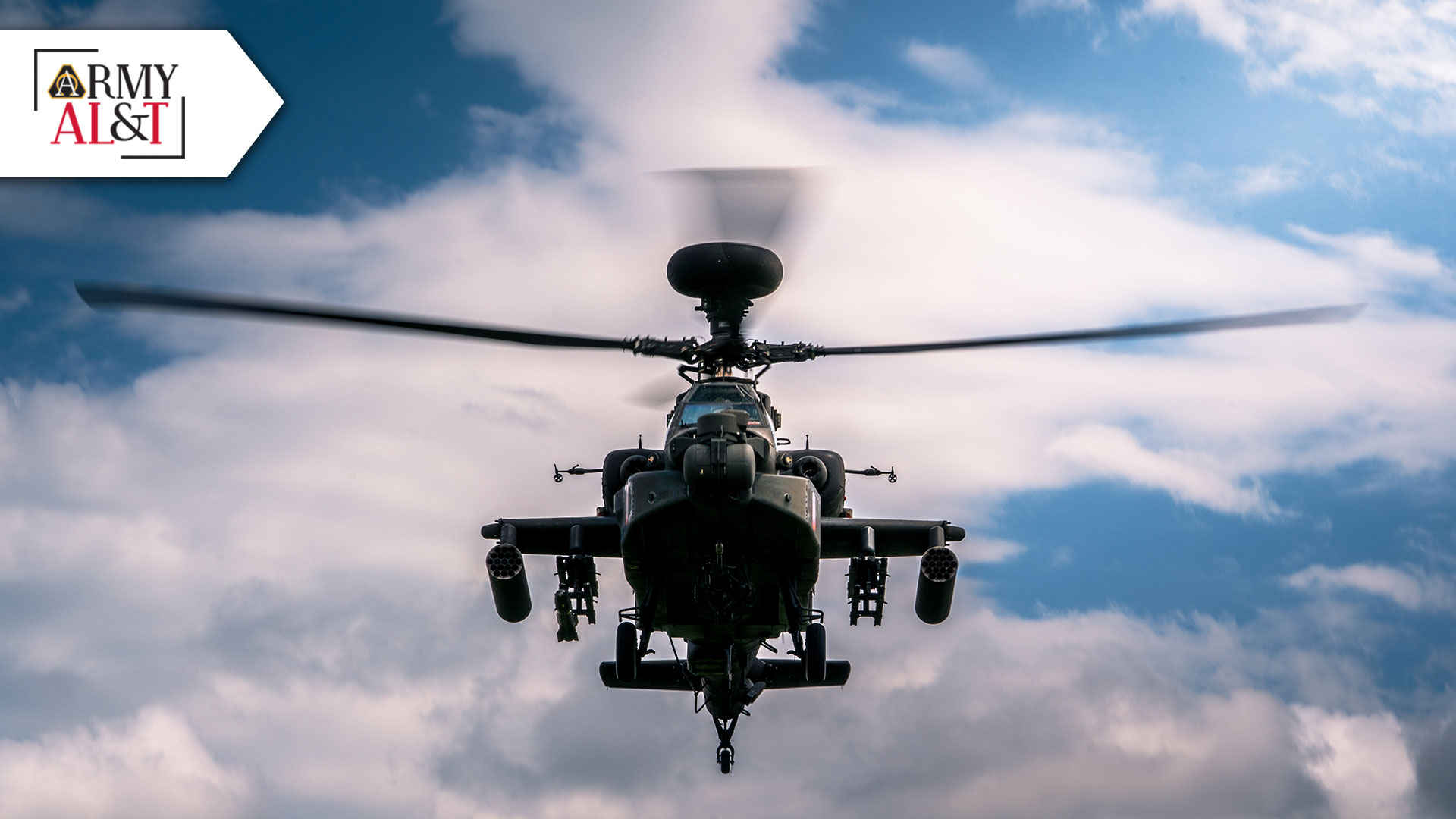
TAKING FLIGHT: An AH-64 Apache takes off at Katterbach Army Airfield, Germany, on June 24, 2021. (Photo by Maj. Robert Fellingham, U.S. Army)
Prognostic and predictive maintenance give aircraft maintainers insight into what might go wrong, and when.
by Lt. Col. Andy Bellocchio, Ph.D. and Danny Parker, Ph.D.
