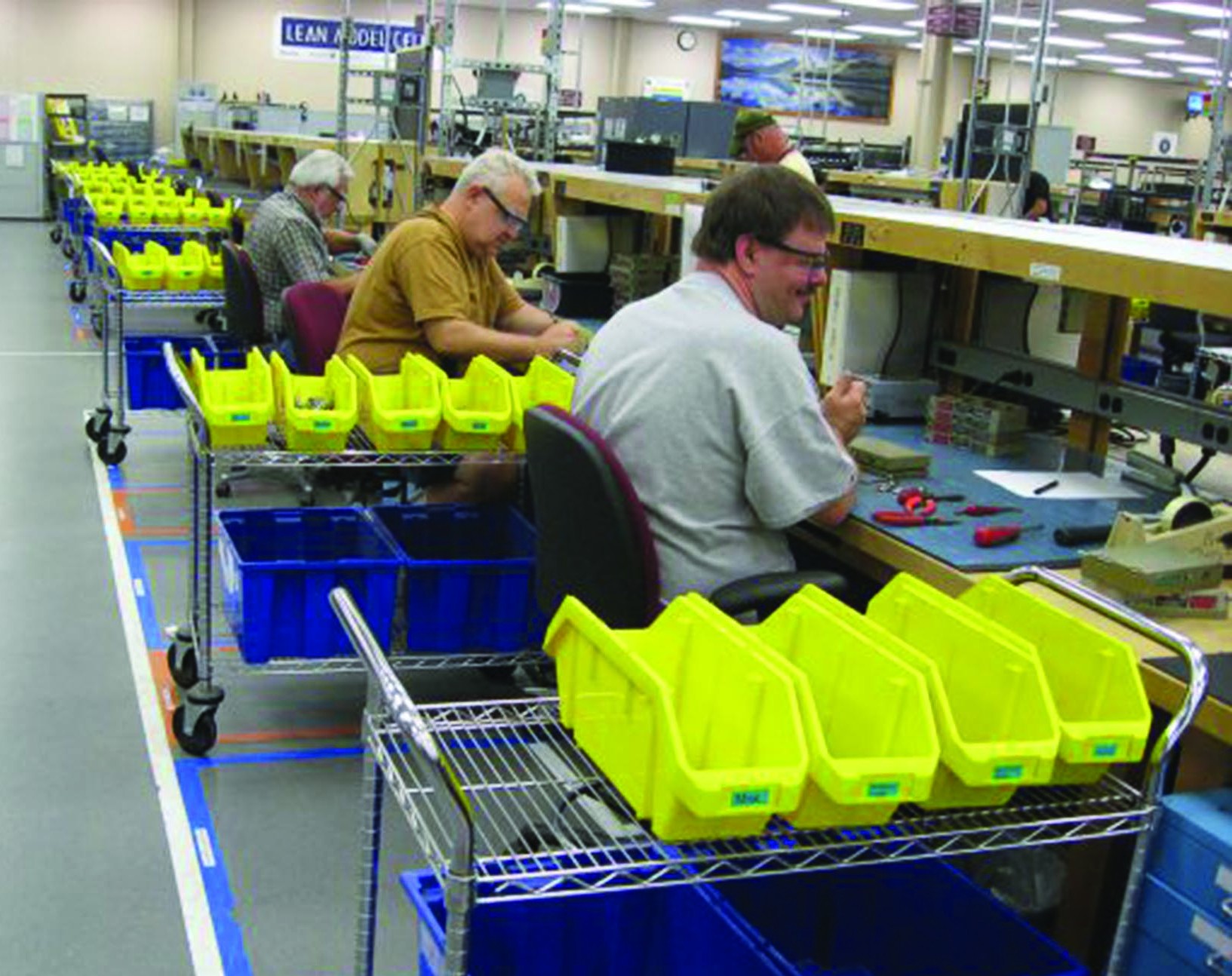
Tobyhanna workforce supports the current and future Army network, one idea at a time
By Mr. Gary P. Martin, MG Daniel P. Hughes and COL Gerhard P.R. Schröter
When you’re at war, sustainment can be one of the last things on your mind. The Army acquisition community’s top priority for the last 13 years was to get equipment out the door rapidly and into Soldiers’ hands. If that required the occasional but necessary increased cost for repair or field support to ensure that troops had what they needed when they needed it, that was something to sort out later.
Later has arrived—and with it, an opportunity to be more strategic about how we execute sustainment for current and future systems. As the commercial defense industrial base adapts to fit a leaner Army, the organic industrial base will be called upon to provide more holistic life-cycle support, while staying ready to surge as contingencies demand. Fortunately for those of us in the Army communications-electronics community, Tobyhanna Army Depot (TYAD) has found one key to smarter and leaner sustainment: tap into the ingenuity of its workforce. By giving employees a voice and a stake in Tobyhanna’s success, the depot fosters a culture of innovation that has led to a variety of process and product improvements and cost savings.
CULTURE OF INNOVATION
Nestled in the Pocono Mountains of northeastern Pennsylvania, TYAD is the Army’s center of excellence for the logistics support of communications and electronics equipment, including satellite terminals, radios, radars, night vision devices, airborne surveillance equipment and electronic warfare systems. Its capabilities range from the traditional depot work of maintenance and storage to original efforts in product design, fabrication, integration and field support. Rather than receiving congressional appropriations, Tobyhanna operates out of the Army Working Capital Fund, which aims to break even by returning any monetary gains to customers through lower rates, while collecting any losses from customers through higher rates. That transparency means that TYAD and other Army depots must act like the private sector, keeping overhead and rates low to satisfy their customers: the Army and other DOD program offices.
Unlike in the private sector, the situation is not quite “perform or perish,” because of the “50/50 rule” that requires military programs to use the federal employees of the organic industrial base rather than private contractors for at least half of their maintenance and repair functions. But that doesn’t mean Tobyhanna leaders are content with just working the margins and taking their due. Indeed, Tobyhanna has busted two stereotypes about the public sector. First, by making efficiency part of its core sustainment mission, TYAD has ingrained continuous performance improvement in every aspect of the depot. Second, by cultivating a workforce and culture that are far from what people often think of as “typical government,” it has built an award-winning team that’s just as motivated as the customer to find the smartest way to do the job.

