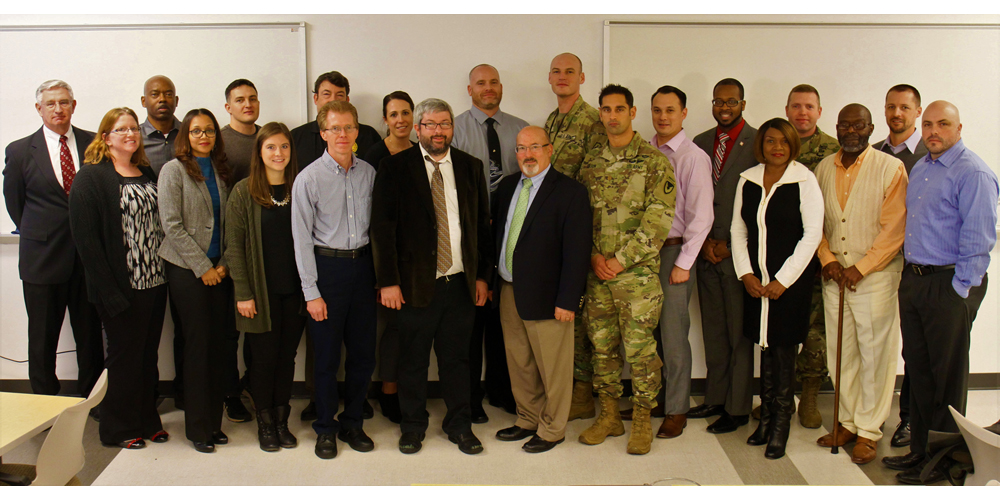
By Dan Lafontaine, PEO C3T Public Affairs
ABERDEEN PROVING GROUND, Md. (Jan. 25, 2017) — As the Army continues to “do more with less,” process improvements such as those spurred by Lean Six Sigma (LSS) ideology are enabling the Army to more efficiently manage government resources.
In support of these concepts, 17 LSS Black Belt candidates from APG, including employees from Program Executive Office for Command, Control and Communications-Tactical (PEO C3T), completed a four-week course in December as part of their certifications.
LSS is a process-improvement framework that enables practitioners to evaluate complex issues, identify inefficiencies and develop solutions to save time and money.
During the class graduation, Gary Martin, PEO for C3T, thanked the LSS students for their efforts, which are executed in parallel to their fulltime jobs. He said the Army is now depending on them to translate their new skills and knowledge into results.
“When you go back to your organization, challenge everything — every process you think is broken or too long,” Martin said. “Your job now is to lead others in finding more efficient ways to do our business. You will be expected to mentor the people within your organization.”

