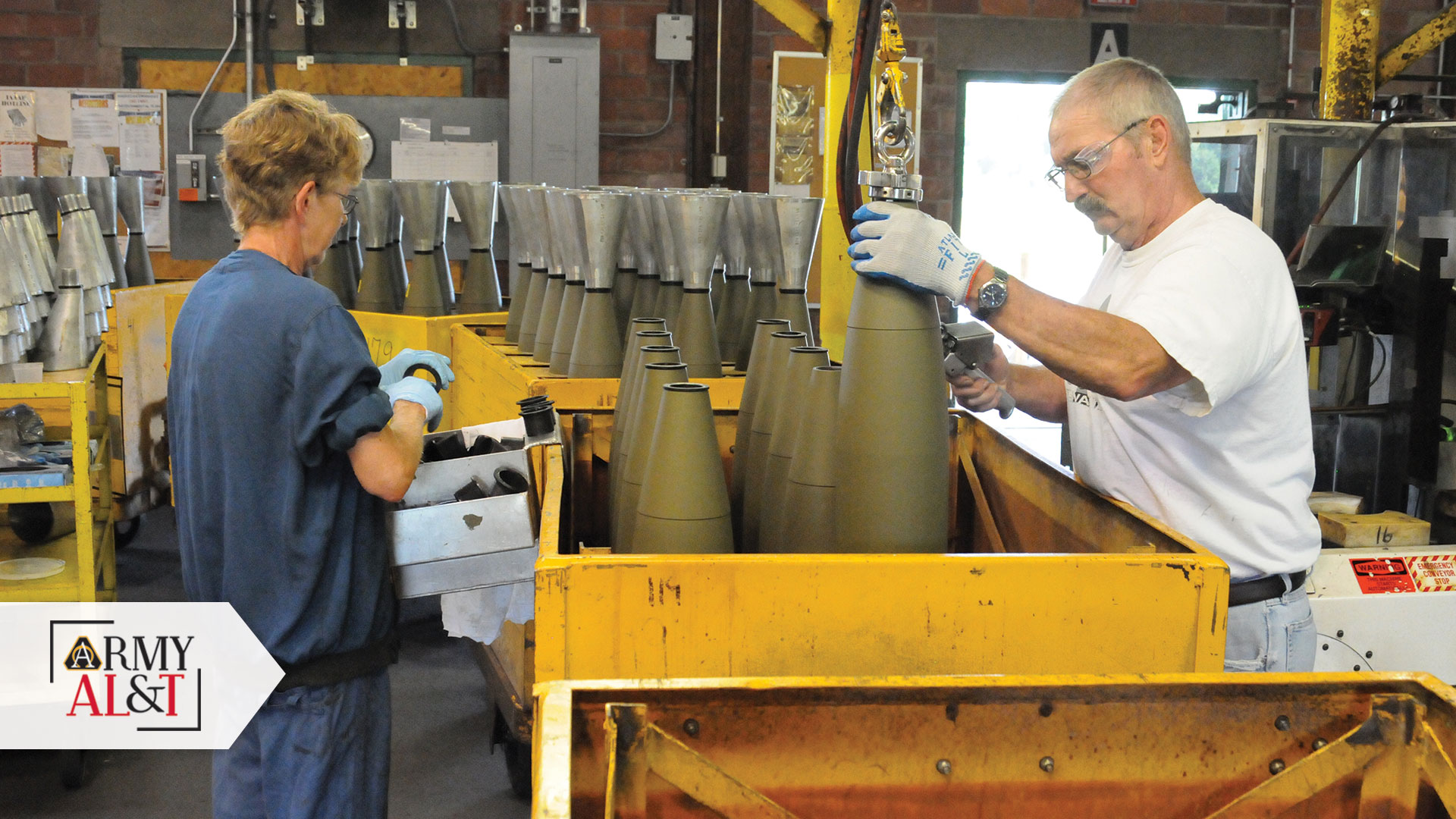
BUILT FOR SURGE: Contractor employees at Iowa Army Ammunition Plant prepare 155 mm artillery rounds to be filled as a part of the load, assemble and pack operation. The plant is an example of surge production, a key consideration in JMC’s risk model. The Iowa plant began production in 1941 to supply troops in World War II, then stopped in 1945 before resuming ammunition manufacturing in 1949, with a surge in 1950 in response to the Korean conflict. (Photo by JMC)
JMC develops risk model to address vulnerabilities in munitions supply chain.
