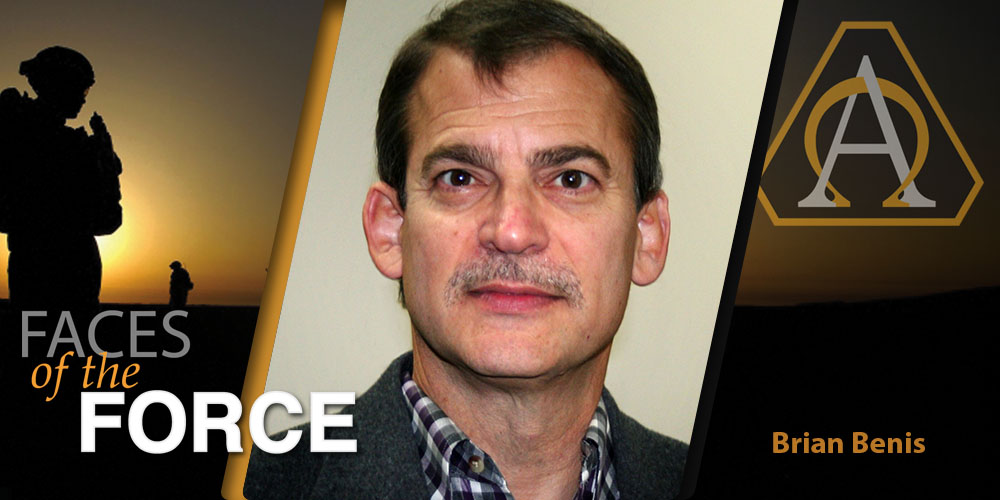
COMMAND/ORGANIZATION: PEO Missiles and Space, Lower Tier Project Office (PATRIOT)
Title: Hardware engineer
DAWIA Certifications: Level III in engineering, production and quality management; Level I in program management
Years of Service in Workforce: 29
Education: B.S. in mechanical engineering, University of Arizona
Awards: Order of Saint Barbara; Achievement Medal for Civilian Service
Sustaining a signature system
By Mary Kate Aylward
Brian Benis has been taking things apart for as long as he can remember—a clock radio here, a desktop fan there—because he was curious about how they worked. That lifelong fascination earned him his mother’s constant refrain of, “You’d better put that back together before your dad comes home!” but also led to a degree in mechanical engineering and, right after graduation, a job with the Army.
Benis isn’t taking things apart and putting them back together anymore—at least, not on the job—but he is taking apart problems that Soldiers identify and engineering solutions to keep the PATRIOT system viable while reducing the cost of sustaining it. Those Soldiers are the guiding force behind his work, and he considers them more than customers or end-users, but rather mentors. That’s why keeping them satisfied and making sure they’re confident in the system are equally important.
Benis came to Army acquisition before the program executive office structure developed, and has supported the PATRIOT missile program for most of his 29-year career. The backbone of the United States’ missile-defense architecture, the PATRIOT has long been a high-profile system: The deployment of PATRIOT missile batteries signals strategic American commitment. And it’s a successful sustainment story. PATRIOT has been around since the Cold War, and has been continually upgraded since then in response to evolving threats and improving technology. Benis has been a part of this sustainment project for much of the system’s lifespan.
What do you do and why is it important to the Army or the warfighter?
Most of my time is spent dealing with hardware upgrades. Typically there will be an item with a high failure rate that needs to be redesigned and requires an additional skill set to remedy. One example is an engineering change that I am currently working on—our number-one priority engineering change. It has to do with the liquid cooling system for the radar and is currently one of the largest influences on downtime and support costs. This engineering change is going to upgrade the system using aircraft-grade coolant lines and more robust heat exchangers, and will reduce refurbishment costs as well.
I have also been involved in the transition to the Configuration 3 upgrade, which was a major enhancement from a blast fragment warhead to a hit-to-kill design, and major upgrades to the ground support equipment as well. The changes have been quite numerous over the years, not only because the threat has changed but also because technology has evolved—making some components obsolescent, and opening up new possibilities.
I am successful with my engineering changes because I stay highly involved in the root-cause analysis of the problem as well as the design, testing and review of user feedback related to the upgrade or modification. This is important to ensure the sustainment of the PATRIOT system and keep it viable for many years.
How did you become part of the Army Acquisition Workforce, and why?
A professor sent my resume to the Product Assurance Directorate and ultimately, I got a job offer over the phone. I started working for the Army because our nation deserves the best equipment. I felt that my knowledge of mechanical and electromechanical devices would be a great asset to the Army to ensure that our Soldiers have the best equipment possible.
What do you see as the most important points in your career with the Army Acquisition Workforce, and why?
I never say no to a challenge and the Army is full of them. The greatest challenge that I have faced is gaining the trust of the user of the system. I take great pride when I am able to improve the Soldier’s experience with what we are fielding. The most important thing to me is when I see failure rates decreasing with the cost of sustainment.
Can you name a particular mentor or mentors who helped you in your career? How did they help you? Have you been a mentor?
Most people have senior management as mentors. I consider the user of the system as my mentor. The Soldiers who use the PATRIOT missile system have helped me in many ways. I listen to their needs and try to provide them with the best product for the least amount of money.
What’s the greatest satisfaction you have in being a part of the workforce?
My greatest satisfaction is when I hear fewer complaints about hardware. The PATRIOT missile system is subjected to a very tough environment and to be part of a redesign or upgrade that survives the abuses of being out in the field brings me the most satisfaction.
What advice would you give to someone who aspires to a career similar to yours?
Listen to the people who are using the equipment that you are providing.
“Faces of the Force” is an online series highlighting members of the Army Acquisition Workforce (AAW) through the power of individual stories. Profiles are produced by the U.S. Army Acquisition Support Center Communication and Support Branch, working closely with public affairs officers to feature Soldiers and civilians currently serving in a variety of AAW disciplines. For more information, or to nominate someone, please call 703-805-1006.
Subscribe to Army AL&T News is the premier online news source for the Acquisition, Logistics, and Technology (AL&T) Workforce.
Subscribe