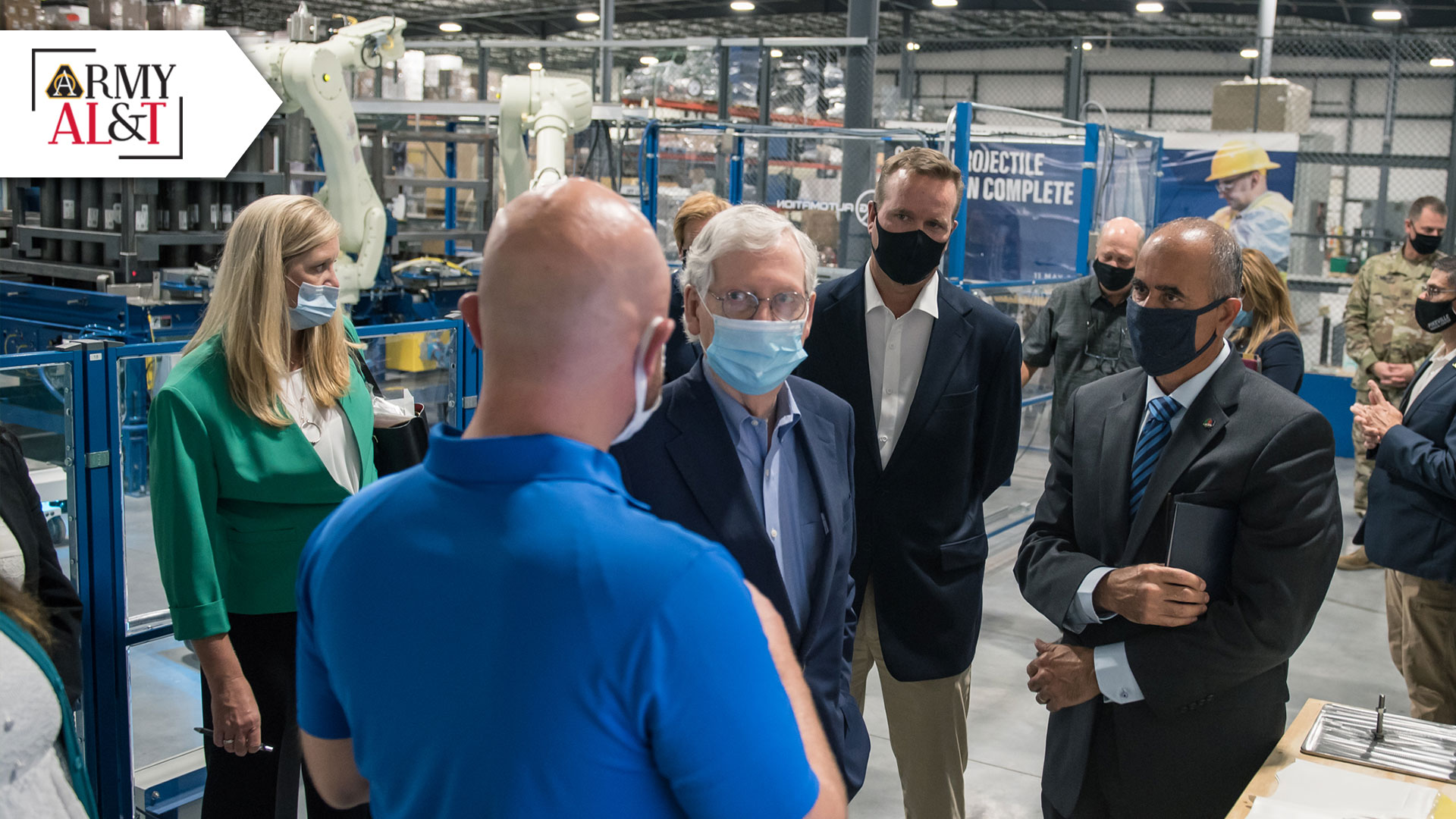
GUIDED TOUR: U.S. Sen. Mitch McConnell (R) and Michael Abaie, program executive officer for PEO ACWA, toured the training center for the chemical weapons processing facility at the Blue Grass Army Depot in Richmond, Kentucky, in fall 2021. (Photo courtesy of PEO ACWA)
PEO ACWA updates rocket handling systems to improve performance while destroying its deadliest chemical weapons.