TOBY TECH: Sarah Gomez, an electrical worker, assembles power distribution box switches using an invention that clarifies the sequence in which wires are used and prevents them from getting tangled during the assembly process. TYAD’s Toby Tech program trains its workforce through partnerships with more than a dozen universities. (Photo by Steve Grzezdzinski, TYAD)
The efficiencies are well-documented. TYAD received national attention in 2012, winning the prestigious Shingo Silver Medallion that recognizes sustained dedication to “lean” processes and organizational self-assessment, after cutting in half the number of days to receive, process and shelve communications security (COMSEC) equipment. But the workforce side of the equation is where Tobyhanna truly stands apart from the stereotype. “Team Tobyhanna” consists of a combination of general-schedule, wage-grade and contract employees—all of whom are cross-trained on numerous systems and specialties so they do not become “siloed” in a particular area of expertise. Employees learn more skills and are motivated to tackle new challenges, and the depot can move workers to different systems as needed—for example, a technician who typically works with radar equipment could just as easily repair an urgent order of radios.
Through a program known as “Toby Tech,” the depot spends approximately $8 million annually to train its workforce through partnerships with more than a dozen universities. Hands-on opportunities abound; more than 3,000 employees have volunteered for overseas deployments to support Operations Iraqi Freedom and Enduring Freedom, where they staffed forward-repair areas so that deployed troops could receive timely and affordable on-site maintenance for their communications equipment.
In addition to workforce development, the Tobyhanna culture fosters comprehensive and efficient sustainment by encouraging innovation from the bottom up. Employees at all levels receive public recognition when they suggest changes that are implemented both to improve their own work areas and to boost overall productivity. Some of the best ideas bubble up from the floor after new workers have spent just a few weeks on the job.

LISTENING TO THE WORKFORCE: John LaCapra, electronics mechanic helper, removes thousands of thumbscrews every month using a new device he designed that prevents injury and improves efficiency. By giving its workforce a voice and stake in its operations, TYAD promotes a culture of innovation. (Photo by Steve Grzezdzinski, TYAD)
One employee suggested that buying a box-making machine would streamline the use of space for packaging COMSEC devices for shipping and storage. He earned a bonus and saved the depot up to $75,000 a year. A former Marine Corps radio operator suggested changing the connection switch used to perform software upgrades on encryption devices so more could be modernized at the same time. His idea cost the depot nothing to implement, but reduced costs by 50 percent—savings that were returned to the operational unit that sent the devices and then reaped by subsequent customers. Just this summer, an electronics mechanic helper found a way to save time and the toll on employees’ wrists and hands from manually removing and installing thousands of thumbscrews a month. He devised a socket adapter that attaches to a power screwdriver, making quick work of the 44 turns it takes to unscrew each of four thumbscrews found on a radio set’s mounting base.
DIRECT IMPACT
This culture of innovation at TYAD has directly affected how we support and sustain Army network programs. When the Army introduced the Nett Warrior system to extend digital communications to the dismounted Soldier as part of Capability Set 13, Tobyhanna engineers fulfilled the requirement for a cable to connect a commercial smartphone to a tactical radio—and went several steps further to deliver a full-service capability package.
Thinking from the perspective of the Soldier who would open the box, employees began to load and configure each phone and radio with the required mission data before shipping the systems to unit locations for training. They packaged the phone and radio in a single box complete with ancillary devices and charged batteries, then labeled each box with the role of the Soldier receiving it, so that Soldiers would open the box to find a customized, simple to use, fully operational kit. Loading cryptographic data is the only remaining task to be done on-site by signal personnel. The idea, driven from the floor in response to user feedback, has significantly improved training procedures for units receiving capability sets.

