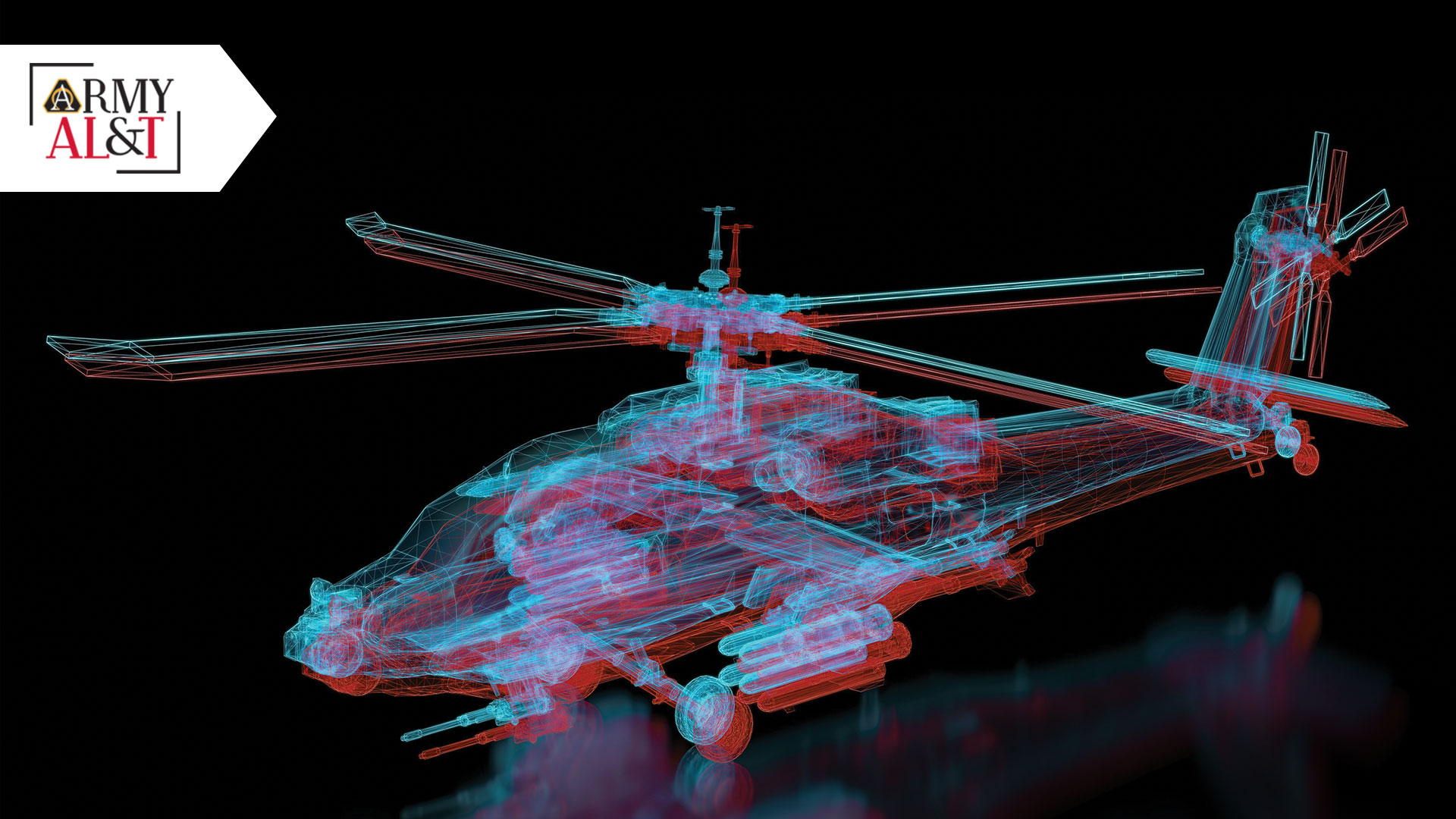
TWINSIES: A digital twin is a digital, 3D model of a real-life object. (Image by Getty Images)
U.S. Army Aviation and Missile Command is leading the way in digital twin technology for the Army.
by Jacqueline M. Hames
In the not-too-distant future, Soldiers will be able to access detailed, 3D models of helicopters, tanks and other vehicles, with a part-by-part rendering of every aspect of the vehicle. Not only measurements, but also listings of what each part is made of and how it affects other parts connected to it. With these 3D models, Soldiers, following appropriate processes, will be able to access specifications and 3D-print select replacement parts, or interact with the model to identify approved areas of where a new radio would fit best—without the frustration and expense of real-life dashboard Tetris.
