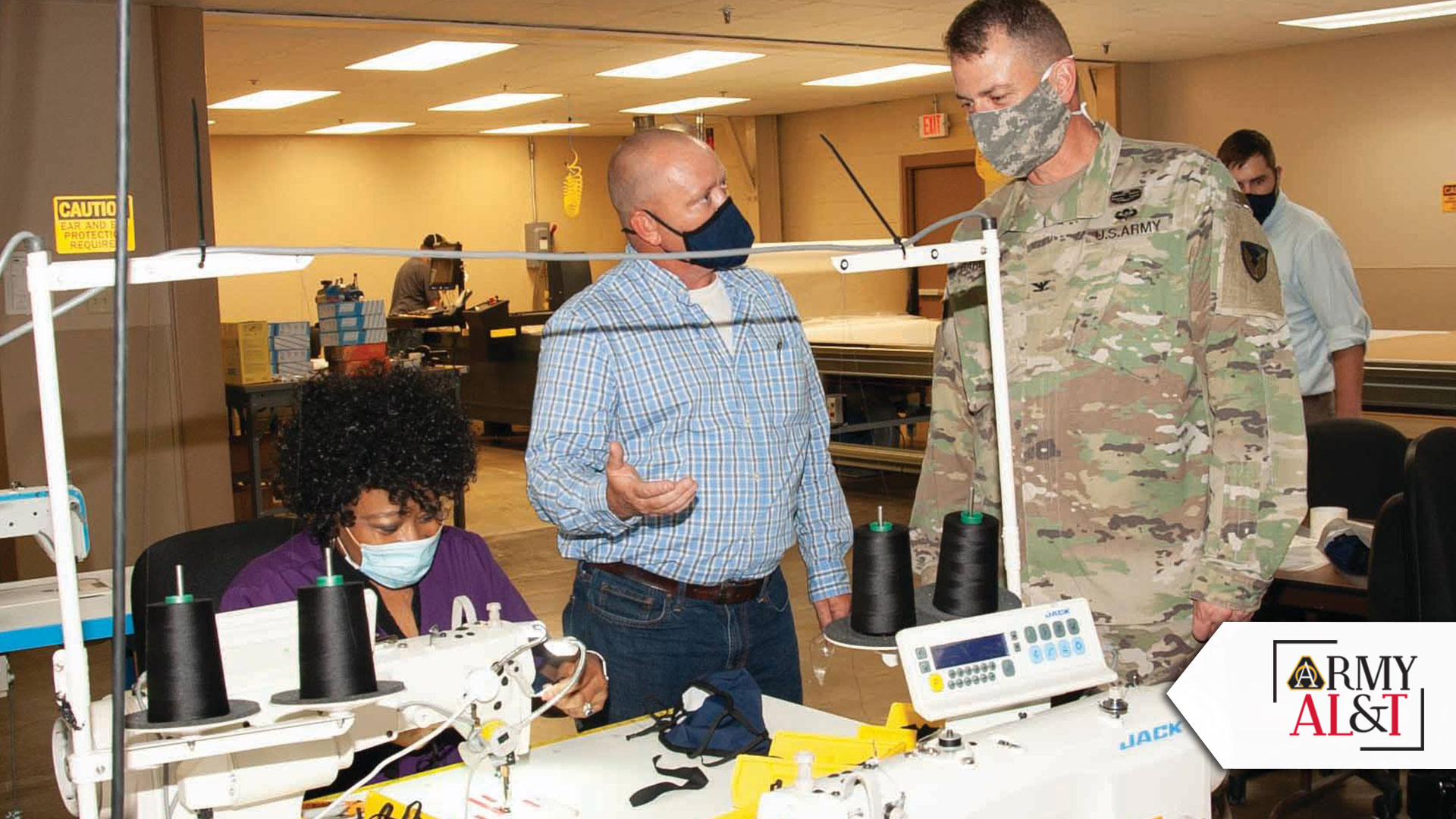
ON TOUR: Jason Fullen, center, project coordinator with Pine Bluff Arsenal’s textile production, gives a tour of sewing operations to Col. Gavin Gardner, JMC commander, during a visit in July. Dee Webb, left, sews protective face masks in support of COVID-19 requirements to protect the force. (Photo by Hugh Morgan, Pine Bluff Arsenal)
JMC produces masks and sanitizer in battle against COVID-19
by JoEtta I. Fisher
In January 2020, the World Health Organization and the U.S. secretary of health and human services declared public health emergencies in response to the emergence of the COVID-19 pandemic. The U.S. Centers for Disease Control and Prevention eventually issued a list of precautions, which included washing hands frequently, using hand sanitizer and wearing cloth masks to cover the nose and mouth. In April, the U.S. secretary of defense ordered all people on military property to wear such masks. This order raised immediate issues, with the United States facing a nationwide shortage of personal protective equipment (PPE).
