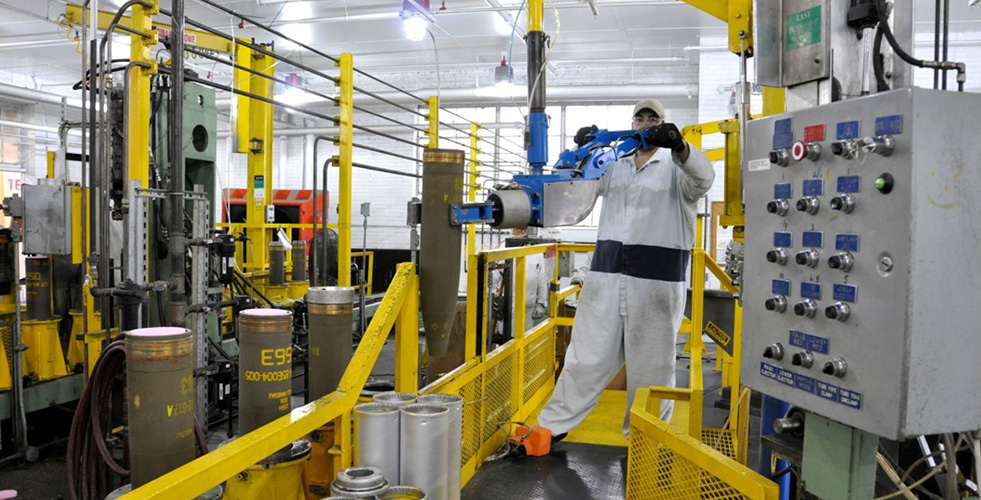
Project management offices throughout DOD must effectively collaborate with other organizations to facilitate problem-solving and efficiency, and achieve additional savings for the taxpayer.
by Lt. Col. Terry G. Crank, Mr. David A. Kondas
and Ms. Tereasa M. Ferguson
While many DOD organizations have little or no overlap between missions, there may be several organizations that have systems or processes in place that can be leveraged to help address substantial acquisition challenges. In the same way that Soldiers tactically coordinate between adjacent units in war, DOD organizations should apply this same concept throughout the acquisition community.
The difficulty lies in determining how to apply this tactical imperative in a stovepiped environment like the acquisition community. Robust lateral communication and coordination, persistence and open-mindedness are important keys to ensuring successful collaboration among organizations. The ability to look beyond benefits that accrue only to the immediate organization and recognize benefits to the greater mission is also critical for successful collaboration.
Two organizations within the Program Executive Office (PEO) for Ammunition exemplified that successful collaboration when they discovered a shared requirement and were able to leverage an established grenade download process from one organization to significantly reduce program execution costs for the other.

PM CAS and PD JS created a new manual line that focused on soft-touching the higher-capacity existing manual lines used by PD JS at McAlester and Crane. Here is the Soft Touch Projectile de-basing operation on the new manual line at McAlester. (U.S. Army photos)
In 2014, the Project Director Joint Services (PD JS) managed a program to download and demilitarize M483A1 projectiles. It was discovered that the Project Manager Combat Ammunition Systems (PM CAS) was executing an M483 Reuse Program that recovered and recycled M483A1 projectile metal parts, primarily the projectile body and base, to build a new family of extended-range artillery projectiles for the warfighter. PD JS was using a much more cost-effective process for grenade download and recovery, so once this overlapping requirement was discovered, PM CAS was able to modify the PD JS process and enhance it for its use. The approach used by both programs, which has a projected cost avoidance of over $100 million for the Army, was collaborative and set conditions for future teaming arrangements. That PD JS and PM CAS are both managed by PEO Ammunition and located at the same installation—Picatinny Arsenal, New Jersey—made the communication, coordination and collaboration process that much more effective.
IDENTIFYING THE OPPORTUNITY
Prior to this collaboration, PD JS and PM CAS pursued different sets of requirements for the M483A1 Dual Purpose Improved Conventional Munition artillery projectile, a cluster munition projectile containing 88 anti-personnel/anti-materiel grenades. PD JS processed M483s for demilitarization by using a destructive approach to downloading the grenades that significantly damaged the body and base of the round. This high-capacity download process unloaded grenades at a high rate on a manual line, yielding lower unit costs, which enabled the sale of leftover metal parts as scrap. At the time, PD JS was funding demilitarization using manual processes and equipment that required a dozen human operators and had minimum automation at four sites: McAlester Army Ammunition Plant, McAlester, Oklahoma; Crane Army Ammunition Activity, Crane, Indiana; Hawthorne Army Depot, Hawthorne, Nevada; and General Dynamics Ordnance and Tactical Systems, Joplin, Missouri.

