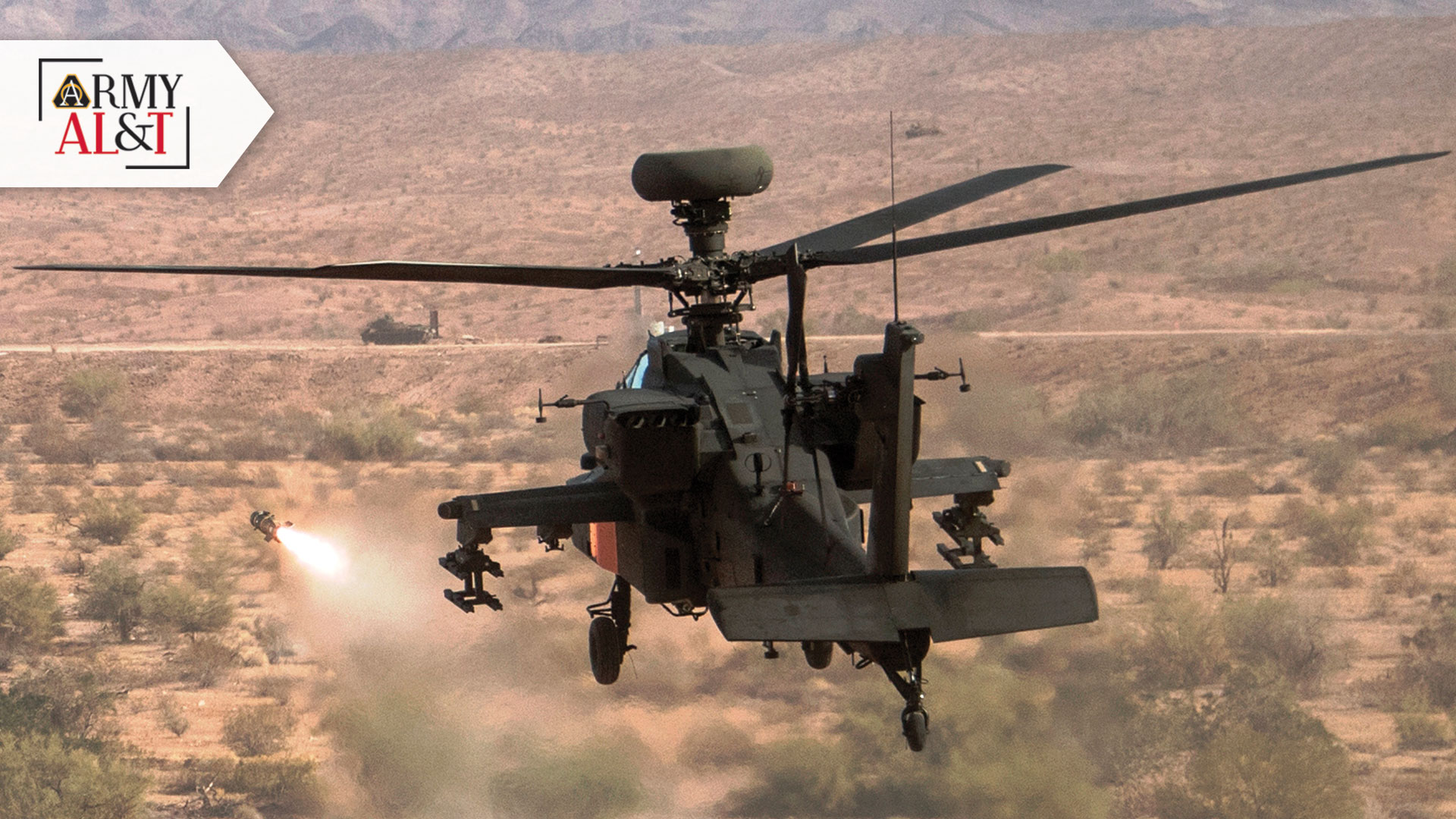
FLIGHT TEST: The JAGM missile was tested at Yuma Proving Ground, Arizona, before the project moved into low-rate initial production. (Photos by U.S. Army)
Missile-seeker components illustrate how the Army works with industry to develop unique or exotic materials to fill capability gaps.
by Argie R. Sarantinos
The U.S. Army Combat Capabilities Development Command’s (CCDC) partnerships with industry are essential to success as it continues to solve some of the Army’s most complex problems by transforming critical technology into capabilities. These collaborative partnerships not only drive CCDC’s science and technology efforts, they also enable the command to provide Soldiers with the best technology for the future fight.