Joint Munitions Command’s (JMC) solution was simple: task its government-owned, government-operated facilities with a new mission, making PPE. JMC installations immediately began manufacturing cloth masks and hand sanitizer for military personnel, civilian employees and contractors within JMC, Army Materiel Command and DOD, thereby reducing the need to acquire these PPE items from the already restricted open market.
“To lay the groundwork to execute the mission, headquarters JMC assembled a team with experience in all needed areas and worked with counterparts at Pine Bluff Arsenal [Arkansas], Crane Army Ammunition Activity [Indiana], and McAlester Army Ammunition Plant [Oklahoma],” explained Caleb Conley, lead industrial specialist in JMC’s government-owned, contractor-operated Directorate Facility Investments Division. “The installations rose to the occasion. They developed ways to meet regulatory requirements, and worked with headquarters JMC to develop a final plan.”
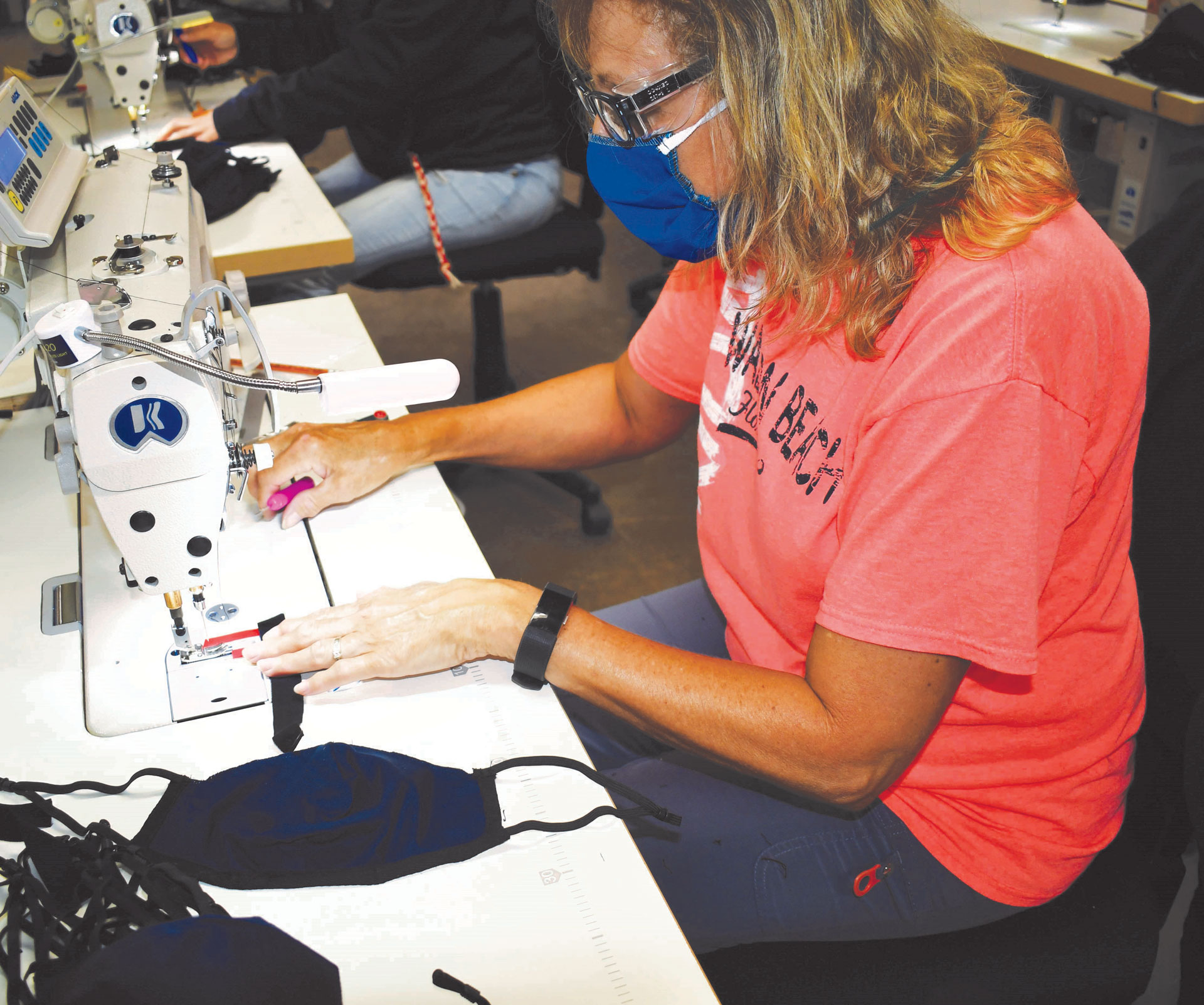
SEWING SAFELY: Pine Bluff Arsenal textile production operator Tyronza Hudson sews protective face masks in support of COVID-19 requirements to protect the force. (Photo by Rachel Selby, Pine Bluff Arsenal)
REMOTELY TOGETHER
Assembling the team with urgency during a pandemic presented unique difficulties. The team included eight members drawn from various departments at headquarters JMC, including facilities, finance, quality assurance and logistics. Because of the pandemic, the team worked remotely, coordinating with on-site personnel at Crane, Pine Bluff and McAlester to set up production lines, secure needed materials for each site and arrange shipment of the final products.
