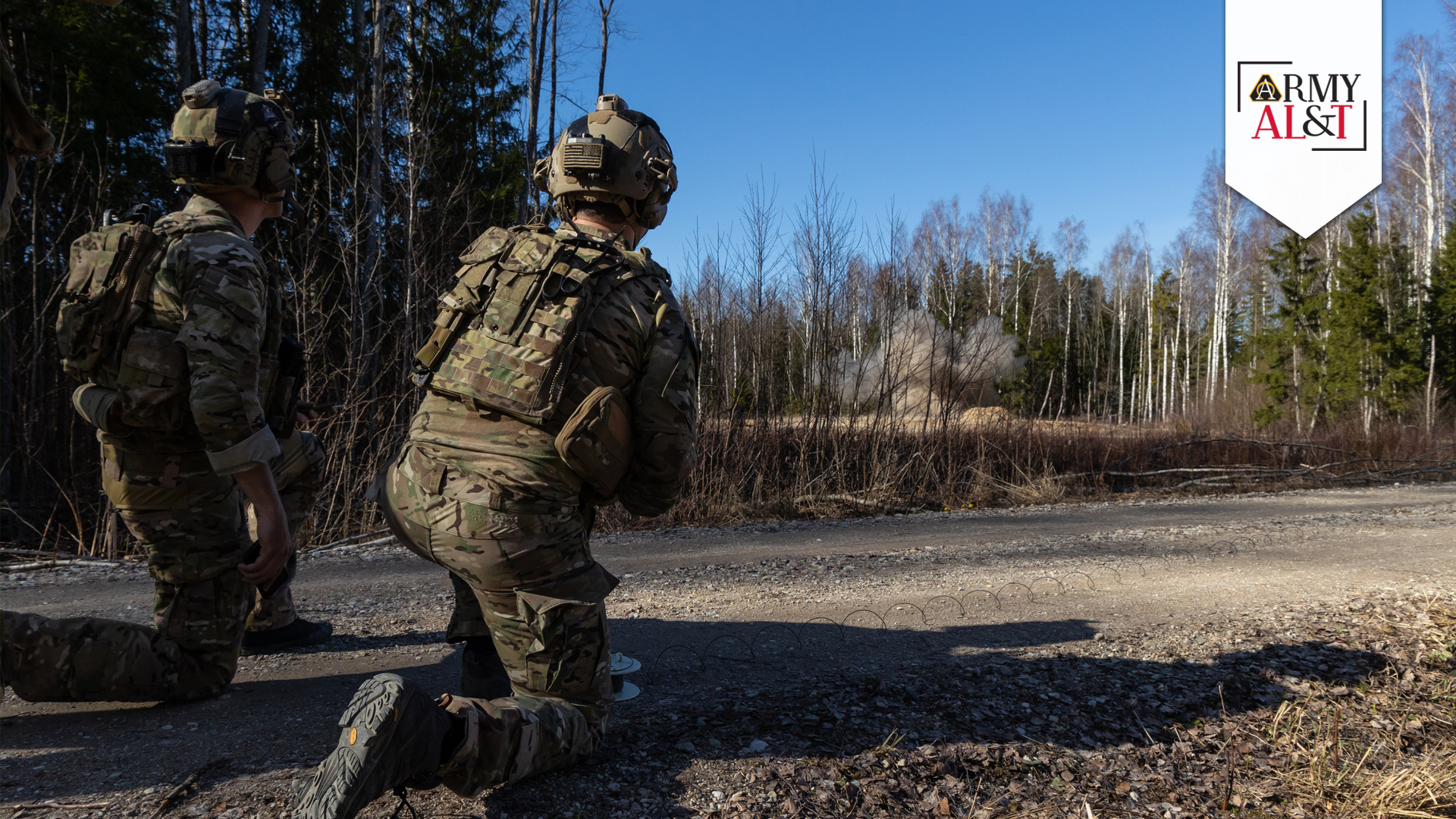
PRACTICE ROUND: Special Forces Soldiers assigned to 10th Special Forces Group (Airborne) detonate a charge during training in Estonia, April 2023. The Army hopes to reuse munitions waste products within the organic industrial base. (Photo by Staff Sgt. Anthony Bryant, U.S. Special Operations Command Europe)
The Project Director Joint Services team turns waste into valuable products for sustainable munitions production.
by Gregory O’Connor
As industries continue to face shifting dynamics in international politics, there is increased pressure on sustainability, supply chains and the use of raw materials. Ammunition production in an environmentally sustainable manner is crucial in today’s world. Therefore, it is essential to minimize the impact on the environment, manage supply chains and reduce reliance on materials from overseas.
