
A FINE VINTAGE: A Marine Corps combat instructor fires an M1 Garand during vintage rifle live-fire competition on Camp Pendleton, Calif., in 2018. (Photo by Lance Cpl. Drake Nickels)
The development of the M1 Garand Rifle—from not quite right to world beater.
by Dr. Thomas E. Ward II
“In my opinion, the M1 rifle is the greatest battle implement ever devised.”
—Gen. George S. Patton Jr.
During WWII, no other nation was able to field a full-power semiautomatic rifle as its primary infantry weapon. Several tried, but for a variety of reasons, they all failed. The U.S. Rifle, Caliber .30, M1 (known informally as the M1 Garand) earned a reputation for accuracy, reliability and ruggedness, but the real technology-enabled overmatch was in terms of firepower. No one else could match the hard-hitting firepower in the hands of the U.S. infantryman. Adversaries were simply outclassed. Still, a little-known part of the M1 Garand story includes a serious redesign effort. The original design, the “gas trap” Garand, did not work very well.
While today’s culture has developed an expectation that new technology drives near-instantaneous evolutionary innovation, the much more mundane backstory is often long and complex. The development of the M1 Garand provides an example, and a cautionary tale. Employing the latest technology in new weapon systems is hard work, and the results are not always predictable. Sometimes the acquisition community gets it right, but seldom do they get it right the first time. The M1 Garand provides an example of an initial design that wasn’t quite right, but with a few design changes it went on to become one of the most successful infantry weapons of all time.

A GARAND HISTORY: Robert Bell, an M1 Garand armorer, holds one of the historic rifle at Camp Perry, Ohio, in August 2018. Over the past 65 years, most of the rifles have been rebuilt, refinished, rebarreled and repaired at least once, with few in original condition still today. (Photo by Sgt. Dana Beesley, U.S. Marine Corps)
COMBINING NEW TECHNOLOGIES
In its original “gas trap” incarnation, the M1 rifle exhibited serious performance problems in the field. Although its development was lengthy and deliberate, the original design was deeply flawed. However, hard-nosed realism and listening to the experience of Soldiers in the field led to a relatively simple redesign that resulted in “the greatest battle implement ever devised.”
The desire to develop and field a self-loading infantry rifle was almost universal in the years between the first and second World Wars. Several recent or emerging technologies were available that could be combined to achieve that goal, but no one was quite sure exactly how to combine those technologies in a way that worked. The development of smokeless powder in 1884 was the first key. Smokeless propellants reduced the visible signature created when a weapon was fired, providing a significant advantage on the battlefield. They also enabled higher chamber pressures and greater projectile velocity, which in turn enabled the use of smaller diameter, lighter-weight projectiles with a greater effective range. These were enormous advantages that were recognized and exploited almost immediately. Rifles could be designed with shorter barrels, which meant lighter-weight weapons. Lighter projectiles meant that the individual Soldier could carry more ammunition. Additionally, the use of smokeless propellants greatly reduced the amount of corrosive residue left behind in the weapon from the burned propellant. With the dramatic reduction of corrosive fouling, it became possible to design reliable mechanisms that could eliminate the requirement to manually manipulate a bolt to extract a spent cartridge, cock the weapon and load a fresh cartridge in the chamber. Weapon designers recognized the possibility, but combining the new technologies was another matter.
There were essentially two competing technologies:
1. Using the recoil energy to operate the action;
2. Using the energy of combustion gases to operate the action.
Recoil-operated mechanisms emerged first.

INNER MECHANISM: In the gas trap design, hot gas is trapped after the projectile leaves the muzzle. In the gas port design, hot gas is ported to the gas cylinder before the projectile leaves the muzzle. (Graphic by the author)
THE RECOIL APPROACH
Semiautomatic pistols emerged in the late 19th century. For low-powered pistol cartridges, the inertia of a slide combined with the tension of a spring sufficed to keep the cartridge case in the chamber long enough to allow chamber pressure to fall off. Higher-powered cartridges required a breech locking mechanism, and a method of delaying breech unlocking. The U.S. M1911 pistol used a short recoil design, in which recoil caused matching grooves and lugs in the barrel and slide to disengage after a relatively short length of travel caused by recoil.
Recoil-operated design of semiautomatic weapons was not confined to pistols. The original Maxim machine gun, which first appeared in 1884, used a recoil-powered toggle lock linkage in its design.
During World War I, the U.S. developed the Pederson device, a recoil-powered adapter that could be placed in a slightly modified M1903 Springfield rifle, making it capable of semiautomatic fire. However, the Pederson device did not use the .30-06 rifle round. Instead, it employed a much lower velocity pistol-type cartridge, so it lacked the range and power of the full-sized rifle round. The technology to adapt semiautomatic operation to a full-power individual infantry weapon just wasn’t available.

