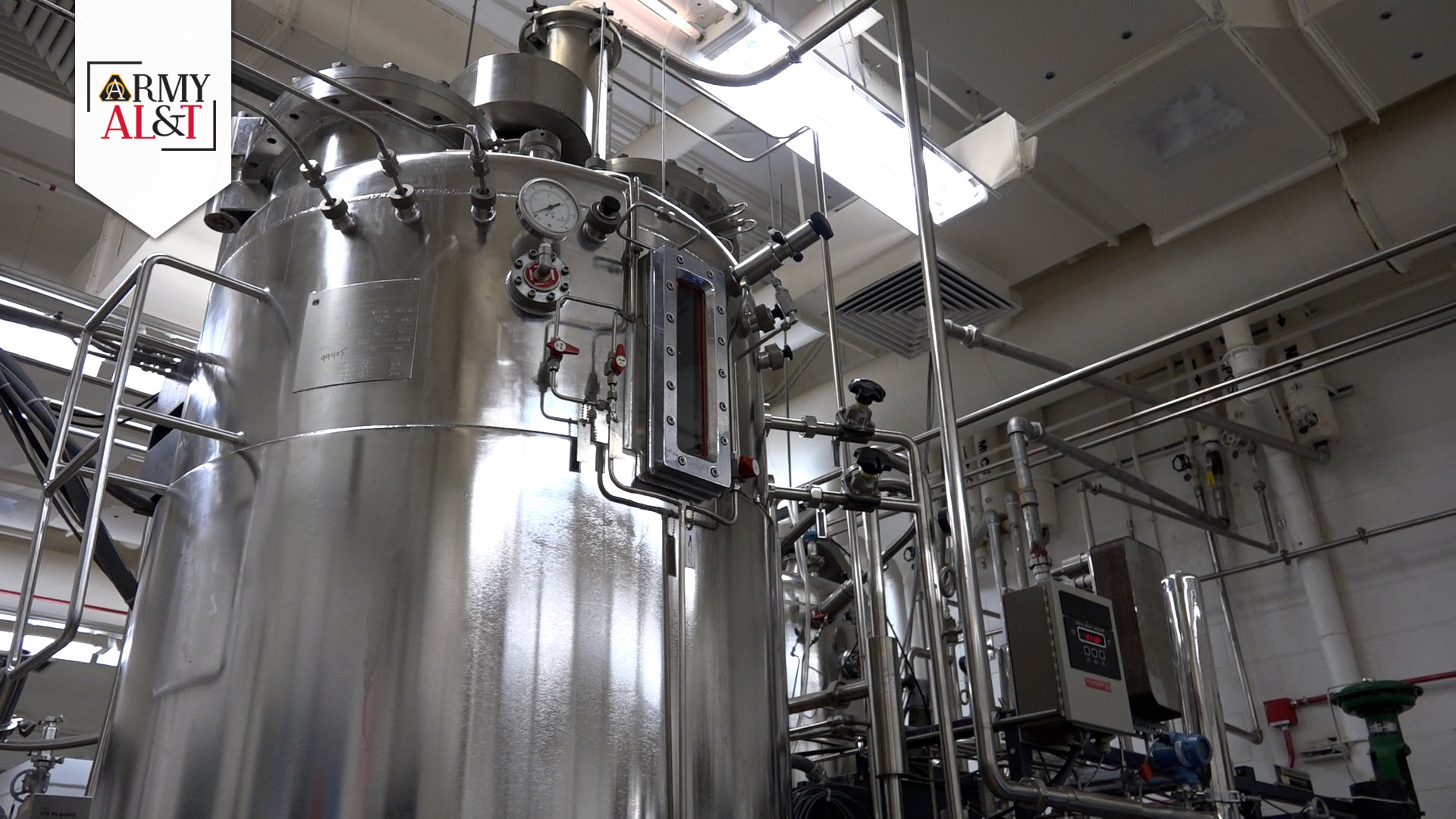
FERMENTATION IN VATS: DEVCOM Chemical Biological Center’s Biomanufacturing Facility can scale biomanufacturing processes in up to 1,000-liter fermentation vats. Once a process is proven at this level, it can be transitioned to industry for further scaling to production. (U.S. Army photo by Gabriella White)
Biotechnology is key to sustainable domestic production of high-value defense materials.
by Henry S. Gibbons, Ph.D. and Brian B. Feeney, Ph.D.
