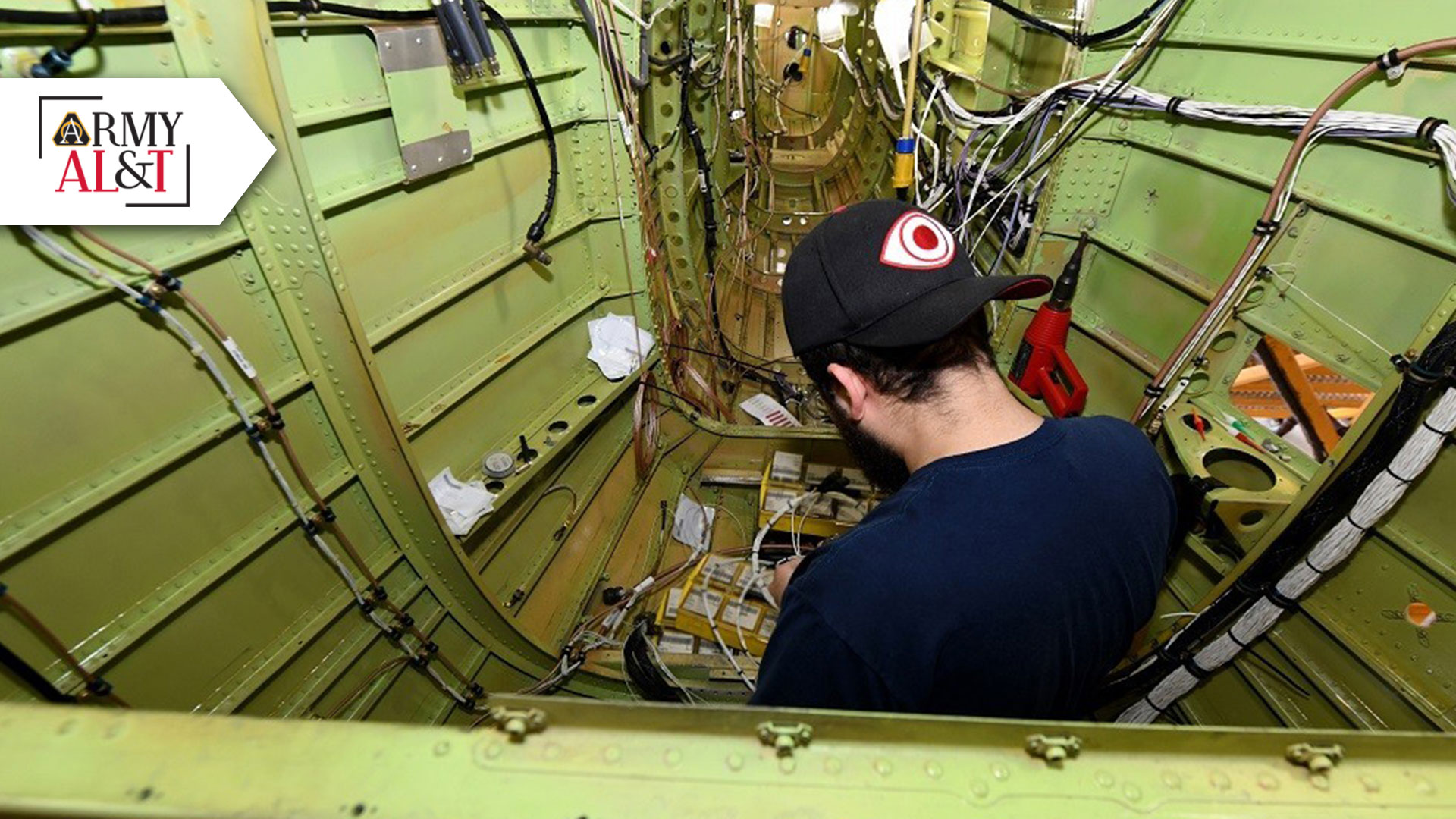
FIRST OF MANY: John Farhat installs wiring for a UH-60L Black Hawk communications system inside the aircraft tail section at the Corpus Christi Army Depot. This is the first aircraft to be painted using 100 percent, chrome six-free Class N primers. (Photo by Ervey Martinez, Corpus Christi Army Depot)
AMCOM is working to remove heavy metals from Army aircraft to ensure the health and safety of aviation personnel.
by Jacqueline M. Hames
In some jobs, there is an inherent danger that simply cannot be avoided—urban window-washers risk falling from great heights; Soldiers risk being shot during wars. But others have dangers that can be avoided. Aviation production and maintenance workers have been working with dangerous contaminants for many years, but the Army is putting a stop to that.