But that technology isn’t available to Soldiers—yet.
That’s where U.S. Army Aviation and Missile Command (AMCOM) comes in—it is on a mission to make that future possible for the Army with digital twin technology. A digital twin is just that—a digital, 3D model of a real-life object, with all the nitty-gritty details of the object accounted for in the model. Army AL&T spoke with Joyce Myers, AMCOM’s chief data and analytics officer, in June to find out all the details.
In September 2020, Maj. Gen. K. Todd Royar established AMCOM Data and Analytics Center—the office Myers leads—“to address our digital transformation and all things related to data and analytics to include our governance and our data literacy program,” she said, which covers advanced manufacturing and digital 3D models. The research and advisory company Gartner defines data literacy as the ability to read, write and communicate data in context, including an understanding of data sources and constructs, analytical methods and techniques applied—and the ability to describe the use case, application and resulting value. “Therefore, as we include advanced manufacturing and digital 3D models into our day to day business, we want to ensure that our data literacy program addresses those specific emerging data areas and not just the familiar data areas already known and familiar to our employees,” Myers explained.
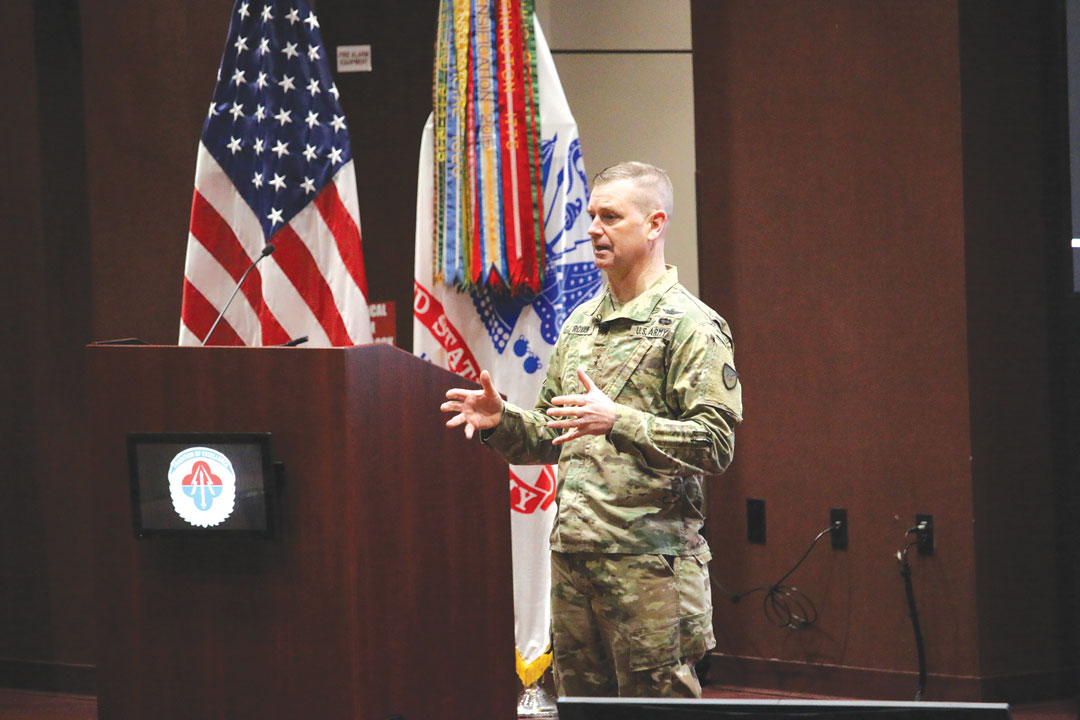
DRIVING FORCE” Maj. Gen. K. Todd Royar, AMCOM commanding general, established the AMCOM Data and Analytics Center to address digital transformation. (Photo by Traci Boutwell, AMCOM)
“Every single bit of data that we receive or create, we’re responsible for creating a structured governance program around that—policy, catalogs, quality, security, etc.,” Myers said. The center is looking at not only how to fix or improve processes already in place, but also how to lay the foundation for the future.
AMCOM’s UH-60 Black Hawk digital-twin pathfinding project is a major part of that future foundation.
WHY BLACK HAWKS
The commercial world is ahead of the Army on digital twin and digital thread technology, Myers said, which is one of the biggest challenges she and her team face. “Industry has already started changing their business processes to adapt to new technology, and we need to as well,” she said.
