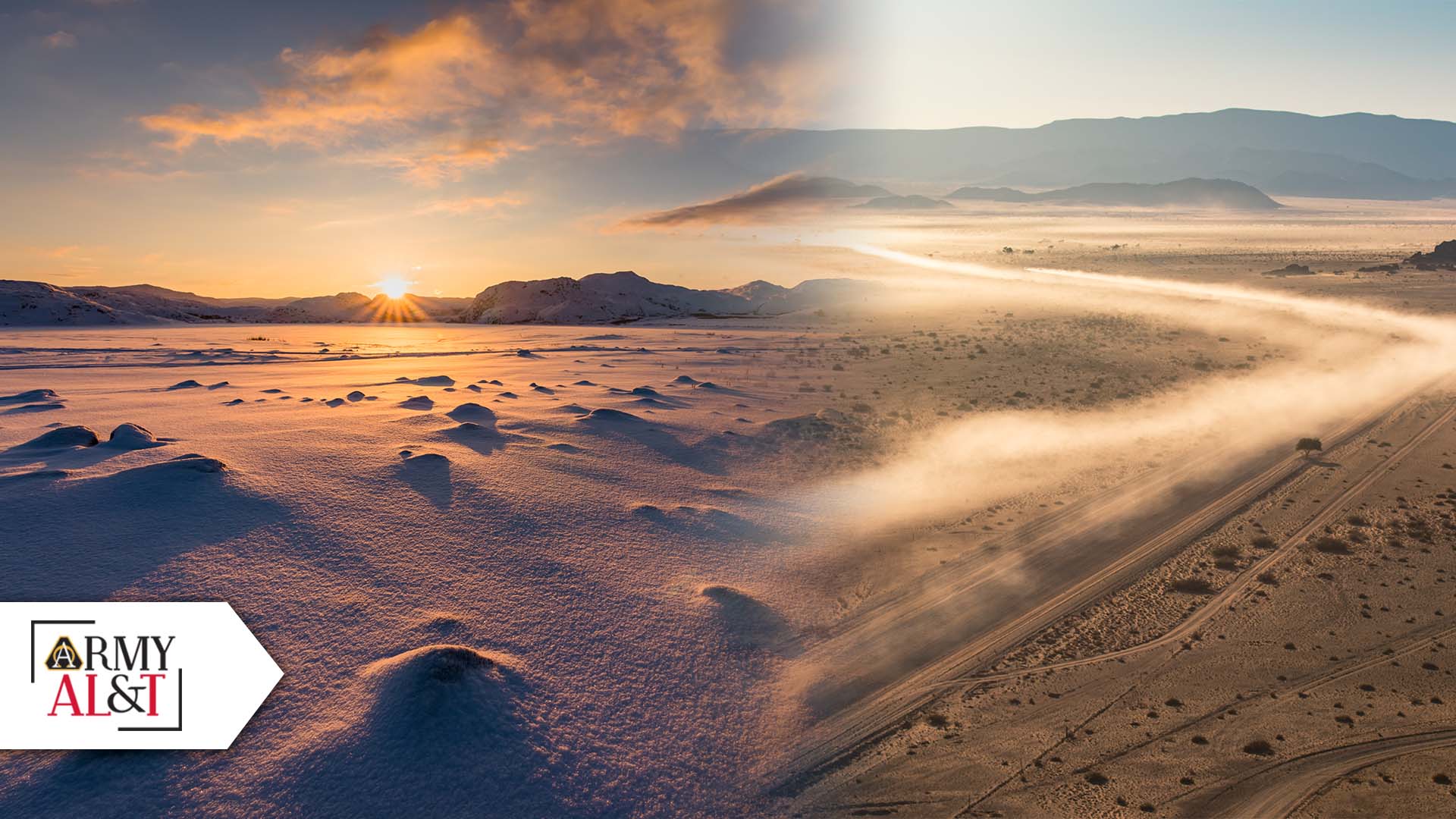
THE BIG CHILL: The Arctic tundra of Murmansk, Russia, at sunset. Murmansk features a subarctic climate with long and cold winters and short cool summers. In the city, freezing temperatures are typically experienced from October through May. (Photo by Getty Images)
For years, the Army has used ambient temperature extrapolation as a shortcut for test and evaluation, but electronically controlled powertrains have changed things and the Army test community is identifying new risks from an old Army practice—and potential cost savings.
by Steven Zielinski and Paul Maguire
Military vehicles have some of the most demanding automotive specifications, requiring operation in extreme environments ranging from arctic (50 below) to desert (120) conditions. (All temperatures are Fahrenheit.) During development, U.S. military vehicles must be tested successfully in those conditions. That’s problematic because no test center in the U.S. gets that hot long enough to test accurately at 120. The Cold Regions Test Center in Alaska meets Army regulation for ambient temperature (Army Regulation 70-38, “Research, Development, Test and Evaluation of Materiel for Worldwide Use”). However, testing for desert conditions often occurs below the 120-degree threshold.
