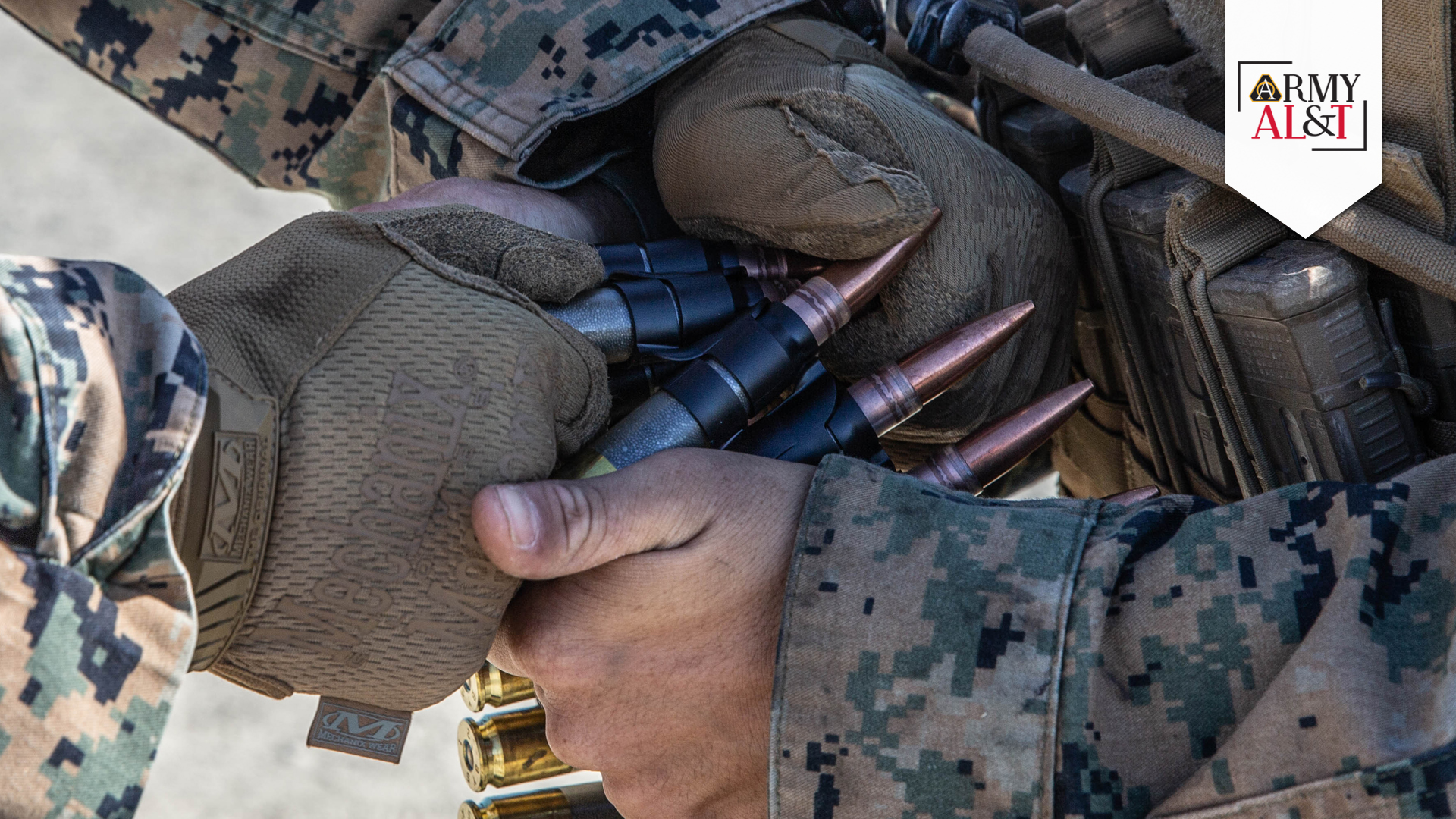
MAKING LIGHT WORK: Polymer-cased rounds like these, used in a recent Marine Corps training exercise, are 30% lighter than their brass counterparts, reducing the weight that warfighters have to transport. (U.S. Marine Corps photo by Cpl. Cameron Hermanet)
Maximizing collaboration and incremental testing to deliver lightweight ammunition to the warfighter.