“What we’re truly doing right now is taking an existing helicopter apart and then we’re using a hand scanner to scan the part to create 3D models,” Myers said.
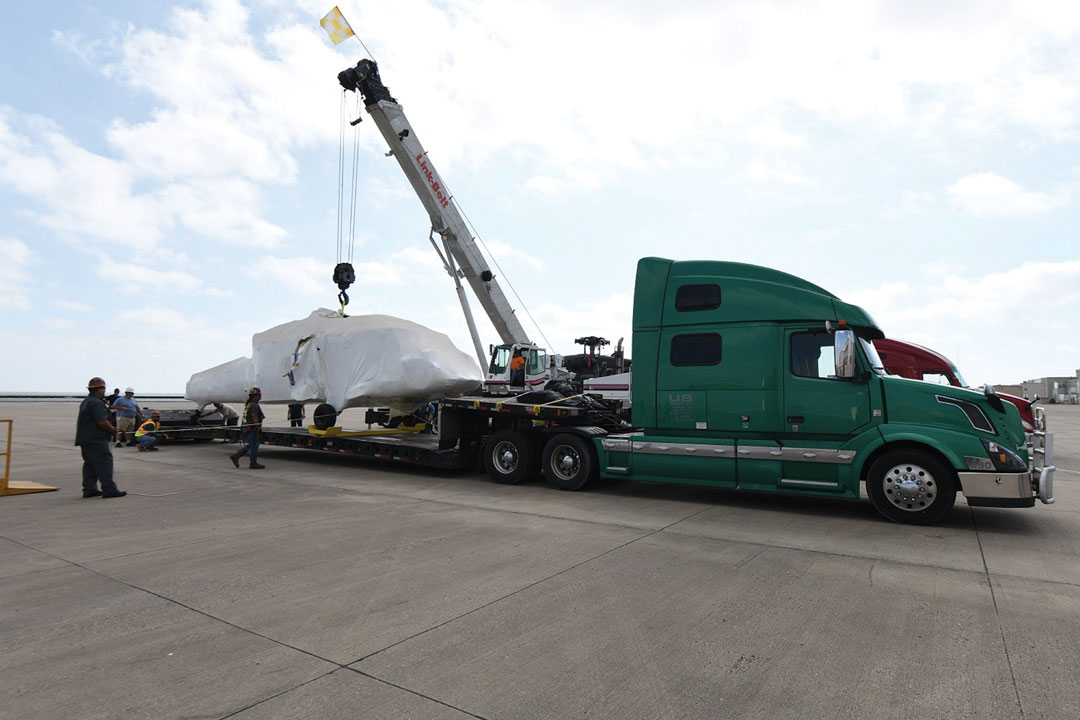
PROVEN PARTNER: One reason AMCOM chose to partner with Wichita State was that it already had demonstrated its capability by creating a digital twin of the Navy’s FA-18. (Photo by Lisa Simunaci, AMCOM)
To catch up with the power curve, AMCOM has partnered with Wichita State University’s National Institute for Aviation Research (NIAR) in developing the twin technology for the Army. “They are the cutting edge,” Myers said of NIAR. It is one of the leading aviation research institutes in the country, with projects spanning from helicopters to hypersonics.
Another reason AMCOM chose to partner with Wichita State was that it already had demonstrated its capability with the Navy in creating a digital twin of the FA-18. Royar noted, however, that AMCOM’s approach was slightly different. To make the process go faster and yield benefits sooner, AMCOM also partnered with the manufacturer, Sikorsky, on the project. “This is a win-win for both the government and industry,” Royar said.
The NIAR is sharing lessons learned from its existing and past efforts, as well as the software and skills to create the twin. It’s also helping AMCOM identify aviation parts that would make good candidates for the advanced manufacturing process, Myers said.
AMCOM chose the Black Hawk for the project out of practicality. “That’s what we have the most of in the Army inventory and also in all of the other services,” Myers said. There were enough Black Hawks in the field to pull one out of service for the project without adversely affecting Soldiers, she explained.
