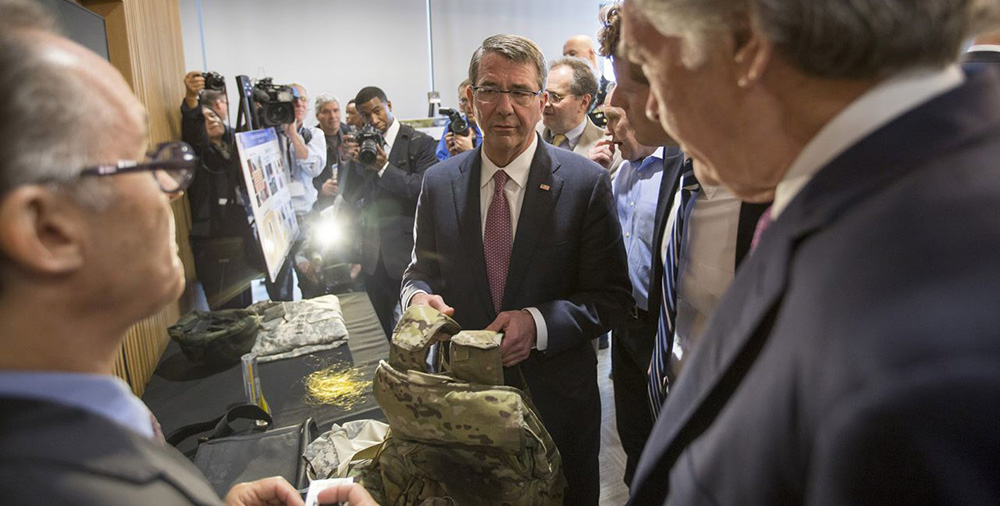
By Maj. Gen. John F. Wharton and Andrew Davis
In a continuing effort to close capability gaps more affordably while spurring advanced manufacturing capabilities in the United States, Secretary of Defense Ash Carter on April 1 inaugurated the new Revolutionary Fibers and Textiles Manufacturing Innovation Institute (MII) in Cambridge, Massachusetts.
In December 2014, President Barack Obama identified advanced manufacturing as a key initiative for the future of the American economy by signing the Revitalize American Manufacturing and Innovation Act into law, thereby formalizing the National Network for Manufacturing Innovation (NNMI), a multiagency initiative with a core focus on a series of MIIs.
Carter is a strong advocate for the president’s priorities. At the announcement of a public-private partnership that marshaled $317 million to establish the Fibers and Textiles Manufacturing Innovation Hub, he said: “It’s important America keeps leading in innovation and brings jobs back home. The reality is that we don’t know all the advances this new technology will make possible. That’s the remarkable thing about innovation, and it’s another reason America and America’s military must get there first. To stay ahead of challenges and stay the best, DOD is investing aggressively in innovation.”

DIRECTION FROM THE TOP
President Barack Obama meets Dr. Greg Harris, program manager of the Digital Manufacturing and Design Innovation Institute. Obama formalized the National Network for Manufacturing Innovation when he signed the Revitalize American Manufacturing and Innovation Act in December 2014. (Official White House photo by Pete Souza)
According to a White House fact sheet, this eighth MII “will combine over $75 million of federal resources with nearly $250 million of nonfederal investment in innovative fabrics and textiles with novel properties ranging from being incredibly lightweight and flame resistant, to having exceptional strength and containing electronic sensors.” The fabrics will see, hear, sense, communicate, store energy, regulate temperature, monitor health, change color and more.
This 89-member consortium (52 industry members and nonprofits, and 32 universities, colleges and schools, and five state government and regional organizations) that makes up this MII, known as the Advanced Functional Fabrics of America Alliance, takes traditional Army Manufacturing Technology Program (ManTech) partners such as Warwick Mills and pairs them with audio equipment maker Bose, computer chip maker Intel, and nanofiber manufacturer FibeRio Technology Corp. to produce new and innovative products that can benefit Soldiers as well as first responders and, eventually, the average consumer.
Possibilities include multifunctional fibers, “advanced nonwovens and yarn production, sophisticated weaving and knitting capabilities and end-product fabrication for first-to-market manufacturing opportunities,” according to the MII‘s website. “For example, lightweight sensors woven into the nylon of parachutes will be able to catch small tears that otherwise would expand in midair, risking paratroopers’ lives,” Carter said. Uniforms might have electronics embedded in their fibers to detect potential chemical and radiological agents, and tents with fabrics that could generate and store their own power and regulate the temperature inside will reduce fuel consumption in the field.