The COVID-19 pandemic exposed weaknesses in U.S. manufacturing that have been developing for years. Decades of outsourcing of U.S. industry had rendered supply chains vulnerable before COVID-19. Pandemic-related disruptions to global supply chains laid bare the fragility of just-in-time production methods using extensive foreign sourcing of components. Over the last 40 years, the corporations controlling U.S. wartime production capacity have dispersed those manufacturing facilities around the world to take advantage of cheaper labor.
Leaders in Washington and the Pentagon have begun to address this issue, both by promoting the return of production to the United States and by leveraging the nation’s global leadership in the burgeoning field of biotechnology. On Sept. 22, 2022, President Joseph R. Biden issued Executive Order 14081. It orders the DOD to incentivize the expansion of domestic, flexible industrial biomanufacturing capacity for a wide range of materials needed for the nation’s defense. This order reflects the realization that, just as with software and artificial intelligence, nations that can harness biomanufacturing for their national defense will possess a vast military advantage over those that cannot. To ensure that, the DOD is investing $1.5 billion in materials biomanufacturing and synthetic biology over the next five years.
The DEVCOM Chemical Biological Center is doing its part to meet this national security need by helping to usher in a new bioeconomy. It has built, and is now expanding, a 20,000-foot biomanufacturing facility at its research campus at Aberdeen Proving Ground, Maryland. Scientists inside the plant use DNA-engineered cells to manufacture materials in 1,000-liter vats. Biomanufacturing enables the creation of high-performance, high-value materials by controlling the growth environment and genetic makeup of the organisms that make them. The Center is uniquely able to do this by bringing together its world-class chemical engineering and molecular biology subject matter experts to finesse the fermentation process.
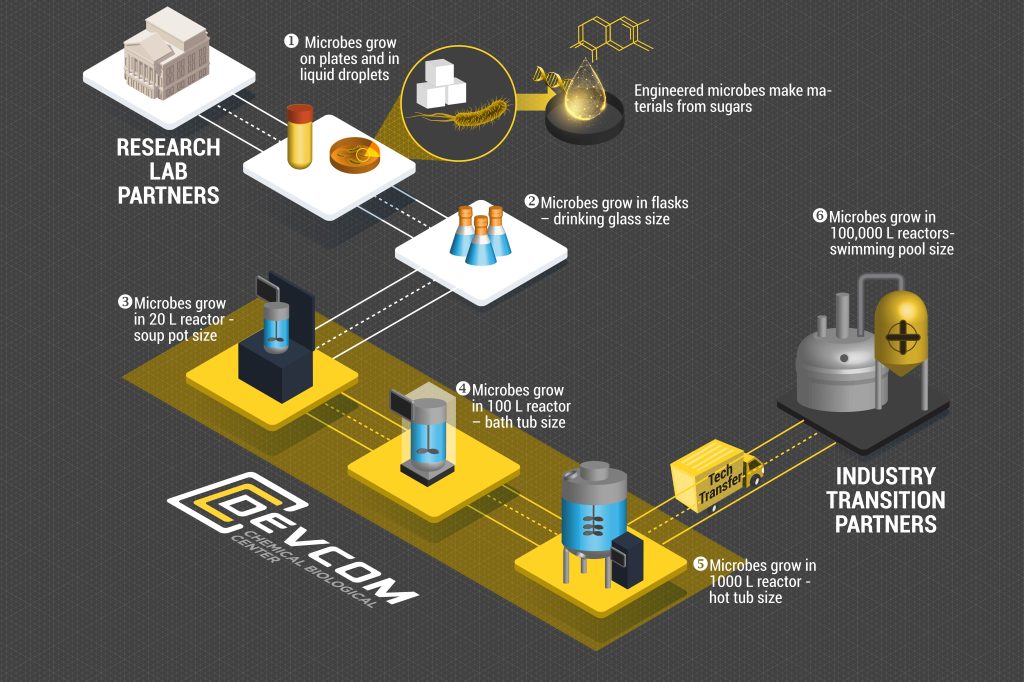
THE BIOMANUFACTURING PROCESS
Army’s DEVCOM Chemical Biological Center collaborates with research lab partners, like the DEVCOM Army Research Lab, to scale up biomanufacturing processes for high-value materials, with the goal of transitioning those processes to industry for bulk production for national defense applications. (U.S. Army graphic by Dr. Anna Crumbley/Addie Huynh)
WHAT IS BIOMANUFACTURING?