by Col. Gavin J. Gardner
Joint warfighters around the world depend upon a steady supply of ammunition. Understanding and maintaining the ammunition supply chain is especially complicated because of the wide array of components needed to produce bullets, bombs and other munitions. The U.S. Army Joint Munitions Command (JMC), in conjunction with governmental and private partners, is working aggressively to identify and mitigate vulnerabilities in the supply chain. To this end, JMC has developed a risk model, which, when incorporated with other data analysis tools, will ensure the maintenance of both ongoing production and surge capabilities, in service to the joint warfighter.
JMC’s risk model is a more holistic way to view the ammunition supply chain and risk, based on information drawn from various data analysis tools. The risk model synthesizes existing supply chain information and includes metrics that highlight problem areas and measure progress. Effective use of this risk model requires the collection of information from a variety of sources.
An important source of information is the Industrial Base Assessment Tool, a web-based tool that provides supply chain management and decision-support information to enhance acquisition planning and industrial base preparedness. This tool documents the production capabilities, capacities, schedules, deficiencies and metrics of the ammunition supply chain. In particular, the database contains information for more than 1,300 components and 1,200 manufactured products used to produce ammunition. More than 300 U.S. government, and domestic and foreign commercial producers supply this information.
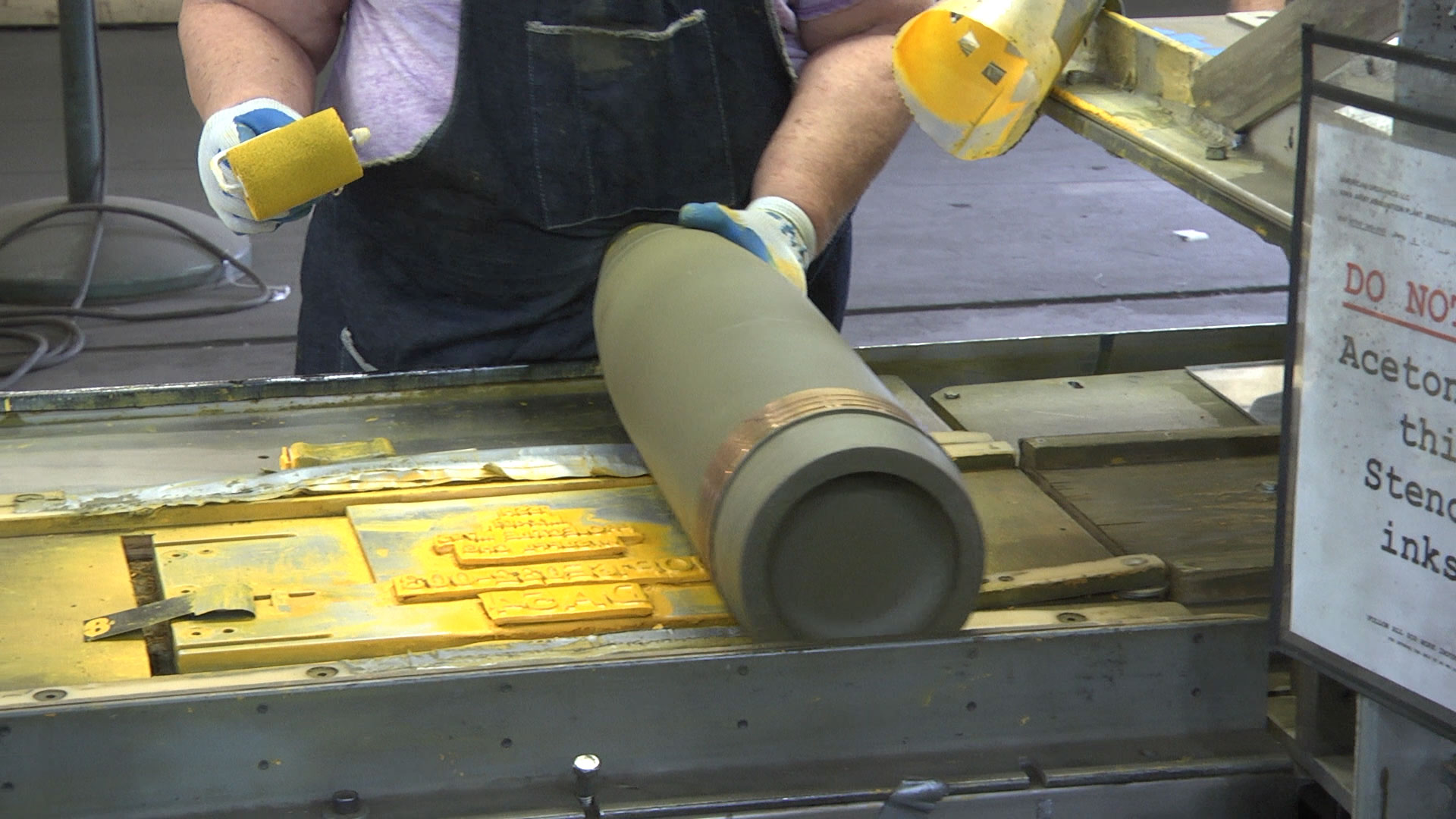
LABEL AND LOAD: A contractor employee at Iowa Army Ammunition Plant labels a 155 mm artillery round as part of the load, assemble and pack operation. (Photo by Dori Whipple, JMC)
IDENTIFYING THE RISKS
Maintaining a consistent, unbroken chain of munitions requires accurate, up-to-date knowledge of sources of supply, production capabilities and the available stockpile. Acquiring this information requires close partnerships with the organic and commercial industrial base, as well as allied partners around the globe, each working to understand its capabilities and vulnerabilities at every step of the process. Using such information is critical for JMC to successfully manage the munitions enterprise while focusing particularly on supply issues, system resiliency and modernization planning.
