
LET’S SEE WHAT THIS THING CAN DO: A successful demonstration of RAIL’s capabilities was held in April 2021 at Anniston Army Depot, Alabama. (U.S. Army Photo by Mark Cleghorn)
RAIL system enables offloading at austere locations.
by Chris Kieffer and Crystal Maynard
As the U.S. increases its military presence in Europe, warfighters will have a new tool that will greatly enhance their flexibility for projecting power.
Trains have long been used by military units to rapidly transport heavy equipment over great distances. However, offloading heavy vehicles like tanks and positioning them where they are needed often presents a logistical challenge. Railyards have special equipment such as cranes or concrete ramps to move tanks from ground level onto the railcar and vice versa, or special configurations with tracks located on a lower plane than the road, allowing tanks to be loaded and offloaded from the back end of the train. However, these railyards are fixed facilities, making them easy targets during a conflict, and if an adversary can destroy a railyard, it can block critical logistics nodes.
Anticipating military mobility needs in Europe, a collaboration between the U.S. Army Engineer Research and Development Center (ERDC) and the Combat Capabilities Development Command Ground Vehicle Systems Center (GVSC), funded by U.S. Transportation Command (USTC) developed a new solution to address this capability gap.
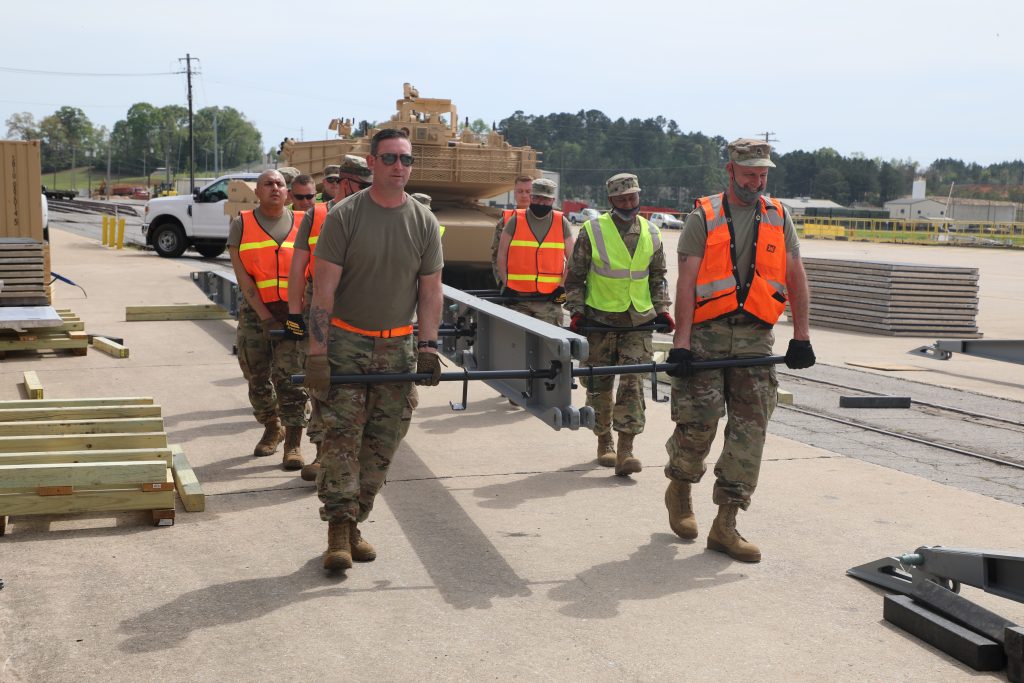
GIRDER LIFT: Soldiers from the 757th Expeditionary Rail Center lift a girder as part of a demonstration of the RAIL system at Anniston Army Depot, Alabama, in April 2021. (U.S. Army Photo by Mark Cleghorn)
The Rapidly Available Interface for trans-Loading (RAIL) is a rail ramp system that can easily be transported anywhere it is needed, allowing heavy military vehicles to be easily offloaded without the need for a permanent railyard.