According to 42 USC § 18901(4), the definition of biomanufacturing is “the utilization of biological systems to develop new and advance existing products, tools, and processes at commercial scale.” Biomanufacturing uses microorganisms to make products in a way that’s similar to how a neighborhood microbrewery uses yeast to produce beer. The range of products that can be biomanufactured is limited only by scientists’ ability to use genetic engineering to reprogram the central metabolism of those cells. Billions of these engineered microorganisms are suspended in a watery liquid in a fermentation vat and fed sugars and salts. As more and more of this material is produced, it is taken out of the vat and turned into precursors for products such as explosives, reactive coatings and textiles, optical and sensor materials or new therapeutics including vaccines. Or it can produce more ordinary—but much needed—materials such as the rubber in tires, polyurethane for cushion foam or the polyethylene that makes plastic bottles. In effect, these microbes are miniature factories programmed to make the high-value molecules needed by American industry and the military.
The process begins inside a research laboratory where scientists reprogram a microbial cell’s DNA to make it produce a desired chemical instead of, or in addition to, simply replicating itself. Designing these changes in the cell’s operating system is comparable to opening a new app on a smartphone—a change in the program renders an entirely different set of operations. Recent advances in DNA engineering have made this possible and the science is advancing rapidly. Biomanufacturing represents an industrial revolution and holds the potential to enhance existing materials and produce new ones. The possibilities include:
- Living textiles for environmentally interactive uniforms.
- Light-bending camouflage for warfighters, vehicles and aircraft.
- Decontaminating lotions that last a lifetime with a single application.
- High-performance fuels generated without a conventional refinery.
- Heat-resistant protective surfaces for applications that require thermal protection.
- Jam-resistant bioelectronic computing components.
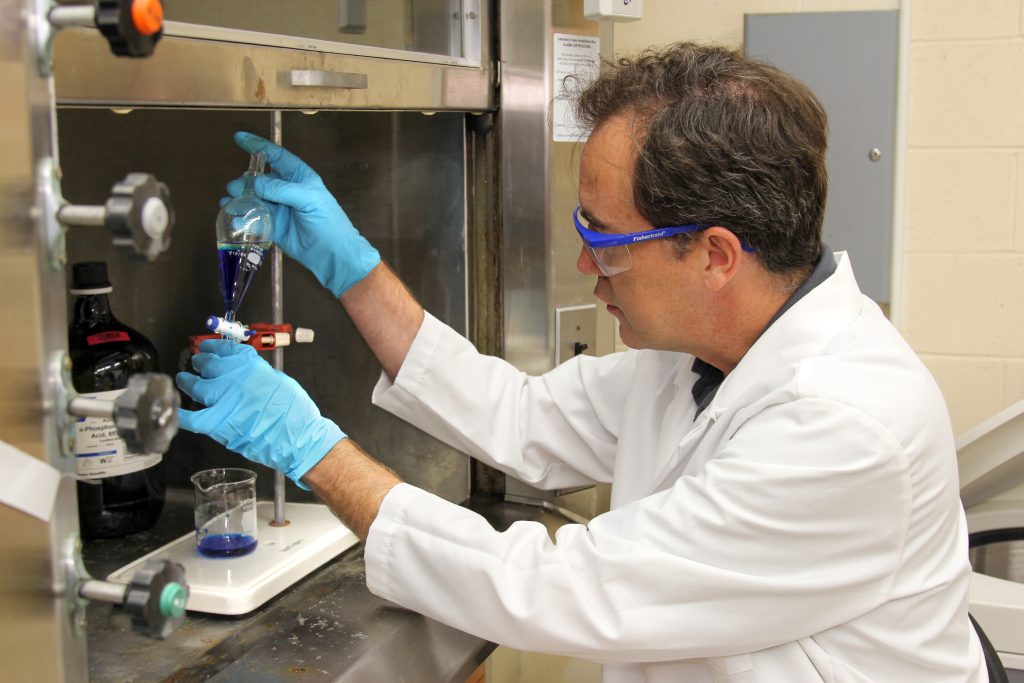
FINESSING FERMENTATION
DEVCOM Chemical Biological Center’s Dr. Henry Gibbons demonstrates a solvent-based extraction process using oil and colored water to remove biomanufactured material from the watery fermentation broth in June 2023. (U.S. Army photo by Gabriella White)
VATS VS. SMOKESTACKS
