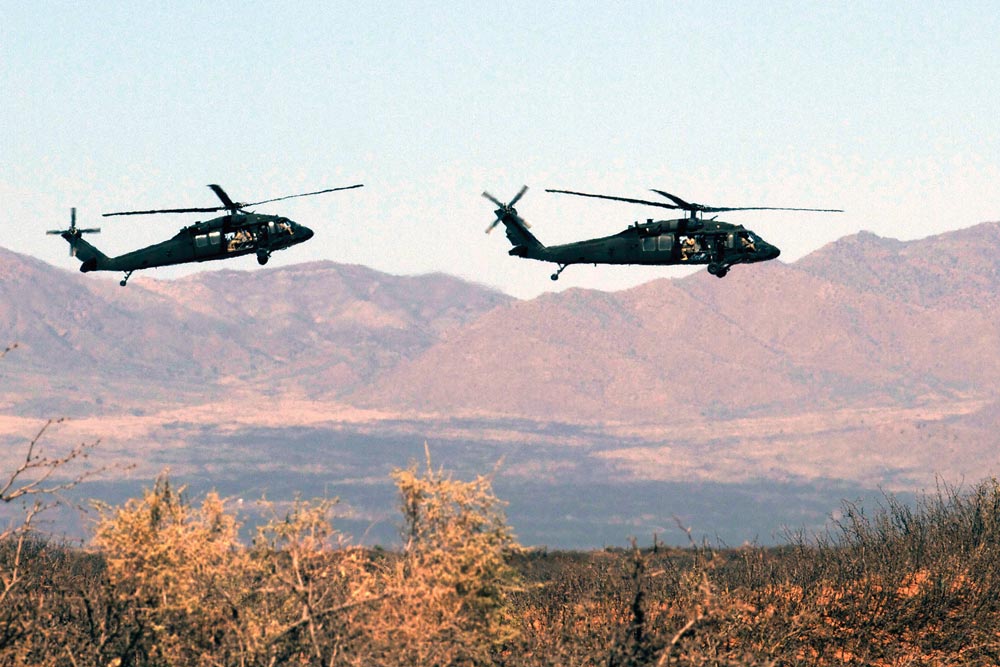
AMRDEC cuts out the middleman and puts engineers next to logisticians to make strategic fix-or-buy decisions and keep warfighters’ equipment in good repair
By Ms. Carlotta Maneice
In 2008, the U.S. Army Aviation and Missile Research, Development and Engineering Center’s (AMRDEC) Engineering Directorate participated in a study with the U.S. Army Aviation and Missile Command (AMCOM) and the Program Executive Offices (PEOs) for Aviation and Missiles and Space to identify ways to help give the warfighter the most reliable, sustainable and affordable weapon systems. One initiative resulting from this study was the AMRDEC Logistics Engineering Team in 2009. Logistics engineering is the intersection of sustainment, logistics and engineering, and our team subscribes to the definition created by the Council of Logistics Engineering Professionals, which says, in part, that logistics engineering “is the professional engineering discipline responsible for the integration of support considerations in the design and development; test and evaluation; production and/or construction; operation; maintenance; and the ultimate disposal/recycling of systems and equipment.” The idea behind the team was to close the gap between the logistics and engineering communities by working within the project offices and reporting directly to the product support manager. Ronnie Chronister, formerly with the engineering directorate and the former deputy to the AMCOM commander, began a precursor to the logistics engineering project in 2003 after identifying the need to purchase numerous, costly aviation replacement parts. “Ken Dulaney, former chief of the AMCOM Industrial Operations Division, and I discussed getting our engineers to better analyze the costs of the replacement parts and determine what solution we could provide to the item managers while reducing the cost to the taxpayer,” Chronister said. Dulaney, Chronister and others met with AMCOM, the PEOs and AMRDEC to discuss the idea of using logistics engineering to solve similar issues with other organizations prior to the start of operations in Afghanistan and Iraq but encountered cultural challenges within the functions of logistics and engineering. The two disciplines were organizationally stovepiped, he explained, with little interaction between the two. Each organization had a different culture and a “this is the way we have always done things” mentality. Operations Iraqi Freedom and Enduring Freedom and the high cost of aviation sustainment forced the two to come together, but the cultures clashed. “The cultures were very strong and change was difficult,” Chronister added. “But if you really want to do good things for the Army and our Soldiers, you have to be adaptable and you have to be open to change.”