by Maj. Robert K. Rodell
Given the significant weight burden of weapons, ammunition, sustainment, protection and mission command equipment that warfighters carry, reducing Soldier load continues to be a top priority for the Army. The Product Manager for Small Caliber Ammunition (PdM SCA)—part of Project Manager for Maneuver Ammunition Systems (PM MAS) within the Joint Program Executive Office for Armaments and Ammunition (JPEO A&A)—continues to support this priority through development and fielding of lightweight small-caliber ammunition. Prototype testing and experimentation with alternative materials such as polymer and steel are in progress to substitute ammunition cartridge components to reduce weight without degrading performance.
EVERY POUND MATTERS
An infantry Soldier’s approach march load, consisting of their combat load and mission-critical equipment, increased from 89 pounds during the Gulf War to 133 pounds during Operation Enduring Freedom and Operation Iraqi Freedom, to 122 pounds today. PdM SCA is currently maturing lightweight metallic- and polymer-cased 7.62 mm ammunition that provide cartridge weight savings of approximately 15% and 24%, respectively. For an M240 7.62 mm machine gun crew, this equates to approximately 13 pounds of weight savings with metallic-cased ammunition and 17 pounds with polymer-cased ammunition. Beyond the individual Soldier and tactical benefits, integrating lightweight small-caliber ammunition holds significant potential for reducing transportation costs and increasing ammunition throughput capacity across the Army’s logistics infrastructure. Replacing legacy brass cases with polymer would reduce the pallet weight of 7.62 mm ammunition by more than 400 pounds and allow for additional pallets of ammunition to be loaded on strategic transportation assets such as cargo ships and planes.
FIELDING NEXT-GEN SOLUTIONS
XM1186 (general purpose) and XM1188 (reduced range) ammunition was fielded with the XM7 and XM250 rifles in support of the Army’s First Unit Equipped (FUE) event for the Next Generation Squad Weapon (NGSW) program at Fort Campbell, Kentucky, in April 2024. Both XM1186 and XM1188 feature a hybrid metal case design consisting of a brass body and steel head, reducing cartridge weight by more than 20% compared with a brass-cased equivalent cartridge. In March 2024, the 11th Airborne Division had the opportunity to put the NGSW and ammunition to the test in extremely cold conditions at Fort Greely, Alaska, where temperatures reached as low as 50 degrees below zero Fahrenheit. Throughout the ammunition development process, improvements were continuously informed by Soldier touch points, engineering assessments and developmental testing. The fielding of XM1186 and XM1188 serves as a critical step forward in the use of alternative materials in small caliber ammunition to lighten Soldier loads.
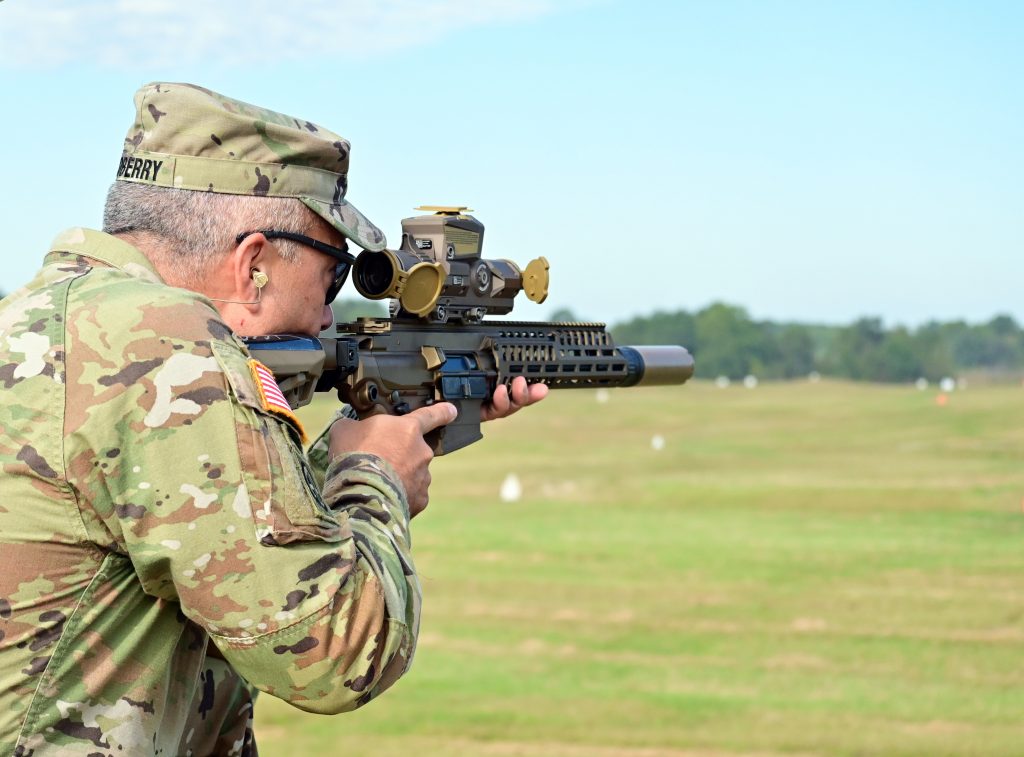