CCDC, a major subordinate command of the U.S. Army Futures Command, maintains a steady stream of world-class technology through its partnerships with other government organizations, academia and industry. With six research and development centers, an Army research laboratory and a data-analysis center, the command works with hundreds of nontraditional defense companies and industry to strengthen its extensive technology portfolio. CCDC also has three regionally aligned international elements, the CCDC – Americas, – Atlantic and – Pacific centers. Through its partnerships, CCDC develops, integrates and delivers technology to support multidomain operations by 2028, while maintaining a balance of scientific research for technology that may not be developed until 2050 or beyond.
The command collaborates with industry by using traditional contracting methods, cooperative research and development agreements, and a number of different collaborative consortiums, including the Defense Ordnance Technology Consortium and the Aviation and Missile Technology Consortium. CCDC also works closely with small businesses by communicating its strategic direction and investing in emerging commercial technologies.
Beginning in 2017, CCDC partnered with industry to develop an affordable manufacturing solution for complex missile-seeker components that will be used on attack helicopters, including the AH-64 Apache and Future Vertical Lift systems. A missile seeker, which is the front part of a missile, senses heat, light or radio waves that keep the missile on target. A missile-seeker component is part of the missile seeker and includes the window, optics, sensors and other electronics. The seekers provide additional capability and enable missiles to precisely hit targets in the anti-access and area-denial environment by using different modes, allowing the missile to switch between optical and radio-frequency guidance that greatly increases the ability of the missile to stay on target. This project strengthened the industrial base and mitigated production delays of the missiles, enabling the Joint Air-to-Ground (JAGM) program to meet its low-rate initial production schedule.
The project was spearheaded by the U.S. Army Manufacturing Technology (ManTech) program, which CCDC manages on behalf of the deputy assistant secretary of the Army for research and technology, who has overall responsibility for the Army’s program. ManTech supports Army readiness and modernization priorities by improving and maturing manufacturing capacity and capabilities. Managers at CCDC centers and labs coordinate efforts by tracking advanced manufacturing science and technology topics of interest in support of their laboratories and acquisition partners. The managers work with science and technology, program executive office and cross-functional team stakeholders to prioritize the best manufacturing technology projects for the Army, including the complex missile-seeker components project.
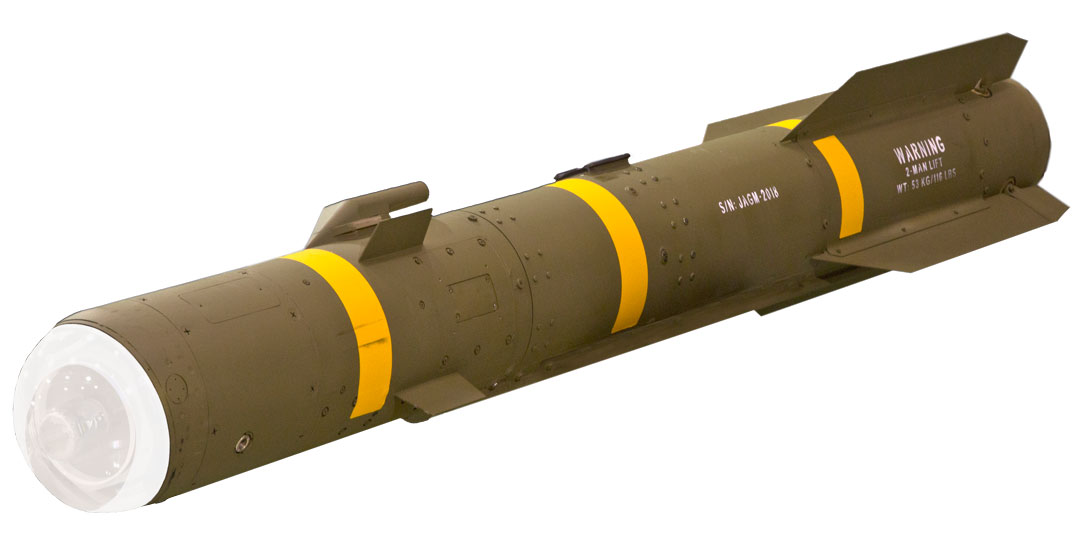
TRIPLE THREAT: A copper-graphite-metal composite is one of the main materials used in JAGM missile seekers. The composite has unique thermal properties for heat removal.