The risk model helps analysts identify potential weak points that could develop into threats. Analysts then consider “what-if” scenarios to highlight potential disruptions to the industrial base. This gives planners a better picture of challenges within the ammunition industrial base. Threats to the supply chain come in a variety of forms, including minimal availability of component materials, limited and evolving production capabilities, human interference and natural disasters.
Assembling and evaluating information about component materials is further complicated by the number of components that can go into a single item. Bomb, small-caliber and large-caliber ammunition currently rely on multiple components and chemicals from outside the United States. For example, the 30 mm ammunition, which is a relatively simple round by ammo standards, has a bill of materials that includes 35 unique components, made by 23 producers across 15 states and three foreign countries.
Depending on sources from outside the United States presents obvious security concerns. In addition to the standard transportation issues involved with importing components, an adversary might choose to interfere with the supply of materials or cut off the source completely. Limited availability of components would likely create further disruptions in the production stage.
JMC and its enterprise partners are investigating alternate sources of supply in an effort to mitigate risks to the supply chain and assess future workload needs. Ensuring ammunition readiness requires partnership between government and industry to address weaknesses in the ammunition supply chain. Potential solutions to address these concerns include developing a stockpile of components large enough to make up for potential shortfalls, or finding alternate sources for items that may be in short supply.
To this end, it is vital that contractors conduct full assessments of their industrial capabilities and their sources of supply. For example, there may be two manufacturers producing the same item, but if both manufacturers use raw materials that come from a single source, an upstream disruption to the supply of that component would impact both producers. Industrial partners must be aware of such vulnerabilities.
Likewise, where multiple layers of industry are involved, a primary contractor cannot assume that its subcontractors have multiple sources of supply, or that those supplies come only from the United States or its allies. Without comprehensive top-to-bottom knowledge of every level of the supply chain, potential vulnerabilities may not be evident.
Limited production capabilities can also negatively impact the supply chain. For example, if the production of an item relies on a single production facility, any disruption to production at that facility could create a critical break in the supply chain.