PRIMED FOR REPLACEMENT: Col. Christopher J. Midberry, Fort Campbell Garrison commander, fires an NGSW machine gun in September 2023 during a weapon familiarization demonstration at Fort Campbell, Kentucky. The XM7 rifle and the XM250 automatic rifle are primed to replace their predecessors, the 5.56 mm M4 and M249 light machine gun, and introduce advancements in military firepower. (U.S. Army photo by Kayla Cosby, Fort Campbell Public Affairs Office)
MANY HANDS MAKE LIGHTWEIGHT WORK
The Joint Lightweight Ammunition Integrated Product Team (JLWIPT) meets annually to synchronize lightweight programs across the services to prevent duplication of effort and to identify opportunities for collaboration. The JLWIPT also has established a partnership with the United Kingdom. Under this partnership, the United Kingdom Ministry of Defence leads the 5.56 mm lightweight effort, with the Army leading 7.62 mm, and the U.S. Marine Corps leading .50-caliber efforts.
Over the course of the past two years, PM MAS and PM Ammo (part of Marine Corps Systems Command) have taken advantage of this partnership to support advancement of the Marine Corps’ MK323 .50-caliber polymer-cased ammunition. Through shared funding and oversight, PM MAS and PM Ammo executed a joint limited user assessment in July 2022, design verification testing in January 2023 and reliability testing in July 2023. These critical activities supported the safety concurrence by the Navy Weapon System Explosives Safety Review Board in early 2024 to allow the fielding of MK323 for Marine Corps use. Collaboration between PM MAS and PM Ammo on these events has significantly reduced testing quantities required for Army qualification. PM MAS and PM Ammo are currently executing a developmental contract for MK323 to improve manufacturability and performance in extreme temperatures to support program transition to the Army, as the Single Manager for Conventional Ammunition, by 2026.
LIGHTER MATERIAL, CONSIDERABLE CHALLENGES
PdM SCA works hand in hand with the U.S. Army Combat Capabilities Development Command Armament Center (DEVCOM AC), DEVCOM Army Research Laboratory (ARL) and industry partners to advance lightweight ammunition solutions. While polymer materials have great potential to maximize weight savings, their physical and chemical properties present unique technical and life cycle challenges that are not present in metallic alternatives. “Extreme temperature performance has historically been a challenge with polymer materials,” said Brian Kim, project officer for Lightweight Small Caliber Ammunition at DEVCOM AC. “There are also many unknowns with how polymer will perform in terms of long-term storage and shelf life. However, with the recent development and incremental testing of new case designs, we have increased confidence in meeting Army extreme temperature requirements. Accelerated aging studies are currently ongoing to inform the limitations of polymer ammunition storage.”