As a result of test program schedule constraints, test vehicle availability, proving ground selection and other factors, military vehicle mobility performance is often tested in the window of only 90 to 110 degrees. Is this good enough when the requirement is 120 degrees? What are the risks to our Soldiers operating these vehicles in desert warfare? By not testing at this upper extreme, vehicles may not be able to reach top speed, climb steep hills or tow disabled vehicles without overheating or suffering catastrophic damage.
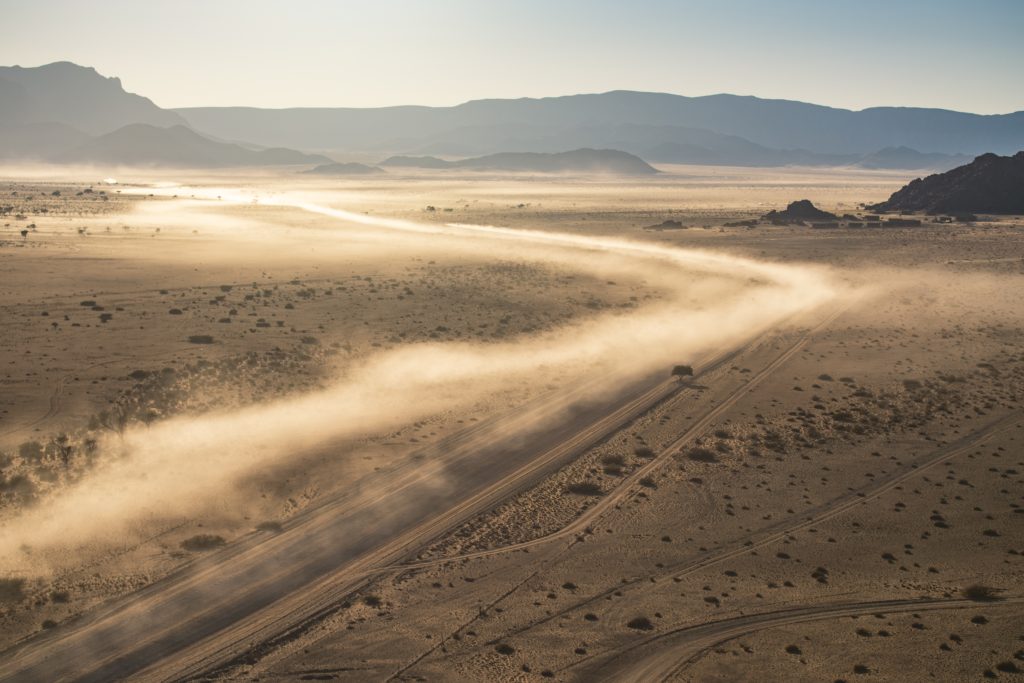
SCORCHED: The hottest temperature every recorded in Namibia’s desert was 115 degrees. (Photo by Getty Images)
THE REALITY OF T&E
In the development cycle of a tactical or combat vehicle, the cost of test and evaluation can represent a significant portion of the program’s research, development, test and engineering (RDT&E) budget. Indeed, vehicle test costs can run into the hundreds of millions of dollars. In a Spring 2018 article in Army AL&T, Dr. Robert Mortlock of the Naval Postgraduate School wrote that the cost of test and evaluation in the Ground Combat Vehicle was a whopping $417 million.
Where are legitimate places to reduce testing cost? The matter of temperature extrapolation might provide a clue.
To address the temperature issue, the Army has been using a linear extrapolation of powertrain test data based on the ambient temperature.
While it sounds technical, “linear extrapolation” is a very simple method of predicting results by extending a trendline beyond verified test data. While this has worked fairly well for almost 50 years, the standard may no longer be as valuable as it once was.
Many ground vehicles within the U.S. Army’s fleet are either newly introduced or have undergone significant modernization in the last several years. Specifically, the vast majority of the fleet no longer uses mechanically controlled powertrains, but are now operating on electronically controlled powertrains. The difference between mechanical and electronic control is best explained by an example. In the years before electronic control gradually took over virtually all of the vehicles on American highways, it was not uncommon to see overheated cars, hoods open and steam pouring out, on the side of the road during the hottest months of summer. That is nearly nonexistent today. The difference is electronic control. The engine is controlled by a computer that employs manufacturer-proprietary algorithms that prevent the vehicle from going past certain thresholds.