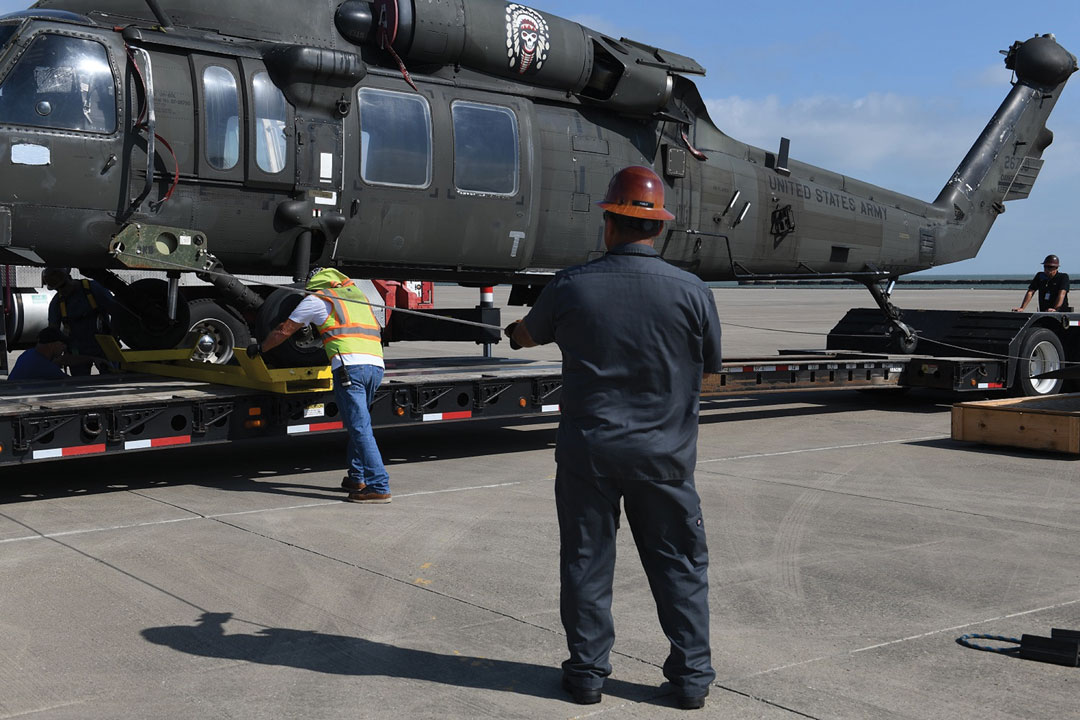
VIRTUAL MODEL: A UH-60L fuselage and an operational Black Hawk helicopter were transported in May from Corpus Christi Army Depot to Wichita State University, where researchers at the National Institute of Aviation Research will create a virtual model. (Photo by Lisa Simunaci, AMCOM)
THE PROCESS
Scanning a helicopter is no easy task. First, the helicopter—just the structural shell, with all the electronics and rotor blades removed—had to be brought to the research center. “For this effort we are focusing on the major structural components; we’re not scanning any of the wiring, harnesses, nuts, bolts or the brackets. We’re not scanning the transmission.” Myers said, a note of relief in her voice.
Once the helicopter skeleton arrives, Wichita State students and supervising engineers take it apart, piece by piece, scanning each part with a hand-held scanner. Yes, that’s right—even large pieces are being scanned by hand.
After each part is scanned, it is matched with 40-year-old structural drawings of the Black Hawk—some of which are difficult to read—and labeled with the correct name and part number, Myers explained. “Every single part is identified,” she said.
To create the full 3D twin, the team has to merge the information in the old 2D drawings with the 3D scan. “That scan gives us a complete 3D model file,” Myers said. “Now we are starting to get the full picture. [The twin] tells us the measurements, it tells us what each scanned part is called, it tells us the part number, it puts in the distribution statement [minimum security level required to read it], it puts in the export warning control [identifies export-controlled technical data], it puts in the annotations,” such as dimensions, geometric tolerances, symbols and notes to document the design and manufacturing requirements.
The team will scan approximately 5,000 individual parts over the course of 30 months, she said. During that arduous process, as each structural component scan is completed, NIAR will review it for quality control and then send it back to the Army. “We will put it into our product life cycle management tool that we use, that the Army uses,” and it will undergo different engineering reviews for further quality and safety evaluation, Myers said.
“Now this is where it’s starting to be real interesting,” she continued. “How do we tie that to the logistics process? How does a logistician go in and look at and understand this 3D model? Do logisticians and maintainers have the software and skills to be able to do it?”
This is another aspect of the pathfinding process, Myers said. Finding out which software needs to be purchased at what cost, who should be viewing the twin model, what skills are needed, etc. “We’re trying to figure out which questions we should ask, which answers do we need—it is truly a pathfinder,” she said.
