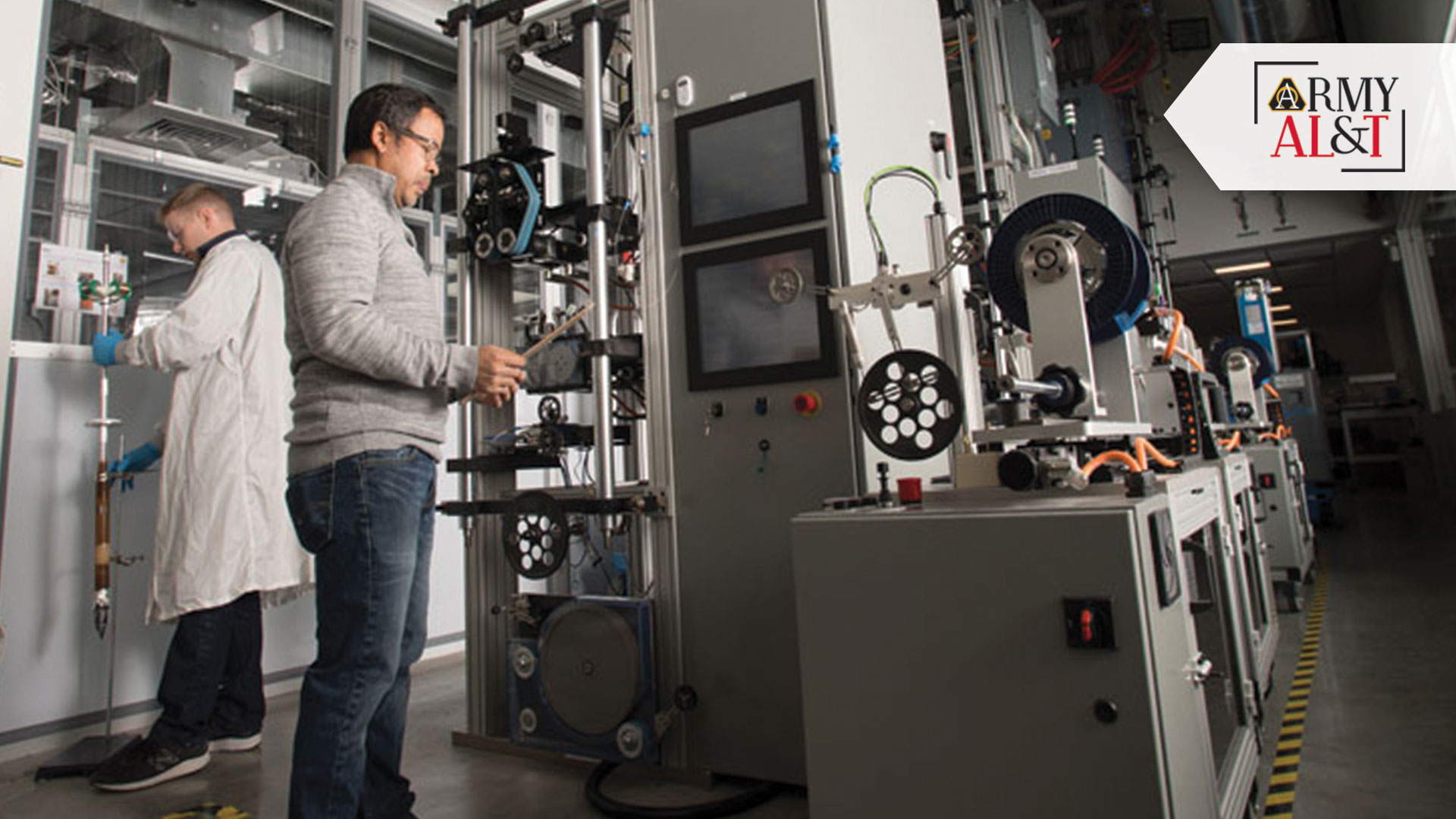
FIBER OPTICS: Advanced Functional Fabrics of America (AFFOA) research and development technician Chhea Chhav monitors a fiber draw on one of AFFOA’s five fiber draw towers. Draws need to be monitored throughout the draw process to ensure fiber’s reliability and success. (Photos by Greg Hren, AFFOA)
Automation in Textile Production: Bringing Value and Capability to the Soldier
by Jeffrey Pacuska, Clay Williamson, Suzanne Horner and Stephen Luckowski
Domestic textile manufacturing capacity is rapidly diminishing as a result of globalization. A healthy domestic industrial base is essential to meet wartime surge production requirements and to ensure that our warfighters are equipped with most advanced uniforms and other textile-based combat equipment in the world.