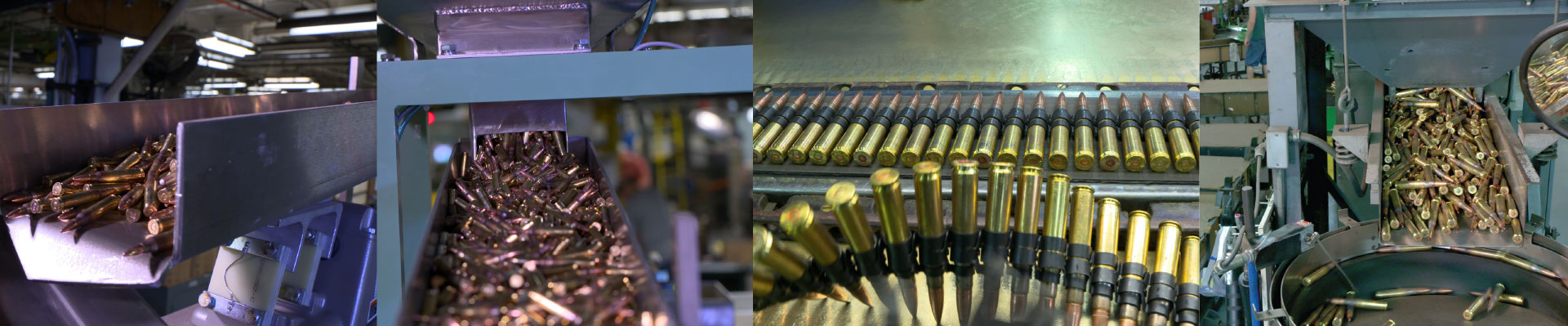
CHUTE FOR SHOOT: Lake City Army Ammunition Plant in Missouri produces 7.62 mm small-caliber munitions for the warfighter in support of global operations. Established in 1940, it is government-owned and contractor-operated. (Photo by JMC)
KEEP A BACKUP
Advancements in technology can create additional problems. Today’s munitions use unique metal and polymer formulations machined with computerized equipment to improve functionality. Some of the greatest technology breakthroughs have been in electronics. For example, where there was once a mechanical fuze, there is now a fuze guidance system, requiring even more unique and technical components. Upgrades like improved circuitry not only add complexity in the production phase, they often require more specialized materials. All of this adds to supply chain requirements.
Counters to vulnerabilities in the manufacturing stage include maintaining redundant production facilities and, if necessary, modernizing existing facilities. It is critical that JMC and its partners move toward further modernization efforts.
Natural disasters can also have a devastating impact on supply lines. While these events are largely unpredictable, careful analysis using the risk model can help JMC prepare for such problems. Foresight, combined with flexibility when disasters do occur, can mitigate the impact. The emergence of the COVID-19 pandemic is an important case in point. Before the outbreak, JMC had already worked to develop an in-depth awareness of its supply chain. As global shutdowns occurred, JMC subject matter experts quickly worked with suppliers to mitigate risks to the supply chain.
Along with the ability to source components and produce materiel, a major concern for the ammunition industrial base is the ability to meet an uptick in requirements. There are several issues to consider when mitigating threats that work against a need for increased production. After-action reports from previous incidents when ammunition needs greatly increased provide leaders with lessons learned, allowing decision-makers to better understand past needs. Current operational plans and “what-if” scenarios then enable leaders to anticipate future needs. It is critical for JMC and its partners to use such tools in order to accurately assess potential demand fluctuations, surge production given current equipment, the ability to hire workers to cover surge requirements, and the length of time required from time of contract award to time of delivery.
At each stage, contractors must be aware of their abilities and relate them to the current situation so that JMC and its partners can collaboratively anticipate and mitigate potential shortfalls. It is vital that both commercial and organic production facilities are communicating and are responsive to industrial-base inquiries regarding production-line layouts, shared production equipment and associated concerns. This will ensure that assessments use accurate data and correctly model the ammunition-production industrial base to enable the government to properly see itself.
