems decades later.
“We want to reduce the probability of a defect leaving the production facility to one in a million,” said Jorge Munoz, with the Small Caliber Munitions Quality, Reliability and Systems Engineering Branch at ARDEC, Picatinny Arsenal, NJ. But with different requirements and little transparency, there were gaps in the supply chain through which defective ammunition could escape. As engagements in Iraq and Afghanistan ramped up and demand for ammunition rose, it became clear it was time to fix the process.

SAFE PACKING
Joshua Nelson, a materials handler leader in the Shipping and Storage Division of the Directorate of Depot Operations, McAlester Army Ammunition Plant, OK, talks to Soldiers from the 578th Forward Support Company, Fort Sill, OK, about the process of drawing small arms ammunition and repackaging it for shipment, during a July 2015 tour of the plant. The consensus from the ammunition community: The best way to prevent injury or death caused by defective ammunition is to keep it from leaving the ammo plant. (Photo by Kevin Jackson, U.S. Army Materiel Command)
SIMPLIFY, CLARIFY REQUIREMENTS
In 2005-2006, a joint-services team was chartered to address these problems. The first change the team made was to round up all best practices and requirements tied to critical characteristics of a piece of ammunition—characteristics related to safety and reliability—and put them in a single document, the critical characteristics control (CCC) clause. Lean Six Sigma principles helped the team develop the CCC clause. A single clause laying out all the safety-critical requirements for any ammunition reduces the amount of time and work it takes for the government to acquire ammunition. It reduces ambiguity for manufacturers, better enabling them to deliver. And it makes it easier to hold suppliers accountable and therefore deliver safer, more reliable ammunition to Soldiers, Marines, Sailors and Airmen.
“The system had a lot of noise prior to the implementation of a single clause accepted as the standard for ammunition quality,” said Sanket Patel, chief engineer with the Expeditionary Systems Evaluation Division at the Crane Division of the Naval Surface Warfare Center Fallbrook Detachment. Now, every time the government orders ammunition, the CCC clause is a part of the order. The standards to keep the ammunition supply safe and reliable are in a single place, and they’re the same every time. Clear requirements put an incumbent and a potential new supplier on a more level playing field, while unclear requirements give a strong advantage to an incumbent who has institutional knowledge from having performed the work before.
The clause-development team evolved into the Joint Munitions and Lethality Life Cycle Management Command’s SQI. Not only was the SQI team successful, but the model it created continues to be used and has driven business-process innovation and improvement in other contract quality requirements. The model pioneered with the CCC clause has carried over to process control (Process Capability, Control and Improvement Clause) and inspection (Measurement System Evaluation clause). (See “Clause for Effect,” Army AL&T magazine, April – June 2014, Page 130; and “Process Capability, Control, and Improvement Clause Allows Enhanced Process Monitoring and Control,” Army AL&T magazine, January – March 2011, Page 66.)
INVOLVE STAKEHOLDERS
Patel described the SQI as “a partnership, in many ways, between the government and private industry.” The industrial base—made up of contractor-owned, contractor-operated manufacturing facilities, government-owned, contractor-operated facilities, and government-owned, government-operated manufacturers—was involved throughout the process.
At the outset, “we didn’t just say, ‘Here’s the clause,’ ” Munoz noted. Each side had concerns to be acknowledged: Government needed industry to understand the real risk of critical defects—service members could be injured or killed, weapon systems damaged and defense capability decreased while supplies and systems are re-inspected or repaired. Suppliers, on the other hand, felt that government had been “gold-plating” requirements, disregarding the reality of a manufacturing environment.

ADJUSTING THE LINKS
Small caliber ammunition is as essential to Soldiers as food, water and boots. The SQI team aimed to make it safer, and the process of procuring it more transparent for both the government and suppliers. (U.S. Army photo)
An industry day was held where suppliers came to ARDEC and reviewed the draft critical characteristic requirements. Similar industry day events have been held for other clauses before implementation. This provides a frank and collaborative forum to raise questions and concerns and to preview the requirements so nothing in a contract or solicitation comes as a surprise.
The team also sought buy-in from in-house stakeholders, including management, contracting officers, contracting specialists and legal staff. Technical requirements that were not contractually or legally feasible would result in rework and potentially longer project schedules, so keeping all parties up to date saved time.
HELP THEM HELP YOU
Before the development of the single, joint CCC clause, some contractors had problems interpreting requirements such as calculation of critical plan-of-action threshold measures, or when a critical defect has officially “escaped” beyond the inspection point. To help contractors and manufacturers understand the requirements, the SQI team also wrote a review guide that expands on each paragraph of the clause, providing concrete examples, and offered training at supplier (government and contractor) facilities.
“[The review guide] is a very important tool—it gives the government and the contractors producing ammo a common framework to understand the requirements,” Patel noted. “We use the guide internally to help our new engineers and new QA [quality assurance] specialists come up to speed.” By being as clear as possible about what it wants and needs, government creates an environment where more suppliers can compete, and where suppliers can be transparent, too.

SHARPENING FIRING SKILLS
U.S. Army Reserve Soldiers from the 354th Military Police Company, St. Louis, MO, wait their turn to fire the M2 Browning .50-caliber machine gun during a familiarization range at Camp Atterbury, IN, in November 2015. The SQI goal is to improve the quality of ammunition Soldiers receive—and a benefit of the steps taken to that end is that more suppliers of all sizes can compete. (U.S. Army photo by MSG Michel Sauret)
MEASURING SUCCESS
Surveys of stakeholders, along with observations made over the years the CCC clause has been in effect, indicate that the SQI’s innovations have been a success. Since 2007 and continuing every year through annual discussions at the Joint Ordnance Commanders Group, Quality Assurance Subgroup meetings, Single Manager for Conventional Ammunition Quality Assurance Day events, data calls to IPT representatives, and during SQI events themselves, ARDEC and JMC survey stakeholders and customers to gather feedback. “The result is it’s been working out fine,” Munoz said.
Collaborating with industry through training events at supplier sites and open communication has generated a particularly positive response: “[Suppliers] are always happy to see us,” Peterson noted. “They always want more information.” Much of the dialogue occurs between the SQI team and IPTs; the SQI team provides an independent, requirements-centric view to the IPT. In addition, these information exchanges offer multiple opportunities for feedback on how the clause and review guide are working on the ground. As a result of this active feedback, the review guide has been revised twice (2012 and 2015) since its original release in 2006 to improve the guidance and capture best practices.
Another key measurement of the SQI’s success is the number of critical plans of action (CPOAs) filed by suppliers. CPOAs are an optional tool for suppliers to describe their plan to reduce the number of nonconformances at a facility. “The number of CPOAs we’ve been receiving has grown every year … compliance is growing,” Patel said.
CONCLUSION
“Clear requirements help current contractors do better, and they invite others into the supplier base, so it invites competition. We want a healthy supplier base, and we have to be clear about what we want,” said Patel. More competition, better product and reliable ammunition in the hands of the warfighter: That’s what the SQI’s CCC clause has accomplished for the long term.
For more information, contact Melanie Lorber, CCC clause manager for JMC, at Melanie.p.lorber.civ@mail.mil.
MS. MARY KATE AYLWARD provides contract support to the U.S. Army Acquisition Support Center. A writer and editor at SAIC, she holds a B.A. in international relations from the College of William & Mary.
This article was originally published in the January – March 2016 issue of Army AL&T magazine.
Subscribe to Army AL&T News, the premier online news source for the Acquisition, Logistics, and Technology (AL&T) Workforce.