by Timothy K. Garrett and Katherine B. DeWeese
The Program Executive Office for Assembled Chemical Weapons Alternatives (PEO ACWA) is charged with destroying the United States’ remaining chemical weapons stockpile, which is stored at U.S. Army installations in Colorado and Kentucky. A portion of the stockpile stored at the Blue Grass Army Depot in Kentucky consists of M55 rockets containing either VX or GB nerve agent, weapons that were slated to go through a designed, constructed and tested destruction process. But after recognizing numerous operational and maintenance challenges ahead, PEO ACWA pivoted to an other-transaction authority process to develop a new rocket processing system for the Blue Grass Chemical Agent-Destruction Pilot Plant.
The existing system included a number of moving components, sensors and waste streams causing maintenance concerns to become top of mind. Maintenance workers must wear the most stringent of personal protective equipment, which includes respirators and tethered air hoses.
The reactors used in the destruction process are a three-story climb, and with a two-hour maximum time period in the suit, the challenges of performing the anticipated frequent maintenance in a complex protective apparatus resulted in an upgrade of the original system to reduce those requirements.
“Our highest priority is the safety of the workforce,” said Michael Abaie, program executive officer for PEO ACWA. “When we learned of the challenges of operating and maintaining the existing system, we applied all the resources at hand to develop a system more conducive to meeting the identified needs and keeping our workers protected, while staying focused on meeting our Chemical Weapons Convention treaty destruction commitment of Sept. 30, 2023.”
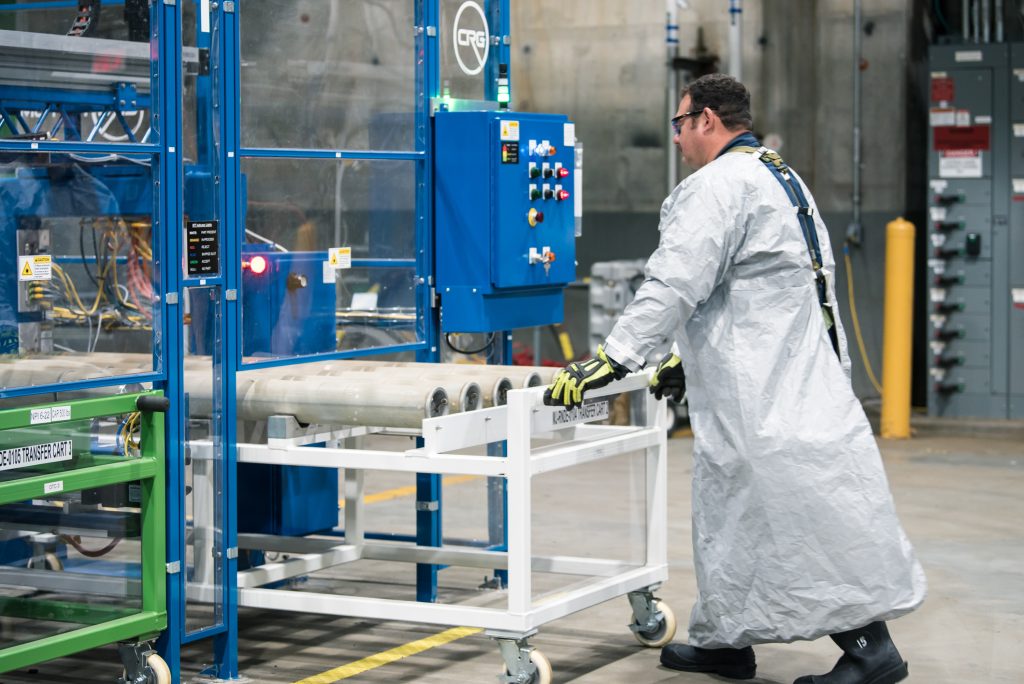
ROCKETS EN ROUTE: An operator pushes a tray of VX nerve-agent M55 rockets into the rocket non-destructive examination system in the Munitions Demilitarization Building at the Blue Grass Chemical Agent-Destruction Pilot Plant. This system allows operators to scan each rocket for potential leakage to avoid contamination of the processing equipment. (Photo courtesy of PEO ACWA)
THE PATH TO PROGRESS
PEO ACWA used the other-transaction authority process to design, fabricate and test a new automated system for the plant, allowing the program to use a more flexible acquisition approach while creating efficiencies and enhancing safety for those involved.
