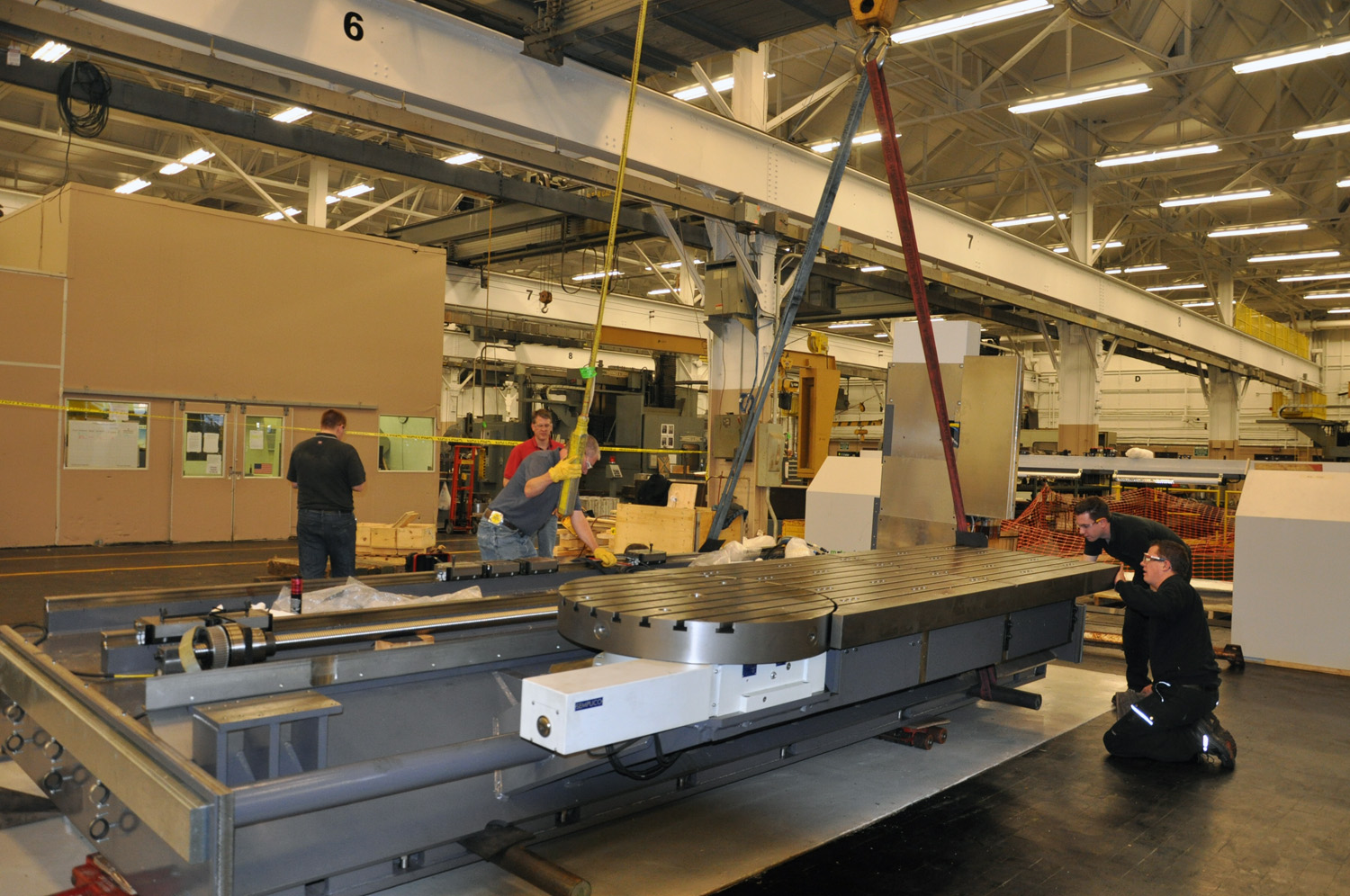
As our country struggles with a worldwide recession, a large-caliber weapon manufacturing facility on a small parcel of land in upstate New York is dealing with its own challenges to survive.
The economic survival of the nearly 200-year-old U.S. Army Watervliet Arsenal in Watervliet, NY, hinges on its continuing to do what has made America great—manufacturing high-quality products that last. Nevertheless, the decline of manufacturing in the United States has been well documented. In recent testimony before Congress, Scott N. Paul, Executive Director of the Alliance for American Manufacturing, said that well over 5 million American manufacturing jobs have been eliminated since 2000, and more than 50,000 manufacturing facilities have closed over the past 10 years.
