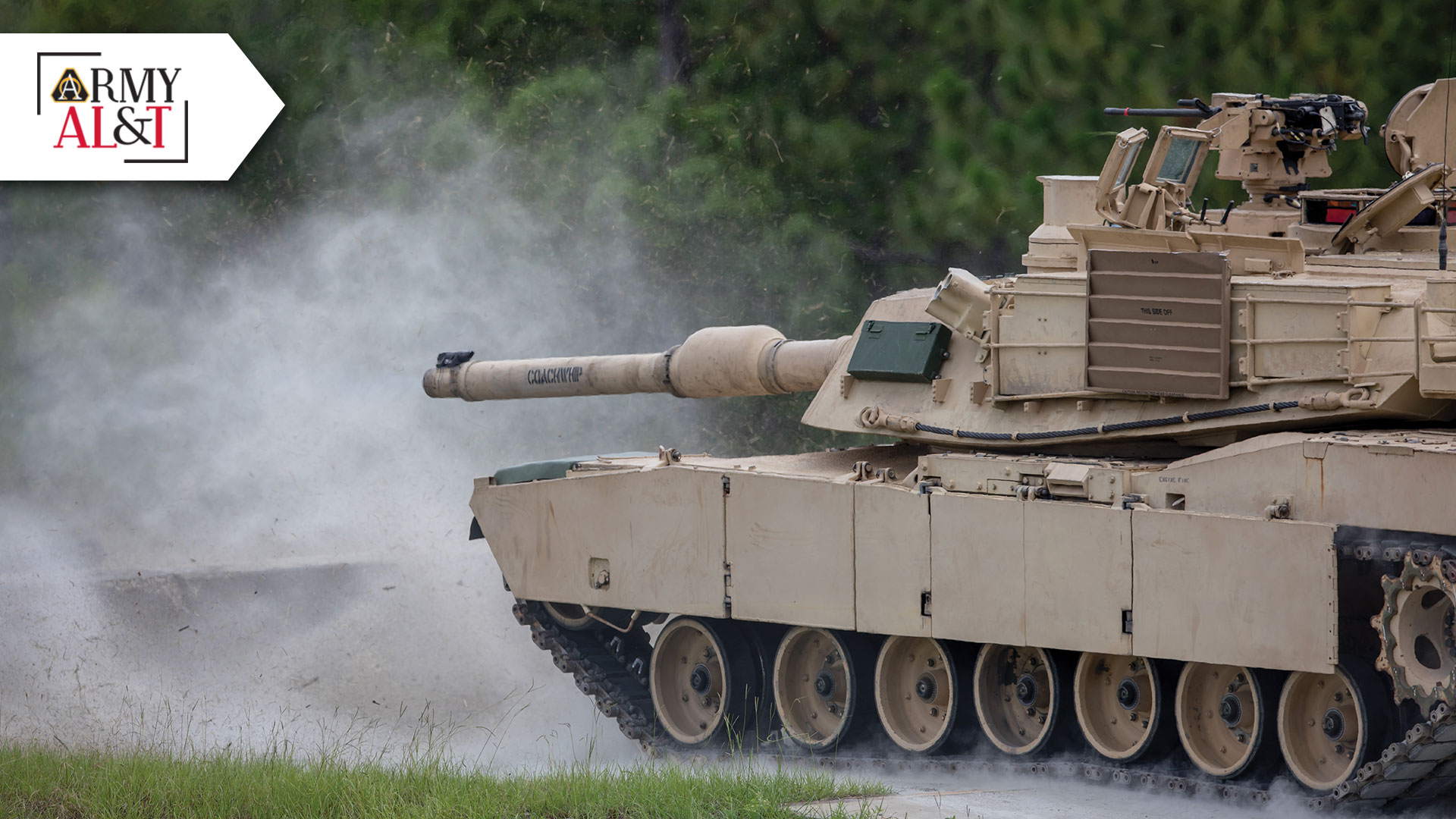
A new tank cartridge primer reduces manufacturing time and critical defects, improving overall ammunition safety for Soldiers.