The Office of the Secretary of Defense (OSD) Industrial Base Analysis and Sustainment (IBAS) office is dedicated to ensuring that DOD is positioned to more effectively and efficiently address industrial base issues and support the national security innovation base. The Textile Automation to Enhance Domestic Military Production program is an IBAS initiative to spur modernization in the domestic clothing and textile defense-industrial base, an industry that has largely relied on the same machinery and manufacturing techniques for decades.
The U.S. textile industry is also facing diminishing workforce availability and increased global competition, primarily from Asia. Investing in new manufacturing technologies that offset workforce losses and create higher value products in the United States will promote global competitiveness in existing textile markets while lowering the risk for technology investments. The payoffs to DOD for this investment are a more robust supply chain that minimizes cost to the services, and advanced capabilities for Soldiers through next generation “smart” textiles being manufactured commercially in the United States.
To this end, the IBAS office has partnered with the Army’s Product Manager for Soldier Clothing and Individual Equipment (PM SCIE) and the Combat Capabilities Development Command – Soldier Center (CCDC-SC) to execute the Textile Automation to Enhance Domestic Military Production program. While there are many elements of the textile supply chain that could benefit from new technology, this effort will initially focus on the automation of textile production and the insertion of robotic cut and sew technologies in the final assembly. In doing so, it will take cues from efficiencies gained in the microprocessor industry.
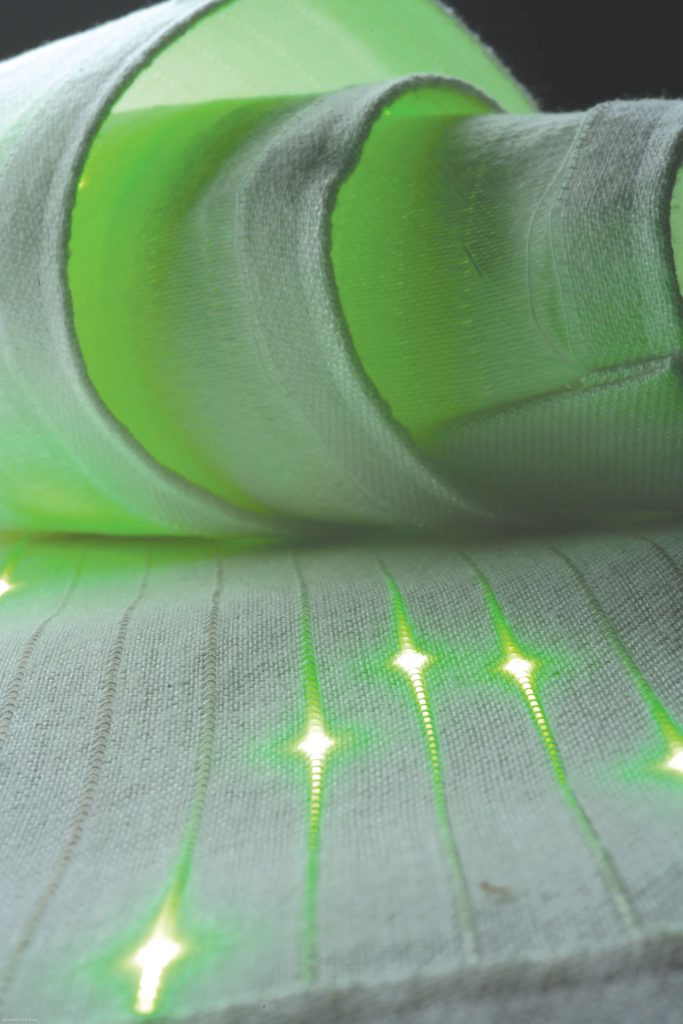
MATERIAL DIFFERENCES: Advanced manufacturing techniques can introduce technology into fabrics, like this swatch with integrated LED fibers. AFFOA’s product development team continuously innovates around incorporating fiber technology seamlessly into fabrics.