PRECISION TIMING
The Chip Scale Atomic Clock (CSAC) provides next-generation position, navigation and timing systems with the ability to provide high-security communication and precision time and frequency sources in GPS-denied environments. The Army ManTech program helped automate a significant portion of the CSAC manufacturing processes. (Photo by Edric Thompson, CERDEC Public Affairs)
The overall Army ManTech strategy for engagement with MIIs is to accelerate manufacturing research and development (R&D) through direct engagement with institutes; leverage institute consortium members to transition technology across the industrial base; and broaden workforce development and science, technology, engineering and mathematics (STEM) impact by coordinating with MII outreach initiatives. Army ManTech has provided subject matter expertise to inform initial MII topic areas, participated in technology advisory boards that roadmap future project investments, and funded discrete projects within MIIs that address Army manufacturing requirements. MIIs are competitively selected and composed of companies, universities, nonprofit organizations, research organizations and start-up incubators.
The Department of Commerce’s National Institute for Standards and Technology oversees the NNMI. These public-private partnerships are designed to advance technologies by improving manufacturing capabilities to spur global competitiveness. The institutes have strong interagency management, contracting and subject-matter expert engagement. Institutes focus on areas such as additive manufacturing, lightweight metals, integrated photonics, power electronics, advanced composites, digital manufacturing and design, fibers and textiles, and flexible hybrid electronics. Federal and non-federal investments total $1.8 billion.
The Army’s ManTech program is executed by the U.S. Army Research, Development and Engineering Command (RDECOM), in support of the Office of the Deputy Assistant Secretary of the Army (Research and Technology). With an annual budget of about $60 million, ManTech provides seed funding to close gaps—technological, risk, manufacturing production and affordability—by working with the Army’s organic industrial base as well as private industry. As researchers focus on innovation, ManTech becomes a critical enabler to affordably transition technology solutions that bring potential capabilities into reality. Science and technology (S&T) and acquisition project managers execute Army ManTech projects.
RDECOM manages three other MIIs in addition to the new fibers and textiles institute. The others are:
- The Digital Manufacturing and Design Innovation Institute (DMDII) will help develop the capabilities and networks necessary to provide advanced manufacturing capability to compete in the global manufacturing arena. The goal is to simultaneously create three-dimensional (3-D) computer-aided design (CAD) files and process information in technical data packages (TDP) instead of the traditional 2-D TDPs. The transition to digital manufacturing will ultimately save time, money and resources across a system’s life cycle. ManTech is working with the DMDII to mature digital manufacturing for adoption and application within the Army’s organic industrial base. These initiatives will enable a more efficient, cost-effective organic industrial base that supports rapid delivery of parts and systems to Soldiers.
- American Institute for Manufacturing Integrated Photonics (AIM Photonics) focuses on emulating successes by the electronics industry during the past 40 years and transitioning key lessons, processes and approaches to the photonic integrated circuit (PIC) industry. The institute seeks to advance integrated photonic circuit manufacturing technology development while providing access to state-of-the-art fabrication, packaging and testing capabilities.
- Flexible Hybrid Electronics (NextFlex), is focused on catalyzing the flexible hybrid electronics ecosystem to commercialize technology through investments in materials scale-up, thinned device processing, device/sensor integrated printing and packaging, system design tools, and reliability testing and modeling. The institute’s technology demonstration topics include wearable human monitoring devices to address DOD, medical and consumer needs; integrated array antennas to demonstrate radio frequency capability in a flexible hybrid electronic application; and soft robotics that could enable stretchable electronics across a variety of applications.
Army S&T develops, demonstrates and transitions knowledge and materiel solutions that enhance our nation’s defense. In support of this, Army ManTech exists to address high-priority manufacturing needs. The program reaches across the S&T and acquisition communities to identify and solve manufacturing gaps. The program participates in national manufacturing initiatives and invests alongside the defense industrial base to realize affordable advanced manufacturing solutions for current force systems and future capabilities.
The ManTech program focuses on cost reduction and sustainability of current systems, support of critical S&T efforts, and maturation of digital and advanced manufacturing processes. The core focus investment areas for Army ManTech are structured around portfolios for:
- Air.
- Ground maneuver.
- Lethality.
- Command, control, communications and intelligence (C4I).
- Soldier and squad.
- Innovation enablers.
The program assists the acquisition community by providing a mechanism to bridge gaps between Army research centers and the program executive offices because of manufacturing obstacles. As program managers focus on the cost, schedule and performance of their projects, these manufacturing hurdles are often too great to transition many critical capabilities to the Soldier. ManTech then steps in where risk factors are steep.
SUPPORT TO THE SOLDIER
Modernization is a key imperative from Chief of Staff of the Army Gen. Mark A. Milley. The ManTech investment in the Low-Light Level Sensor (LLLS) project within the C4I portfolio area addresses this need while meeting the Army Training and Doctrine Command Army Warfighting Challenges of exercising mission command and developing situational understanding for Soldiers.
Night vision devices are crucial to Soldiers across an array of missions, mounted and dismounted, for survivability, maneuverability and lethality. For the Army to retain “ownership of the night,” emerging vision systems will require novel electronics that enable multifunction sensing and digital, low-light level devices, including conformal displays that provide the same or better performance as the current, traditional image intensifier tubes.