Prognostic and Predictive Maintenance (PPMx) is the U.S. Army Aviation’s initiative to advance from a reactive maintenance posture to a proactive, decision-based approach. PPMx’s goal is to arm the maintenance manager with the information to make efficient decisions that avoid mission disruption and eliminate premature removal of components. The desired effect is increased availability, reduced cost of ownership and increased safety.
Traditional aircraft maintenance has been the combination of correcting unexpected faults and following a preventive schedule that is reactive and overly prescriptive. This reactive approach is akin to Gen. George Washington and the American Army responding to brutally cold weather at Valley Forge, as it happened, with almost no advance notice of changing conditions. Fast forward 200-plus years and weather predictions are part of our everyday life. They help us decide what to wear each day, understand whether it is safe to fly, and anticipate any impacts on a mission. Weather forecasting is so prevalent that we often do not think about how it is informed by a network of stations and radars that feed advanced models capable of predicting weather with a varying degree of accuracy over several days.
The maturation of PPMx is similar to the advance of weather forecasting. Diagnostics and failure characteristics provide maintainers with a more complete understanding of an aircraft’s health, much like radar and weather stations define conditions in the sky. Prognostic systems forecast the future health of an aircraft, just like weather forecast models predict daily conditions. Such information about current and future health will inform our decisions on aircraft readiness, what maintenance needs to be done today, and which in the future, to best meet upcoming operational demands. Planning maintenance for the future based on the current health of the aircraft and its forecast state is known as predictive maintenance. The advantage of PPMx is that maintainers gain new, quantifiable knowledge of impending failures. They can decide when to conduct a repair by weighing the risk to the aircraft against operational demands. The efficient control of maintenance will increase operational availability, decrease lifecycle costs and reduce mission disruption.
QUANTIFYING RISK
Predictive maintenance is built on a series of decisions following a framework that scientifically evaluates the likelihood of component failure and its effect on the system. The approach is not much different than the Army’s composite risk management. Risk is defined as the product of probability (likelihood of component failure) and severity.
Risk=Probability×Severity
Severity is measured by the criticality of a fault and is denoted by the threat of injury to crew and damage to systems, repair time, repair cost and mission disruption. The weighting and combination of these factors, from criticality to mission disruption, are defined in reliability engineering as the “loss function.” Risk is formally calculated using a Bayesian framework with loss functions. The Bayesian framework is a mathematical means to update the probability of failure given measured evidence (data). The likelihood of failure is updated by diagnostics that provide the data (measured evidence) to evaluate system health. The likelihood is fused with the criticality to give an estimate of the