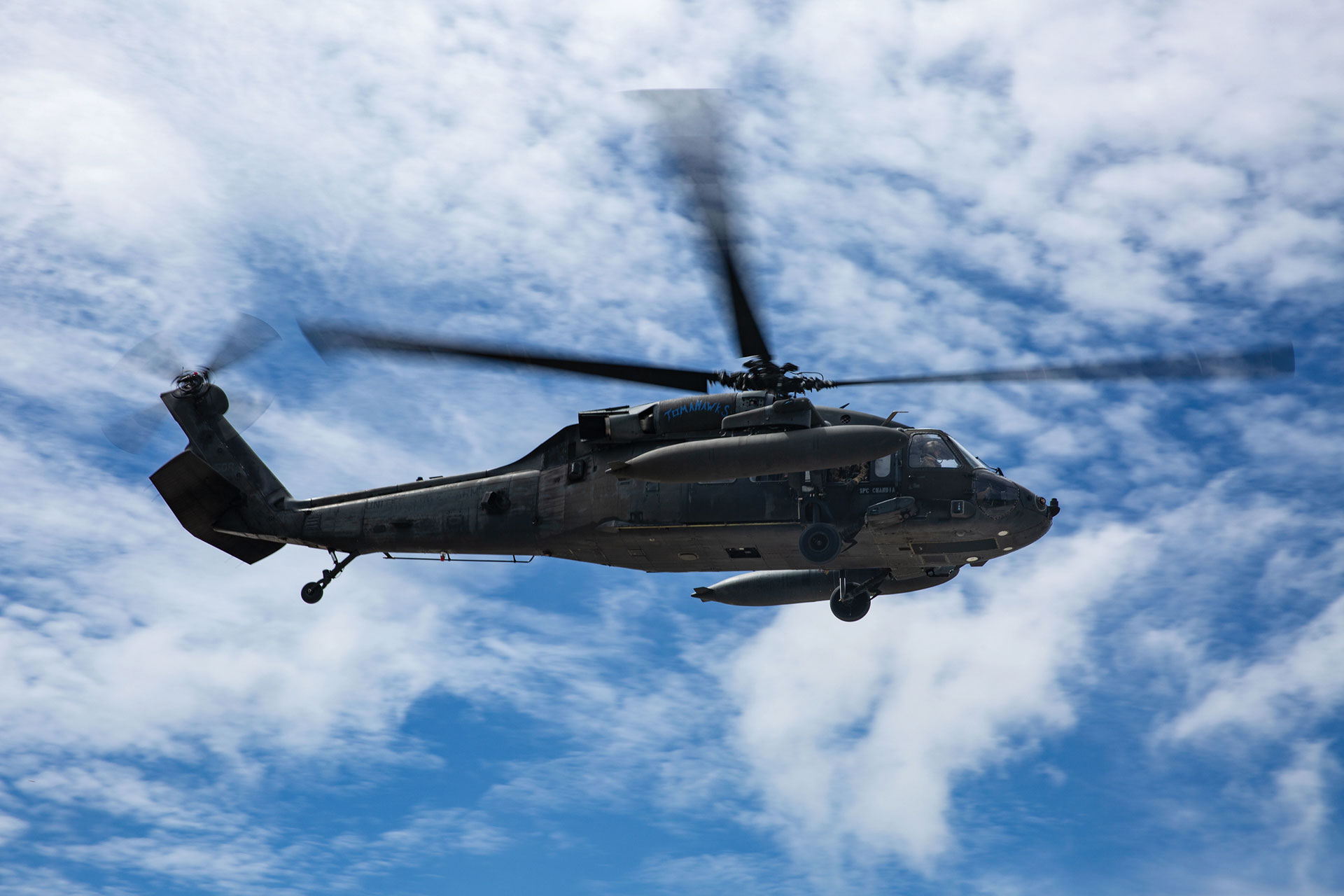
WORKHORSE: The UH-60 Black Hawk is the workhorse of Army aviation. (Photo by Spc. Thoman Johnson, U.S. Army Pacific Public Affairs Offic
The Black Hawk, at 40 years old, has parts that are obsolete or hard to get—some vendors don’t want to make parts for it because the drawings are too difficult to read, and they would have to reverse engineer to make a model, mold or casting to create a replacement part from that “old, often hard-to-read drawing,” Myers said. “We can use these models to give to vendors to perhaps create a part after it’s been qualified for advanced manufacturing, after it’s gone through the appropriate qualification process.”
In the future, the Army could require manufacturers to provide a digital twin with each type of aircraft—creating a digital thread from the beginning of the manufacturing processes. In fact, the National Defense Authorization Act for fiscal year 2022 asks that DOD report on the development of digital twin technology and how it can be best used in the future.