THE BENEFITS OF TEAMING A technician performs a system check in the cockpit of a UH-72A Lakota at the Redstone Army Airfield in Huntsville, AL, in March. The logistics engineering program demonstrated that pairing an engineer with the logistics team improved the integration of the engineering and logistics capabilities and helped Soldiers execute their mission more effectively. (Photo by Joseph Carmichael)
PILOT PROGRAM TAKES OFF
After five years of discussions and meetings, a formal working group was established in 2008 to develop the approach that culminated in a pilot program with the UH-60 Black Hawk program office. “Data, people and leadership were the keys in getting the pilot program off the ground,” Chronister said. The team had to identify what was being replaced at what interval and at what cost to perform the proper return-on-investment analysis to determine if it was more economical to continue to buy as-is or invest in redesign, he explained. “And everyone had to be comfortable enough to understand we were a team trying to save the Army money and get a better product for our Soldiers.” “The initial response from our weapon system team members and logisticians was ‘I don’t need a logistics engineer,’ ” said John Jensen, director of the AMCOM Aviation Directorate. “Educating the logisticians on the benefits of having logistics engineers co-located with them was the key.” They were resistant partially because of normal friction between engineers and logisticians, as well as a lack of understanding of how a logistics engineer can help get the job done, he said. “Before the pilot program, program engineers and logisticians didn’t speak the same way,” noted Jensen. “If we are talking about a servo cylinder, for example, a logistician may discuss the supply chain aspects of the item—the lead time to buy it, who makes it, how much it costs, for example. An engineer may talk about the technical aspects, such as the pounds per square inch or dimension,” he explained. “Today, logistics engineers are able to work side by side with our logisticians, and this bridges the communication gap between the two groups.” The Army and the warfighter are reaping those benefits, which include lower costs, faster turnaround times and greater efficiency. AMRDEC logistics engineers use their expertise and knowledge of engineering to interpret the logistics requirements for the engineering community. They work with engineers in the technical management offices and many of the other Engineering Directorate’s specialty areas to address logistics issues related to testing, sustainment, improvement, design, development and acquisition. They assist in weapon system design and sustainment efforts to reduce the logistics footprint, increase readiness, reduce the maintenance burden and improve supply chain performance. They also introduce best practices to improve logistics efficiency and reduce total ownership cost.

COOLING SPENDING A machinist at Fort Hood, TX, performs a cold spray repair of an Apache helicopter mast base support. The use of cold spraying, implemented through a logistics engineering program, has helped the UH-60 Black Hawk program reduce repair times and sustainment costs. (Photo by Vic Champagne, U.S. Army Research Laboratory)
WHO PAYS?
One major challenge of the logistics engineering pilot program was funding. “Even though logistics engineers and the logistics engineering program pay for themselves almost instantaneously, determining who funds them is always a big challenge,” said Keith Roberson, former deputy project manager for Utility Helicopters. “The logistics engineer’s ability to help improve readiness and provide efficient solutions to issues that arise in the field offset any cost of having them on staff,” added Roberson, who is now director of the AMCOM Logistics Center. Today, the Utility Helicopter Program continues to see the financial benefit of adding logistics engineers. “We had a logistics engineer with a statistical background who used his knowledge to develop an automated data analysis tool for our logisticians,” said Marsha Bailey, director of the AMCOM Logistics Center’s Utility Helicopter Directorate. “This is just one of the benefits of having logistics engineers work side by side with us. They know the engineering side and they can apply their expertise to the needs of the logistician.” In addition to working with the logisticians to identify problems, logistics engineers must be able to work with the systems engineering team to identify how their design decisions impact a system’s life-cycle sustainment costs. Logistics engineers work to reduce the sustainment burden by analyzing support structures for each system design and selecting those that emphasize reduced manpower requirements, modularity, reliability and use of existing tools and facilities. Good communication skills are also vital for logistics engineers to validate a process into products or systems. “Logisticians and engineers are not wired the same way,” Chronister said. “Logistics engineers have to be good communicators and be that consensus builder with their people skills and credibility.”