This effort will provide the foundation for innovation and technological dominance required to support the National Security Strategy (NSS) and National Defense Strategy (NDS) in three key areas
• Assess financial and production capability of current domestic textile producers that support key product lines from fiber to finished product, ensuring resiliency and redundancy throughout the relevant supply chains (fiber, fabric and assembly). These assessments will allow the IBAS program to prioritize limited resources toward more vulnerable sectors of the industry.
• Develop prototype machinery and production lines that address emerging operational needs and existing technology gaps to drive affordability and availability across the domestic defense industrial base. By comparison, overseas advancements in textile technology may not be available to the DOD, potentially creating a situation where peer competitor forces have advantages in area such as detectability and environmental and ballistic protection.
• Expand the current United States manufacturing industrial base to meet critical material supply requirements through capability and skill improvements with traditional and non-traditional suppliers through innovative financial investments and technology infusion. The United States must maintain surge production capacity for textile products to support rapidly emerging wartime demand. This will not be possible without modern factories and trained workers.
BERRY-REGULATED
From the 1970s until 2004, world textile trade was governed by the Multi Fiber Arrangement (MFA). This consisted of a system of quotas that limited bilateral imports of specific types of textiles and apparel with the purpose of preventing any one country from dominating the textiles export market. Phasing out of that agreement began in 1995 and then was eliminated in 2005 as the textile trade came under the jurisdiction of the World Trade Organization.
In 1995, the United States was the world’s leading apparel maker, accounting for 13 percent of the world’s textile market. However, by 2017 it had dropped to 3 percent. The second order effects to the United States have been the loss not only of manufacturing competencies but also of more skilled design, engineering, and production skills across supporting industries.
Textiles form an integral component to many defense and commercial systems in ways that don’t appear obvious to the common observer. While uniforms, tents, parachutes and backpacks are certainly fabric based, textile applications also include composite and non-woven structures. Kevlar body armor, fiberglass in drones and carbon fiber in advanced aircraft are all textile based applications. For DOD textile products, the government retains domestic capability through protected supplier arrangements such as the Berry Amendment and the Javits-Wagner-O’Day Act. These protections have also resulted in a fragile DOD supply chain, for which the government is often the only customer.
The Berry Amendment requires DOD to give preference in procurement to domestically produced, manufactured or home-grown products, most notably food, clothing, fabrics, and specialty metals. No textile-based product procured by DOD can contain any foreign-made fiber or be processed otherwise overseas. The Berry Amendment-protected DOD supply chain represents the output of 12 percent of textile mills, 21 percent of textile product mills and 26 percent of apparel production, and these are generally seen as an essential element of the remaining U.S. textile, apparel and footwear industrial base.
Increased automation and assembly capabilities would help to add flexibility to the Berry-protected supply chain, allowing for greater diversity in production and potential expansion into non-DOD markets. Moreover, the U.S. textile industry is identified in a report drafted by the Interagency Task Force in Fulfillment of Executive Order 13806 on “Assessing and Strengthening the Manufacturing and Defense Industrial Base and Supply Chain Resiliency of the United States” (September 2018). With the large movement of textile manufacturing to cheaper foreign markets, and fewer domestic companies producing textiles, shelters, clothing, individual equipment and composites, such as body armor and helmets, face greater risk. Currently, only a few domestic sources can provide the material requirements for defense-specific textiles.