Within two days of the secretary of defense’s April order, Pine Bluff started designing, testing and producing face masks by adapting an existing mission that produced chemical patient protective wrap (to prevent exposure to contamination), integrated footwear (a protective sock system worn under normal combat footwear), and neck dams (a chemical and biological defense garment with impregnated carbon material). Using the equipment on hand, the Pine Bluff team rapidly acquired the needed material and started production.
“I am reminded daily that Pine Bluff has a superb team of employees that accomplishes its mission effectively,” said Col. Patrick Daulton, commander of Pine Bluff Arsenal. “This expertise was on display as team Pine Bluff produced cloth face coverings for the JMC enterprise to ensure employees were protected from COVID-19 pandemic. Pine Bluff still maintained the same level of dedication and support, while storing and producing quality ammunition for America’s joint warfighter.”
The resulting masks include a breathable, water-resistant outer layer, a filtered middle layer and a cotton-blend inner layer, providing a comfortable barrier to airborne particulates. Working remotely, an eight-person team at Pine Bluff processed more than 90 orders for 77,259 cloth face coverings. JMC filled these equipment orders with coordinating help from Army Materiel Command, Deputy Chief of Staff for Integration & Synchronization (AMC G3/4), and shipped to sites in the U.S. and overseas, providing personnel with the required protective equipment.
“When we say that people are our strongest asset, it doesn’t just apply to our day-to-day mission. It applies to times like these,” said Col. Stephen P. Dondero, commander of Crane Army Ammunition Activity. “Since the beginning of the coronavirus pandemic, our employees have adapted to make sure we still provide munitions to our men and women on the front lines.”