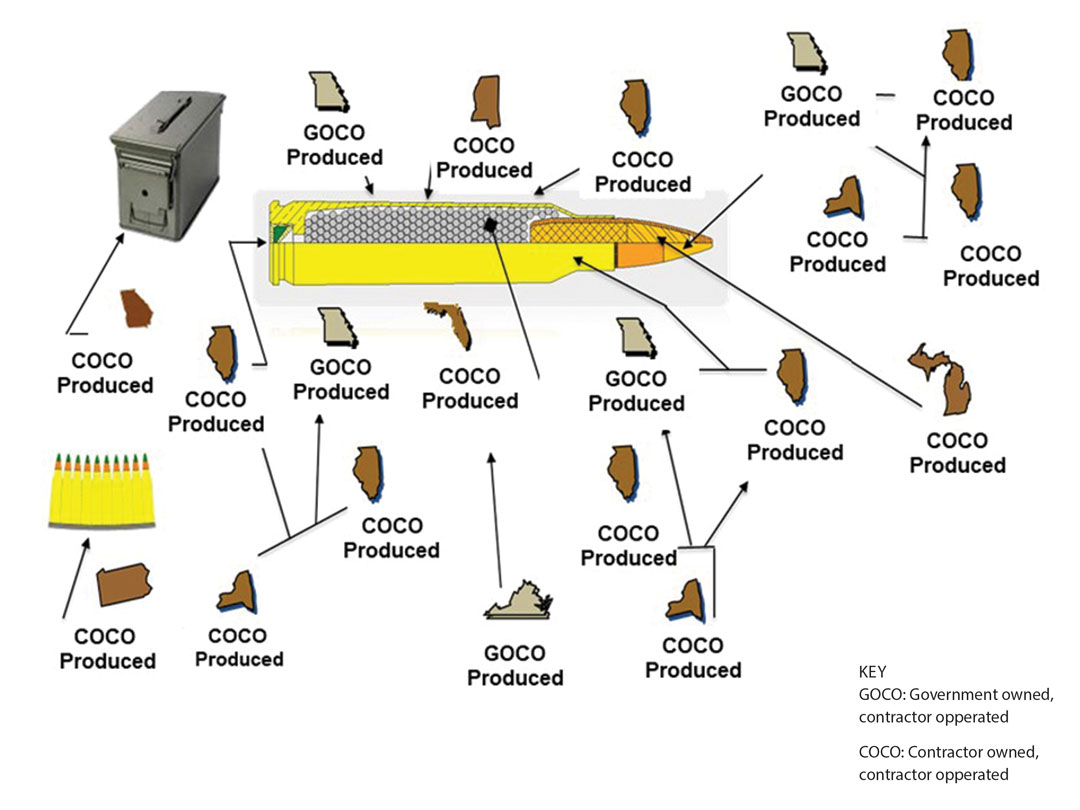
SUPPLY STRATEGY: Of the multiple parts that go into the cartridge (CTG) of the 5.56 mm M855 Enhanced Performance Round (EPR), the vast majority are produced at more than one facility in the Army industrial base. The M855 EPR ammunition box is an item produced at only one facility. The graphic shows the type of facility—government-owned and contractor-operated or contractor-owned and -operated—and the state where it is located. (Graphic by JMC)
CONCLUSION
Given the importance of safeguarding the munitions supply line for the joint warfighter, JMC maintains a stockpile of ammunition for use in the event of war or surge needs. Collectively, stockpiles of components and complete items ensure preparedness domestically and at global strategic theater locations. JMC continuously weighs its detailed knowledge of industrial base capabilities against the costs of establishing and sustaining strategic stockpiles of ammunition and components to ensure munitions readiness.
The successful delivery of munitions to the joint warfighter depends on cooperation among all partners within the ammunition industrial base. This partnership, in turn, requires effective communication not just between industry and government, but between industry and industry, ensuring that government, contractors and subcontractors understand one another’s vulnerabilities and capabilities as well as their own. Through active assessment and open communication, JMC and its partners can reduce reliance on foreign sources and mitigate potential threats to the munitions supply chain, meeting the needs of the joint warfighter by consistently providing lethality that wins.