The Army Communications-Electronics Research, Development and Engineering Center (CERDEC) has demonstrated a major advancement in technology maturity through this four-year effort. The project focuses on replacing traditional image intensifier tubes with digital sensors that allow for remote use and image capture, image processing and better performance at the lowest light levels. It addresses key manufacturing metrics by increasing production, optimizing individual components for better performance and automating production steps. LLLS will reduce unit costs by more than 75 percent and decrease life cycle costs, which will allow for more widespread implementation of this technology.
The increased performance and reliability of the sensor system has resulted in user acceptance and a multitude of cross-service transition paths, including the AH-64 Apache, the F-35 Joint Strike Fighter helmet and forward-looking camera, and adoption of the system as a leading candidate for the future Enhanced Visual Acuity system for the Naval Air Systems Command. The LLLS has transitioned to full-rate production, and the first fielding was with the 1st Battalion, Apache 82nd Combat Aviation Brigade.
Similarly, in 2006, DOD turned to the S&T community and the ManTech program for an improved helmet, which became known as the Enhanced Combat Helmet and is now being fielded by the Army and the U.S. Marine Corps. ManTech supports manufacturing technologies with its Soldier and squad portfolio that reduce the commercial risk in transitioning military-unique manufacturing processes to production. Before ManTech, the Army’s technology for manufacturing helmets was more than 30 years old and not adaptable for fully exploiting new materials.

INNOVATIVE FABRICS
Secretary of Defense Ash Carter views technologies from the Army Natick Soldier Research, Development and Engineering Center during the announcement of the fibers and textiles manufacturing innovation hub April 1 at Cambridge, Massachusetts. The hub will develop innovative fabrics and textiles with novel properties. (U.S. Army photo)
The Army helmet fabrication goal was to develop an entirely new methodology for mass producing complex shapes combining layers of different thermoplastic materials. Researchers pioneered an innovative molding technology, a preform process that reduces touch labor by as much as 40 percent and waste by as much as 70 percent. Army material researchers developed, executed and transitioned manufacturing methods that had precluded the use of ultra-high-molecular-weight polyethylene. This reduced costs and increased ballistic and fragmentation protection by 35 percent while maintaining similar weight.
The ManTech program allowed the Army to serve as a catalyst to stimulate industry into unconventional ways of adopting these new materials for ballistic protection. New thermoplastic-based composites are inherently more expensive, so handling them, reducing the waste associated with the process to form them, and maximizing their benefit in terms of how they are formed into the ultimate part is critical.
The Chip Scale Atomic Clock (CSAC) is a prime example of Army researchers spurring the defense industrial base to create an advanced manufacturing process. The communications industry uses atomic clocks, which are recognized for their accuracy, in larger systems, but the typical units are large, heavy and require significant power. However, CSAC is a miniature atomic clock demonstrated by the Defense Advanced Research Projects Agency (DARPA) in a laboratory environment which, when integrated into communications systems, can provide Soldiers with situational awareness in the absence of GPS.
The Army ManTech program, with co-investment from the Defensewide Manufacturing Science and Technology Program, automated a significant portion of the CSAC manufacturing processes to enhance production capabilities, increase yields and reduce unit costs. Key manufacturing issues addressed include redesigning processes, and using less expensive and 20 percent fewer parts while maintaining peak performance. The effort fostered competing manufacturing technologies to ensure more effective solutions and manufacturing readiness level maturity. Using multiple vendors significantly reduced acquisition cost and has led to CSAC availability in the commercial sector and defense position, navigation and timing solutions.
CONCLUSION
As the Army continues to develop more complex systems that combine multiple scientific and engineering disciplines, affordability and producibility will continue to be the keys to successful transition of advanced technologies from the lab to the field.
Senior DOD and Army leaders are focused on how Army R&D will empower decisive overmatch for decades into the future. The Army’s ManTech program, through specific investments in core areas as well as supporting the president’s advanced manufacturing initiatives and the NNMI, continues to be a vital tool for delivering capabilities for Soldiers.
MAJ. GEN. JOHN F. WHARTON is the commanding general of RDECOM, a major subordinate command of the U.S. Army Materiel Command (AMC), at Aberdeen Proving Ground, Maryland, leading more than 13,000 researchers, engineers and support personnel. He holds an M.A. in national security and strategic studies from the Naval War College and a B.S. from the United States Military Academy at West Point, and studied at the U.S. Army Command and General Staff College. He also completed the Quartermaster Officer Basic and Advanced courses and the Inspector General’s Course.
MR. ANDREW DAVIS is a program manager for the U.S. Army’s ManTech program and an RDECOM employee. He directly supports the Deputy Assistant Secretary of the Army for Research and Technology and RDECOM as a subject-matter expert on manufacturing technology and process development. He holds a master’s in mechanical engineering from Johns Hopkins University and a B.S. in mechanical engineering from Grove City College. He is Level III certified in program management and engineering.