In maturing 7.62 mm polymer ammunition technology, the team has learned that testing often and failing early is key to learning. PdM SCA is currently executing an other-transaction authority contract with a polymer ammunition vendor, maximizing test iterations and data exchange between the contractor and the U.S. government. “It is critical to have a continuous feedback loop of designing tests to isolate and understand key variables, test execution first at ambient and then at operational temperature extremes, and then use those observations to refine the test design for the next round of testing,” Randy Mrozek, Ph.D., team lead for polymer physics and processing at DEVCOM ARL, explained. “This critical feedback loop is only enabled by having expertise in ammunition manufacturing, weapons operation and materials understanding on the development team.”
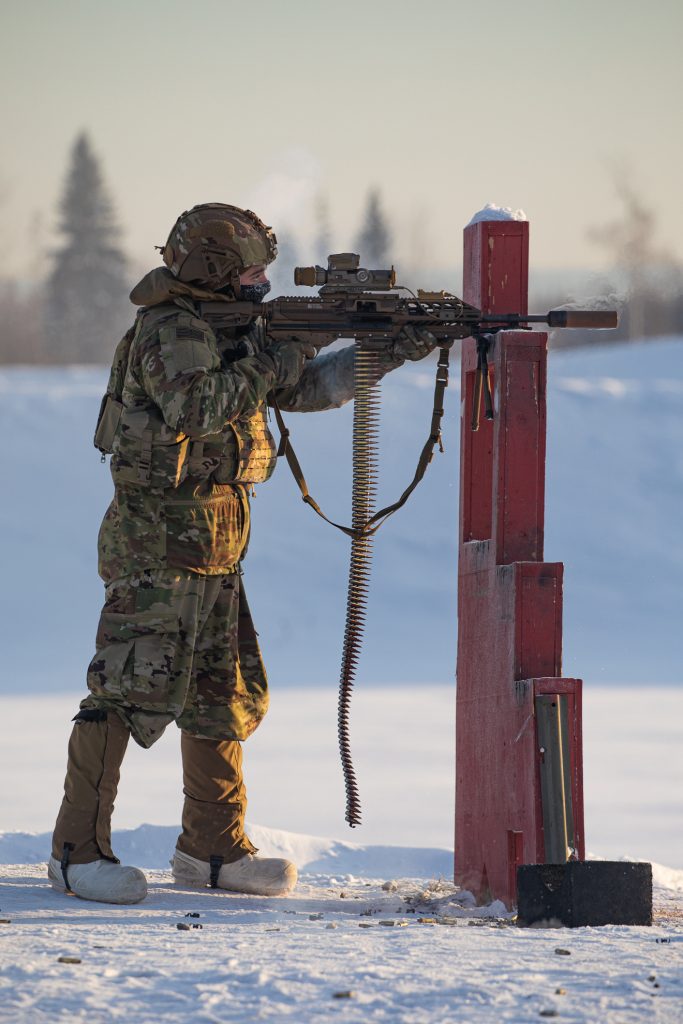
WEIGHING THE BENEFITS: The Army Cold Regions Test Center staged a multiweek test of the Army’s NGSW at Fort Greely in January 2024. The XM7 and XM250boast improved accuracy and range, weigh less than their predecessors and fire with less recoil. (U.S. Army Photo by Sebastian Saarloos, Yuma Proving Ground)
CONCLUSION
Lightweight small-caliber efforts have come a long way. Despite the inherent challenges of incorporating new materials into products, the successful fielding of XM1186 and XM1188 as well as the approval of MK323 for fielding to the Marine Corps set a path for further lightweight integration. PdM SCA continues to leverage collaborative opportunities through the JLWIPT, incremental testing methodology and industry expertise to support weight reduction priorities that will benefit the warfighter.
For more information, go to the PdM SCA webpage at https://jpeoaa.army.mil/Project-Offices/PM-MAS/Teams/PdM-Small-Caliber/.
MAJ. ROBERT K. RODELL is the project officer for Lightweight Small Caliber Ammunition and Precision Munitions, serving as an assistant product manager for PdM SCA within PM MAS, assigned to JPEO A&A at Picatinny Arsenal, New Jersey. He earned an M.A. in transportation and logistics management from American Military University and a B.S. in criminology from George Mason University and served as a logistics officer for 10 years before joining the Army Acquisition Workforce in 2022.