by Hjalmar “Jay” Canela
For today’s Soldiers, maintaining tactical proficiency on the M1 Abrams tank requires tactical and training rounds that are safe and perform as intended. Tactical cartridges for the M1 Abrams must create maximum impact with minimal use of ammunition. Compared with the wide array of ammunition being used and developed by the U.S. Army, tank cartridges stand out as complicated and require extensive focus on quality and safety assurance. Primers are key components in tank cartridges—ensuring they function reliably is critical, as they are the primary ignition element in the cartridge ignition sequence. The Joint Program Executive Office for Armaments and Ammunition’s Project Manager for Maneuver Systems (PM MAS) manages the life cycle of small-, medium- and large-caliber ammunition, including tank cartridges.
In 2021, the PM MAS tank ammunition team incorporated an improved primer into the Kinetic Energy Tank Training M865A1 and the XM1147 Advanced Multi-Purpose cartridges. The primer qualification occurred during the M865A1 cartridge qualification, saving the government considerable time and money by combining test requirements and engineering efforts. The new primer improves manufacturability, decreases susceptibility to electromagnetic safety hazards and reduces manufacturing costs. It is known as the Hazards of Electromagnetic Radiation to Ordnance (HERO) primer.
PRIMER DESIGN HISTORY
The initial 120 mm family of tank cartridges qualified with the M125 “thin-walled body” primer in 1984 (Figure 1). Engineers at Picatinny Arsenal, New Jersey, later determined through internal testing that the thin wall could conduct enough heat to the propellant to ignite it in the event that a just-fired primer came in contact with another Abrams tank cartridge. The first redesign consisted of a rubber coating applied to the M125 thin-walled primer body to prevent heat transfer.
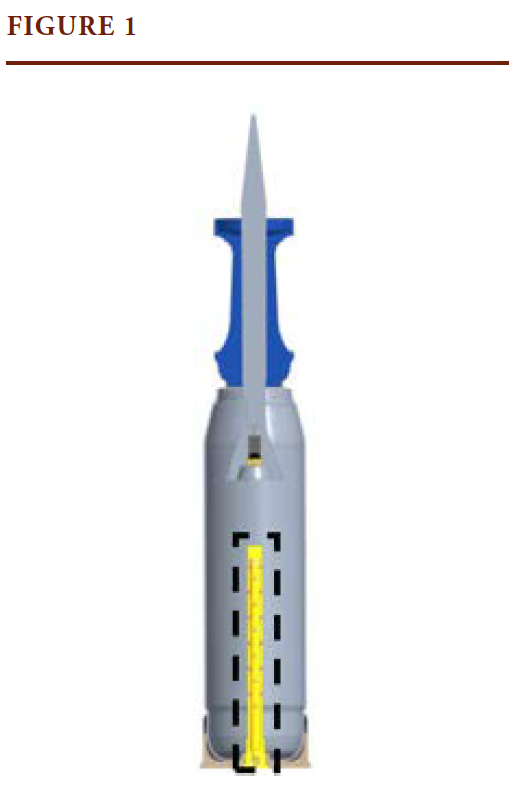
These are the primary differences between the legacy thick-wall, one-piece and two-piece primers.
The next redesign occurred in 1998 with the M125 Electric Primer (Figure 2), which included a thick-wall body, replacing the rubber coated thin-walled primer. The thick wall provides enough thermal mass to delay heating of the primer body, preventing premature ignition of the propellant. These design changes only affected the body of the primer, not the interior. The ignition element assembly (IEA) (Figure 3) maintained the same configuration since the 1984 cartridge qualification, and it is the primary charge in the ignition train of the cartridge. The IEA is what initiates the propellant, expelling the cartridge out of the gun tube.