COMPARATIVE QUALITY: The U.S. Marine Corps’ two primary rifles in WWII were the M1903 Springfield (middle) and the M1 Garand (bottom). A .30-40 “Krag” rifle is shown at top. (Photo by U.S. Marine Corps)
EXPANDING GAS
The competing technology used expanding combustion gases to cycle the operating system. Inventors tried a variety of technological approaches to use propellant combustion gases to achieve automatic or semiautomatic operation of firearms. Some used gas ported from the barrel (a “gas port” design), while others used gas escaping from the muzzle (a “gas trap” design). The original M1 Garand employed a fixed muzzle cap to trap muzzle gases, which then acted on a gas piston that moved in the opposite direction from the projectile.
Several other weapons tried this design; none were successful. The problems were with the basic design concept. Once gases escape from the muzzle, they tend to cool rapidly, leaving carbon deposits behind (carbon fouling). Additionally, primers of the day used corrosive salts that required careful cleaning after use, but the complex design of the gas trap mechanism and its close tolerances made cleaning difficult.
OVERCOMING CHALLENGES
The prototypes and early production specimens of the M1 Garand seemed to work well enough but proved to be unreliable in the field. Shortcomings included the complex procedure to clean the gas trap assembly, an unstable front sight and a weak bayonet mounting system. During field testing, a loose screw securing the muzzle cap to the barrel allowed the assembly to move out of alignment. This resulted in the projectile striking the gas trap assembly as the projectile exited the muzzle, taking the gas trap assembly with the projectile. Ultimately, John Garand—the rifle’s principal designer and whose name it still bears—and the Springfield Armory in Massachusetts modified the design to employ a gas port drilled near the muzzle. The port bled combustion gases into a closed chamber, where the gases acted on a piston at the end of an operating rod. The cylinder and piston assembly near the muzzle was simple to remove for operator maintenance and proved to be extremely reliable.
Why did Garand initially use a gas trap mechanism, rather than a ported barrel and a closed-chamber gas piston? Although smokeless propellants had been around for 50 years, weapon designers of the day did not fully understand or trust the technology, even with examples of successful designs in the field. The Colt M1895 “potato digger” machine gun employed a gas port design, but its port allowed gas to move the lever as it escaped through the port and vented into the atmosphere. The M1918 Browning Automatic Rifle was a gas port design but was much too heavy to use as a standard individual weapon.
Distrust of the gas port was not unique to the United States. Interestingly, a 1941 German request for proposal equivalent precluded a ported barrel. The German G41 (M) and G41 (W) both used gas trap designs similar to the early Garand design, and were unsuccessful. A follow-on to the G41 (W), the G43, used a gas piston design and was highly successful, with 400,000 produced between 1943 and 1945. However, the Americans had at least a five-year head start. Americans recognized and solved their problems with their semiautomatic infantry rifle before they entered the war.
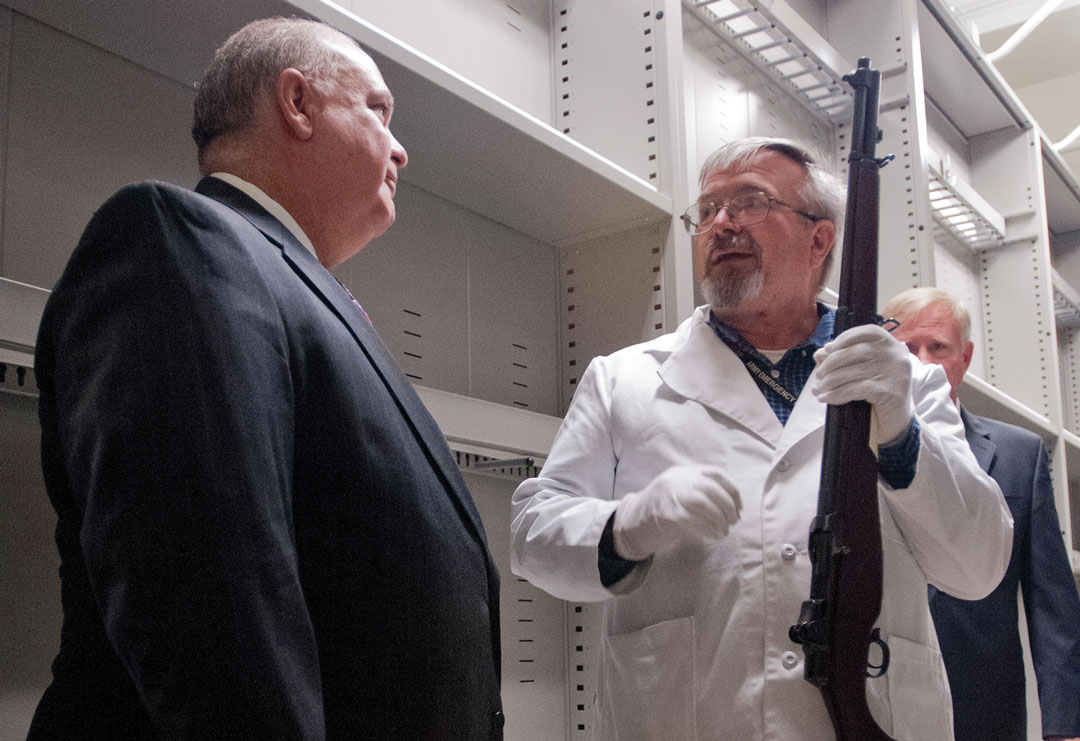