“RAIL is a new, innovative capability that gives warfighters more agility and flexibility when setting up an expeditionary railhead,” said Justin Strickler, division chief at ERDC’s Geotechnical and Structures Laboratory.
The system provides flexibility to offload heavy vehicles anywhere along a rail line in order to keep an enemy guessing. It also allows for much quicker transport to remote locations than current methods that would require tanks to be carried by train to the nearest railyard and then driven by trucks to their final destinations, perhaps hundreds of miles away from the railyard. And if a train were to be incapacitated along its journey – such as if its tracks were destroyed – the RAIL system would still allow its cargo to be offloaded, a capability that currently does not exist. These mid-line offload points are typically along uneven terrain with minimal foundation preparation, and RAIL’s ability to be used in these settings sets it apart from other market solutions.
“The problem with fixed facilities is they are easily targetable,” Strickler said. “If you can only offload at point B and an adversary can stop you from getting to point B, they can stop you from transporting that equipment and ultimately accomplishing the mission.”
The RAIL system contains six basic building components that can be assembled into various configurations, allowing for equipment to be offloaded from either the side or the end of the train. This sideloading capability is significant because in most cases, tanks are loaded and unloaded from the back of the train. It’s a time-consuming process in which the vehicle moves along a special ramp that takes it from ground level to the back of the last railcar and then advances toward the front of the train, in a first-in, last-off configuration. If changing circumstances mean you need to offload a vehicle from one of the front railcars, the only way to get it out is by first offloading all of the vehicles behind it. With RAIL’s sideloading capability, it can be set up next to any rail car and allow you to offload the vehicle directly from that particular car. RAIL can also be used at a fixed facility as an additional offload point to give increased throughput.
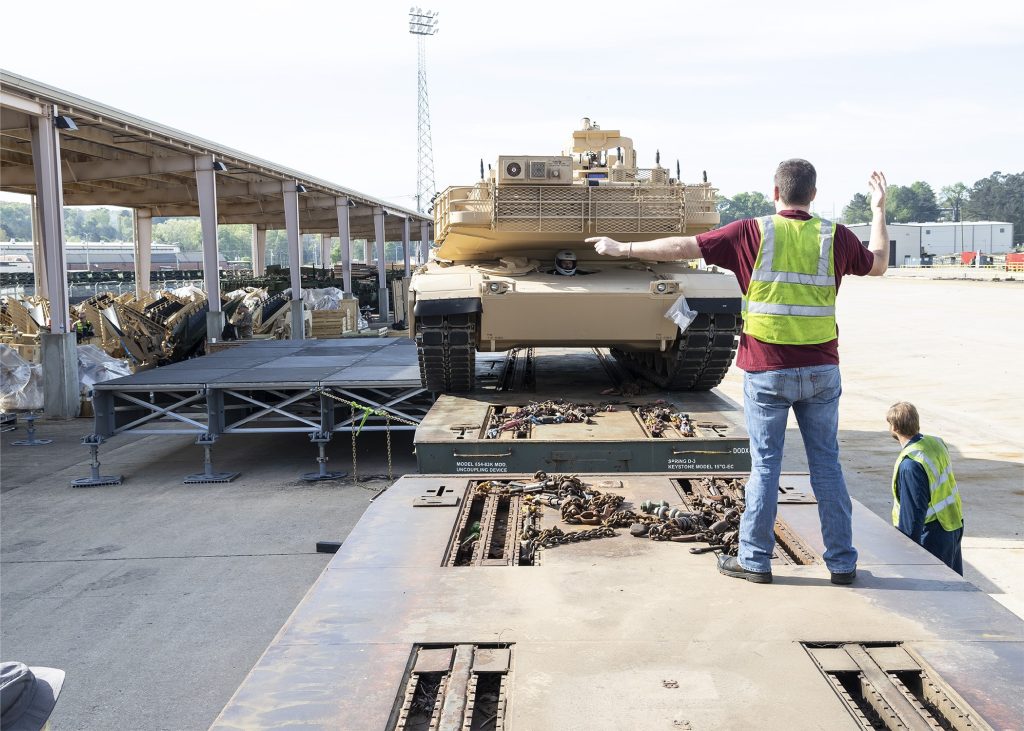
TURN PAD PLATFORM: Workers guide an M1A1 Abrams tank onto a railcar using the RAIL turn pad platform configuration during a demonstration at Anniston Army Depot, Alabama in April, 2021. (U.S. Army Photo by Mark Cleghorn)
. A team of 16 people can set the system up by hand, and it provides flexibility to offload on a variety of terrains. Other innovations designed into the system include adjustable heights and man portability, and the ability to transport in 20-foot Conex containers. It’s also small enough that it can be airdropped from a C-17 or C-130 or even transported by helicopter sling load to a location where it is needed.