By using plant-based feedstocks, biomanufacturing brings many advantages over petrochemical-based production. Biomanufacturing operates at lower ambient temperatures and pressures which reduces utility costs and environmental impacts. It uses fewer toxic materials such as industrial solvents. Petroleum plants consume more energy and have a far more elaborate logistics train. Petrochemical facilities rely on an oil supply, much of which is controlled by foreign governments.
Also, petroleum-based manufacturing is a relatively stagnant technology compared to biomanufacturing, where the science and technology are ever improving. In academic and military research laboratories all over the nation, chemists and biologists work with systems engineers and use artificial intelligence to steadily improve upon the three essential elements of biomanufacturing:
- Increasing the sophistication of DNA engineering to produce new kinds of materials, including as-of-yet unconceived of materials.
- Improving the effectiveness of the fermentation process in the vats to increase material yield.
- Refining the methods for extracting the useful material that microbial organisms generate, also increasing yield.
If you think about the emerging biomanufacturing infrastructure as a landscape, what you see is an archipelago of research laboratories in which scientists are hard at work creating new strains of DNA-engineered microbial organisms. These organisms, and the chemical processes for extracting the desired product, are tested and optimized using small-volume cultures in bench-scale chemical glassware. If a journey of a thousand miles begins with a single step, so the journey to industrial-scale production begins with one flask. Industry needs the new material available at the kilogram quantities or greater. Within DOD, a consortium of laboratories is emerging that will deliver biomanufactured products and processes to industry. The DEVCOM Chemical Biological Center and the DEVCOM Army Research Laboratory hold key roles in that effort.
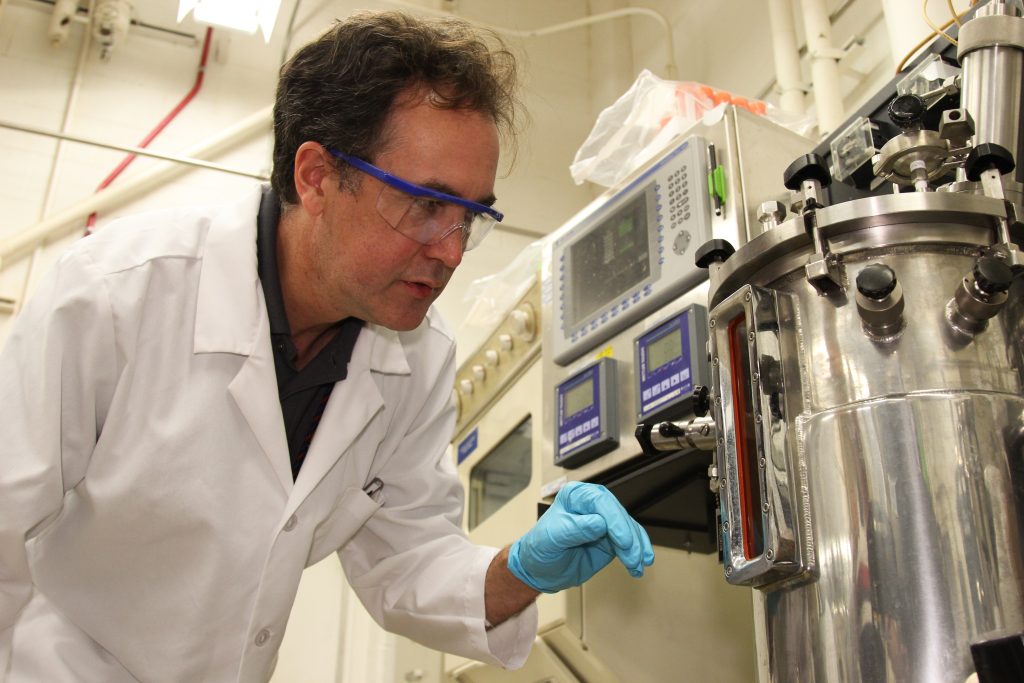
MAINTAINING THE RIGHT ENVIRONMENT
Dr. Henry Gibbons monitors the growth of a microbial culture in a 20-liter fermenter in June 2023. Industrial fermenters are equipped with electronic process controls that allow scientists to monitor conditions within the bioreactor and maintain a constant favorable growth environment for producing microbes. (U.S. Army photo by Gabriella White)
ORGANISM DISCOVERY AND ENGINEERING
DEVCOM Army Research Laboratory typically takes the first look at newly engineered microbial organisms being considered for scale-up production using their specialized synthetic biology expertise. In effect, DEVCOM Army Research Laboratory finds the microbe best suited to generating the desired product via biomanufacturing plants like DEVCOM Chemical Biological Center’s biomanufacturing facility. They prospect for new strains by scouring the scientific literature and through their partnerships with other defense laboratories, research universities and industry.