Lean Six Sigma Black Belt candidates from Aberdeen Proving Ground, Maryland, tour the Marquip Ward United factory Nov. 16, 2016, in Hunt Valley, Maryland. (Photo Credit: U.S. Army photo by Thom Hawkins, PEO C3T)
Two PEO C3T employees taught LSS Black Belt courses in the fall and spring of 2016: Thom Hawkins, director of PEO C3T’s Continuous Performance Improvement Program, and Maj. Keith Jordan, assistant product manager for Warfighter Information Network-Tactical Increment 1, the Army’s at-the-halt tactical communications network.
As LSS teachers, their mission focuses complemented each other — Hawkins has a background in analysis and working with data, and Jordan has a Soldier’s field experience.
“The students learned to look at every situation as a process versus an unchangeable situation they encounter,” Jordan said. “They have tools to break a situation down into its components and find ways to improve it, versus just accepting a situation as it is.”
Both Hawkins and Jordan are pursuing Master Black Belt certification. To earn this level of certification, a candidate must have an existing LSS Black Belt, take a three-week statistics course and complete an exam, teach all modules of a Black Belt course, complete a second Black Belt-level project and a project identification and selection workshop, and mentor two Black Belt candidates through their projects.
“LSS is used in the corporate world where time and efficiency is important to the bottom line,” Jordan said. “When we apply LSS concepts to the Army, it results in reduced cost and labor hours and operational benefit to the Army.”
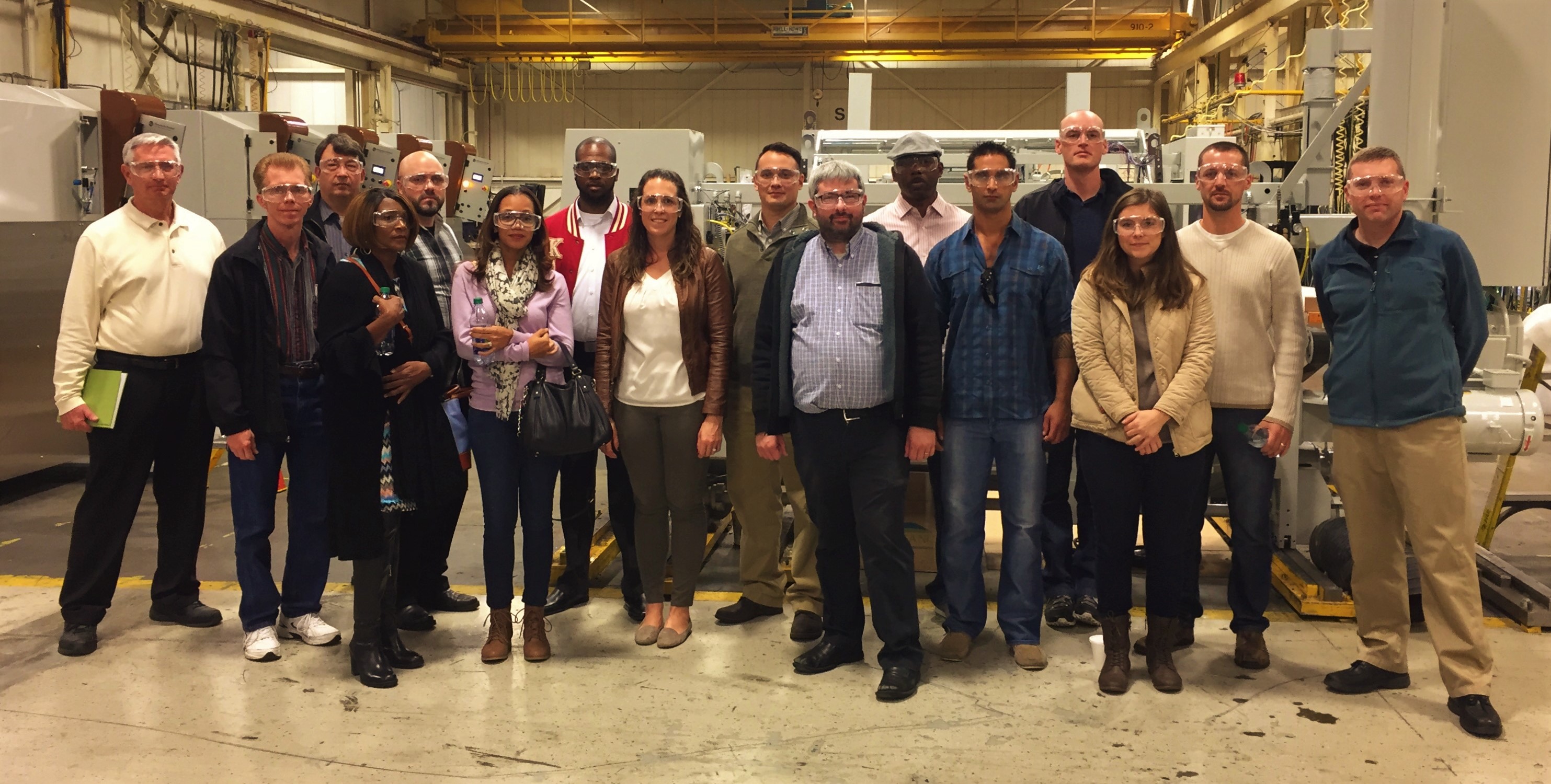
Lean Six Sigma Black Belt candidates from Aberdeen Proving Ground, Maryland, tour the Marquip Ward United factory Nov. 16, 2016, in Hunt Valley, Maryland. (Photo Credit: Photo by Wade McCartin, Marquip Ward United)
Hawkins’ said his Master Black Belt project will help ensure that PEO C3T is consistent in reporting schedule data to external audiences. The organization’s analysis found that each report or briefing was reviewed through the chain of command but not compared with each other for consistency. To resolve the issue, the team repurposed an existing review step to include that lateral assessment.
“One of the great things about LSS is that it shows us how to focus on what the customer wants, and how we can improve the customer’s experience,” Hawkins said. “Every one of us has customers, ultimately leading to the soldier and the taxpayer.”
Each Black Belt course that Hawkins and Jordan taught included a field trip that enabled their students to see firsthand how a company invested in LSS ideology can encompass these process improvements into their operations. The spring class toured an Amazon.com distribution plant in Middletown, Delaware, in June 2016. The fall class traveled in November to Hunt Valley, Maryland, to tour Marquip Ward United, a company that builds and repairs machines used to make corrugated cardboard.
“[Amazon.com] has thought about process improvement all day, every day for the last 20 years,” said Andrea Jordan, a PEO C3T budget analyst who participated in the spring LSS course. “How can we shave off two or three seconds here or there? Their business model is very different from what you’d think it would be. It was eye-opening.”
Jordan said that she found LSS appealing in that she could help the Army get more benefit out of the same amount of resources.

Lean Six Sigma Black Belt candidates from Aberdeen Proving Ground, Maryland, tour the Marquip Ward United factory Nov. 16, 2016, in Hunt Valley, Maryland. (Photo Credit: U.S. Army photo by Thom Hawkins, PEO C3T)
“The course gives you a set of tools to go about improving things and make [better] decisions,” she said. “You can take the model of Lean Six Sigma and apply it to almost anything.”
To gain their official LSS Black Belt Certification, the students must now complete a project that improves efficiency within their organizations. Ed Lauer, platform fielding team lead for Project Manager Mission Command, is searching for an improved process to reduce inefficiencies during fielding of the Army’s Joint Battle Command-Platform — the Army’s next-generation friendly-force tracking system.
“One of the best things about the course is that it changed my perspective,” Lauer said. “I constantly look for ways to improve things. This would be a great opportunity to help streamline the [fielding] process.”
Lauer hopes to complete his project by this summer and obtain his LSS Black Belt certification. He said that he plans to follow Martin’s advice on mentoring his organization by encouraging his team to incorporate the lessons he learned from the LSS course.
“Lean Six Sigma really changes your thinking about certain things; to get away from, ‘This is the way we’ve always done it,’ ” Lauer said. “[We need to] spend time now to develop processes that will save time in the future, map out the processes, eliminate unnecessary steps. Maybe we can make our lives easier.”
This article was originally published at https://www.army.mil/article/181248.

Lean Six Sigma Black Belt candidates, instructors and Gary Martin (front row, middle), program executive officer for Command, Control and Communications-Tactical, gather for the LSS graduation ceremony Dec. 9, 2016, at Aberdeen Proving Ground, Maryland. (Photo Credit: U.S. Army photo by Ryan Myers, PEO C3T)
RELATED LINKS