The U.S. Army Aviation and Missile Command (AMCOM) is developing new ways to eliminate heavy-metal exposure from the workplace. Heavy metals are any naturally occurring metallic chemical elements that have a relatively high density, such as mercury, cadmium, arsenic, chromium, thallium and lead. Some, such as zinc and iron, are required for good health in small amounts, but in larger amounts can be toxic. Others are just plain toxic in any amount—mercury, cadmium, arsenic. AMCOM is eliminating the heavy metals in the aviation fleet, in part, through use of a new anti-corrosive coating—a Class N primer. But getting the primer into the manufacturing process and onto existing aircraft isn’t exactly easy.
William Quinn, chief of operational safety in AMCOM’s Safety Office, and Mark Feathers, program manager for AMCOM’s toxic metal reduction program, sat down with Army AL&T over the summer to talk about how their organization is making the workplace safer for Soldiers and civilians.
ENVIRONMENTAL HOTLINE AMCOM’s Environmental Hotline is available 24/7 at 256-313-1711 to report heavy metals or exposure to heavy metals. You can also reach safety personnel via email at usarmy.amcom-environmental@mail.mil. |
STEEL FRAME—RUSTED
Corrosion is a natural, if undesired, part of the aviation life cycle. Rust—a type of iron oxide—is one of the most common forms of corrosion and it can easily degrade metal equipment, helicopters and other vehicles in regular use if they don’t have an anti-corrosive coating.
“If you have iron in an oxidated environment, what will happen is the oxygen will adhere to the iron and it will form iron oxide,” Quinn said. “Over time that starts to break down and it forms more and more and more, until you get to the point where the iron oxide is basically all that’s left.” In other words, unprotected metals break down when exposed to oxygen and moisture.
One particular heavy metal, hexavalent chromium—also known as chromium-6 or chrome six—is used widely in aviation as an anti-corrosive protective layer. “Hexavalent chromium is a corrosion inhibitor that has been used in processes for over 50 years,” Feathers said. Some of those processes include hard chrome plating, anodizing of aluminum and magnesium—which allows for better primer adhesion—sealants, adhesive bond primers, and as post-treatment sealing for other processes, like cadmium plating, and pretreatment of aluminum. “Coatings interrupt the corrosion process or minimize its ability to occur,” he said.
AMCOM has been working for more than a decade to mitigate heavy metals exposure—they specifically began researching hexavalent chromium in 2006. The organization has always followed Occupational Safety and Health Administration (OSHA) and U.S. Army safety guidelines for permissible exposure limits, Quinn explained. But when the Army adopted the ACIGH (American Conference of Governmental Industrial Hygienists) lower hexavalent chrome exposure limit standard in 2018, this heavy metal’s days became numbered. The new ACGIH standard is about 10 times more restrictive than the previous OSHA standard, Quinn said.
“We put together a heavy metals working group at AMCOM [in 2018] and we literally tested every single operation that had heavy metal exposure—specifically chrome six—and identified the levels, the risk and what we needed to do to bring those facilities into line,” Quinn said. Because AMCOM started working on hexavalent chromium mitigation and replacement more than 10 years ago, it is now meeting the more rigorous 2018 standards, he added. The Army’s heavy metals working group and those working the Army’s toxic metal reduction program are a large part of that success.
The Army’s toxic metal reduction program has worked with AMCOM to develop alternatives for hazardous constituents in the products used in aircraft and missile weapon systems depot and field maintenance processes. “We leverage existing technology or develop new ones” to do so, Feathers said.
One of those new methods is the Class N primer, which does not contain chrome six.