By adopting sustainable production practices, the Army can organically increase the supply of critical chemicals and reduce the cost of waste disposal. One effective strategy to achieve sustainability in ammunition production is through byproduct synergy. This approach involves identifying and utilizing waste materials generated during the production process as raw materials for other industries or reworking the waste so that it can be reused as feeder stock within the Army’s organic industrial base. By doing so, the Army can minimize waste disposal, increase supply readiness of critical chemicals and create a circular economy where materials are reused.
Through byproducts synergy, waste materials can be transformed into valuable resources, creating new opportunities for economic growth and innovation. For example, various waste chemicals are produced when manufacturing explosives and propellants; disposing of these waste streams can be a costly environmental challenge. The Army traditionally has relied on inexpensive chemicals sourced from outside the United States, some of which are used for producing explosives and propellants. However, concerns over supply chain issues and dependence on foreign sources have highlighted the need for alternative solutions. The Project Director Joint Services (PD JS) team came up with a way to manage environmental and supply chain risks with one clever idea that focuses on the benefit of turning waste into valuable products.
To combat these challenges, the Army has invested in PD JS Life Cycle Pilot Process Program research, development, technology and evaluation funding to research and explore sustainable approaches. One such approach involves utilizing waste streams generated at government-owned, contractor-operated (GOCO) facilities to produce critical chemicals. These waste streams, which are byproducts of production, often contain chemicals that are a disposal challenge. Instead of disposing of these waste streams, the Army aims to chemically convert them into ingredients that can be used in the production processes within the facility or within DOD end items. This approach addresses the issue of costly waste disposal, ensures a reliable supply of critical chemicals onsite and reduces dependence on overseas suppliers.
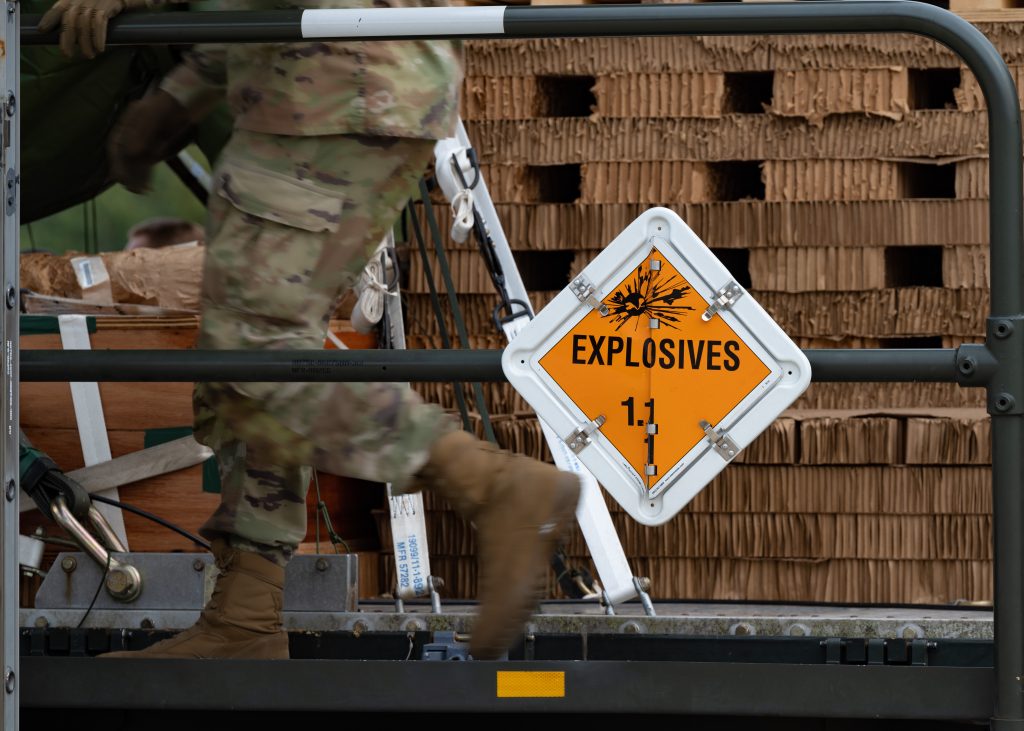
AMMO ON THE MOVE: The PD JS Life Cycle Pilot Process Program focuses on converting ammonium nitrate solution—a waste product of explosives manufacturing—into potassium nitrate. (Photo by Senior Airman Andrew Bertain)
CONVERSION SUCCESS
This project specifically focuses on the conversion of ammonium nitrate solution, a waste product of explosives manufacturing, into potassium nitrate, a critical chemical used in some DOD end items. It is being conducted in multiple phases to demonstrate feasibility and provide insights for further development.