Once DEVCOM Army Research Laboratory has a good candidate organism, their scientists work on making it better at its intended function. That can mean finetuning the DNA using genetic engineering to narrow down the activities of the organism so that more of its metabolic energy goes into producing the desired material, thereby increasing the yield. Or it could mean making the organism more survivable in the vat by ruggedizing it so that it better tolerates the other ingredients inside the vat. This effort is usually performed below the one-liter scale, and once DEVCOM Army Research Laboratory has made improvements and verified the performance of the microbe and the material it produces, it hands the organism off to the DEVCOM Chemical Biological Center for scale-up.
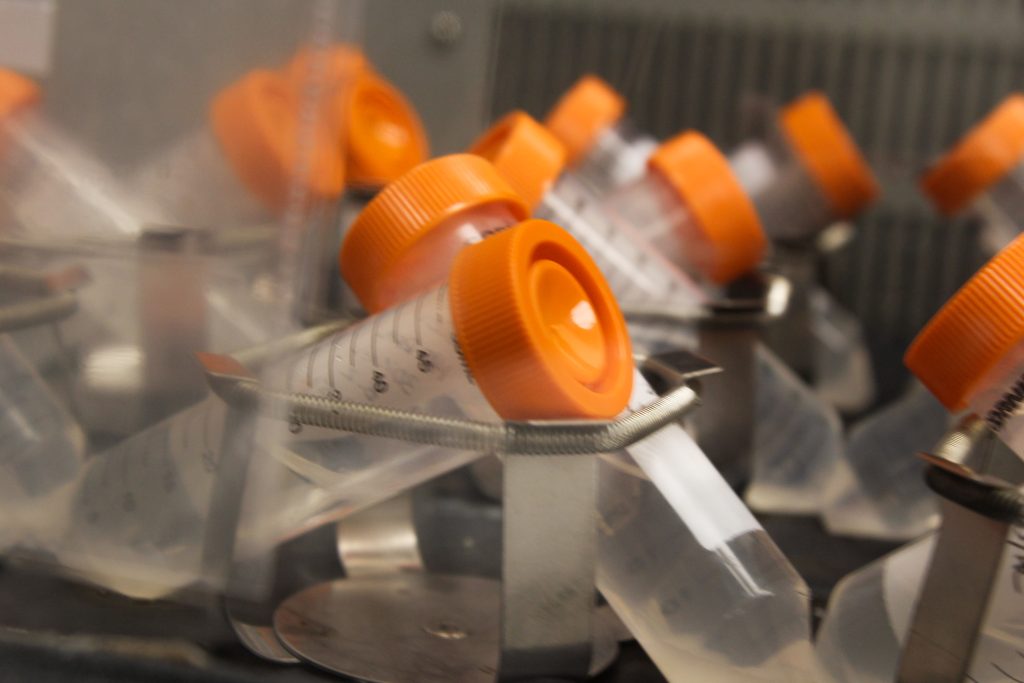
FINDING THE BEST SUITED MICROBE
DEVCOM Army Research Laboratory scientists evaluate microorganisms to find the microbe best suited for scale-up production of materials via biomanufacturing. (U.S. Army photo by Jack Bunja)
PRODUCTION AT SCALE
Getting from flask-size to 1,000 liters as a scale-up for industry use is an exacting process. It requires scientists and engineers who are seasoned in the art of enhancing the strains that basic research laboratories discover. The DEVCOM Chemical Biological Center biomanufacturing team creates the best conditions for them to thrive inside the vats. This includes placing them in the right-sized vats at the right time and placing just the right mixtures of salts and sugars in the vats. They optimize aeration and mixing inside the vats to keep the microbials producing the new material consistently and in large quantities. The team seeks to maximize each strain’s ability to precisely create the material it was designed to produce and do it with the greatest yield possible.
The biomanufacturing team also works with DEVCOM Chemical Biological Center engineers to devise the best way to extract these new materials from the vats, which are full of nutrient soup. To do this, the Center pulls together a project team of professionals from across the organization to create the right mix of skills and knowledge. Throughout the process, from strain discovery and process optimization to full-scale production, information flows between the DEVCOM teams involved. This shared knowledge enables them to continuously make improvements to the process. The result is that when the Army hands off the scaled-up process to its industry partners for commercial production, those partners get an optimized organism and an optimized production process.