Defense contractor Amentum performed as the lead for the project. Amentum, one of the teaming partners of Bechtel Parsons Blue Grass, the systems contractor selected to design, construct, test, operate and ultimately close the pilot plant, brought in Swedish company DynaSafe, as well as Crown Packaging and CRG Automation, both of Louisville, Kentucky, to establish the new rocket processing system.
“CRG Automation developed a newly designed rocket warhead containerization system to dispose of rockets which measure six feet long and 4.4 inches in diameter,” said James DeSmet, CRG Automation president and CEO.
“Once the warhead containing chemical agent is separated from the rocket motor assembly and punched and drained of its agent, the all-robotic system places the warhead into a steel container with a lid that is sealed in place using a crimp station,” DeSmet said. “The drained chemical agent is then neutralized in a separate process.”
The automated system places the containers into packaging skids that hold 25 containers each. These skids are then monitored in an airlock to detect any surface contamination of chemical agent. If no agent is detected, the skids are moved to temporary storage on the depot to await the next step in the destruction process, a static detonation chamber, in which intense heat greater than 1,000 degrees Fahrenheit will destroy the warhead and overpacked container. The pilot plant will use two of these chambers to augment the main plant.
CRG Automation engineers used eight industrial robots, as well as six autonomous mobile robots, in the customized system, which is designed to improve speed and efficiency and reduce downtime.
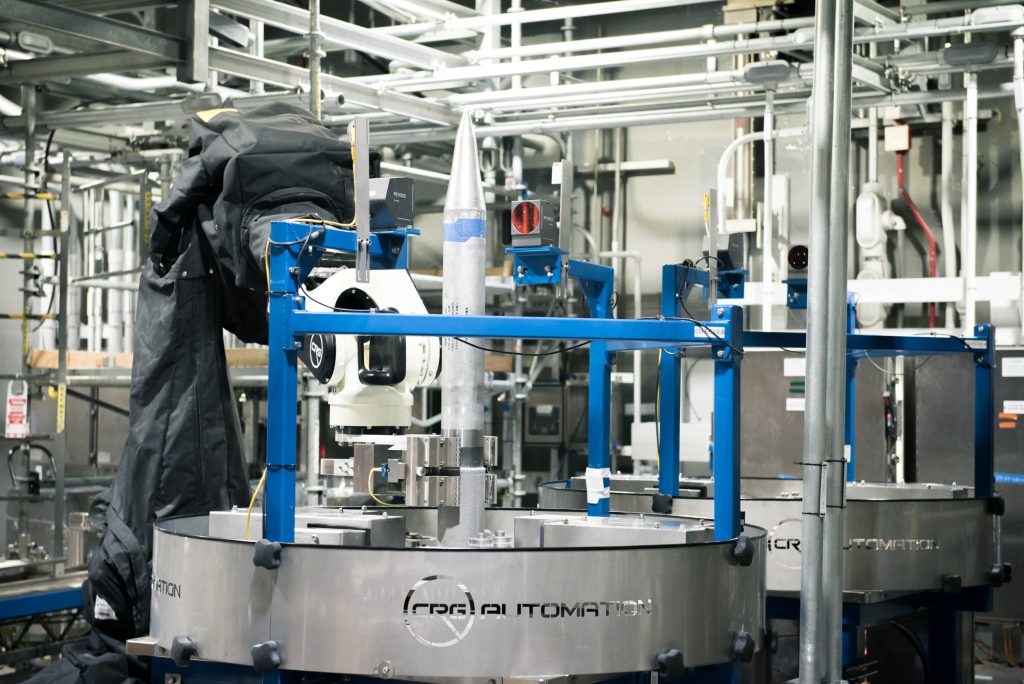
UP AND AWAY: A robot lifts a test rocket warhead from the Vertical Rocket Cutting Machine in the Munitions Demilitarization Building at the Blue Grass Chemical Agent-Destruction Pilot Plant. This equipment cuts the shipping and firing tube from around the rocket, then separates the warhead from the rocket motor. (Photo courtesy of PEO ACWA)
UNPLANNED DETOUR
With the revamped process complete, another problem arose. It became clear that a significant number of aging M55 rockets, which began production in the 1950s, had warped during storage, creating the possibility that their different dimensions would not fit properly in the system.