The system has no electronic or hydraulic parts, meaning it requires little maintenance, Strickler said. It is designed for a 20-year life cycle.
ERDC and GVSC developed the prototype through a joint research and development program by leveraging past science and technology investments and the Army labs’ expertise in military bridging, structural engineering and military rail operations. The ERDC and GVSC team rapidly adopted technology it had previously developed together for offloading battle tanks at damaged seaport facilities to enable rail offloading at austere locations away from easily targeted railhead yards.
At the request of the 21st Theater Sustainment Command (TSC), ERDC sent two prototype RAIL systems to U.S. European Command to support real world operations. Soldiers trained on the capability at Coleman Barracks in Mannheim, Germany, from May 3 through May 10 and gave developers feedback for future iterations that will incorporate unique flexibility requirements for European operations.

PRIMED FOR TRANSPORT: Soldiers at Coleman Barracks in Mannheim, Germany on May 3-10, demonstrated how the ramp system is configured for storage and shipping. The entire system fits inside a standard 20-foot ISO container. (Photo by U.S. Army)
WEIGHING THE BENEFITS
“The RAIL system provides the European theater a 21st century capability to improvise and build a railhead off-load [and] on-load capability at nonstandard locations,” said John M. Gallagher, a supervisory traffic management specialist with the 21st Theater Sustainment Command. “This provides us a level of flexibility to adapt operational plans to enable freedom of movement and ensure speed of assembly for U.S. forces.”
The two prototype systems will stay in Europe for training, and the 21st Theater Sustainment Command has procured funds for eight additional kits—containing the panels and beams used to construct the ramps as well as the tools that are needed to assemble them into three unique configurations — that will create operational flexibility and provide deterrence through logistical capability. Several NATO members have also expressed interest in the kits, and Latvia sent two Soldiers to participate in the training.
“We are excited to have this capability in the hands of our inland cargo transfer company,” Gallagher said. “The 21st TSC is indebted to the team at ERDC and GVSC for their efforts with RAIL updates, testing and evaluations.”
The initial technology was developed under the Port Improvement via Exigent Repair (PIER) Joint Capability Technology Demonstration (JCTD) that developed and transitioned a solution for U.S. Indo-Pacific Command that could fix damaged piers across the globe within nine days to enable military sealift offload. Leveraging its deep force projection expertise, ERDC collaborated with GVSC to adapt a line of communication bridge design to develop the Pier Over-Decking System, or PODS, a modular kit that can be rapidly assembled to create a roadway capable of supporting onloading and offloading on top of a damaged pier. ERDC and GVSC share a patent on the system.
In trying to discover a solution to the challenge of unloading rail cars at austere locations, the research team had the idea to apply the PODS technology in a new way, using its same basic components to create the RAIL system. ERDC was able to use its premier research facilities to conduct component level testing for supporting heavy vehicle loads.