When linear extrapolation is applied to electronically controlled powertrains, the results suffer from significant error or may be invalid entirely. Linear extrapolation has limited uses where it can be trusted, and electronically controlled powertrains is not one of them.
Everyone who has ever tried investing knows that drawing a trendline on past financial data doesn’t account for all—or even any—of the economic variables that will set future pricing. Like the stock market, electronically controlled powertrains operate on complex algorithms that are influenced by too many variables to trust linear extrapolation.
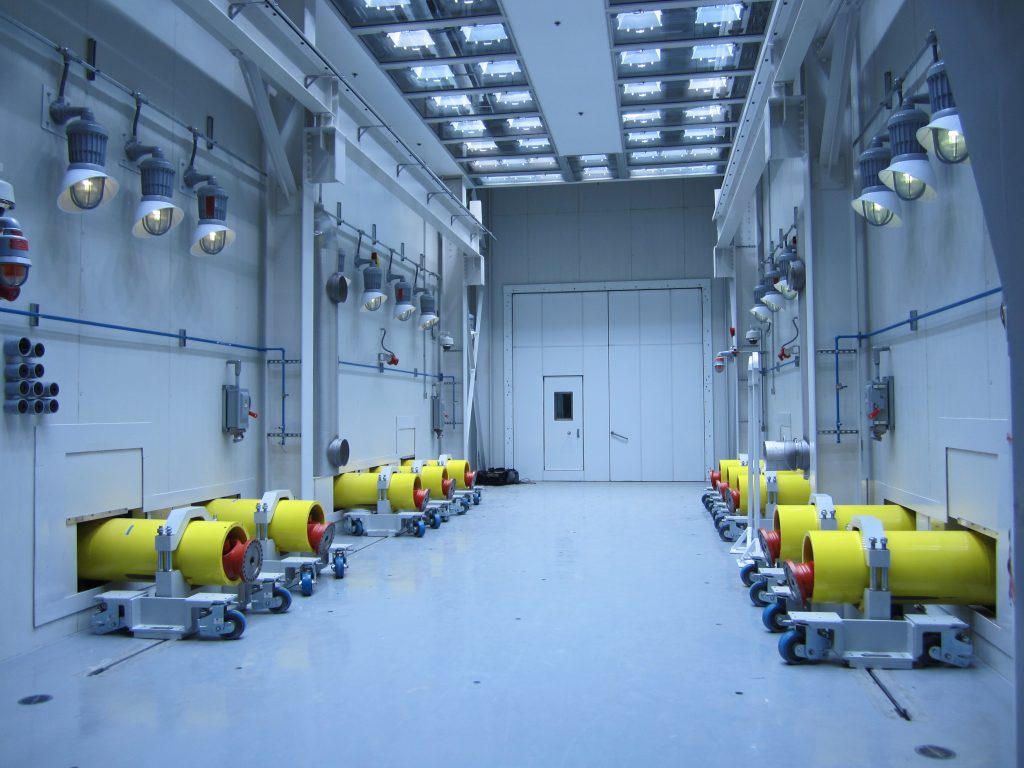
DYNO LAB: The PEVEL Environmental and Dynamometer Laboratory has the capability to test every tactical or combat vehicle from a Humvee to an Abrams, all with the vehicle operating at top speed but standing still. (Photo by Stephen Roberts, GVSC)
BEHIND THE SCENES IN ELECTRONICALLY CONTROLLED POWERTRAINS
In order to achieve goals such as better fuel economy, increased power output, reduced emissions and enhanced diagnostic information, the heavy-duty truck industry transitioned to electronically controlled powertrains starting in the 1990s. Eventually, this transition also reached military vehicles as new vehicles were introduced or older vehicles were modernized.
Although electronically controlled powertrains often have multiple controllers, the two most common types are the engine control module (ECM) and the transmission control module (TCM). These two controllers are programmed to work in harmony to produce the optimized response of a vehicle based on criteria such as driver demand, road grade, vehicle load, ambient temperature, elevation and other factors.
To account for all of the combinations of conditions, these controllers have complex algorithms that usually have upwards of a million lines of software code.
While the driver interfaces with these controllers through the simple and singular input of the accelerator pedal, a network of feedback sensors is providing data to those controllers such as wheel speed, engine speed, coolant temperature, transmission oil temperature, engine oil pressure, intake manifold air temperature and many other parameters.