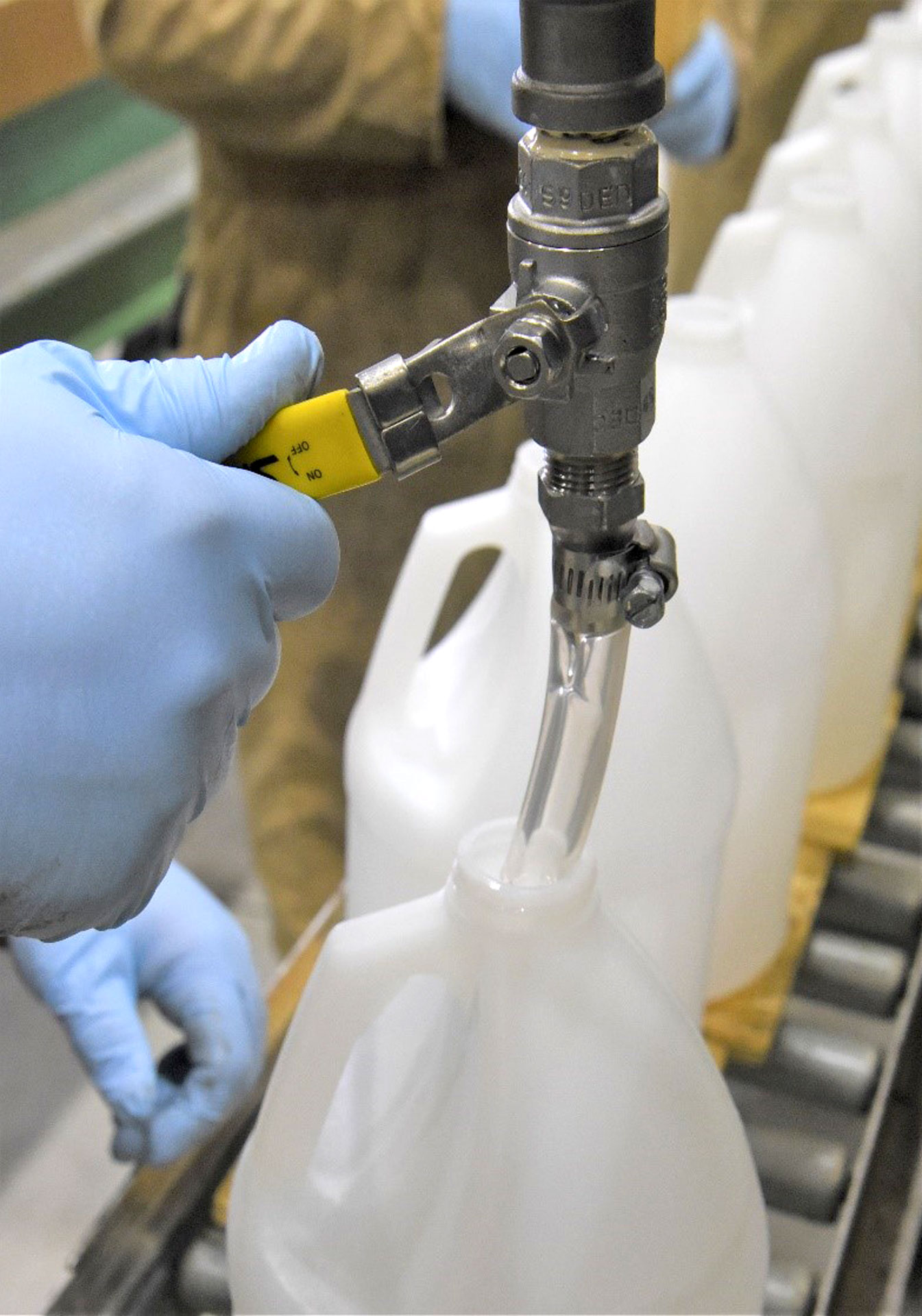
BOTTLE IT UP: Assembly workers pour hand sanitizer into plastic containers at McAlester Army Ammunition Plant during the packaging phase. After packaging, it is shipped to points of need in support of COVID-19 prevention. (Photo by Gideon Rogers, McAlester Army Ammunition Plant)
CLEAN AND SAFE
JMC also established a team of experts to handle production and transportation of hand sanitizer. McAlester and Crane led this production effort. JMC worked with the site program managers to acquire raw material supplies and coordinate customer orders for the hand sanitizer. Crane experts coordinated directly with private hand sanitizer companies to ensure the use of all baseline ingredients necessary for effective hand sanitizer—isopropyl alcohol, glycerin, hydrogen peroxide, and purified water. McAlester and Crane produced more than 2,820 gallons of hand sanitizer and completed more than 62 orders for JMC, AMC, the United States Military Academy at West Point and other Army units with urgent requirements.
“The dedicated and professional workforce that exists across the organic industrial base stepped up once again to answer the nation’s call,” said Col. Shane E. Upton, commander of McAlester Army Ammunition Plant. “From providing munitions to the joint warfighter while operating in in a COVID environment, to adapting rapidly to produce critical protective items for our nation in a time of need, our people continue to deliver.”