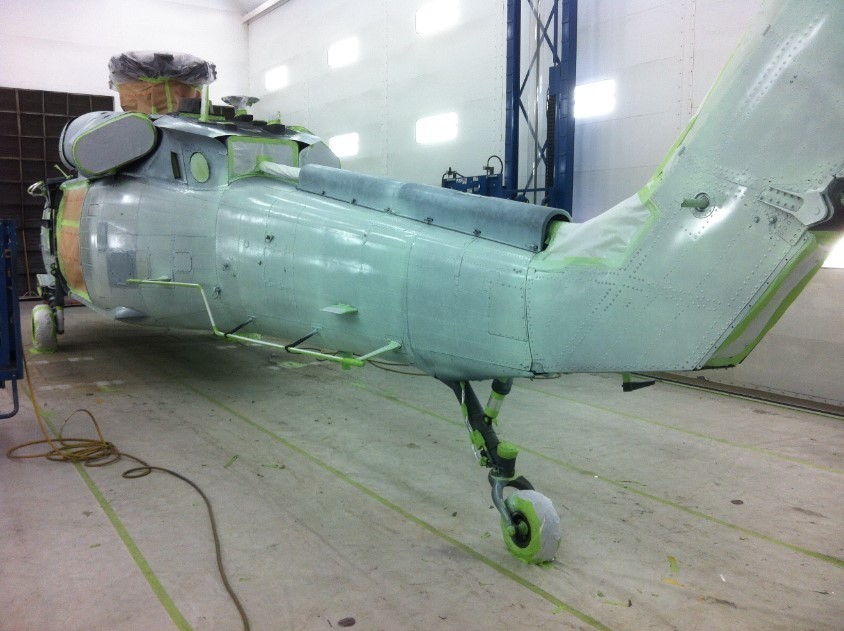
PRIMED AND READY: Class N Primer applied to UH-60 at 1107th TASM-G, at Springfield, Missouri. (Courtesy Photo)
PRIMED
To remove heavy metal additives from the fleet, specifically hexavalent chromium, AMCOM must replace the anticorrosive coatings on current aircraft with the newly approved Class N primers.
“The [Class N] primer is an epoxy coating that is applied over the pretreatment—which is on the base metal—and is designed to provide corrosion protection and also serve as a base layer to the polyurethane topcoat,” Feathers explained. “The polyurethane topcoat is a chemical agent-resistant coating and does not contain hexavalent chromium.”
Feathers described these coating layers as similar to the ones you can buy at your local hardware store, but with much higher performance.
But before the new primer can go on, the old coatings have to be removed. “There is a cleaning process to remove any contaminants before a chemical pretreatment coating is applied. Only then can the primer be applied,” he said.
The Class N primer is applied to everything from the aircraft airframe to the components that go on it, like the gear box and transmissions made of magnesium, to all the many small parts on the aircraft. “You name it, just about every part gets primer on it,” Feathers said.
The primer is applied using high-volume, low-pressure paint sprayers, applied at a specific thickness, and is usually tack free in about five hours and fully cured in 14 days in normal conditions, Feathers said.
It can take up to 300 hours to prepare and coat the aircraft with primer, he added.
DRIVING THE CHANGE
Hexavalent chromium is extremely harmful to humans and the environment, which is why AMCOM is prioritizing its removal in its effort to remove heavy metals from the Army’s aviation fleet. It can cause kidney and lung damage, as well as damage to DNA. It can leach into groundwater and cause damage to the ecosystem, Feathers explained.
For example, most people know the story of Erin Brockovich’s litigation against Pacific Gas & Electric Co. (PG&E), settled in 1996. The company had used hexavalent chromium cooling towers to fight corrosion at a Hinkley, California, natural gas compressor station. The toxic wastewater from the towers was drained into unlined ponds and contaminated the groundwater, affecting an area of about two square miles around the station. “Of course, families in the neighborhood were drinking that stuff and [it caused] a cancer cluster in that area,” Feathers said. PG&E is still working to clean up the site.
Maj. Gen. K. Todd Royar is driving AMCOM’s push to remove current toxic coatings from the fleet and to incorporate new, nontoxic primers into the manufacturing process. Royar told Quinn that he didn’t just want to meet current requirements, he wanted to exceed them—to be the leader in safety for aviation.
“So we put together a safety assessment and a risk analysis of all the operations within the Army, in the whole Army. And I was able to break it down to specifically those operations where we had hexavalent chrome exposure. We were able to present this to the Department of the Army heavy metal working group. As a result of that presentation, we became a member of that Army-level group and continue to communicate the results of our efforts to hopefully help others following in our footsteps,” he said.
AMCOM is attacking the heavy metals problem from both ends—Feathers and the team at the toxic metal reduction program are identifying, certifying and qualifying all the products that will replace hexavalent chromium, and Quinn and the Safety Office are “working with the heavy metals working group to help facilitate policy change at the Army level to allow for use of the alternatives. So it’s a two-pronged approach,” Quinn said. “We call it our top-down, bottom-up approach. Maj. Gen. Royar embraced this strategy and has engaged throughout this process on both ends. His efforts have pushed us where we have broken new ground, gotten further than I thought we could, and are now starting to see impacts across the Army, DOD and even with our partner equipment manufacturers.”