The PM CAS download process used a soft-touch robotic line that was less destructive but operated at a slower rate to deliver usable metal parts.
Simultaneously, PM CAS financed a separate M483 download capability for metal parts recovery at McAlester to support the development and new production of the M1122, M1123, M1124 and M110A3 suite of 155 mm projectiles under the M483 Reuse Program. The PM CAS download process used a soft-touch robotic line that was heavily automated, required three operators and was less destructive, but ran at a slower rate to deliver usable metal parts. Nonetheless, this robotic line allowed for the recovery of metal parts such that PM CAS was able to realize a per-projectile savings of approximately $700, compared with new parts production.
However, the cost to download each M483 using the soft-touch line was beginning to rise, increasing the M483 Reuse Program projectile unit cost and threatening to breach the acquisition program baseline threshold cost agreed upon by PM CAS and PEO Ammunition at the beginning of the program. Additionally, the robotic line would not be able to recover sufficient metal parts on a yearly basis to meet the future demands of the M483 Reuse Program. Also, M483 demilitarization (with no metal parts recovery, using the PD JS manual line) was progressing at such a rapid pace that PM CAS was concerned that the supply of recoverable M483s worldwide could potentially be depleted before the M483 Reuse Program had fulfilled its production requirements.
In August 2014, PM CAS contacted PD JS for assistance with a collaborative solution that focused on introducing the soft-touch robotic line to the higher-capacity existing manual lines used by PD JS at McAlester and Crane. In September 2014, PD JS and PM CAS agreed to an M483 metal parts download strategy, the details of which would be documented in a memorandum for record signed by all stakeholders and supported by a yearly M483 metal parts recovery plan of action.

In August 2014, PM CAS approached PD JS for help with a collaborative solution that focused on adding soft-touch robotics to the higher-capacity existing manual lines used by PD JS at McAlester Army Ammunition Plant and Crane Army Ammunition Activity. Here is the Soft Touch Projectile Clamp at the new manual line at McAlester.
COMMUNICATION, COORDINATION AND COLLABORATION
PD JS, PM CAS and the Joint Munitions Command Demilitarization Office signed the memorandum for record in November 2014, with all stakeholders agreeing to a plan to coordinate respective efforts to provide downloaded projectile hardware paid for and meeting PD JS objectives for the 155 mm M483 Reuse Program. The memorandum documented that the PMOs would work together to coordinate schedules and ensure that the desired metal parts would be supplied by PD JS in time for upload at the respective projectile load, assemble and pack facilities managed by PM CAS. In addition, both PMOs agreed to the following important conditions:
- PD JS would continue to fund all download of M483 projectiles and demilitarization of the Dual Purpose Improved Conventional Munition grenades as previously planned at McAlester and Crane; PM CAS would pay for cleaning, inspection, temporary packing and transportation of metal parts to the load, assemble and pack sites.
- PD JS would conduct download operations for metal parts recovery at McAlester and Crane only, with PM CAS funding enhancements to soft-touch existing manual download processes at each facility to minimize damage to metal parts.
- PM CAS would fund the difference in added labor cost needed to ensure proper metal parts handling during download.
- Other M483 demilitarization commitments (Hawthorne Army Depot and General Dynamics Ordnance) would remain unaffected by this agreement.
The memorandum was followed by an M483 metal parts recovery plan of action developed by PM CAS and signed in July 2015. It provided a strategy to maximize metal parts recovery to support the build of over 1 million extended-range artillery rounds through 2021. The plan of action examined actual and forecast M483 Reuse Program metal parts requirements and planned M483A1 demilitarization quantities and locations in order to synchronize schedules to supply downloaded hardware to several 155 mm production lines for projectile upload and final load, assembly and packing. The plan of action, reviewed each January, focuses heavily on the first two years of execution, with an eye on the 3- to 5-year period and beyond. It contains extremely detailed information based on a lot-by-lot analysis of M483A1 projectiles in the inventory. An important decision made during plan-of-action development was to cease demilitarization of M483 assets at Hawthorne and General Dynamics in order to recover as many M483 metal parts as possible by eventually shipping them to McAlester or Crane for download.