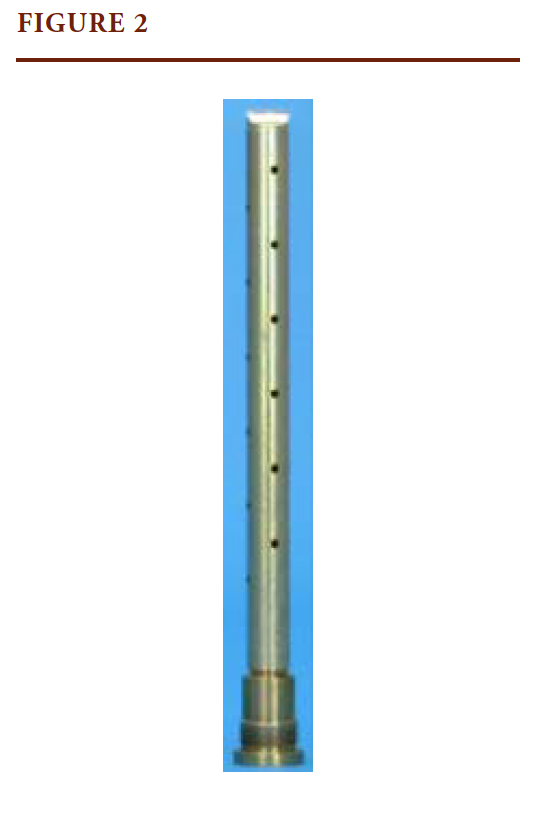
The addition of a thick-walled body prevent heat transfer that could cause premature ignition.
The manufacture of the legacy M125 electric primer provided its own share of manufacturing issues. Small, fragile parts made automation nearly impossible, and the numerous individual components increased the chances of manufacturing defects. Picatinny Arsenal’s Combat Capabilities Development Command (DEVCOM) Armaments Center teams monitored the most critical aspects of the manufacturing process to ensure that a component failure would not risk life or limb. The quality assurance process inspected for 16 critical defects in the M125 electric primer. A critical defect is a production non-conformance that could have catastrophic results in the field if not caught during production. The high number of critical defects in the design contributed to manufacturing delays because of work stoppage, leading to additional costs and potential defects reaching the field.
Another persistent issue in the production assembly of the thick-walled primer was the application of the lacquer plug resin on the primer body. The lacquer material would plug the primer body holes (Figure 2), creating a seal and preventing moisture from accumulating inside the primer body to protect the benite (Figure 3). Benite is a black powder substitute that’s also widely used in wood conditioners. Moisture in the primer body would adversely affect the performance of the primers. The lacquer came off the body holes during handling or transportation many times during primer production, making lacquer inspections a critical inspection item during lot acceptance.

The ignition element assembly in the M125 Electric primer maintained the same configuration since the 1984 cartridge qualification.
To fix the lacquer issue, the Picatinny engineering team recommended adding a plastic liner design into the HERO primer configuration. The plastic liner is a tube inserted in the primer body that provides a more effective moisture seal for the benite. Picatinny engineers developed an engineering change proposal to incorporate the plastic tube into tank cartridge primers in 2011 as a superior design to the lacquer paint.
PREVENTING HAZARDS
In addition to the improvements above, an investigation of a 2002 tank fire at Fort Hood, Texas, led Picatinny engineers to discover that tank cartridges were very susceptible to initiation by radio frequencies if the primer was in contact with any of the electrodes of the electronics in the tank. This discovery necessitated the Army to require primers to be HERO compliant. The radio frequency signals were not the cause of the tank fire, but the radio frequency susceptibility needed correction.