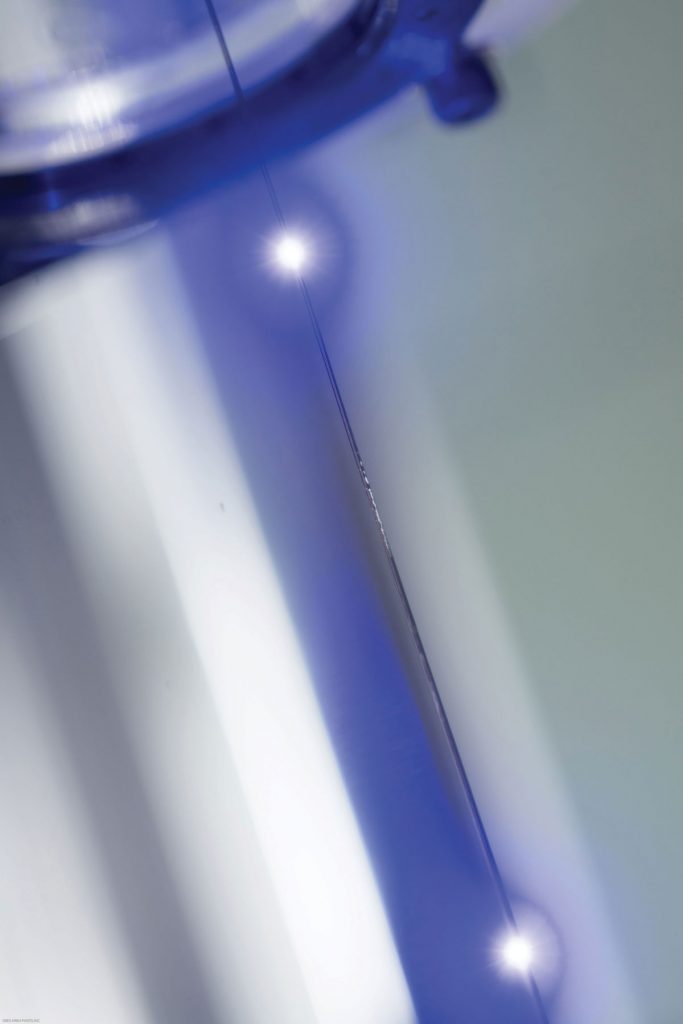
OUT OF THE BLUE: There are many potential uses for fabric containing advanced monofilament LED fibers, which are able to emit and receive data.
CHANGING THE PLAYING FIELD
At the materiel level, the equipment used in most fabric manufacturing and cut and sew operations has not changed substantially in over a century. These machines are highly manpower-intensive, not upgradable and ill-suited for incorporation of eTextiles, smart materials or other next-generation technologies. Most of the mills and factories, particularly in the DOD supply chain, operate on extremely tight margins that rarely offer them the ability to innovate or upgrade existing equipment, both of which are critical to remaining viable and sustainable. Not only does this limit or threaten DOD’s current and future procurement activities, it all but eliminates the possibility for manufacturing advanced fiber- and fabric-based technologies.
While automation will certainly help to shore up elements of the textile value chain, the gains to be made in traditional textiles may be limited due to the significant losses to global competitors through the last three decades. A solution may be to leverage U.S. innovation by creating a new textile paradigm based on microelectronics and advanced materials which could provide operational advantages to warfighters, and new commercial consumer markets.
Examples on the DOD side might include Soldier-worn sensors, unmanned aerial vehicles with communication or detection components built into their structural elements and materials that change shape or appearance based on environmental or physical conditions. Commercial applications could include such things as patient-monitoring technologies for hospitals, monitoring and recording systems built into the panels on new lightweight vehicles, or adaptive insulation and moisture control for construction applications.
Additionally, a new high-tech workforce will be required in order to support building the infrastructure and operating automated textile manufacturing facilities. Advanced skills will be required for textile manufacturing, finishing, programming digital machine interfaces and managing intelligent-sourcing decisions in more complex, higher value textile supply chains.
Future Soldier systems objectives include lightening the Soldiers’ load, capitalizing on lessons learned after years of fighting, developing modular, agile materiel solutions that take advantage of advances in sensor technology and materials engineering.
To achieve these ends, the Army needs access to a skilled workforce and modernized industrial base capable of achieving advanced designs and developing novel industrial capabilities. Substantively enhancing the capabilities of the domestic textile industrial base is a major challenge. Through the Textile Automation to Enhance Domestic Military Production program, the OSD IBAS office is combining its manufacturing base expertise with the product knowledge and buying power of PM SCIE and the technical acumen of CCDC-SC.