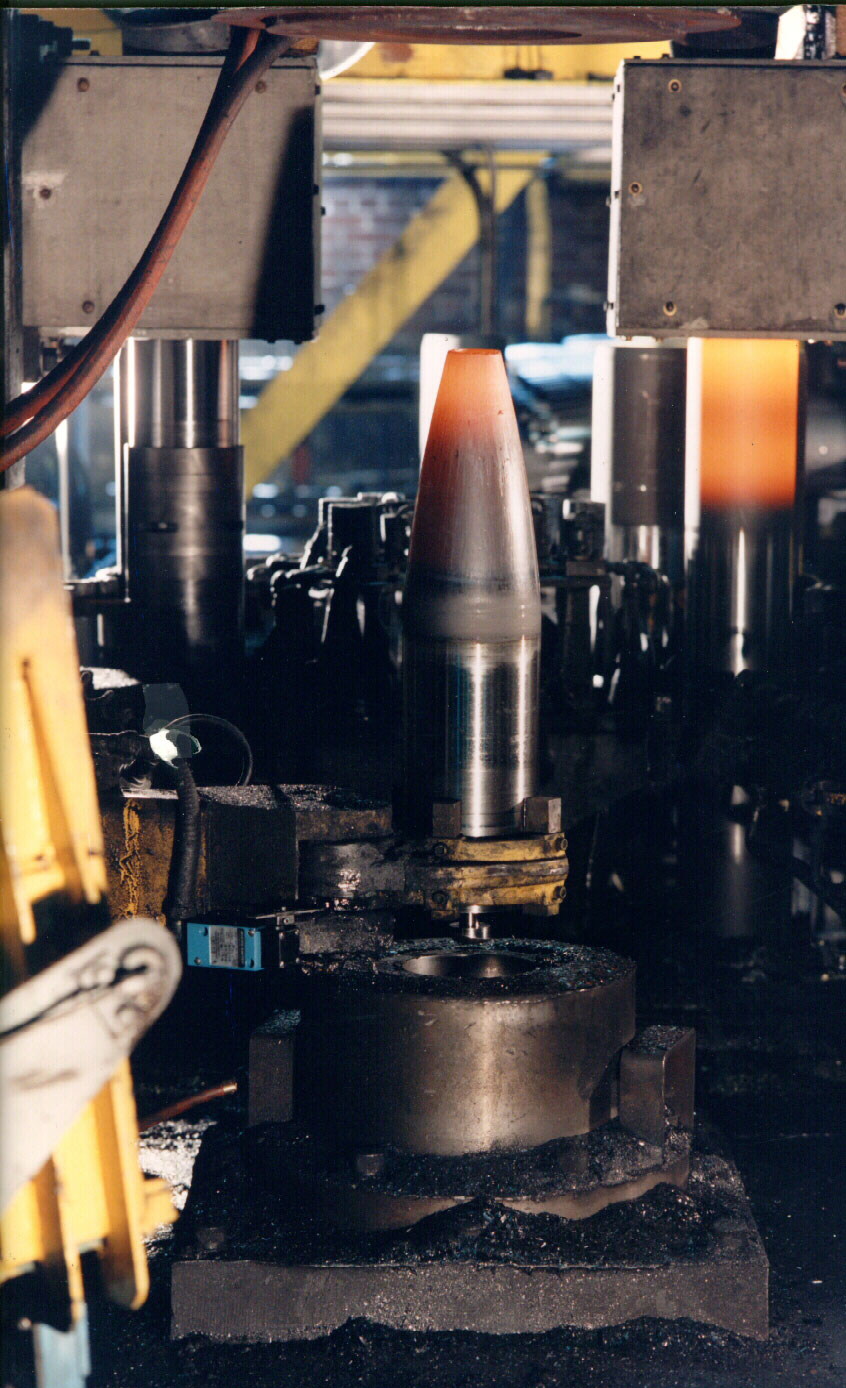
HOT OFF THE ASSEMBLY LINE: In the nosing process, shown here for large-caliber metal projectiles at Scranton Army Ammunition Plant in Pennsylvania, the open end of the cylindrical part is formed into the round tapered ogive, the curve of the forward section. The parts are glowing red from the forming process. (Photo by Dori Whipple, JMC)
For more information, visit www.jmc.army.mil
COL. GAVIN J. GARDNER assumed the duties of commander of the Joint Munitions Command and Joint Munitions and Lethality Life Cycle Management Command, headquartered at Rock Island Arsenal, Illinois, on June 11. He holds an M.S. in logistics management from the Florida Institute of Technology, M.A. in national security and strategic studies from the U.S. Naval War College and an M.S. in national resource strategy from the Eisenhower School for National Security. He earned a three-year Army ROTC scholarship and is a Distinguished Military Graduate from the University of Georgia with a Bachelor of Business Administration in production and operations management.
Read the full article in the Fall 2020 issue of Army AL&T magazine.
Subscribe to Army AL&T News – the premier online news source for the Army Acquisition Workforce. Subscribe