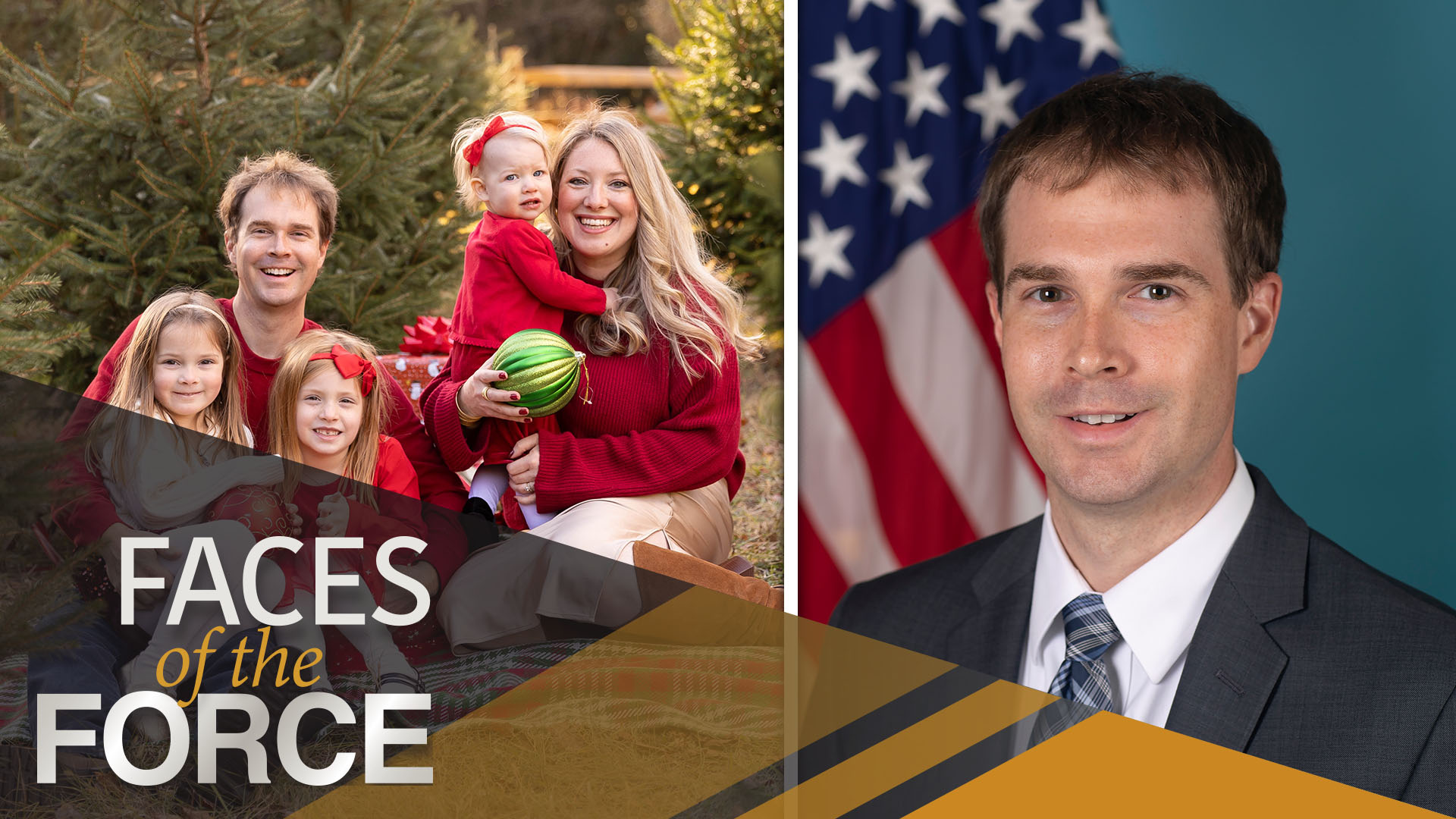
COMMAND/ORGANIZATION: Joint Program Executive Office for Armaments & Ammunition/Directorate of Integration
TITLE: Environmental, safety and occupational health manager
YEARS OF SERVICE IN WORKFORCE: 15
DAWIA CERTIFICATIONS: Practitioner, engineering and technical management
EDUCATION: Master of Civil Engineering and Bachelor of Environmental Engineering, both from University of Delaware
AWARDS: Army Civilian Service Commendation Medal (May 2024), Army Commander’s Award for Civilian Service (December 2017)
Brian Hubbard
by Cheryl Marino
Removing hazardous chemicals from essential resources is vital to protect health, ecosystems and future access to clean water, air and soil. Finding safer alternatives to potentially harmful chemicals in ammunition is critical. Without a qualified substitute, loss of access to these critical chemicals or materials would prevent the Soldier from obtaining overmatch capabilities when they are required.
As the environmental safety and occupational health (ESOH) manager for the Joint Program Executive Office for Armaments and Ammunition (JPEO A&A), Brian Hubbard works closely with project management and project lead offices to identify, assess and mitigate environmental hazards and occupational health risks impacting the armaments and ammunition life cycle, as well as the supply chain—from early research, development, technology and engineering through disposal.