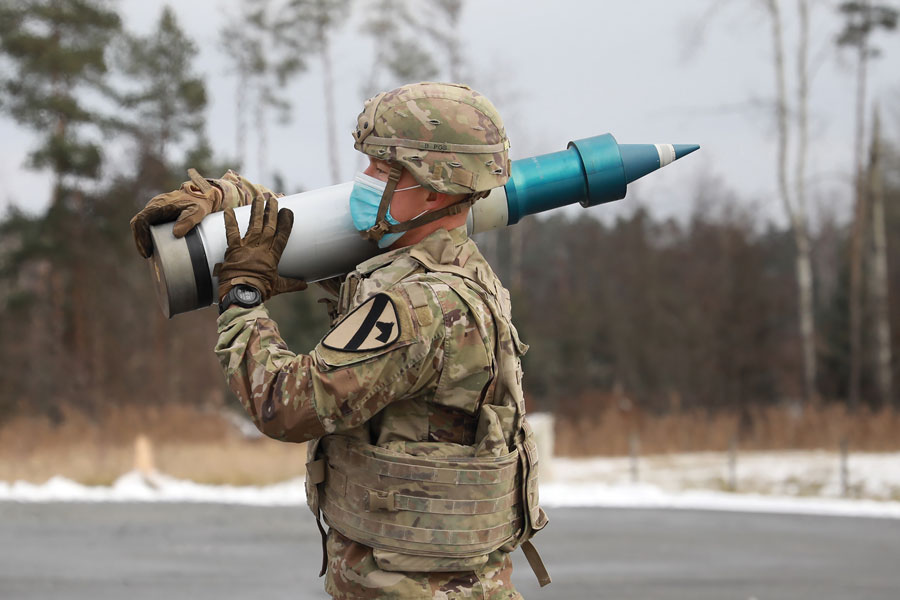
NECESSARY PREPARATIONS: A Soldier assigned to 1st Armored Brigade Combat Team, 1st Cavalry Division carries a 120 mm tank round in December 2020, in preparation for qualification at Grafenwoehr Training Area, Germany. (Photo by . Thomas Stubblefield, 241st Mobile Public AffairsDetachment)
Picatinny engineers, with help from the Navy Support Facility Dahlgren, Virginia, which had conducted testing for the investigation, confirmed that the primers were susceptible to radio frequency signals and provided the basis for the Army to issue a Safety of Use message in 2004, titled SOUM-04-020, Operational, Use of Standard and COTS/NDI UHF Radios. The safety message stated that standard and commercial off-the-shelf UHF radios operating in the range of 200-280 MHz have enough energy to initiate the cartridge primer if the center electrode is touched by either a person or object when within 30 meters of unpackaged tank ammunition. Engineers determined that a primer designed to fire only when exposed to a current of 1.3 amperes or greater would solve the safety problem. This value became the threshold requirement for future primers.
The Picatinny engineers and Dahlgren test results provided the basis for the U.S. Army’s HERO military standard (MIL-STD), DOD MIL-STD-464, which provides guidance for making all ammunition and systems HERO compliant. On Dec. 1, 2010, DOD released the latest version of the standard, MIL-STD-464C, “Department of Defense Interface Standard: Electromagnetic Environmental Effects Requirements for Systems,” that “establishes electromagnetic environmental effects (E3) requirements and verification criteria for airborne, sea, space, and ground systems, including associated ordnance.” The intent was to ensure that all systems and ordnance for those systems could be “sufficiently shielded or otherwise so protected that all electrically initiated devices (EIDs) contained by the item are immune to adverse safety or reliability effects when the item is employed in the radio frequency environment delineated in the standard.” The objective for PM MAS then became to develop a HERO-safe primer for all large caliber (120 mm and 105 mm) tank cartridges.