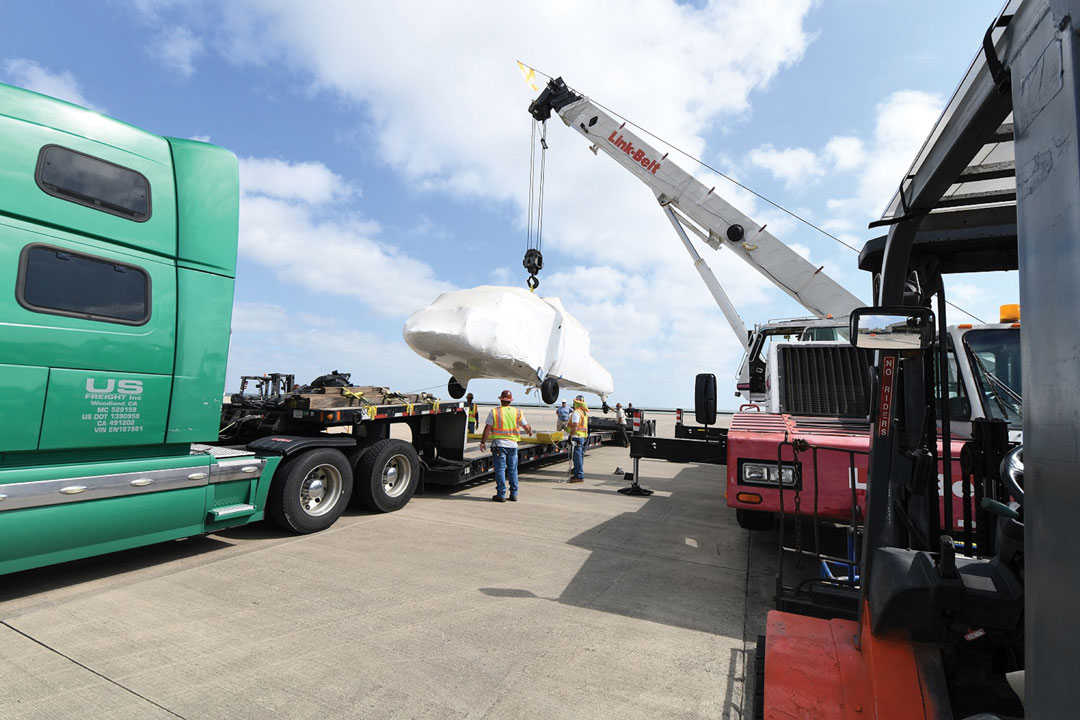
LOOKING AHEAD: AMCOM’s Data and Analytics Center is looking at how to fix or improve processes already in place, as well as how to lay the foundation for the future. The Black Hawk digital-twin pathfinding project is part of that future. (Photo by Lisa Simunaci, AMCOM)
TWINS AND THREADS
The digital twin has another sibling, sort of—the digital thread. What’s the difference between a digital thread and a digital twin? Simply put, a digital twin is the current representation of a system or product, while the digital thread is a lifetime record of the system or product, from creation to removal.
“Digital threads start at the beginning,” Myers said. Engineers create a digital model of something that does not currently exist that they would like to produce—like a new and improved recliner, she explained. This is also where the digital twin begins, at the from-scratch manufacturing process. The Black Hawk twin pathfinding project is doing things a little backward, since it is producing a twin of something that already exists, to help inform future efforts.
However—at the beginning of the digital thread—the twin is used for engineers to perform various analyses. Will the chair hold a certain amount of weight? Will it flip back too far when opened with vigorous force? And that digital model, after testing, is used to build a prototype, Myers said, which then endures its own round of tests.
After that round of testing, advanced manufacturing can be brought into the digital thread process. Parts of the recliner can be engineered to be lighter and stronger, or new 3D-printed features can be added, she said.
“We’re creating that digital thread from the time [an aircraft is] created as a new platform through its entire life cycle,” Myers said. “So, if we add a radio, we update the digital twin with the radio on it and we know exactly where it’s been mounted. In four years, if that radio comes out for whatever reason, we can update the digital twin and show that the space is available again.”