SAFETY FIRST
AMCOM is using mechanical methods, like plastic media blasting, to remove the coatings with heavy metals from aircraft. It’s not an ideal method, as the dust created from the process poses a risk to personnel and therefore requires personal protective equipment. “AMCOM is investigating alternative removal methods,” Feathers said.
“AMCOM performs routine testing at its industrial operations where there is potential for hexavalent chrome exposure and provides standard and certified personal protective equipment,” Quinn added. “Traditionally, when levels exceeded OSHA standards, additional precautions are taken. These include performing workforce medical surveillance, use of engineering controls including air shower, exclusion areas and special equipment with HEPA [high efficiency particulate air filter] vacuums attached, and use of personal protective equipment such as Tyvek suits and respirators. All this has been done to isolate areas of risk and prevent hexavalent chrome particulates from sanding and grinding processes from impacting our workforce and migrating to common areas,” he said.
“The hardest exposure areas to control are field operations, since limited facility control and oversight are present. That is why replacing hexavalent chrome products is so critical to the health of Soldiers and the workforce,” he said.
If Soldiers or civilian personnel are identified as being in an area with potential exposure to chrome six or heavy metal dust, they are fitted for a respirator, Quinn explained. Each person must have the respirator fitted specifically for his or her own use, and the filters must be checked for clogs and deterioration regularly, he said.
Safety officers perform “swipe tests” of the area, according to ACGIH standards, to monitor the level of hexavalent chromium dust in the air. Personnel in these areas are also checked medically. “If it’s determined that an area has elevated chromate levels, at that point we ensure our employees in that area are medically tested. That medical surveillance includes regular blood tests and things of that nature to ensure our workforce remains safe,” Quinn said.
Recently, Quinn performed an inspection at a paint shop at Corpus Christi Army Depot, AMCOM’s aircraft industrial facility in Texas. While performing his inspection, the facility manager approached Quinn and showed him around the shop. “He says, ‘Are you working with the team that’s eliminating the hexavalent chrome from the process?’ I said, ‘Yeah, yeah, we are.’ He … shook my hand and he said, ‘I want to thank you,’ ” Quinn said. “ ‘You’re making a safer workplace for us and that makes a difference.’ ”
“We have literally removed a health risk from the work environment, ultimately removing the risk to our workforce, removing the requirement for them to be medically surveilled,” Quinn said.
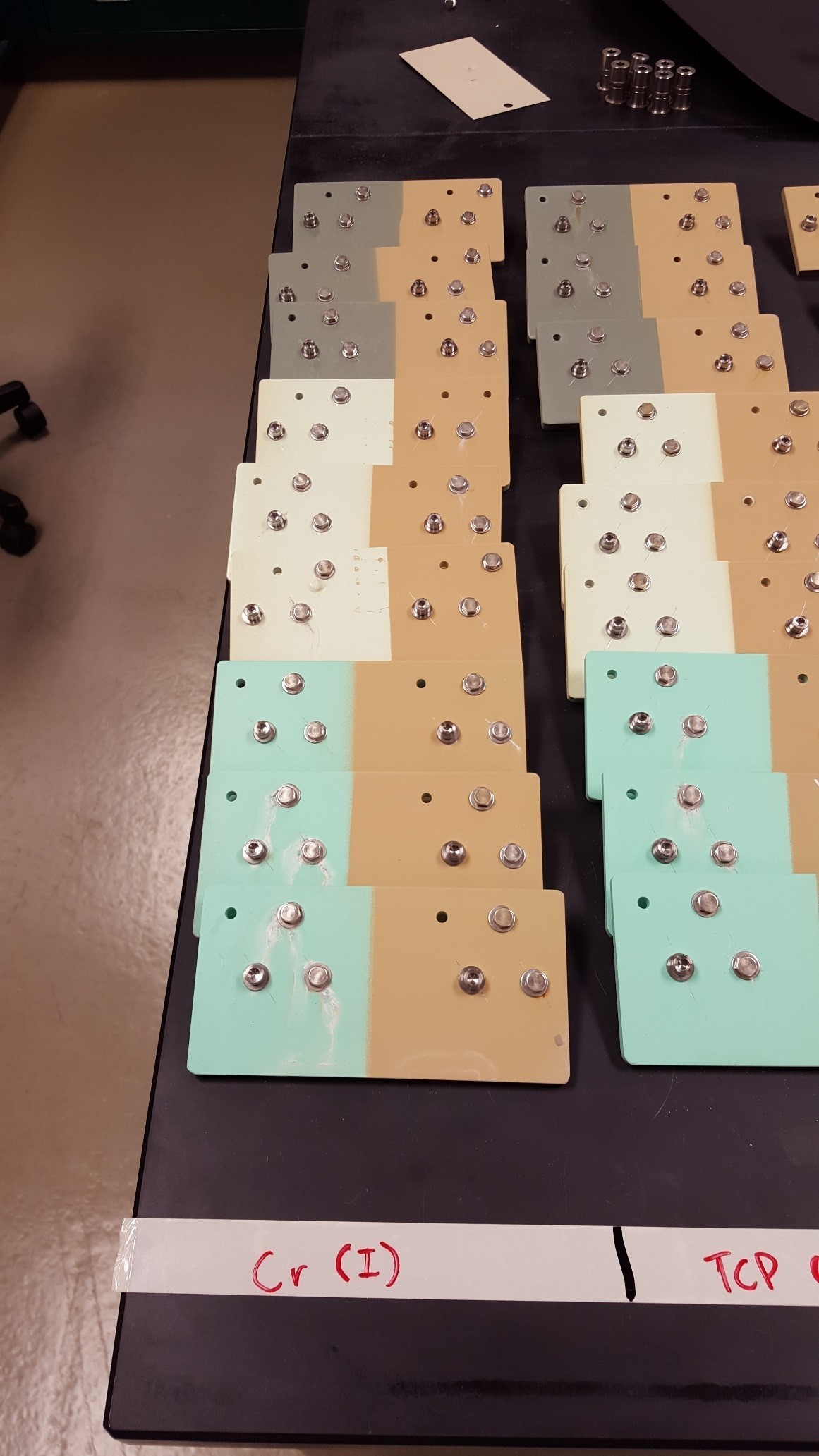