To understand the major components of electronically controlled powertrains, think of the controller as the brain and the sensor network as the nervous system. The sensor network is constantly relaying information to the controllers about the vehicle’s status and health. The controllers then make decisions on behalf of the driver to deliver the best available performance. Without the brain and nerve system of the algorithm and the controller and sensor network, mechanically controlled powertrains are unaware of their health status, unable to provide warning information to the driver (check engine light) or initiate self-protecting countermeasures to avoid catastrophic failure, such as overheating and blowing the engine head gasket.
Interpretation of the data from feedback sensors by the controller is handled by a series of proprietary algorithms owned by the manufacturer. Since this information is not typically made available to the U.S. military, it is crucial to test the vehicle in representative conditions and observe the response to ensure the vehicle meets the requirement.
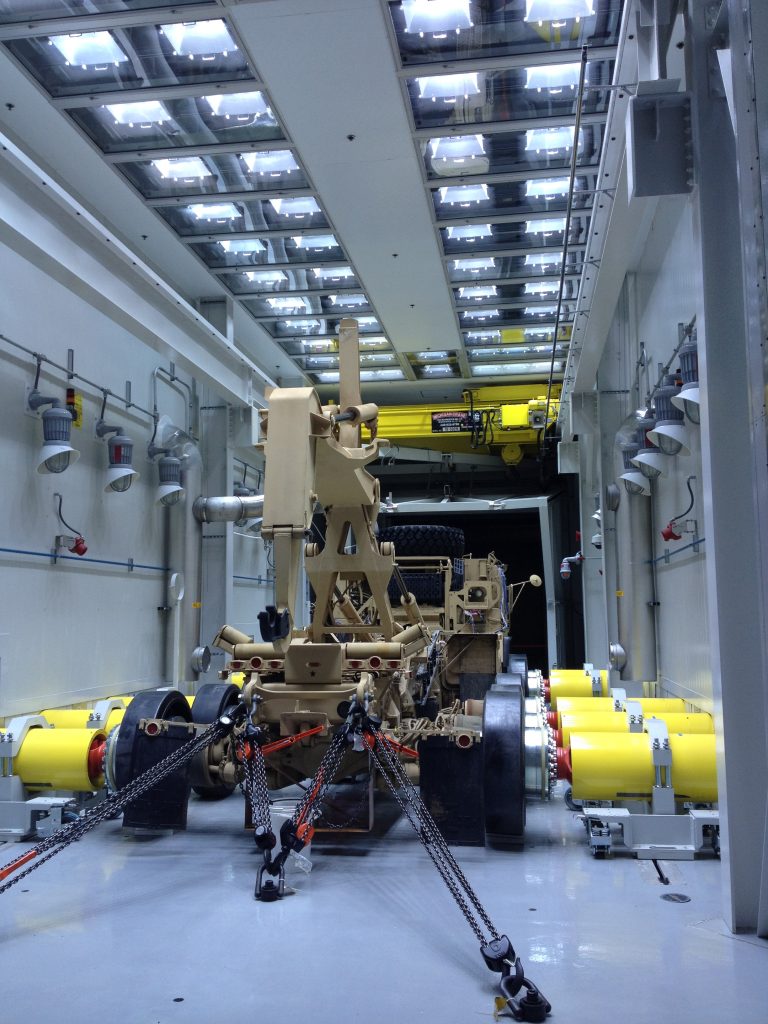
MORE OR LESS MOBILITY: The Palletized Loading System (M1074A1) in PEVEL for mobility performance testing at 120 degrees. Using environmental control, vehicle laboratories can heat or cool the air from 50 below to 120, and are equipped with dynamometers to exercise the vehicle’s powertrain. (Photo by Stephen Roberts, GVSC)
NO SUBSTITUTE FOR PROOF
Even when information is available from the manufacturer regarding its control algorithms, the importance of testing in representative conditions is not diminished. Manufacturers do not always know the decisions their controller will make in all circumstances. Manufacturers use software modeling tools to predict the controller’s decision, but these software models also require validation in order to be fully trusted when operating at the extremes of their design intent. Furthermore, even with validated software models, there could be powertrain hardware limitations that remain undiscovered until the vehicle undergoes comprehensive testing.
While electronically controlled powertrains have greatly simplified the responsibilities of the operator, they provide challenges to the Army test community when attempting to evaluate mobility performance at desert operating conditions (120 degrees). Their ability to self-regulate their critical operating limits occurs in two primary methods, engine deration and modulated powertrain cooling.
Both of these regulation methods often have a nonlinear response to the change in ambient temperature. In order to definitively evaluate a vehicle’s mobility performance of an electronically controlled powertrain, the vehicle must be immersed in the targeted environment to produce a representative response. This becomes particularly challenging for ambient temperatures at 120 degrees as these temperatures are rarely occurring within the United States.