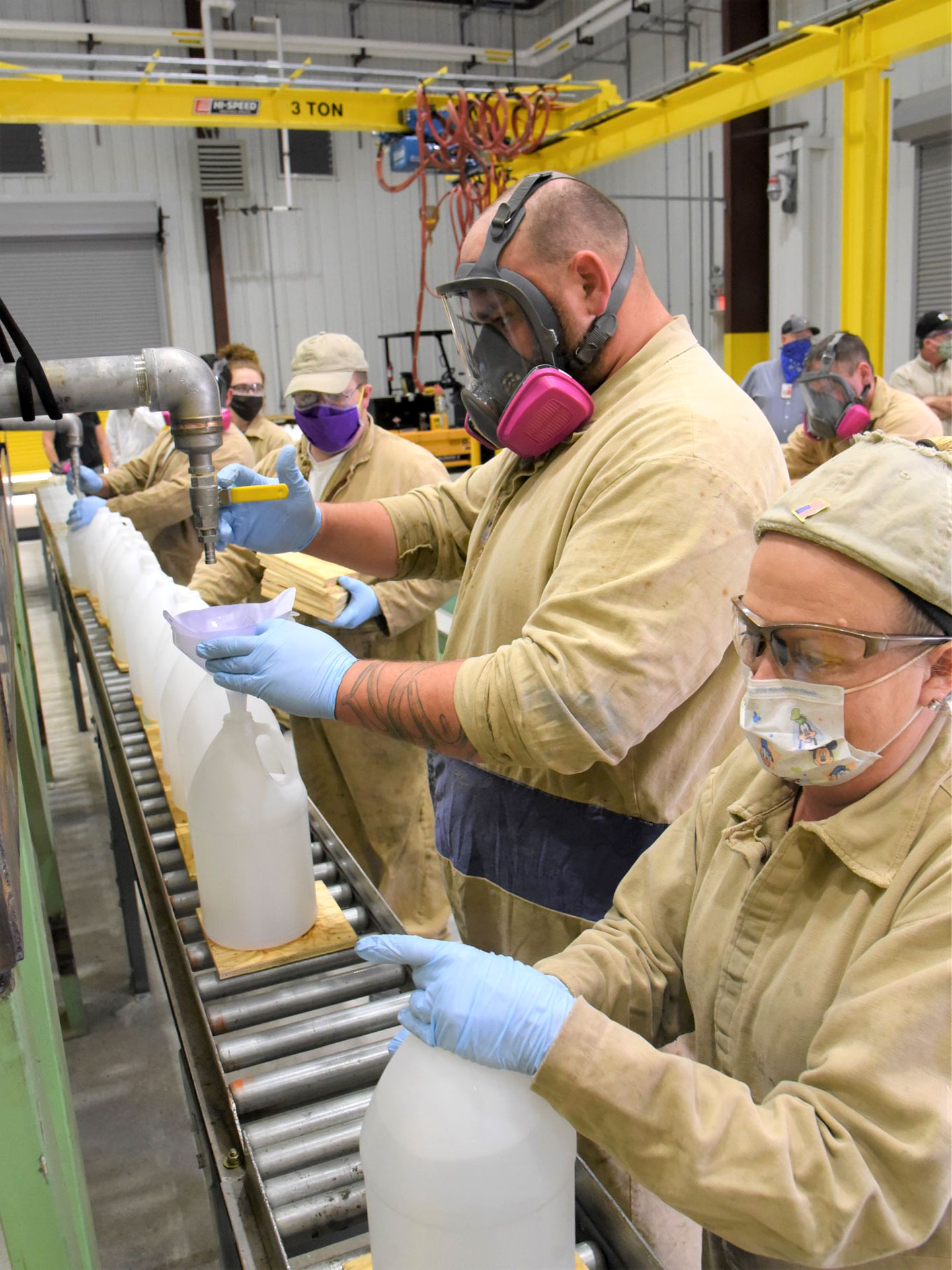
NEXT, PLEASE!: McAlester Army Ammunition Plant production workers use existing equipment to produce critically needed hand sanitizer for distribution to points of need in support of the COVID-19 response while continuing to meet ammunition readiness for the joint force. (Photo by Gideon Rogers, McAlester Army Ammunition Plant)
CONCLUSION
Thanks to the proactive and timely efforts of its expert teams, JMC is working to create safer work environments for its personnel and units throughout DOD, ensuring the continuation of mission-essential operations across the United States and around the world.