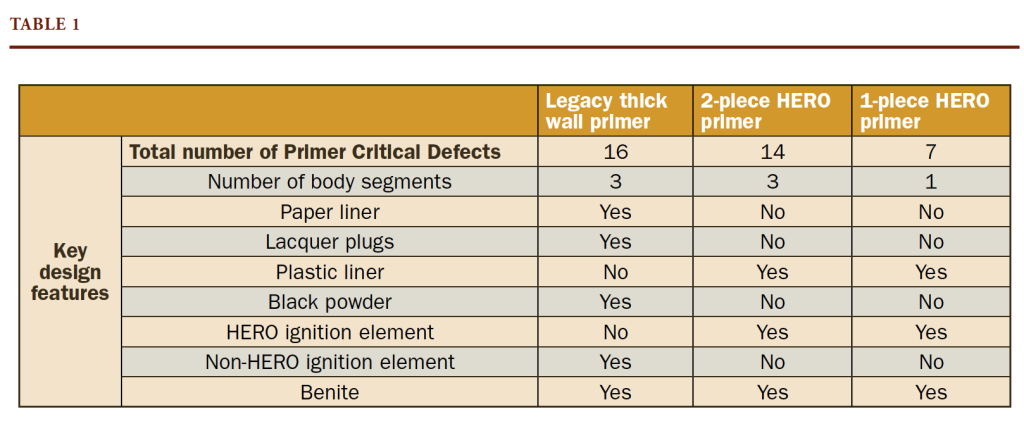
These are the primary differences between the legacy thick-wall, one-piece and two-piece primers.
THE HERO PRIMER
After much work between Picatinny engineer design teams and industry partners, there are now two acceptable configurations of the HERO primer—the one-piece and two-piece designs (Figures 4 and 5).
Table 1 identifies the differences between the legacy thick-wall, one-piece and two-piece primers. The manufacturing process of both variants of HERO primer reduces the level of hands-on assembly required, thereby reducing production costs. The HERO configurations also eliminate the need for lacquer plugs and black powder.
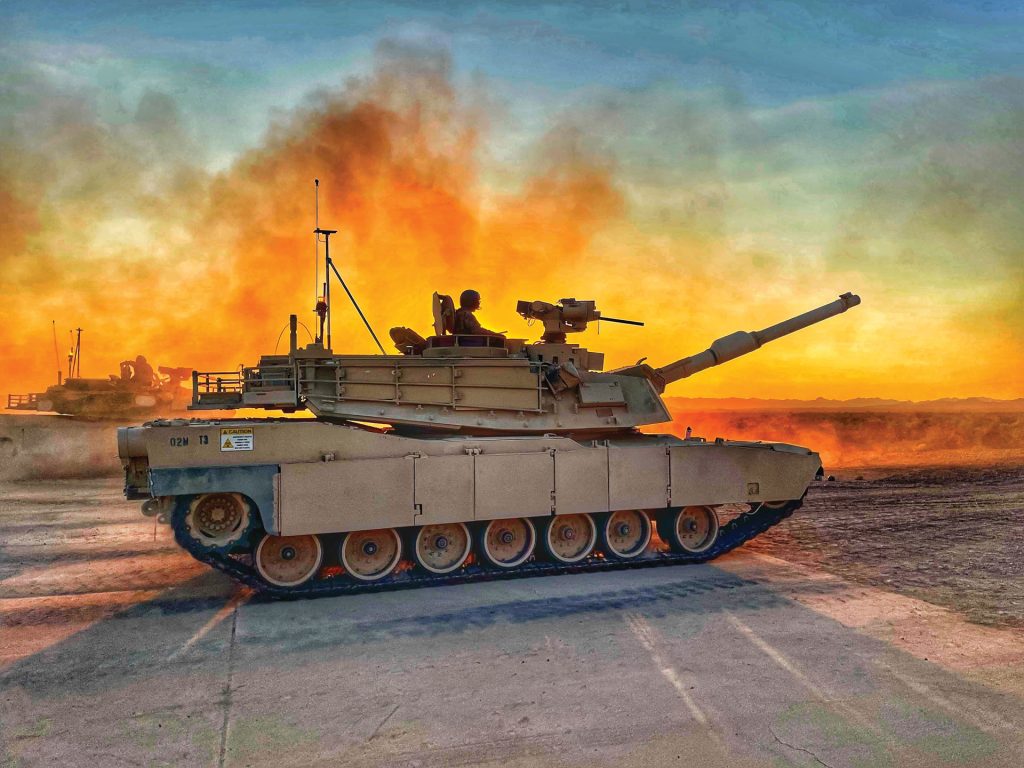
TEST ROUND: Soldiers assigned to 4th Infantry Division test the XM-1147 Advanced Multipurpose round in September at Yuma Proving Grounds, Arizona. (U.S. Army photo illustration courtesy of Maj. Michael Brabner)
The comparison table shows the reduction in the number of critical defects from the legacy electric primer from 14 to seven for the one-piece HERO primer variant.