risk to the platform. The risk for each component is then synthesized into an overall risk to the aircraft. A deep dive into this topic, along with the data requirements and calculations, is best reserved for a technical article; however, it is important to know that minimization of the composite risk drives the decision about whether to conduct maintenance now or defer to the next window, ensuring there is no unscheduled maintenance in between. The framework accurately assesses and properly bounds predictions and conveys that information to commanders, maintainers and logisticians.
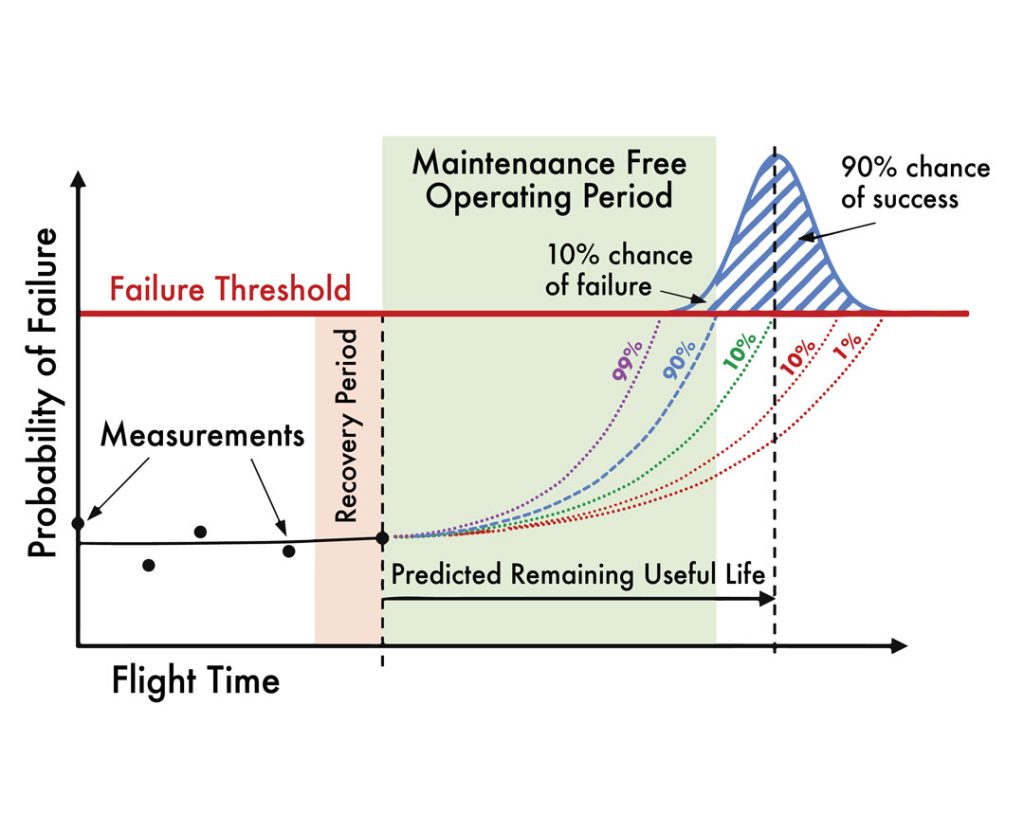
SURVIVABILITY ASSESSMENT: The probability of failure increases with the accumulation of wear during flight hours. (Graphic courtesy of the authors)
USING RISK TO MODERNIZE
Making predictions about the future is inherently a probabilistic task. Uncertainty grows the further into the future a prediction is made. We have experienced this. Weather predictions become less reliable the further in the future they forecast. The same is true for components that experience wear and fatigue in the rotor, flight controls, airframe, engine, drive and weapon systems. Figure 1 (see Page XX) illustrates the probability of failure increasing with accumulation of wear during flight hours. In practice, an onboard diagnostic system collects usage and environment data to make an estimate of the current health state. Next, expected usage and prognostic models forecast failure times where the spread of possible outcomes increases the further in the future the prediction is made.
Figure 1 illustrates PPMx supporting a maintenance-free operating period. The operating period, shaded green, provides an extended period without disruption by maintenance. The recovery period, shaded orange, consolidates maintenance tasks between the operating period and provides discrete windows for maintenance. The key question when entering a recovery period is: “What is the likelihood each component survives to the next recovery period?” To answer this question, a measurement is performed that assesses the health state while in the maintenance window. This can be done through a combination of embedded solutions and nondestructive inspections. The estimated health state is then combined with expected usage to predict the remaining useful life.
Because of the uncertainty in predicting the future, a range of possibilities is computed. This is shown as a blue normal distribution. The dotted lines that lead from the current health estimate to the future represent the probability that the component survives at least that many hours. The most likely time of failure (highest point in the distribution) is called the expected remaining useful life, but the component may fail at any of the times under the distribution of possible outcomes.
As indicated by the blue hash area, the component has a 90 percent chance to remain functional by the end of the operating period and, consequently, a 10 percent chance the component will fail. The future risk is the product of this 10 percent probability and the criticality of the component. With this estimate of the future, a maintainer has the information necessary to make appropriate maintenance decisions today. If the risk is unacceptable, then the framework can be queried for which components are driving the risk over the acceptable threshold.