SEARCH FOR SOLUTIONS
One of the Army’s challenges is finding companies in the defense industrial base that have the expertise or production capability to make items or produce the prototypes that scientists and engineers develop in laboratories. ManTech funds projects to mature high-risk, high-payoff manufacturing processes that strengthen U.S. industry and provide more affordable weapon system components for the Army. The ManTech team also works closely with the Army’s organic industrial base, which includes depots, arsenals and ammunition plants, to provide these manufacturing solutions.
The ManTech program invested in improved manufacturing processes for boron carbide, which is used in body armor plates. Body armor plates use a combination of elements in a metal-like matrix that improves performance by providing an extremely hard material to protect Soldiers. ManTech invested in an improved manufacturing process for boron carbide and functionally equivalent silicon carbide in the 1990s, which enabled initial production of the Interceptor Multi-Threat Body Armor system. The armor was used by the armed forces during the 2000s, with limited usage into the mid-2010s.
In response to the need for more affordable manufacturing solutions for complex missile-seeker components, ManTech selected two manufacturing improvement projects, one for a complex material and one for lenses. These efforts kicked off in the 2017 fiscal year and concluded in the 2019 and 2020 fiscal years, respectively.
A main material used in JAGM missile seekers is a copper-graphite-metal composite (trade name Cu-MetGraf), which is a unique material that dissipates heat, allowing the missile seeker to function properly. Effectively removing heat from sensitive electronic devices attached to circuit boards is critical for high-performing JAGM seeker assemblies. Making the material for this application is unique and specialized. When the Army required JAGM production to ramp up, Parker Hannifin’s Advanced Products Business Unit in North Haven, Connecticut, partnered with the National Center for Defense Manufacturing and Machining (NCDMM) to transition from a low-volume, pilot-scale operation to a full-rate production environment. Improvements to yields, cycle time and capacity were needed in order to effectively strengthen the copper-graphite manufacturing for long term supply chain sustainability.
One of the key improvements focused on automating the melting and handling of molten copper, which is used to make Cu-MetGraf. NCDMM was instrumental to bringing industry best practices and new ideas to this project because it offers technical expertise and access to a vast alliance network of other companies.
ManTech’s partnership with NCDMM began in 2003. NCDMM established a strong connection between acquisition program needs and science and technology solutions from the beginning of this partnership and facilitated implementation of ManTech-funded projects within the industrial base that ultimately affected Soldier warfighting capabilities. NCDMM has increased its portfolio since its inception with a variety of collaboration and partnerships across DOD. NCDMM, which is a not-for-profit company, proactively engages with all branches of the U.S. military and its industrial base to control cost and improve productivity and performance of manufactured parts and assemblies. The company strengthens the U.S. industrial base by connecting manufacturing companies across the country. Recently, NCDMM was selected to lead America Makes, the Manufacturing USA Institute for additive manufacturing.