[raw][image align=”left” caption=”Once the old machinery has been removed and floor space has been reconfigured, new machinery can be brought in. Here, the foundation for a new $2.3 million, five-axis milling machine is inspected. (U.S. Army photo by John Snyder.)” linkto=”/web/wp-content/uploads/DSC_1349_2.jpg” linktype=”image”]”/web/wp-content/uploads/DSC_1349_2.jpg” height=”167″width=”246″[/image][/raw]
The Fight for Survival
The fact that the arsenal is government-owned and –operated, and is the only large-caliber weapon manufacturer in the country, does not exempt it from having to fight for its survival. Using strategy on the level of a world championship chess match, the Watervliet Arsenal is transforming under-used manufacturing space into state-of-the-art capability. Machine by machine, square foot by square foot, the arsenal is methodically opening up floor space for advanced machining through the Capital Improvement Program (CIP). With this program, the arsenal will significantly improve its capability and capacity to manufacture legacy and future weapon systems.
According to Bill Dingmon, Industrial Operations Foreman at the arsenal, “There is more than 2 million square feet of floor space at the arsenal, but only about half of that is available for manufacturing.” The rest of the space is for support operations such as supply, procurement, and maintenance.
Because the Army cannot build more buildings at the arsenal to improve its manufacturing capability, it must transform under-used space, while not hampering existing operations, Dingmon said.
Retrofit Challenges
“The retrofit process, from concept to operational testing of new machines, can take years if we allowed it to,” Dingmon said. “Because we have to run the arsenal like a business, we do not have the luxury of time, and so we quickly move through the process.”
[quote align=”right”]Each time we replace a piece of equipment, it takes the integration and synergy of the entire arsenal to ensure success.[/quote]Dingmon’s “battle buddy” in this retrofit process is Bryan Myers, Industrial Engineer Technician. Myers said that identifying space and then finding the right machinery to not only improve the arsenal’s manufacturing capability but also to fit into the cleared space is a matter of both science and art.
To remove heavy industrial equipment, some of which dates to World War II, is not as easy as ordering the delivery of a new appliance and having the old one hauled away.
“The science is identifying a piece of equipment that no longer provides us much utility and then finding a modern machine that will fit into the same space of the old machine while adding capability,” Myers said. “You have got to keep in mind that newer machines actually take up more space because of requirements for such things as computer controls and cooling assemblies.”
Dingmon and Myers used as an example the recent arrival of two new machines in Building 20, a major components structure built during World War II.
Once Building 20’s equipment replacement plan was approved by the Director of Industrial Operations and Production, it made its way through a maze of contracting, maintenance, and supply personnel, Myers said.
This is where the “art” of retrofitting a capability comes in.
[raw][image align=”right” caption=”After delivery of new machinery, it can take months of testing before the machine is ready for production. Here, a Hankook lathe, which came from South Korea, is tested before machinists receive operator training. (U.S. Army photo by John Snyder.) ” linkto=”/web/wp-content/uploads/DSC_5037_2.jpg” linktype=”image”]”/web/wp-content/uploads/DSC_5037_2.jpg” height=”167″width=”246″[/image][/raw]
“Each time we replace a piece of equipment, it takes the integration and synergy of the entire arsenal to ensure success,” Myers explained.
Beginning in 2008, Dingmon and Myers began coordinating the purchase of two traveling column machines from GBI Cincinnati Inc.
What that means is that Building 20 now has two state-of-the-art precision engineering machines with swivel heads that can do horizontal and vertical machining on a fixed, long-bed table. In essence, instead of stopping the machine to move the head from one angle to another for boring or milling, the computer-controlled swivel head assembly moves automatically without stopping work.
The cost of these machines, more than $2.3 million together, is daunting, but this is just one of many CIP projects the arsenal has recently funded. In the past three fiscal years, the arsenal has obligated more than $40 million to capital improvements, and its leadership plans to spend nearly $10 million more this fiscal year to further improve manufacturing capability.
And so, the arsenal workforce is methodically building capability and capacity to support not only today’s warfighters but also the next generation of warfighters with the highest-quality tank guns, large-caliber cannons, and mortars.
[list type=”arrow”]
- JOHN SNYDER is the U.S. Army Watervliet Arsenal Public Affairs Officer. He is a retired Army colonel who served in the field artillery and public affairs fields. Snyder holds a B.S. in market and management from Siena College and an M.A. in journalism from Marshall University. He is a graduate of the U.S. Army War College and the DOD Joint Senior Public Affairs Officers Course.