Phase I aimed to prove the concept that ammonium nitrate solution can be chemically neutralized to yield potassium nitrate. The first phase involved small laboratory-scale experiments to determine the optimal neutralizing agent and identifying the optimal waste stream feedstock for potassium nitrate manufacture. It also included laboratory-scale reactions to assess scalability and safety. The results of Phase I demonstrated successful synthesis of approximately 10 pounds of recrystallized potassium nitrate product from ammonium nitrate solution, along with the identification of the optimal process parameters.
Phase II focused on scaling up the process to produce 350 pounds of potassium nitrate. This phase involved utilizing a larger pilot-scale reactor and incorporating the potassium nitrate into a flash suppressant formulation. The resulting potassium nitrate product was characterized and compared to military specification requirements. The successful completion of Phase II led to the formulation of the potassium nitrate product into a flash suppressant. The findings from Phases I and II have paved the way for further scale-up and optimization. Phase III will develop an implementation plan for a larger scale process to maximize the value of waste streams in munitions production.
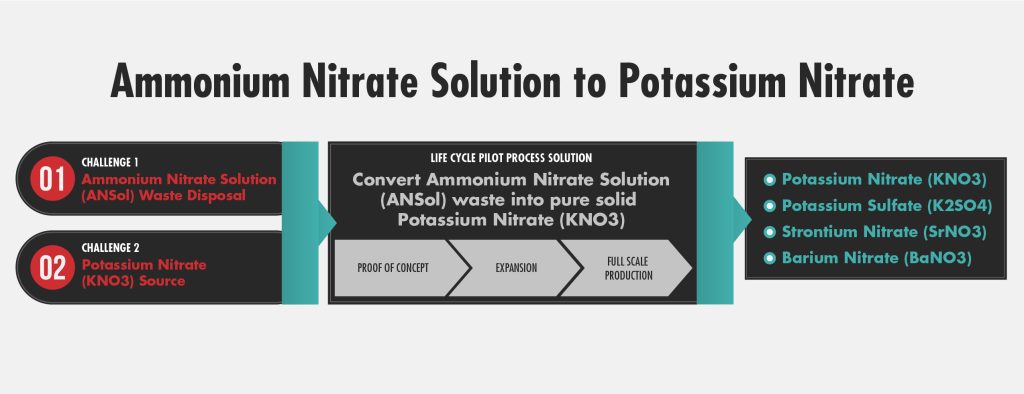
THE CONVERSION PROCESS: Chart shows the conversion of Ammonium Nitrate Solution (ANSol) into Potassium Nitrate (KNO3), which addresses supply chain vulnerabilities and contributes to sustainability efforts. (Graphic by Gregory O’Connor, JPEO A&A – Project Director Joint Services and USAASC)
CONCLUSION
Overall, the project has successfully demonstrated the feasibility and merit of turning waste into valuable products within the Army’s munitions production process. The successful conversion of ammonium nitrate solution into potassium nitrate not only addresses supply chain vulnerabilities but also contributes to sustainability efforts by reducing waste disposal, reliance on external sources and exemplifies the Army’s commitment to a greener future. Additional work is currently underway analyzing the potential of processing ammonium nitrate solution into strontium nitrate and barium nitrate, as well as exploring other manufacturing waste streams for synthesis of potassium sulfate, all of which are chemicals used by DOD. By integrating environmental sustainability and waste reuse into GOCO production facilities, the Army can reduce its environmental footprint while becoming a more resilient organic ammunition industrial base.
For more information, contact Gregory O’Connor at gregory.j.oconnor.civ@army.mil or 973-724-5008.
GREGORY O’CONNOR is the government-owned contractor-operated modernization manager within the Project Director Joint Services. He did postgraduate work in systems engineering at Stevens Institute of Technology, holds an M.S. in environmental chemistry from New Jersey Institute of Technology and a B.S. in environmental chemistry from Delaware Valley University. He received executive certificates from the Massachusetts Institute of Technology, the University of Pennsylvania and Cornell University.