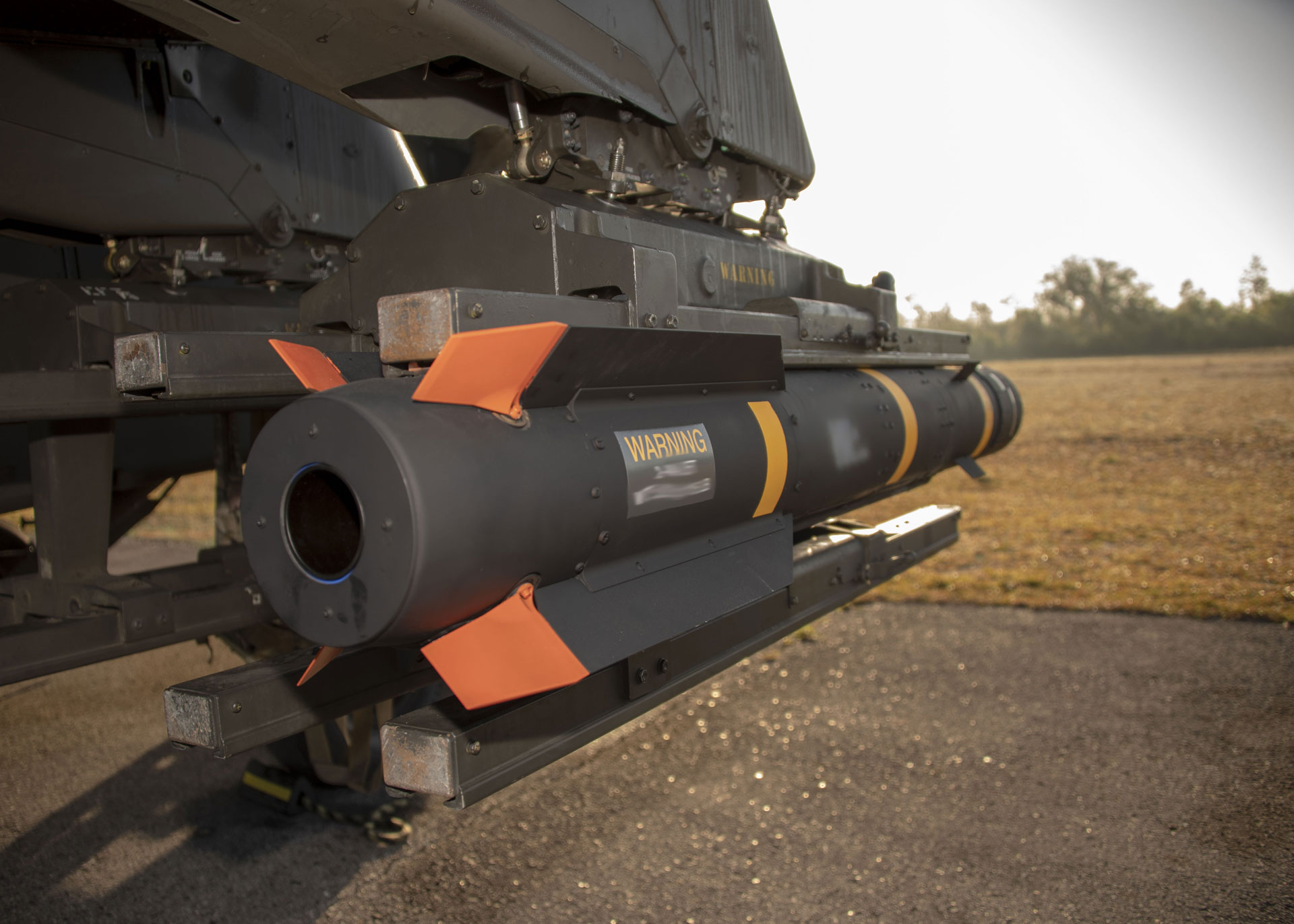
LOAD IT UP: A JAGM missile is loaded onto an AH-64 Apache attack helicopter during the JAGM initial operational test and evaluation. The test was conducted at Eglin Air Force Base, Florida.
CUSTOMIZING PROCESSES
Lenses are used in guided missiles to change the direction of the light rays to enable missiles to see their targets. Scratched or warped lenses alter the laser line of sight, which may disrupt the missiles’ mission. The ManTech team partnered with industry on the missile seeker project by implementing custom tooling and an automated process.
Before the new process, lenses were often damaged and ultimately scrapped during the grinding and polishing process. The team implemented a customized machine with a vacuum tool to pick up the lenses without damaging or dropping them. The new process reduced the number of steps the operators needed to perform and enabled operators to measure components without worrying about alignment issues. The new process is also much more efficient and repeatable, and is easier for new operators to learn.
The project drastically reduced the processing time for lens assembly from seven days to approximately one and a half hours and improved safety by automating the transfer and pouring of molten copper. Automating the process not only controlled the copper transfer and pour time, it also improved repeatability of the process. NCDMM was also instrumental in this project—for example, the team discovered that adding bumps to the bottom of the lens allowed the epoxy to evenly disperse without impacting the function of the lens. Without this partnership, a great idea may have been missed and the project may not have been as successful.
CONCLUSION
NCDMM’s role through the years has ranged from project integration to project execution of Army ManTech projects. They have used a variety of contracting methods, including traditional contracting, cooperative agreements and other-transaction authorities. Through America Makes, NCDMM also participates in developing technology road maps and informing strategic planning for critical topics, including additive manufacturing.
CCDC’s relationships with industry partners around the world enable the command to discover new and different manufacturing processes that are critical to developing technology for Soldiers. These technologies are the foundation for the battlefield of the future, supporting the Army’s modernization priorities and giving Soldiers the tools they need to fight and win.
ARGIE SARANTINOS, a public affairs specialist for Huntington Ingalls Industries – Technical Solutions Division, provides contract support to CCDC. She holds an M.S. in professional writing and a B.A. in mass communications from Towson University. She has 14 years of public affairs experience supporting DOD.
Read the full article in the Winter 2020 issue of Army AL&T magazine.
Subscribe to Army AL&T News – the premier online news source for the Army Acquisition Workforce. Subscribe