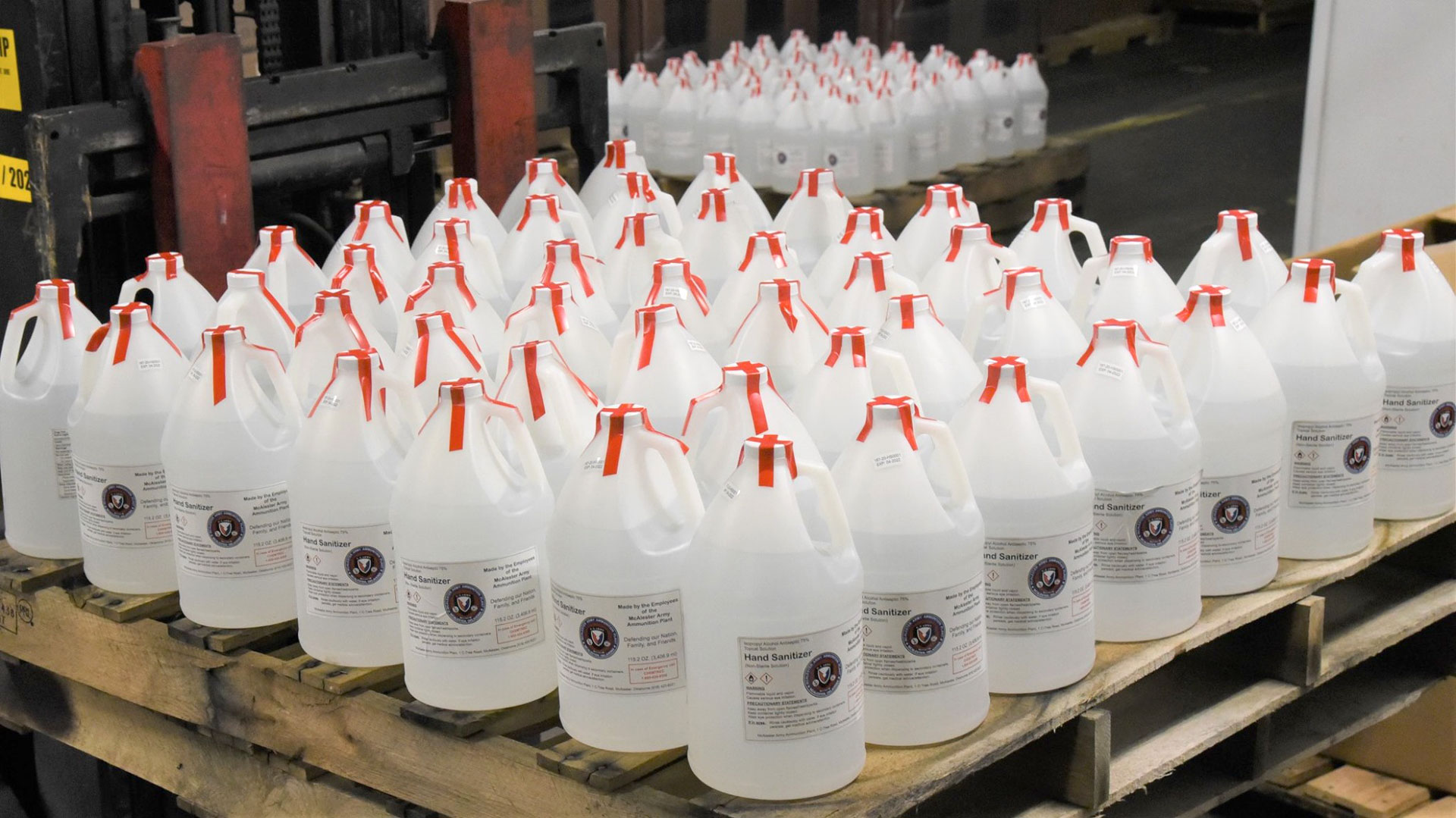
READY TO GO: Pallets of hand sanitizer produced at McAlester Army Ammunition Plant are staged for shipment and distribution to protect the joint force. (Photo by Gideon Rogers, McAlester Army Ammunition Plant)
JOETTA I. FISHER serves as the executive director for ammunition and the deputy to the commander for the Joint Munitions Command. Fisher is the organization’s senior civilian responsible for the command’s mission to distribute, store, demilitarize and produce ammunition for joint services and coalition partners to sustain worldwide readiness. She also serves as the Ammunition Management (CP-33) Career Program Representative for JMC. Before this position, Fisher served as the deputy for the Munitions and Logistics Readiness Center at JMC.
Read the full article in the Winter 2021 issue of Army AL&T magazine.
Subscribe to Army AL&T – the premier source of Army acquisition news and information.