OUT OF THE DESERT AND INTO THE OVEN
Even though permitted by test operating procedures, linear extrapolation of powertrains fluids based on ambient temperature should be heavily discouraged when considering electronically controlled powertrains as this can practice introduce significant error or invalidate the test results.
If linear extrapolation is not an option for electronically controlled powertrains, what is the solution?
Since the 1950s, the Army has invested hundreds of millions of dollars in vehicle laboratories that have environmental control. These facilities can heat or cool the air from 50 below to 120. Furthermore, they are equipped with dynamometers to exercise the vehicle’s powertrain. A dynamometer is essentially a treadmill for vehicles. These vehicle laboratories have the capability to test every tactical or combat vehicle from a Humvee to an Abrams, all with the vehicle operating at top speed but standing still.
To study the dangers of linear extrapolation on electronically controlled powertrains, test data was analyzed by test engineers from the Ground Vehicle Systems Center (GVSC). This test data came from various sources including engine, power pack (engine plus transmission plus cooling system), or full-vehicle test programs on vehicle platforms such as Abrams, Stryker, the Self-Propelled Howitzer (SPH) and the Heavy Equipment Transporter.
Testing took place at the GVSC Propulsion Systems Laboratory and the Power Energy Vehicle Environmental Laboratory (PEVEL). In the laboratory setting, the ambient temperatures were controlled to produce representative environments matching the vehicle’s upper ambient temperature specification (120 degrees). Performance data was then compared on the same test setup at the same operating point while at a lower ambient temperature (80-90 degrees).
From this test data, the linear extrapolation method described in Army test operating procedures (Test Operations Procedure (TOP) 2-2-607 “Cooling Systems (Automotive)” was then applied to measurements of engine oil temperature. This provided a set of actual results at desert operating conditions (120) and an extrapolated set.
With a set of results from actual ambient temperatures and a set from extrapolated temperatures, we could calculate the error introduced by the prediction of extrapolation. Based on this test data, extrapolation of engine oil temperature was 65 percent to 116 percent off from the actual measurement. The electronic controls prevented the powertrain from overheating even though linear extrapolation said it would.
For example, with that 65 percent error, linear extrapolation predicted engine oil temperature was 270 degrees when it was actually 250. This is a huge change considering a vehicle will pass or fail mobility performance testing at the proving ground by crossing the threshold by 1 degree.
In the past, the Army has led many investigations such as Yuma Proving Ground Report No. 221 and No. 135 into the impact of extrapolation error. This series of studies occurred back in the 1970s and only studied mechanically controlled powertrains. At that time, extrapolation was usually observed as 10-20 percent. However, the extrapolation error on electronically controlled powertrains is approximately three to five times more severe than the extrapolation error for mechanically controlled powertrains. With so much error in the test results for powertrain performance, we can have little confidence in how the vehicle will actually respond to the extreme demands of desert warfare.
In addition, it is important to note that the error resulting from linear extrapolation is biased towards false failures. In other words, linear extrapolation will predict engine or transmission overheat on a vehicle that may have had no issue if actually tested at 120 degrees.
This is because linear extrapolation cannot account for control algorithms that might derate the engine power or increase powertrain cooling to lower key parameters such as engine oil temperature, engine coolant temperature, and transmission oil temperature.