Hubbard’s role also includes monitoring evolving domestic (Toxic Substances Control Act) and international (European Union’s Registration, Evaluation, Authorisation and Restriction of Chemicals) environmental regulations and determining their impacts to JPEO A&A’s mission.
“These dynamic regulations often impact critical manufacturer and supplier decisions to either remain in the market or exit it entirely,” Hubbard said. “Through partnership with our JPEO A&A colleagues, as well as Army and DOD higher headquarters, I’ve had the opportunity to communicate how these emerging risks may impact the armaments and ammunition life cycle as well as advocate for continued access to the material/item or invest in projects to develop alternates that are not only more ESOH-friendly but also achieve performance and cost requirements.”
Hubbard joined the JPEO as the ESOH officer in 2017. He said the role appealed to him because it was the first of its kind—offering an opportunity to engage with Army stakeholders across the enterprise to seek out, develop and actively coordinate with teams to advocate for armaments, ammunition equities within Army and DOD policies; identify research programs; and assess and mitigate not only today’s ESOH challenges but those that could emerge in the future. These are challenges, he said, that if left unresolved, could adversely impact a program or the ability to deliver that capability to the warfighter.
“This position affords an exciting opportunity to combine ESOH engineering and science, policy and the life cycle acquisition process to support JPEO A&A teams developing and fielding next-generation end items to provide the Soldier with overmatch capabilities,” he said.
Prior to his position as an ESOH officer, Hubbard served as an environmental engineer supporting Organic Industrial Base Modernization and leading explosive production wastewater treatment projects, as well as air pollution control projects and hazardous waste management efforts.
In a recent career-broadening role, Hubbard served as a principal investigator on a newly completed DOD Environmental Security Technology Certification Program (ESTCP) project, during which his team successfully validated a novel nano-zero valent iron–hydrogen peroxide technology for munitions production wastewater treatment. The goal of the project, he said, was to demonstrate a process that could help reduce a potential bottleneck in the load, assemble, pack (LAP) production process – wastewater treatment.
“Our technology was able to completely degrade the energetic components of a highly concentrated actual waste stream within minutes,” Hubbard said. As a result of the successful ESTCP effort, his team is working to further evaluate and reduce potential technology transition risks, with the ultimate goal of transitioning to the industrial base.
“This project provided me an opportunity to lead a research team, where I was responsible for not only budget but also technology performance and execution,” he said. “Throughout the project we engaged with our DOD ESTCP customer and also coordinated with Army stakeholders to support technology transition opportunities.”
In addition to the career-broadening role discussed earlier, Hubbard recently completed the Acquisition Leadership Challenge II Program (virtually) in August 2023 to learn tools and techniques to build coalitions and develop shared values to address ill-structured problems.
“I wasn’t really sure what to expect heading into the program, though [I] kept an open mind. As the course proceeded, I appreciated the group activities and opportunities to engage with leaders across the Army,” said Hubbard, who garnered three top takeaways from the course: 1) learn and develop methods to enhance critical/strategic thinking as it relates to his role; 2) utilize actionable techniques to enhance coordination, communication and collaboration both up and down the chain of command; and 3) embrace thought diversity and how teams synergize to address tough challenges.
“One of the skills I try to apply most from this program to my job and outside of work is active listening,” he said, which has come in handy in his personal life with his wife, Caitlyn, and three young daughters: Charlotte, 5, Maeve, 4, and Gillian, 1. “This program has had a positive impact on my career. It has helped me to use the tools learned in the course and take steps to be more proactive, seek collaboration opportunities and leverage the power of teams to address not only today’s but also tomorrow’s challenges in my job.”
Prior to children, Hubbard enjoyed distance running and completed half marathons and three full marathons like the Philadelphia Marathon in 2014, Lake Placid in 2015 and Chicago in 2017. These days, he and his family try to fit in a few local 5K runs and family-fun runs.
“I believe distance running (and parenting) has a few aspects in common with work,” he said. “Starting out, it may seem like I’m never going to reach the finish or that the task at hand is daunting, but with perseverance, the farther you go—much like with work tasks—the race or current project becomes more manageable. Hubbard admits he “definitely was not a fast runner,” but kept moving, fell into a groove and before he knew it the race was over.
“I think the most important lesson I’ve learned over the course of my career is to keep an open mind and seek opportunities for collaboration. This is something I try to apply off the job as well,” he said. For example, as an environmental engineer, he may see a particular topic or challenge from his vantage yet wants to understand and learn how a colleague views it from their perspective. Through developing this understanding, he believes a synergy develops for solving ESOH challenges that could impact the armaments and ammunition life cycle.
“I never thought I would have become an acquisition professional; thinking I was going to remain only technical in my career but took a chance on applying for the ESOH officer role,” Hubbard said. “This is the best, most rewarding job I’ve had in my career. I’ve stepped outside of my comfort zone, and I try to share with my proteges that finding opportunities to expand your comfort zone will help you prosper.”