Working together with forward-leaning industry partners, the program team expects to begin affecting change toward a more modernized domestic textile industry. However, spurring change in an industry that is slow to change and limited in resources is likely beyond the scope of a single DOD program effort. Therefore, as this effort evolves it will lean more heavily on both a widening circle of industry partners as well as other DOD investments in manufacturing technology are currently ongoing to help develop new technologies and providers. Investments made by the OSD Manufacturing Technology office in functional fibers at the Revolutionary Fibers and Textiles Institute and robotics at the Advanced Robotics for Manufacturing Institute are developing enabling technologies to enhance Soldier performance and add value to what were formerly commoditized products. Inclusion of these new technologies will require automation to make the technology affordable and accessible.
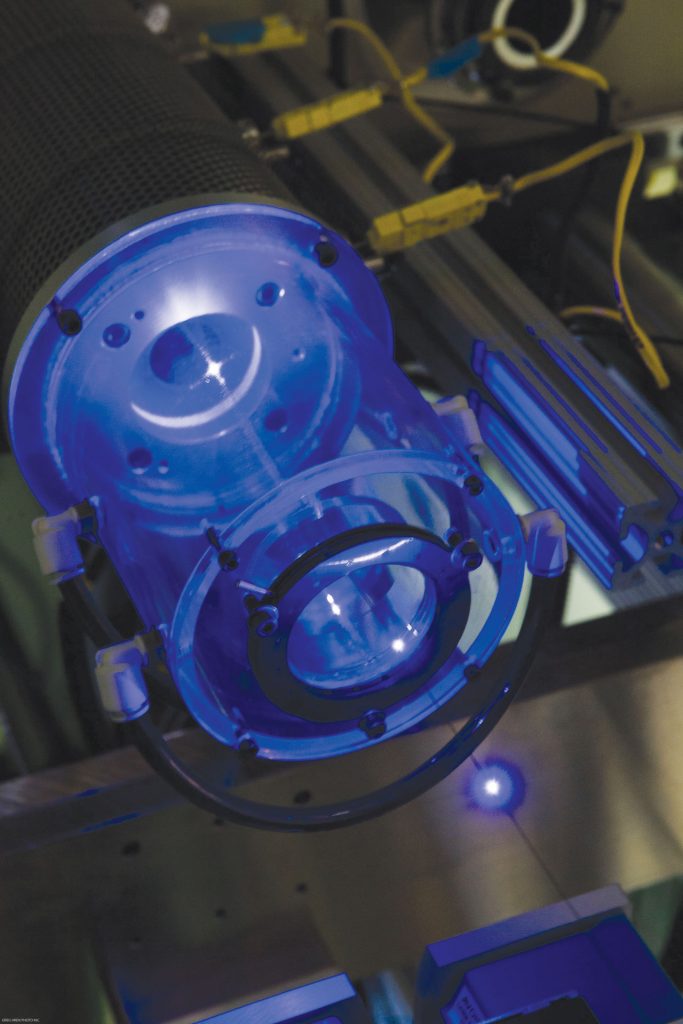
SWEET NEW THREADS: Semiconductors so small they are measured in microns, are embedded into monofilament fibers by drawing the semiconductor, insulators and conductors at the same rate using AFFOA’s draw towers.
CONCLUSION
By investing in and working with industry, the Textile Automation to Enhance Domestic Military Production program will enable the commercial rollout of automated manufacturing solutions by building a public-private collaboration to strengthen the U.S. industrial base while also making production more economically viable for all customers. Furthermore, these investments will serve to establish U.S. leadership in this critical area thereby improving domestic competitiveness.
This will create a growing need for a high-tech workforce in burgeoning, lasting markets, serving both the government and commercial industries. Because the domestic textile industry operates on extremely low profit margins and, as a result, is collectively limited in its access to internal research and development funding, it is highly unlikely that manufacturers would make the required capital investments in automation for the limited DOD market alone. Given partnership and investment through this OSD program and other federal investments, however, it may be possible to modernize the sector. By focusing on near term gains through automation of legacy textile and textile product production, the program may demonstrate the increased value proposition for technology insertion across a wider swath of the entire industry.