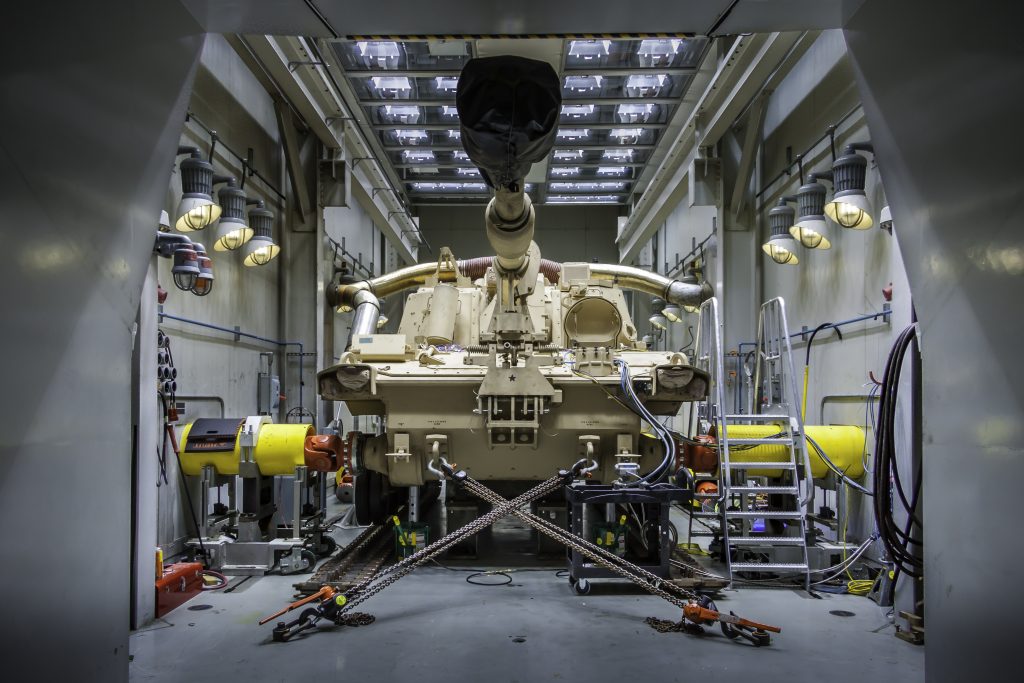
HIGH TEST: Self-Propelled Howitzer (M109A7) in PEVEL for mobility performance testing at 120 degrees. The types of tests conducted at the vehicle laboratory on tactical and combat ground vehicles are vast with varying levels of influence by ambient temperature. (Photo by Steven Zielinski, GVSC)
SOLUTION FOR NONREPRESENTATIVE TEST CONDITIONS
If you have ever attempted to adjust the thermostat in your home or workplace to your preferred setting, you have probably experienced the disruption in harmony with those individuals who are hypersensitive to changes in temperature. A battle over 70 degrees vs. 72 degrees ensues. Electronically controlled powertrains know when the “thermostat” has been touched and they care. Linear extrapolation of key powertrain parameters such as engine oil temperature, engine coolant temperature and transmission oil temperature has too much error to be trusted during mobility performance testing.
What does this mean for the test and evaluation community? How does this impact ongoing or future test programs?
The types of tests conducted on our tactical and combat ground vehicles are vast with varying levels of influence by ambient temperature. For instance, determining a vehicle’s roll-over tipping point on a tilt table is completely unrelated to the ambient temperature during the test. The tests most impacted by the change in ambient temperature are those that will require peak engine power and torque during mobility-performance testing.
Mobility performance testing is predominately evaluated by three different tests: 1) Vehicle top speed; 2) Max grade hill climb; and 3) Full-load cooling. The outcomes of these tests tell the Army the vehicles’ maximum traveling speed, the steepest grade it can climb and how much torque it can produce without overheating to the point of engine damage.
The Army needs to run these three tests at 120 degrees to guarantee that electronically controlled powertrains will deliver the performance advertised by the manufacturer. This means that tests will need to be scheduled both geographically and seasonally in order to ensure this ambient temperature is reached. If this is not possible because of test program schedule constraints, the test needs to be performed in a laboratory with environmental control and dynamometers.
WHAT IS ENGINE DERATE? Though both operate via a simple accelerator pedal, electronically and mechanically controlled powertrains are vastly different under the hood, so to speak. In a mechanically controlled powertrain, the force of the driver’s foot on the accelerator pedal is physically transferred via linkage or cable to the engine’s fuel injection pump. More force on the pedal, more gas to the engine. While this simplicity has a predictable outcome, it comes with some disadvantages. In the event the vehicle is operating in a hot environment or under heavy load, a driver may unintentionally surpass critical limits for engine oil temperature or coolant temperature, which could result in severe damage, like blown head gaskets, failed main bearings, scored cylinder walls and other heat-induced failures. That means that a mechanically controlled powertrain will meet the driver’s demands even to the point of total catastrophic failure. The only restraint might be a driver’s own response to indicators like temperature gauges or warning lights. In