Ken Ankrom, a project manager for Amentum, estimated that up to 12,500 rockets may be warped, and each one that enters the line can conceivably stop the process, requiring workers to enter and resolve issues, potentially adding up to two days to the overall destruction timeline each time the line stops.
The former system required clamping the rocket assembly (a complete M55 rocket inside a fiberglass shipping and firing tube) in a horizontal orientation, rotating it, and creating a vertical cut to remove the warhead portion of the shipping and firing tube, and then separating the warhead from the motor. But vertical cuts meant any warped rockets that may have leaked inside their shipping and firing tubes would spread their chemical agent with the first cut, instead of keeping it neatly confined. An alternative method was developed by holding the rocket assembly fixed vertically and making a rotating horizontal cut, ensuring that any leaking chemical agent would gather in a containment device. Making these horizontal cuts also added more precision and accuracy, with the robots able to make cuts as small as one thousandth of an inch consistently, Ankrom said.
Should a leaking rocket be encountered following the shipping and firing tube cut, a new tilting reject station is used to take the leaking rocket and place it into an overpack container. The new design creates yet another efficiency and safety improvement, as the old system required workers to manually perform the overpack operation. The new technology also identifies whether the cut location of the rockets has warped and adjusts the system’s hydraulics to compensate and keeps the same pressure around the rocket while cutting.
Ankrom added that the new rocket-cutting robots also require far less maintenance than the earlier designs. “That keeps people out of the room, which is always safer.”
With the vertical rocket cutting design complete, the team turned to developing a system to help identify leaking rockets long before the robots make their first cut.
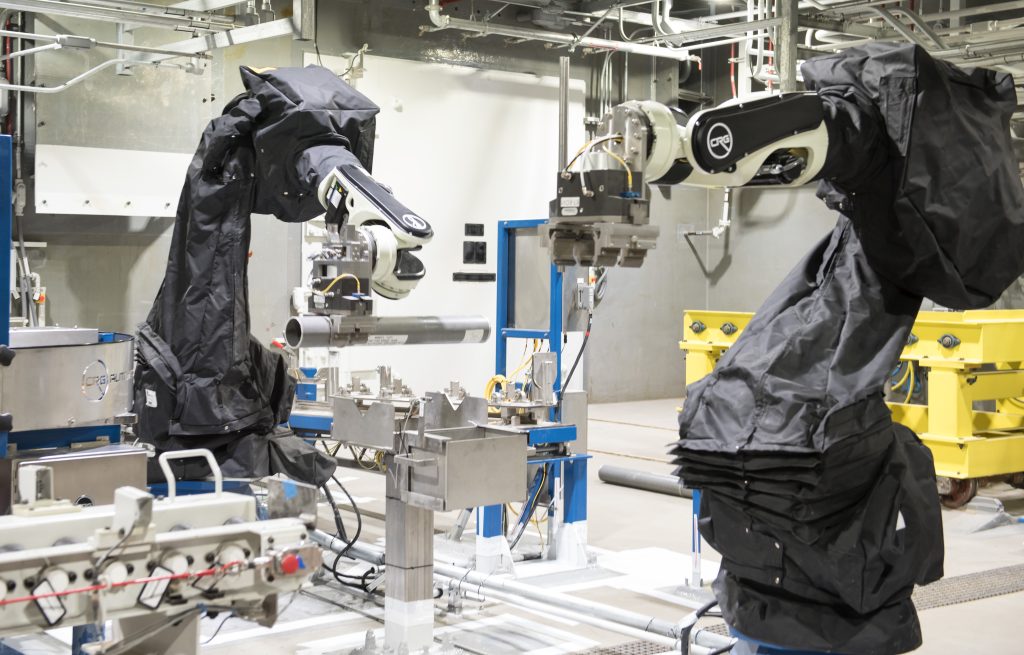
DIRTY WORK: These robots in the Munitions Demilitarization Building at the Blue Grass Chemical Agent-Destruction Pilot Plant transfer a piece of a test M55 rocket shipping and firing tube to place it onto a conveyor for packaging as waste. (Photo courtesy of PEO ACWA)
STOP THE LEAKS
“If we can avoid the leakers before they ever go to the vertical rocket cutting machine, then we’re never having downtime,” said Ankrom, noting that less downtime is essential to the goal of completing disposal of more than 70,000 rockets by late 2023.