PROCESS MADE SIMPLE: Peter Ankner, electronics worker, found a way to perform software upgrades on thousands of KG-175D encryption devices by simplifying a cumbersome process. As a result, employees were also able maximize work space. (Photo by Steve Grzezdzinski, TYAD)
Tobyhanna’s efforts to cross-train employees are also paying off in the area of field support. As the Army right-sizes contractor field support for tactical communications systems, TYAD increasingly will provide total-package fielding support to help fill the gap. With the recent closure of the Product Management Office for Command Post Systems and Integration (CPS&I), a group of TYAD government employees who had executed new equipment training and new equipment fielding (NET/NEF) for CPS&I is now serving as a “surge team” to fulfill NET/NEF needs for other programs, so they don’t have to continually pay for outside, system-specific field support representatives.
One of the most productive breeding grounds for sustainment efficiencies and employee ingenuity at Tobyhanna is the COMSEC division, a “depot within a depot.” All supply and maintenance functions are in a single, secure facility. That provides a controlled environment to experiment with cradle-to-grave process improvements, from addressing misdirected shipments to packaging new items to upgrading or demilitarizing older devices.
Over the past three years, the COMSEC workforce has led the demilitarization effort to remove thousands of obsolete items from the shelves, saving millions of dollars while freeing storage space for modern equipment and standardizing the Army’s COMSEC footprint. These efficiencies simplify network operations for Soldiers and enable better life-cycle management across the COMSEC portfolio.

PRIZE-WINNING EMPLOYEES: TYAD’s Communications Security Division improved the time it takes to receive, process and shelve equipment, cutting it by almost half. Division personnel used Lean techniques and brainstorming to improve processes, earning a Shingo Silver Medallion. (Photo courtesy of PEO C3T)
For tactical communications acquisition programs, the next several years pose a combination of challenges in which we will look to the organic industrial base for help. The Army will continue to field integrated capability sets using new equipment; “clean up” the battlefield by converging and simplifying existing systems; and insert next-generation technologies to help create a robust, versatile network in support of Force 2025. Depending on program need, Tobyhanna may be called to take on a role previously filled by a prime contractor, serve as a subcontractor to a prime or participate in a hybrid arrangement that allows the vendor to retain control of certain information and processes while the depot does the rest.
For example, with the ongoing fielding of Warfighter Information Network – Tactical (WIN-T) Increment 2, the Army’s on-the-move tactical network backbone, to select brigade combat teams, the WIN-T Increment 1 program is transferring several functions formerly performed by its prime contractor to organic support. Working with the program office and vendor for the workforce to obtain the necessary data and training, Tobyhanna has begun to overhaul WIN-T Satellite Transportable Terminals. About 1,800 terminals are expected to flow through the depot to be returned to like-new condition, establishing a pool of systems so units can swap their old terminals with no downtime.
Perhaps the biggest future sustainment challenge in Army communications-electronics equipment is tactical radios. For the new software-defined Rifleman and Manpack Radios, the Army is executing a Non-Developmental Item (NDI) strategy to create a competitive “radio marketplace” that incentivizes industry to offer superior products at lower costs. To mitigate the logistics challenges of working with multiple vendors, the Army is working to implement standards for ancillary items such as cables and installation kits, as well as to obtain the necessary technical data, to enable Tobyhanna to maintain and upgrade the NDI radios over the long term. We are applying sustainment lessons learned over the past several years, when the Army purchased several commercial off-the-shelf radio models in response to operational needs and TYAD adapted to support them, helping to shape this effort.

PROPOSED COST SAVINGS: Tobyhanna Army Depot employees begin to dismantle an aging AN/FSC-78 Satellite Communications Terminal Antenna Systems at Fort Detrick, MD, in 2013, putting in motion a value engineering proposal that will result in a $30 million cost avoidance. (U.S. Army photo)
CONCLUSION
Even as budgets decline, the demand for tactical communications technologies is not diminishing—in fact, it will increase to enable a lean but still highly capable force. As these systems become more integrated to form a holistic network, we must adopt a strategic approach that takes advantage of the value provided by the Army organic industrial base to make the most of our limited resources. It is time to bring sustainment back into the conversation, and doing that smartly goes beyond commitments at the leadership level. It takes an investment in the people closest to the work, and the desire to see through their eyes.
For more information, visit http://www.tobyhanna.army.mil/.
MR. GARY P. MARTIN is the U.S. Army Communications-Electronics Command deputy to the commanding general. He holds an M.S. in engineering management from the University of Pennsylvania and a B.S. in electrical engineering from Norwich University, and has attended the Harvard Business School, where he graduated from the Program for Management Development. He is a member of the Army Acquisition Corps (AAC).
MG DANIEL P. HUGHES is the program executive officer for command, control and communications – tactical (PEO C3T). He holds an MBA in business management from Oklahoma City University, an M.S. in national resource strategy from the Industrial College of the Armed Forces and a B.A. in political science from the University of Texas at Arlington. He is Level III certified in program management and a member of the AAC.
COL GERHARD P.R. SCHRÖTER is the commander of Tobyhanna Army Depot. He holds an M.A. in national security policy and strategic studies from the Naval War College, a B.A. in international studies and German from Virginia Tech and a certificate in International Security Policy.
This article was originally published in the October – December 2014 issue of Army AL&T magazine.
Subscribe to Access AL&T is the premier online news source for the Acquisition, Logistics, and Technology (AL&T) Workforce.
Subscribe