BETTER EQUIPPED WARFIGHTERS
Everything that DEVCOM Chemical Biological Center and DEVCOM Army Research Laboratory scientists and engineers do to support the biomanufacturing facility is with the warfighter in mind. A more complete domestic defense supply chain means more certainty in getting the warfighters what they need when they need it. Developing new, specialized materials increases warfighter lethality and survivability. Better artillery propellants increase range, better composites for body armor and combat vehicles makes them robust and enables warfighters to stay in the fight. Jam-resistant bioelectronic computing components keeps warfighters communicating and coordinating on the battlefield. The range of benefits to the warfighter expands with every new material discovered, optimized and scaled up to industrial production.
CONCLUSION
The world is on the cusp of a bioindustrial revolution made possible by the blurring of the divisions between the digital and biological technology and advances in genetic engineering. It is likely to disrupt all prior industrial technology, with all the military applications that implies. Its military impact may be on the same scale as the transition from sail to steam, horses to armored vehicles, and propellers to jets.
DEVCOM Chemical Biological Center stands poised to function as the DOD’s go-to agency for enhancing and scaling up the manufacture high-value chemicals and materials of military value for hand-off to industry. This places it in a key role in the larger national project of developing America’s bioindustrial base and driving the evolution of the nation’s arsenal of democracy.
For more information or to contact DEVCOM Chemical Biological Center, go to https://www.cbc.devcom.army.mil.
HENRY S. GIBBONS, PH.D., is a research microbiologist at the U.S. Army Combat Capabilities Development Command Chemical Biological Center where he serves as principal investigator on research and development programs in synthetic biology, biomanufacturing and chemical and biological defense. He also serves as the Army’s Deputy Program Manager for the DOD’s Triservice Biotechnology for Resilient Supply Chains program. He holds a Ph.D. in biochemistry from Duke University and a B.A. in chemistry from Amherst College.
BRIAN B. FEENEY, PH.D., is a public affairs specialist at the U.S. Army Combat Capabilities Development Command Chemical Biological Center where he writes news and feature stories on the science and engineering achievements of the Center’s researchers. He has written for the Center since 2014. He holds a Ph.D. in risk communication from Temple University, an M.A. in communications from Cornell University, and a B.A. in history from Colorado College.