Over the course of a few months, the team evaluated four technologies to improve the process, both in speed and accuracy. Among them was handheld leak-detection technology used in petrochemical plants, as well as iridium used in medical industries.
A process was devised to perform an X-ray scan of each rocket and focus on the areas where there is most likely to be leakage. CRG Automation’s engineers also crafted the ability to tilt each rocket up to 10 degrees for better clarity of the image.
Solving the challenges by designing and developing the new containerization system, vertical rocket cutting system, and the X-ray scan took approximately 18 months. With multiple actions required to process the rockets and incorporating two identical process lines, the system spans about nine rooms of the Munitions Demilitarization Building at the pilot plant. Multiple tight deadlines proved challenging, particularly given the ongoing coronavirus pandemic and its complications.
“This process allowed us to move quickly to keep us on track for the treaty destruction commitment of September 2023,” said Dr. Candace Coyle, site project manager for the pilot plant. “The team did a great job of bringing this all to fruition, pandemic notwithstanding.”
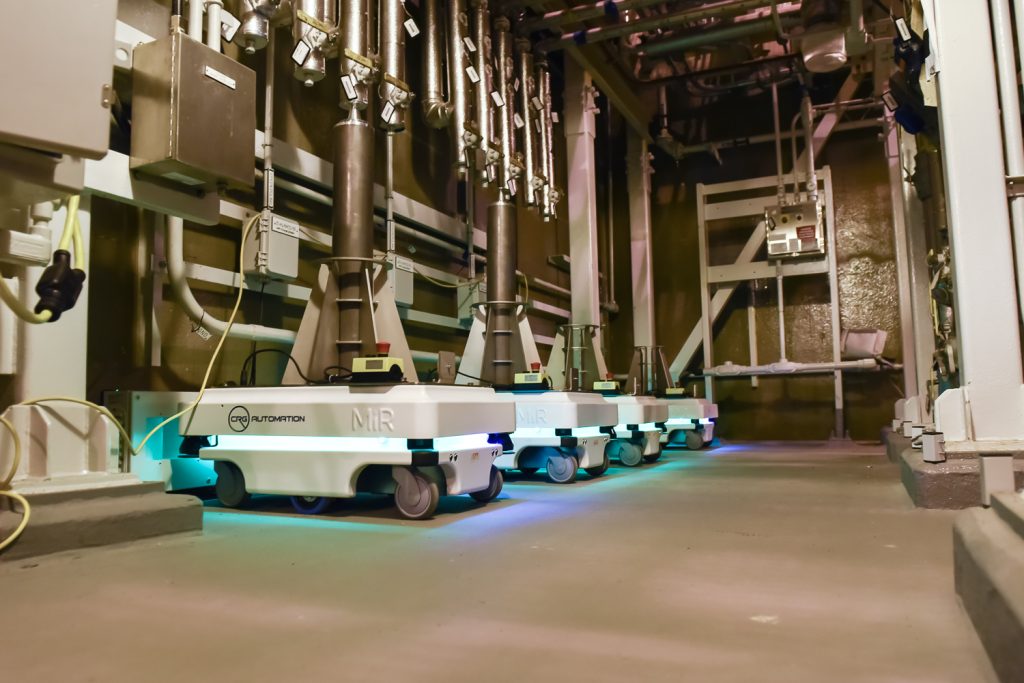
AUTONOMOUS GLOW-UP: Autonomous mobile robots line up in their charging stations in the Munitions Demilitarization Building at the Blue Grass Chemical Agent-Destruction Pilot Plant. These robots transfer empty and filled M55 rocket warhead canisters to and from different steps of the warhead destruction process. (Photo courtesy of PEO ACWA)
CONCLUSION
In July 2021, the first M55 rocket containing VX nerve agent was destroyed using the new system. The team is using this chemical weapons destruction campaign to destroy just under 18,000 VX rockets as an optimization period before starting the final campaign. Then, the team will destroy more than 50,000 rockets containing GB nerve agent—the largest portion of the Blue Grass stockpile—expected to begin in spring 2022.