THE PRECURSOR: James Speraw, an Army curator, shows Joseph W. Westphal, then undersecretary of the Army, a T3E2 semiautomatic, .276-caliber experimental rifle at the Army Center of Military History’s Museum Support Center Facility at Fort Belvoir, Virginia, in 2012. This rifle, developed by John Garand at Springfield Armory, was the precursor to the M1 rifle of WWII fame. (Photo by Staff Sgt. Bernardo Fuller)
Initial adoption of the M1 Garand did not go smoothly. Springfield Armory produced roughly 50,000 “gas trap” rifles between 1936 and 1940. Unfavorable field experience prompted a redesign, from a gas trap to a gas port. Fortunately, the modification was easily implemented in new production, and modification of existing gas trap rifles could be accomplished at depot level maintenance facilities. Starting in 1940, all new production of M1 rifles used the new gas port design.
What became of the 50,000 gas trap Garand rifles produced between 1936 and 1940? Priority for distribution for the majority of the early production rifles was to the troops in the field—including U.S. Army forces in the Philippines. For refit of existing gas trap rifles, the plan was to replace the gas trap assembly when the barrel or the gas trap assembly became unserviceable. Rifles within the United States were returned to U.S. depots for modification. Rifles issued to deployed units were modified by forward depots. A small number of gas trap rifles saw service during WWII. The upgrade modification process was ultimately successful, and the vast majority of M1 rifles received the modification long before the war’s end. Consequently, unmodified gas trap Garand rifles are exceptionally rare today and command an enormous premium in the collector’s market.
A number of M1 rifles fell into Japanese hands when besieged U.S. forces at Corregidor Island in the Philippines surrendered. The Japanese exploited this technical intelligence bonanza and worked hard to reverse-engineer the M1 Garand design for their own use. They were only partially successful. Japanese copies of the M1 never progressed much beyond the prototype stage. An example of the Japanese Type 4/Type 5, a copy of the M1 Garand rifle, can be seen in the collection of the National Rifle Association Museum.
PROVEN IN BATTLE
At the beginning of the WWII, the U.S. Army was committed to replacing its M1903 Springfield rifles with M1 Garand rifles. The U.S. Marine Corps did not adopt the M1 until 1940, so it began WWII relying primarily on the M1903 Springfield rifle. Photographs of the Guadalcanal campaign show Marines equipped with Springfield rifles. Marine Corps forces did the best they could with what they had, and their success at Guadalcanal hinged on the ability of U.S. Navy forces to prevent Japanese reinforcement. U.S. Army forces began reinforcing the Marines on Guadalcanal in November 1942, and in December the U.S. XIV Corps assumed responsibility for the operation. As U.S. Army forces flowed in, the Marines observed firsthand the enormous increase in firepower that Army forces enjoyed with the M1 Garand. Seeing was believing, and the Marines were finally convinced they needed “some of that.” Reequipping Marine Corps forces with the M1 Garand became a high priority, and the Marines thereafter enjoyed the same firepower advantage that their Soldier brothers brought with them to Guadalcanal.