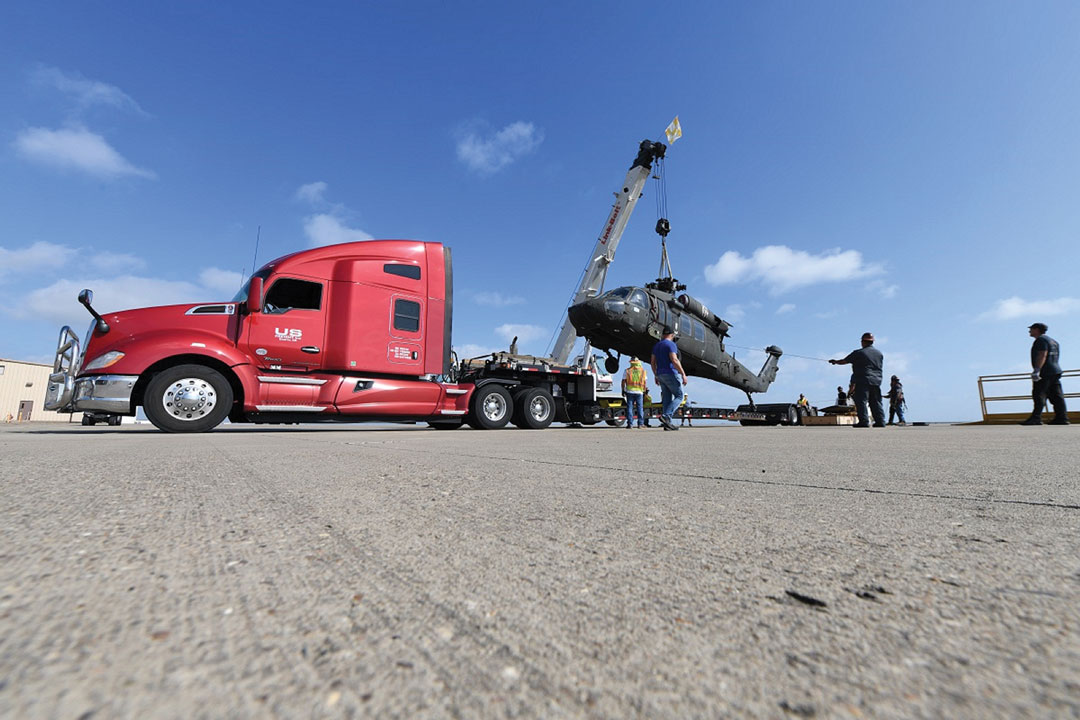
ON THE WAY: An operational Black Hawk helicopter and a separate fuselage began an 800-mile journey on May 18 from Corpus Christi Army Depot in Texas to Wichita, Kansas. (Photo by Lisa Simunaci, AMCOM)
THE FUTURE IS PRINTED
AMCOM’s March 2021 policy memorandum addressed advanced manufacturing for Army aircraft parts, components and support products. As aircraft like the Black Hawk continue in service, the supply system faces obsolescence challenges—parts becoming hard to buy or make—and advanced manufacturing, using the digital thread and twin technologies, can help overcome those challenges.
“The policy is really put in place to provide some structure and guidance to say, these are the different categories of the aviation items that can be printed,” Myers said. AMCOM’s policy is there to help provide further guidance on the Army’s overall advanced manufacturing policy for the aviation enterprise. “Gen. Royar held working groups … [with] our aviation counterparts, GE, Boeing, across the community to come together as a collaborative cohort, if you will, to write this” policy. The policy is not static, though, and they are already working on the next revision.
AMCOM is also working closely with Army Materiel Command, which is leading the advanced manufacturing effort, she said. The policy will help determine what will make a good candidate for advanced manufacturing in the aviation community.
“We will be able to print parts, but we may not want to advance-manufacture airworthiness or critical safety items today based on the technology available. However, having a digital model for these complex parts sets the groundwork for the future,” Myers said. “There’s going to be levels of who can print what. It’ll be very controlled and tied to specific roles to ensure traceability.”
Advanced manufacturing, using the digital thread and twin technologies, ultimately will help improve the supply chain, reducing the lead time on part acquisition and potentially allowing for on-site part production for quick repairs.
“We’re already engaged with Wichita State to look at some composite advanced manufacturing of parts,” Myers said. They are working with the university to determine appropriate processes and what might be missing in the AMCOM advanced manufacturing strategy, she added.
AMCOM is also pursuing other advanced manufacturing efforts with different universities—like Auburn University—“and the Army looks forward to realizing there’s a lot of value to be gained by partnering with academia, especially where they have research on the front end,” Myers said.