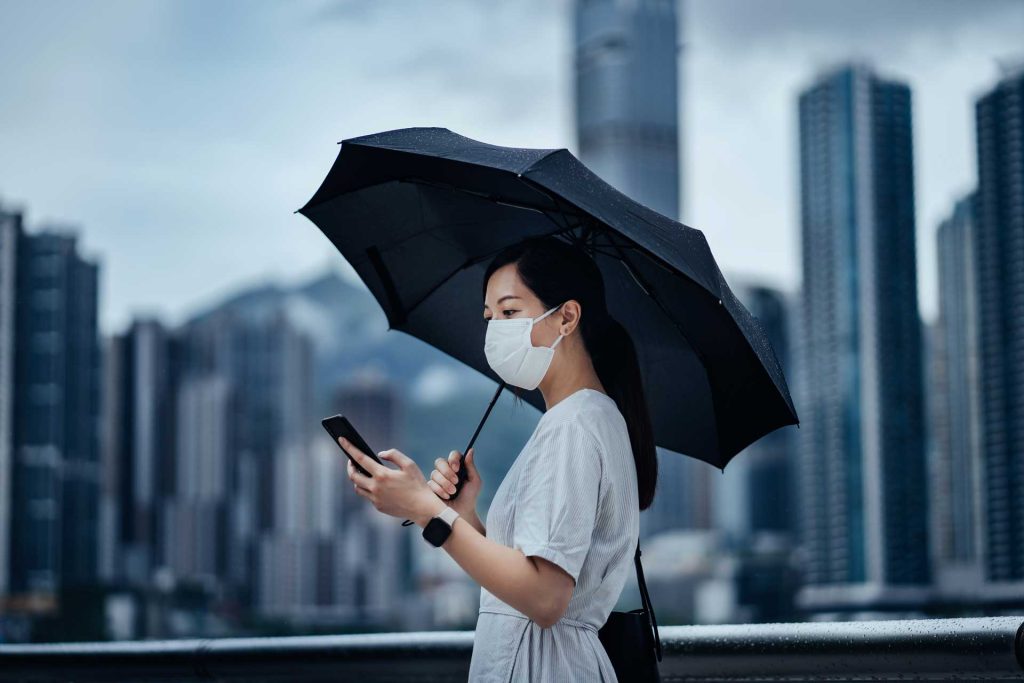
CHANCE OF RAIN: Just as weather forecasts allow travelers to prepare for rain, predictive maintenance will allow aircraft maintainers to anticipate needed repairs before component failure. (Photo by Getty Images)
Under PPMx, the uncertainty about the remaining useful life adds complexity to the maintenance decision. Using the weather example, if the forecast gives a 40 percent chance of rain in five days, a traveler may pack an umbrella for a trip. Thus, the uncertainty about the prediction influences actions today as we hedge against future risk. With less variation in the predicted remaining useful life, a component will remain in service longer and the Army will see more benefits from PPMx.
Risk mitigation is a core goal under PPMx. To maintain safety, most of the time the failure will never occur. For aircraft using PPMx in a maintenance-free operating period strategy, some near-but-not-yet-failed parts will be removed. In doing this, the maintainer is trading economically useful life for uninterrupted flight operations. These parts would still be operating in the prescribed limits, but will be removed because they are expected to fail before the next maintenance window.
Our inability to know the exact moment of component failure is quantified by the uncertainty. The uncertainty about the health statement drives maintenance actions which then raise sustainment costs and keep availability low. Better diagnostic systems and prognostic models with reduced uncertainty maximize the use of the remaining useful life to save money and minimize mission disruption.
MODERNIZED THINKING
PPMx is a concept that hinges on probabilities, yet thinking in probabilistic terms does not come naturally to humans. The engineering community needs to strive to give accurate assessments of the risks, broken out into usable information. For example, the risks could be reported as several different categories like safety critical, mission affecting, or reduced mission capabilities.
In addition, commanders, pilots and maintainers will need dedicated training to use the risk information effectively. Commanders need to know how to evaluate their local risk tolerance and match it to the equipment on hand. Pilots can use the information to familiarize themselves with emergency procedures relating to high-risk component failures. Maintainers will need guidance on the cost-benefit analysis of replacing components before they fail, how to handle near-but-not-yet-failed parts, and what opportunistic maintenance should be performed in the recovery period. This is a vastly different mindset than current maintenance.
Support organizations will have to modernize for PPMx. Spares can be purchased by looking at the probability distributions and calculating the expected number of failures over the fiscal quarter. Predictive maintenance allows logistical ordering to lead the maintenance, thereby reducing logistical downtime and increasing availability. However, depots will need to develop additional testing capabilities because the parts will be removed before failure and the onboard systems will rarely collect data that show what a failure looks like. Depots should run these parts to failure and feed the data back into prognostic systems to improve the quality of the predictions.