contrast, electronically controlled powertrains inherently possess the ability to self-limit—and effectively override the driver’s demand for more. They monitor and control their own condition from the feedback of the sensor network and prevent operation beyond critical limits. If the driver floors demands 100 percent, the system won’t honor the demand if the driving conditions are too severe. That is engine derate. What’s important to understand here is that error resulting from extrapolation combined with electronic controls introduces a bias toward failure—the error can fail a perfectly good vehicle because the test data is wrong. Due to these operating principles, linear extrapolation will always produce a false failure, but never a false pass. It’s important that this one-way bias is recognized as it presents significant risk to a vehicle acquisition program. |
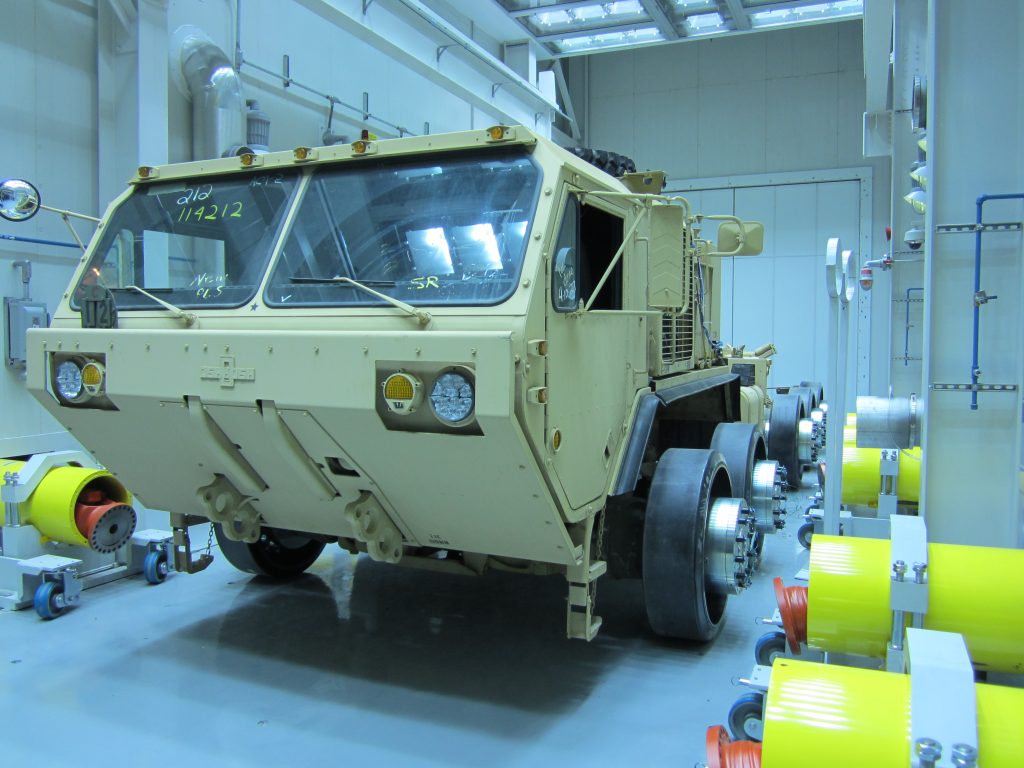
UP FRONT PERSPECTIVE: The Palletized Loading System (M1074A1) in PEVEL for mobility performance testing at 120 degrees. During mobility-performance testing, several key temperatures govern outcome—ambient temperature in the test environment for powertrain cooling, critical limits for each of the vehicle powertrain fluid temperatures and ambient temperature which significantly impacts the measured performance. (Photo by Stephen Roberts, GVSC)
WHAT IS LINEAR EXTRAPOLATION? During mobility-performance testing, there are several key temperatures that govern the outcome. First, the vehicle performance specification lists an upper requirement of ambient temperature in the test environment for powertrain cooling. Most commonly, this is 120 degrees as this represents the extremes of desert warfare. Second, the vehicle powertrain has critical limits for each of its fluid temperatures (i.e., coolant, engine oil, transmission fluid, intake manifold air, etc.). The manufacturer assigns these critical-limit temperatures as a not-to-exceed boundary before damage or failure ensues, and the test fails. Lastly, ambient temperature—the air temperature during the test—significantly impacts the measured performance. While ambient temperature at time of testing should be the same as the vehicle’s upper requirement for ambient temperature, that presents a problem. Ambient temperatures above 110 degrees rarely occur except as the peak temperature of the day within the United States. So, even though places like Death Valley and Yuma Proving Ground—can touch 120 degrees, but, out of the year, they can do that only for part of it, in June through August, and so the windows of opportunity to test at the temperature necessary are very small. Contrast that with the Army’s environmental chambers that can do it any day. As an example, assume testers measure the ambient temperature as 90 degrees and engine oil temperature as 250. We need to know the fluid temperature in hot desert conditions, so we subtract 90 degrees from 120, then add that extra 30 degrees to the fluid temperature of 250. That’s linear extrapolation. For every increase of 1 degree in the ambient temperature, the fluid temperature can be expected to rise by the same amount. Therefore, in this test, linear extrapolation would predict the engine oil temperature as 280 degrees. If the vehicle had a critical limit for engine oil temperature at 275 degrees, it would fail the test. Under the right conditions, linear extrapolation of ambient temperature has been a useful tool when attempting to predict the performance of mechanically controlled powertrains. Because there are so many more variables with electronically controlled powertrains, linear extrapolation isn’t any longer a valid approach to the Army’s needs because we can’t see into proprietary algorithms and don’t know the variables the algorithms are using for control. |