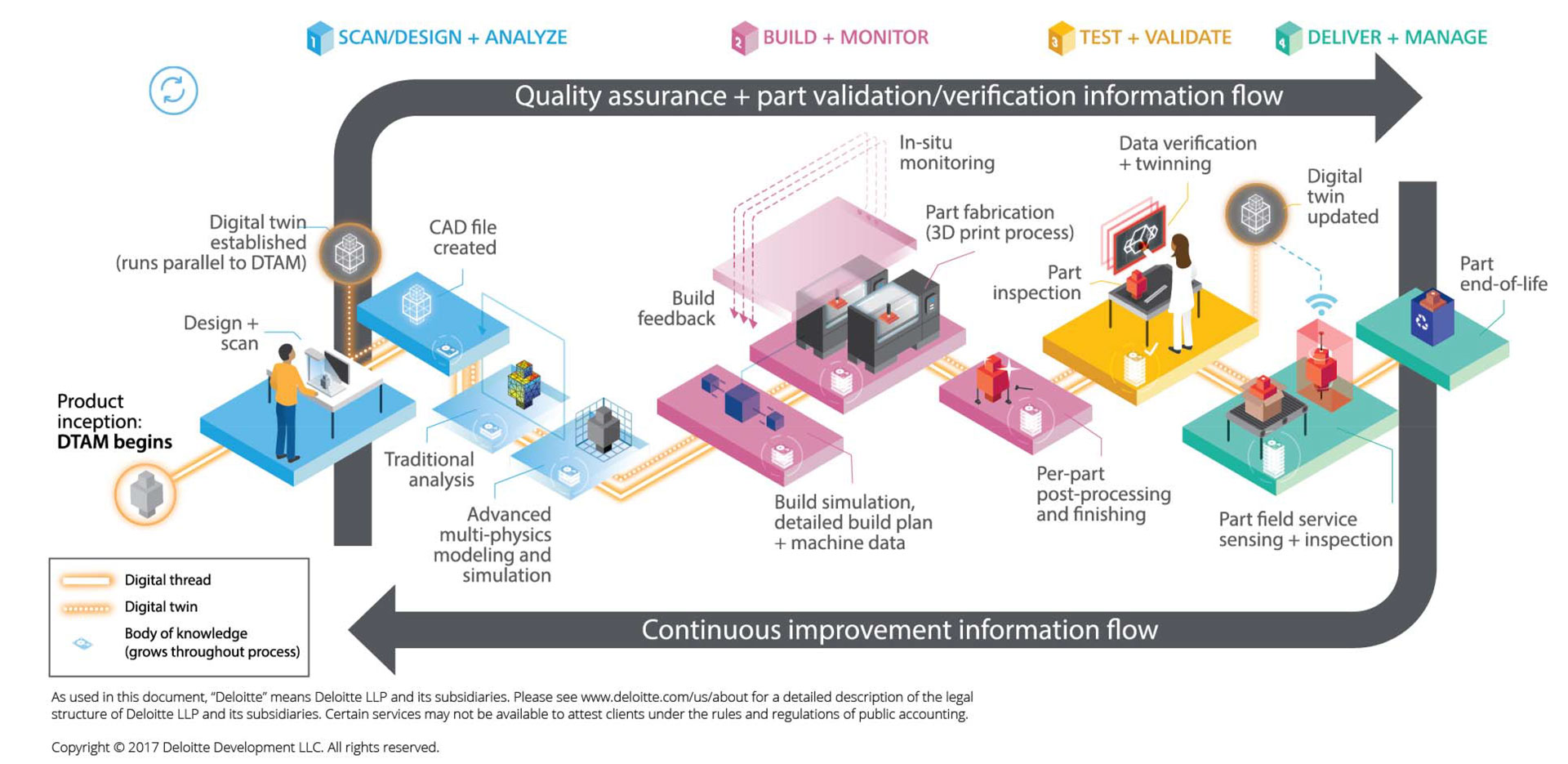
BUILDING A TWIN: The digital twin process, from beginning to end. (Graphic by Deloitte Development LLC)
CONCLUSION
The digital twin technology will help improve supply and maintenance for current aircraft like the Black Hawk. But if AMCOM can improve its processes and skills, identify the right software and pinpoint gaps in policy and procedure, it will help to inform the people, process and technology decisions as it moves forward.
“Gen. Royar’s just really leaning forward to make sure that not only is he helping the Soldier today, but that we keep helping Soldiers for years to come,” Myers said.
For more information, contact the AMCOM Data and Analytics Center at usarmy.redstone.amcom.list.data–analytics@mail.mil.
JACQUELINE M. HAMES is an editor with Army AL&T magazine. She holds a B.A. in creative writing from Christopher Newport University. She has more than 10 years of experience writing and editing news and feature articles for publication.