EVALUATING THE OPTIONS A repair technician completes the wiring on the UH-72A Lakota helicopter as part of the Wide Area Augmentation System upgrade at the Redstone Army Airfield in Huntsville, AL, in March. Logistics engineers can minimize the sustainment burden by analyzing support structures for each system design and selecting those that reduce manpower requirements and use existing tools and facilities. (Photo by Joseph Carmichael)
RECENT SUCCESSES
The program has generated a number of cost-effective solutions. For example, the Black Hawk Project Office found that having an engineer working with their logistics team improved the integration of the engineering and logistics capabilities and helped them better execute their mission. Recently the logistics engineering team provided a break-even analysis on the UH-60 main rotor hub. The issue was whether purchasing new rotor hubs was more cost-effective than overhauling the existing obsolete ones. The team compared the life-cycle costs, and determined it would be more expensive in the immediate future to buy new hubs. After five years, however, the model indicated that the cost of buying new hubs would break even with the cost of overhauling the obsolete hubs. After 12 years, overhauling the obsolete hubs proved to be $11.51 million more costly. Logistics engineers have also helped the UH-60 program reduce sustainment costs through the implementation of new technologies, including cold spray, a method of suspending metals or other materials in gas, then spraying the gas on damaged machine parts at supersonic speeds, reducing repair times. The UH-60 logistics engineering team lead chaired an integrated product team (IPT) to transition new cold spray repair technology to aviation components. A transmission sump pan, a component of the gearbox housing, was chosen from the salvage yard as the test component. The team sprayed, tested and qualified the pan with an immediate cost avoidance of roughly $17,000. The sump pan would have been disposed of if not for the work of the IPT. The fallout rate for the transmission sump alone is roughly four per year, which translates to a cost avoidance of about $68,000 annually with the cold spray technology. The repair techniques identified in this test will be applied in the future to components experiencing similar damage and, if applied to the other gearbox housing components, this technology could achieve a savings of $3.5 million. Earlier this year, AMRDEC’s Fernando “Rios” Merritt, the Black Hawk logistics engineering team lead, won a Defense Manufacturing Technology Achievement Award for his work to integrate cold spray technology into Army systems.

MAKING THE DROP UH-60 Black Hawks from the 1st Armored Division Combat Aviation Brigade prepare to drop off infantrymen during an air assault raid simulation as part of Exercise Iron Focus, held March 26 at Fort Bliss, TX. A logistics engineering program first piloted with the Black Hawk Program Office in 2009 now includes the Chinook, Lakota and Apache helicopter programs. (U.S. Army photo by SPC Maricris C. Cosejo)
STEADY GROWTH SUPPORTING SOLDIERS
Since its inception, the logistics engineering program has grown steadily, from two engineers supporting the Black Hawk program in 2009 to 19 engineers supporting 12 organizations today, including the Chinook, Lakota and Apache helicopter programs, close combat weapon systems and unmanned aircraft systems. “Much of the success goes to the first two logistics engineers, Merritt and Chad Reeves, and the immediate impact they made in the first pilot of this capability in the Black Hawk Project Office,” said Lou Sciaroni, AMRDEC Logistics Engineering Branch Chief. “However, each of the successive team members has continued this line of excellence and through their efforts has helped the team evolve to where it is today.” “The logistics engineering program here at AMRDEC is unique because we are supporting the warfighter in a very real way,” said Merritt. “A lot of times you don’t see the fruits of your labor, but when technical solutions are made on behalf of the Soldier, you know your team has a direct impact on whether that Soldier has everything he or she needs to continue and complete their mission.”
CONCLUSION
AMRDEC logistics engineers help reduce life-cycle costs, enhance operational capability and optimize support infrastructure through their impact on design and logistics efforts. Their knowledge helps technicians, logisticians and other engineers to take advantage of new capabilities and incorporate them into their processes. “The program is growing, and AMRDEC logistics engineers will continue to impact the life-cycle costs of Army weapon systems, and ultimately the warfighter, through their engineering efforts and their focus on improving supportability,” said Sciaroni.
For more information, go to http://www.amrdec.army.mil/AMRDEC/.
MS.CARLOTTA MANEICE is a program analyst for Intuitive Research and Technology and provides program support for AMRDEC Public Affairs. She has an MBA and a B.A. in communication from the University of Mary Hardin-Baylor.
This article was originally published in the July – September 2015 issue of Army AL&T magazine.
Subscribe to Army AL&T News, the premier online news source for the Acquisition, Logistics, and Technology (AL&T) Workforce.
Subscribe