Since the issuance of DOD MIL-STD-464, all new lots of tank ammunition required a waiver for not meeting the HERO requirement. In 2015, the HERO ignition element assembly qualified on the M1002 and M865 cartridges, but due to extenuating circumstances, there were issues in incorporating the HERO primer into tank cartridges at that time.
In 2016, PM MAS stopped waiving the requirement. Subsequently, the XM1147 Advanced Multi-Purpose and the M865A1 cartridge programs both qualified with HERO primers. Both programs conducted life cycle testing to ensure reliability and survivability of the cartridge systems and became the first lots with HERO primers in tank ammunition inventory. Additionally, the new M865A1 kinetic energy tank training cartridge qualified in 2021 with the one-piece HERO primer (Figure 5). This will allow the incorporation of the same primer into the M1002 High Explosive Anti-Tank trainer tank cartridge.
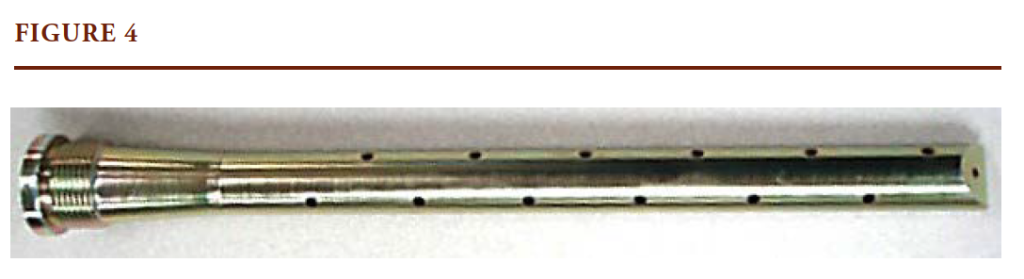
The one-piece design is one of only two acceptable configurations of the HERO primer.
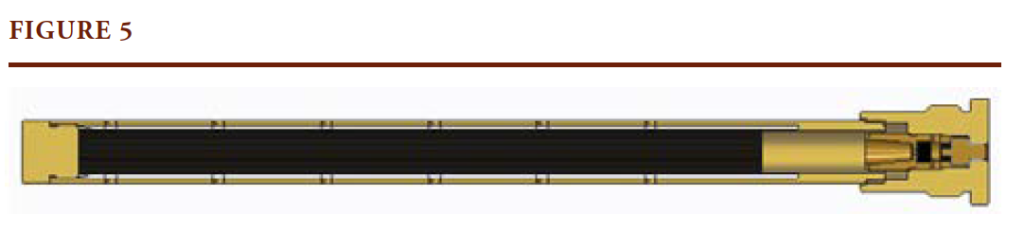
The two-piece HERO primer reduces the level of hands-on assembly required, thereby reducing production costs.
CONCLUSION
PM MAS strives to enhance the lethality, reliability and performance of tank cartridges. Individual component improvements can be a major step forward in performance, and the HERO primer is an example of that. The legacy tank ammunition primer had been in production for many years with relatively little advancement and an archaic manufacturing process. The HERO primer reduces manufacturing time, number of parts, critical defects and overall production costs. Most importantly, the HERO primer improves the safety of our 120 mm Abrams tank ammunition for our Soldiers.
For more information on MIL-STD-464C, go to: https://tinyurl.com/5zbsr83z.
HJALMAR “JAY” CANELA is the item manager for the 120 mm Tank Training Ammunition at the Joint Program Executive Office for Armaments and Ammunition, PM MAS. He holds an M.S. in mechanical engineering from Stevens Institute of Technology, and is Level III certified in engineering.