The original manual download line at McAlester Army Ammunition Plant, where grenades from the M483A1 Dual Purpose Improved Conventional Munition Artillery Projectile were processed at a high rate.
CREATING A FAMILY OF NEW PROJECTILES
By virtue of the collaborative effort to recover as many metal parts as inexpensively as possible, PM CAS is able to execute the M483 Reuse Program in a manner that maintains projectile unit costs within the acquisition program baseline threshold costs and ensures an adequate source of hardware for a longer period of time. As a result, the M483 Reuse Program is able to develop and field the following 155 mm projectiles:
- M1122 High Explosive (HE) Training Projectile.
- M1123 Infrared Illuminating Projectile.
- M1124 Visible Light Illuminating Projectile.
- M110A3 White Phosphorus Marking Smoke Projectile.
- XM1125 Obscuring Smoke Projectile.
All of these projectiles are range-matched to the M795 HE Projectile (22.5 km), the Army’s primary HE tactical projectile used in combat, to essentially create a family of low-cost rounds that can be used to train, illuminate and provide smoke-marking or obscuration to the same range as the M795.

Through the reuse of M483 metal parts, a family of five new 155 mm artillery projectiles was created that provide extended range (up to 5 km), improved performance and lower cost when compared with the current version of each round.
CONCLUSION
The linchpin of the M483 Reuse Program’s success is that it required several organizations to work cohesively to achieve what one organization could not accomplish alone. Backstopping that collaboration were several important components. The first is the open-mindedness to recognize and appreciate the magnitude of the opportunity to generate a significant cost avoidance for the Army. The second is the effective, robust and persistent communication between all parties. The third is the ability to jointly envision an agreement that meets each organization’s requirements. The final key is the willingness to trust each party to execute its agreed-upon responsibilities. Without these important tenets, the Army, and other DOD organizations, may miss significant cost-saving and efficiency opportunities that can improve the overall effectiveness to execute program requirements.
Having the details of this working relationship documented in a memorandum for record and executed via a plan of action is also essential. It not only serves as a template for how to construct such working relationships in the future, but it provides a historical record (with rationale) for future management that may rotate into a project management office assignment.

While the M483 projectile body and base are the primary components that are reused to build the family of extended-range projectiles, the expanded view of the M483 reflects all of the additional hardware that is salvaged and incorporated into each new round.
For more information, please contact Mr. David A. Kondas at david.a.kondas.civ@mail.mil.
LT. COL. TERRY G. CRANK is PM Demil for PD JS. He has more than 26 years of experience with munitions and program management. He holds an M.S. in management from the Florida Institute of Technology and a B.S. in geography from the University of Kentucky. He is a graduate of the Program Manager’s Course and is Level III certified in program management.
DAVID A. KONDAS is a senior program management engineer and project officer for the Conventional Ammunition Division of PM CAS. He has more than 26 years of experience working in the field of artillery projectiles, with much of the last 15 years spent supervising several conventional ammunition programs. He is the lead M483 Reuse Project officer and the primary architect of the M483 metal parts recovery strategy. He holds an M.S. and a B.S. in electrical engineering from North Carolina State University. He is Level III certified in program management and engineering and is a Lean Six Sigma Black Belt.
TEREASA M. FERGUSON is a project officer for the U.S. Army Armament Research, Development and Engineering Center. She has more than 10 years of experience working on networked munitions programs. She holds an M.S. in systems engineering from Stevens Institute of Technology and a B.S. in astronomy and astrophysics from Villanova University. She is Level III certified in systems engineering and Level II certified in production, quality and manufacturing.
RELATED LINKS:
PEO Ammunition
Product Manager Combat Ammunition Systems