ACING THE TEST: Class N primers undergo laboratory corrosion testing. At right, with topcoat, at left, without topcoat. (Photo by AMCOM)
CONCLUSION
AMCOM is pursuing a number of heavy metal mitigation and replacement projects, beyond hexavalent chrome, to help ensure the health and safety of its workforce, Feathers said. But the removal of hexavalent chromium primer remains AMCOM’s current focus because it is so widely used and affects so many different installations. Three other efforts are being concurrently worked for hexavalent chrome removal. Zirconium oxide, which removes hexavalent chromium from many treatment processes, is in the final stages before implementation. It should go into use near the end of this fiscal year. In addition, AMCOM is already using tagnite, another pretreatment coating, on magnesium aircraft parts at Corpus Christi Army Depot. Replacement of sealants containing hexavalent chromium used throughout aircraft is also being addressed, and is expected to be pushed to the fleet by the end of the year.
The process of retrofitting the current fleet and incorporating Class N primers into the production line can get expensive—establishing a new plating line could cost $3 million or $4 million, Feathers said—but it’s worth it.
“The cost associated with supplies and equipment—while not insignificant—pales in comparison to that of health care costs and loss of experienced professionals in the workforce due to illness,” Quinn said. “The real cost savings is in the health and well being of the workforce, a healthy workforce means longevity, stability and sustained productivity.”
“Under the leadership of Maj. Gen. Royar, we helped build a diverse and capable Army team, identified a common issue, developed a protection and replacement strategy, validated alternatives, obtained Army approval for the alternatives use and built consensus across aviation commands to stop using hexavalent chromium,” he said.
AMCOM’s goal is to remove or mitigate heavy metal risks to the Soldier and the Army’s sustainment workforce. This effort will enable all aircraft that will remain in the Army’s inventory to become chrome six free. In addition, these advances are being communicated to the rest of DOD and industry to remove them during initial production. However daunting, AMCOM hopes to remove hexavalent chrome from the fleet by the mid 2030s.
“The Army and our higher command, the Army Materiel Command, are committed to a safe environment for its workforce and Soldiers,” Quinn said. “This hexavalent chrome replacement program on Army aircraft is just one example where AMCOM is playing our role in that commitment.”
For more information, go to https://www.amcom.army.mil/.
JACQUELINE M. HAMES is an editor with Army AL&T magazine. She holds a B.A. in creative writing from Christopher Newport University. She has more than 10 years of experience writing and editing news and feature articles for publication.