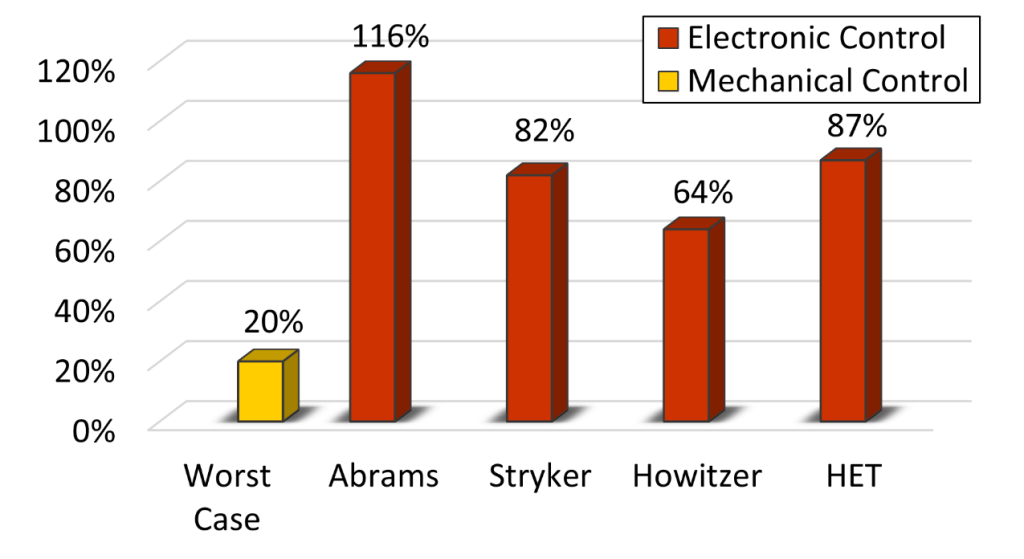
TEMPERATURE TESTING: Extrapolation error of engine oil temperature during mobility performance testing at desert conditions. (Graphic provided by Steven Zielinski, GVSC)
CONCLUSION
As technology continues to advance in order to ensure that the United States warfighter has superior advantage, military vehicles will continue to gain in complexity and sophistication. When evaluating vehicles with electronically controlled powertrains, linear extrapolation of powertrain fluids can introduce significant error during mobility performance testing or deliver completely invalid results.
For conducting mobility performance testing at the upper requirement for ambient temperature (120 degrees), the test program can be supplemented with laboratory testing. This is not just about simple cost savings. Most likely, there is a slight cost savings to running tests in the environmental chamber over the proving ground. The point is that we pay a great deal of money for testing that may be bogus. People think that linear extrapolation reduces costs, and therefore they can test anywhere in the United States at any temperature. Freedom in exchange for useless results—or results that harm the chances of a vehicle the Army wants and needs in passing a test—is a terrible bargain. If you evaluate cost savings for testing in seasonally and geographically appropriate areas to actually have 120 degrees, environmental chamber testing would probably be a huge savings. But that proposition remains to be tested, because up to this point we as a test community have not been willing to limit themselves to test at 120 and instead insist on extrapolation.
Within the laboratory environment, the ambient temperature can be controlled to produce representative responses from the vehicle’s powertrain. However, laboratory testing cannot be seen as a replacement for field testing as other vehicle systems such as wheels or tracks or suspension are not being exercised. Using both field and laboratory testing is necessary to comprehensively evaluate vehicles with electronically controlled powertrains.
For more information, a comprehensive technical paper can be found in DTIC (AD1170619) or by contacting the authors, steven.m.zielinski2.civ@army.mil and paul.b.maguire4.civ@army.mil.
STEVEN ZIELINSKI is a technical specialist for Ground Vehicle Power and Mobility – Test and Evaluation team at the Ground Vehicle Systems Center (GVSC). He holds an M.S. in mechanical engineering from Wayne State University and a B.S. in engineering physics from Oakland University. He is a practitioner in engineering and technical management.
PAUL MAGUIRE is a technical specialist for Ground Vehicle Power & Mobility – Test and Evaluation team at GVSC. He holds an M.S. in mechanical engineering and a B.S. in chemical engineering, both from Wayne State University. He earned his Professional Engineering license in mechanical engineering in 2006. He is a practitioner in engineering and technical management.