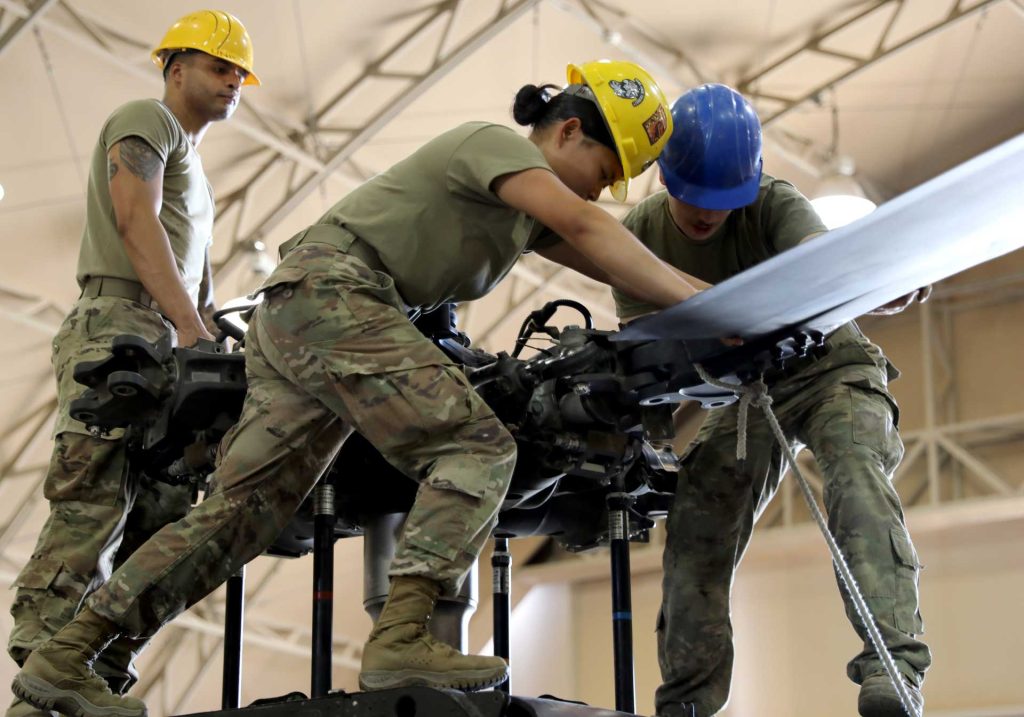
A GROUP EFFORT: UH-60 Black Hawk helicopter mechanics with Bravo Company, 640th Aviation Support Battalion, prepare to loosen a helicopter blade before pre-maintenance for a Black Hawk at Camp Buehring, Kuwait, June 25, 2021. (Photo by Sgt. 1st Class Ryan Sheldon, 40th Combat Aviation Brigade)
CONCLUSION
The changes to the current sustainment system required to implement PPMx are numerous and go beyond adding sensors to the aircraft. Formalizing the decision framework first is of utmost importance since all requirements—data, accuracy, organizational and training—flow from that implementation. Policies need to be created and changed as necessary to allow for probabilistic assessments of the future health state. Hardware requirements and standardization should be developed. Training should be done to guide humans on how to use risk-based assessments of the future and the limitations of the information provided.
Predictive and Prognostic Maintenance touches nearly every area of the sustainment chain.
While the work necessary to implement it is substantial, it is essential to enabling the Army Aviation Enterprise Sustainment Strategy, and its benefits to the Army include reduced logistical footprint, improved operational availability and decreased life-cycle cost.
For more information on the Army Aviation Enterprise Sustainment Strategy and PPMx, please refer to the January issue of Army Aviation magazine or contact the authors at Andrew.Bellocchio@westpoint.edu or Danny.L.Parker20.ctr@army.mil.
LT. COL. ANDY BELLOCCHIO, Ph.D., is the director of the U.S. Military Academy at West Point Center for Innovation and Engineering, where he also teaches mechanical engineering. He previously taught aeronautics, thermodynamics, fluid mechanics, ballistics and design. Additionally, he has course-directed cadet capstone research in mechanical engineering and led interdisciplinary projects for the Academy at West Point. His active research is in aircraft reliability and structural health monitoring. He earned an M.S. and a Ph.D. in aerospace engineering from the Georgia Institute of Technology, and he holds a B.S. in mechanical engineering from West Point.
DANNY PARKER, Ph.D., has more than 15 years of control theory, optimization, machine learning and signal processing experience in the defense industry. He has been the principal investigator in various government research projects totaling over $20 million. One of his major contributions is in the application of dynamical systems principles to the development of formal design methodologies for structural health monitoring systems. In this field, he has adapted and implemented modern control theory techniques in removing environmental effects and estimation of amounts of damage. He has also done extensive work in target estimation, tracking and classification using acoustics. He received his Ph.D. in electrical engineering, a master’s degree in control theory and a bachelor’s in electrical engineering from Mississippi State University.