The U.S. Transportation Command sponsored the RAIL program, which was conceived in August 2019 during the final PIER JCTD operation demonstration in Earle, New Jersey and was successfully demonstrated in April 2021, at Anniston Army Depot in Alabama
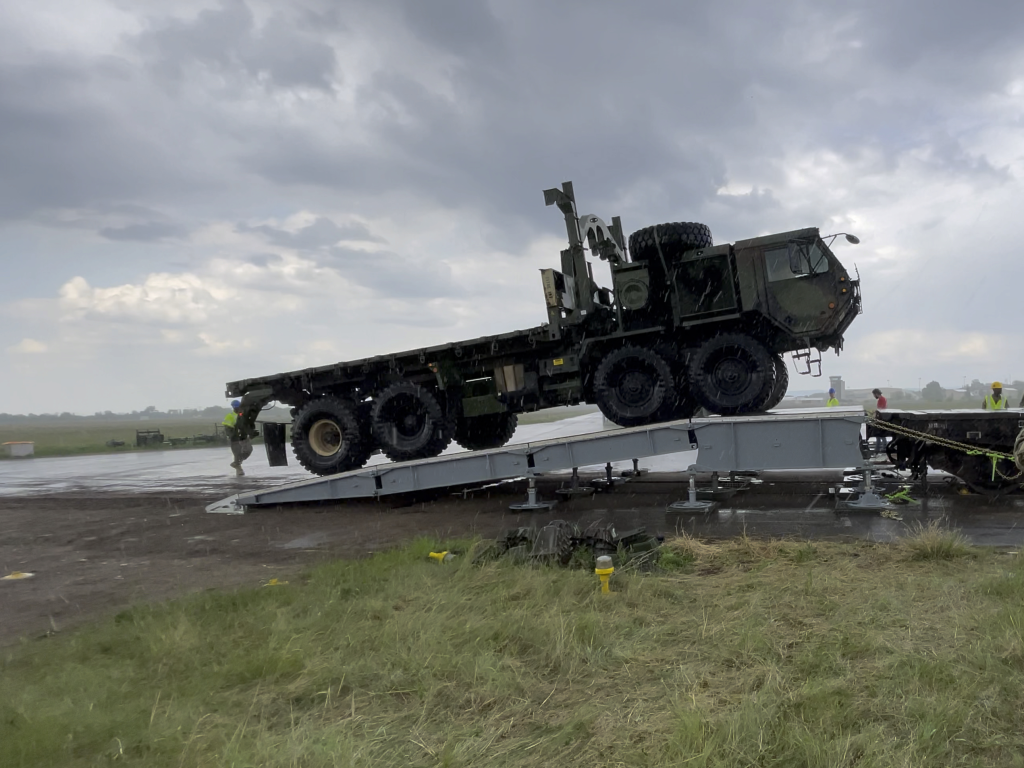
TRUCK LOAD TRAINING: A Palletized Load System truck is being loaded onto a train at Coleman Barracks in Germany. (Photo by U.S. Army)
CONCLUSION
The RAIL system is designed with the future in mind and will accommodate the heavier tanks and military vehicles that are anticipated in the years ahead. This makes the system particularly valuable, as do its flexible configurations and adaptability to other military missions like pier overdecking.
“Once additional kits and components become available, a commander would have one system capable of restoring damaged piers, unloading rail cars and overbridging under-classed bridges,” Strickler said. “We now have one system that offers three capabilities versus having three unique systems that only do one thing.”
For more information go to: https://www.erdc.usace.army.mil/.
CHRIS KIEFFER is a communications specialist with the U.S. Army Engineer Research and Development Center. He spent more than a decade as a reporter and editor with the Northeast Mississippi Daily Journal and Oxford (Mississippi) Eagle newspapers. He holds a masters degree in journalism from Columbia University and a bachelors degree in journalism from the University of Mississippi.
CRYSTAL MAYNARD works as a communications specialist with the U.S. Army Engineer Research and Development Center’s corporate communications team. She has a B.S. in public relations from the University of Tennessee and has spent almost 20 years working for various Army commands in public affairs and corporate communications.