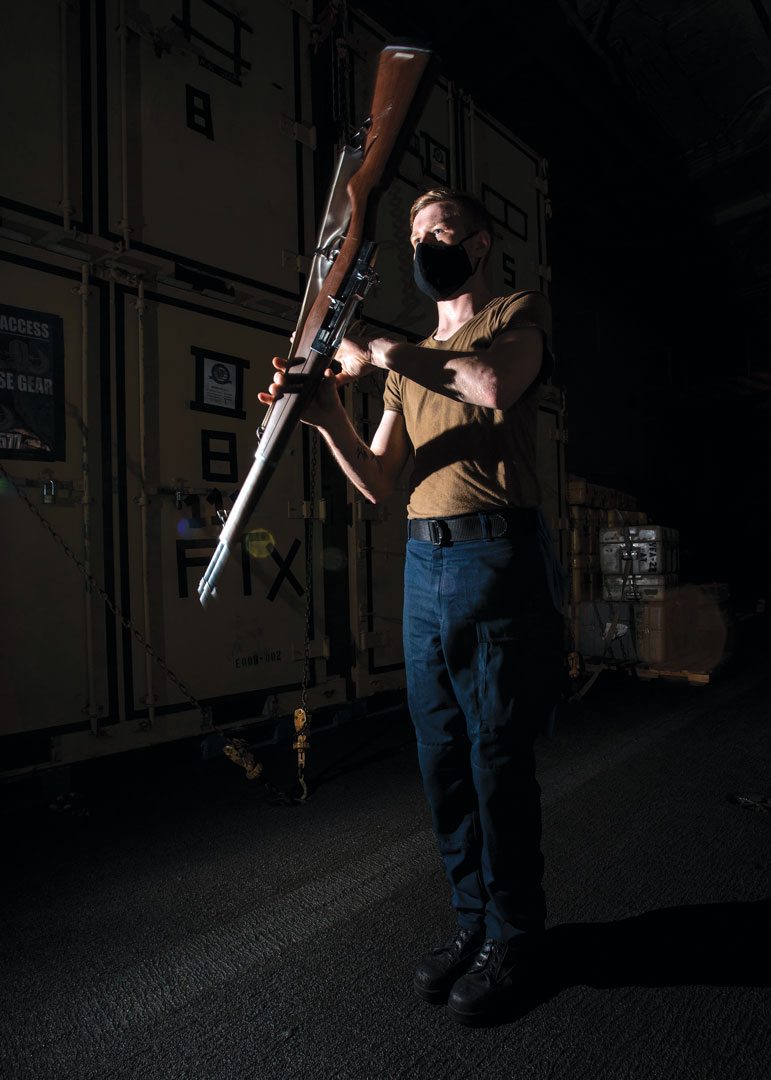
CEREMONIAL USE: The M1 Garand is now frequently used for ceremonial purposes, including honor guards and color guards. (Photo by Petty Officer 3rd Class Elliot Schaudt)
FROM GOOD TO GREAT
The rest, as they say, is history. The adoption of the gas port design to the M1 Garand turned a flawed, mediocre weapon into a world beater—literally. The U.S. had an enormous head start over both its enemies and its allies in its development of the infantryman’s rifle. That head start was the result of deliberate and persistent effort over a period of many years, starting immediately after the end of WWI. The path was not a straight one; it was full of dead-end ideas and concepts that were ahead of their time. Still, by the time the original gas trap Garand was selected and fielded, no one else was even close to fielding a full-power, self-loading service rifle. In the intervening years between the rifle’s adoption and the U.S. entry in WWII, the Army had an opportunity to sort out the “bugs” before putting the rifle to the ultimate test of combat. That was time well spent. While it may have been a “good” design, the gas trap Garand was not great—it had too many problems. The relatively minor modification, from a gas trap design to a gas port design, made all the difference in the world.
CONCLUSION
What lessons should one learn from this experience? First, despite years of developmental effort by the best designers in the world, the first product may not turn out to be quite what we expect. Low-rate initial production (today’s term for producing an initial batch of approximately 10 percent of anticipated production) is an excellent practice. The U.S. Army is doing exactly that right now with the Joint Light Tactical Vehicle. Putting a new product in the hands of troops and paying attention to their feedback based on experience creates an opportunity to detect and correct unexpected shortcomings.
These days, the U.S. does not design and produce its small arms in the arsenal system any longer. It outsources that function to industry and relies on commercial sources for meeting its needs. That makes prototyping and competitive testing even more important than ever.
The complex story of the M1 Garand’s development provides good cause for encouragement. The rifle’s groundbreaking design wasn’t quite perfect at birth, but it was close. Although field performance of the gas trap design was sorely disappointing, with just a little bit of tweaking it became a great rifle—the stuff of legend, and the very best, most reliable “friend” for millions of GIs.
For more information on the Springfield Armory and the development of the M1 Garand, go to https://www.nps.gov/spar/index.htm.
THOMAS E. WARD II is an associate professor in the Department of Sustainment and Force Management at the U.S. Army Command and General Staff College (CGSC) at Fort Leavenworth, Kansas. He has a Ph.D. in organization and management from Capella University, an MBA from the Florida Institute of Technology and a B.A. in political science from the University of Oklahoma. He served 26 years on active duty as a U. S. Army ordnance officer, and has taught force management at CGSC for 14 years.