“There would normally be a longer testing period known as systemization, before we start an agent campaign, but due to the short timeline and success in factory and site acceptance testing, we are able to safely use the VX rocket destruction campaign to optimize the equipment for the upcoming GB agent campaign,” Coyle said.
PEO ACWA and its contractor teams worked together to meet the challenges discovered in the rocket-destruction process, and the abilities of additional partnering companies using the other-transaction authority process allowed for quick design, fabrication and testing in a short period of time. Once the chemical weapons in Kentucky and Colorado are destroyed, destruction of the U.S. stockpile of chemical weapons will be complete.
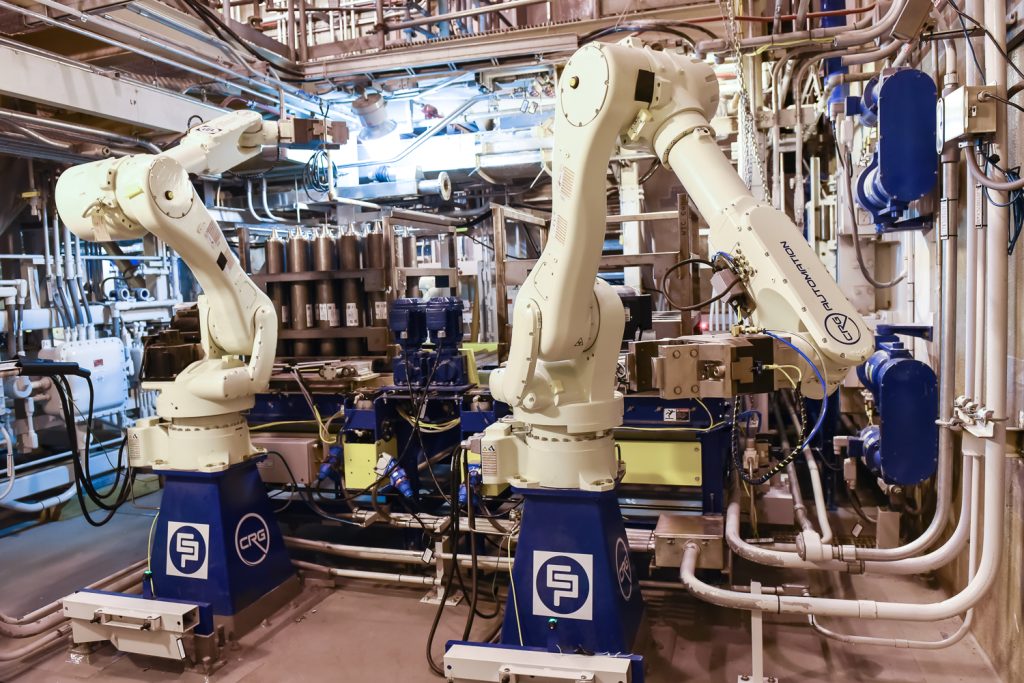
ROBOTS AT THE READY: Robots stand ready in the Munitions Demilitarization Building to load drained rocket warhead canisters into custom packaging skids for transport to temporary storage before their destruction in one of the static detonation chamber units at the Blue Grass Chemical Agent-Destruction Pilot Plant. (Photo courtesy of PEO ACWA)
For more information, go to the PEO ACWA website: https://www.peoacwa.army.mil/.
TIMOTHY K. GARRETT is director of field operations for PEO ACWA. He is a licensed professional engineer and holds an M.S. in environmental engineering and a B.S. in chemical engineering, both from the University of Alabama. A member of the Army Acquisition Corps, he has 35 years of expertise in chemical and environmental engineering related to chemical demilitarization.
KATHERINE B. DEWEESE is the public affairs officer for PEO ACWA. She holds a B.S. in advertising from the University of Maryland and is a Distinguished Honor Graduate of the Defense Information School. She has more than 30 years of experience in Army public affairs, primarily with chemical defense programs and demilitarization.