Of course, the initial reaction of many is that an increase in production automation and robotic assembly would reduce existing jobs across the textile industry. However, a 2017 study by the U.S. Department of Commerce, Bureau of Industry and Security titled “Textile and Apparel Assessment” paints a different picture. Of the 571 domestic manufacturers surveyed, 61 percent reported difficulties hiring and retaining employees, specifically “production line workers such as operators and machine technicians.” The reasons for this are many, but include facility locations that lack a large labor pool from which to draw, as well as competition for that same labor pool. Further, the study cites the lack of available workforce as the number one condition limiting their ability to increase manufacturing utilization rates to 100 percent in the event of a surge in demand. These factors seem to indicate that increased domestic manufacturing is not hampered by lack of jobs, but rather by the lack of people to fill them. Increased automation and the implementation of new technologies could help to fill these gaps.
The impacts to defense-related procurement are significant, both in the ability to surge the industrial base in times of conflict and also to integrate advanced capabilities into uniforms and equipment that can increase Soldier effectiveness. The defense textile industrial base has always surged to meet wartime requirements. This default expectation may no longer be possible. Labor, fiscal and global market constraints limit future adaptability.
The incorporation of increased automation and robotic assembly can help to offset industry production and innovation challenges resulting from a shrinking labor pool and legacy machinery. Meanwhile, these new innovations can both increase domestic competitiveness and create the adaptability needed for future Army requirements. The successful venture between PM SCIE, CCDC-SC, and OSD IBAS in the Textile Automation to Enhance Domestic Military Production program will help foster these industry changes.
For more information, visit the Office of the Secretary of Defense (OSD) Industrial Base Analysis and Sustainment (IBAS) website at: https://www.businessdefense.gov/IBAS/
JEFFREY PACUSKA is the Program Manager for Future Technologies Integration at the U.S. Army CCDC-SC, Natick, Massachusetts, and the technology and systems integration lead at the Defense Fabric Discovery Center (DFDC) at MIT Lincoln Labs. He previously worked as a CCDC-SC team leader and portfolio manager and as an assistant product manager and project engineer within the U.S. Army PEO Soldier. He holds an M.S. in materials system engineering management from Worcester Polytechnic Institute and received a B.S. in biochemistry from Tufts University. He is certified as a Project Management Professional, and is a member of the Army Acquisition Corps.
CLAY WILLIAMSON is the Future Programs Officer for PM SCIE at PEO Soldier and serves as DOD Soldier Systems Sector Lead for Executive Order 13806. He retired as a major from the Army and was an assistant product manager and then co-founder and president of a publicly traded defense industry company. He has an M.A. in procurement and acquisition management and a B.A. in industrial-organizational psychology. He is certified as a Project Management Professional and is a member of the Army Acquisition Corps.
SUZANNE HORNER is the lead systems engineer for Soldier Clothing and Individual Equipment at PEO Soldier in Fort Belvoir, Virginia. She served as an assistant director technical management for Project Manager Soldier Survivability, managing research and development programs for the Soldier Protection portfolio. Horner received a M.S. in mechanical engineering from the University of Massachusetts and is a member of the Army Acquisition Corps.
STEPHEN LUCKOWSKI is a directorate advanced manufacturing associate at the Combat Capabilities Development Command Armaments Center, Picatinny Arsenal, New Jersey. His primary roles are program manager of the DOD Revolutionary Fibers and Textiles Manufacturing Innovation Institute and providing strategic planning for the Armaments Engineering Analysis and Manufacturing Directorate. Luckowski is working on behalf of the DOD’s Manufacturing Technology Program to establish an advanced fibers and textiles manufacturing innovation ecosystem. He holds a B.S. in materials engineering from Drexel University and previously served in the U.S. Army, leaving service at the rank of major. He is a member of the Army Acquisition Corps and a prior chair and current member of the American Welding Society D1.9 Structural Welding Titanium Code Committee. Luckowski has been awarded multiple patents and has been recognized by the Army’s Greatest Invention Awards Program for inventions in titanium welding as well as armament and protection systems.
Read the full article in the Fall 2020 issue of Army AL&T magazine.
Subscribe to Army AL&T News – the premier online news source for the Army Acquisition Workforce. Subscribe